Digital Twin: Enabling Technologies, Challenges and Open Research
Ieee account.
- Change Username/Password
- Update Address

Purchase Details
- Payment Options
- Order History
- View Purchased Documents
Profile Information
- Communications Preferences
- Profession and Education
- Technical Interests
- US & Canada: +1 800 678 4333
- Worldwide: +1 732 981 0060
- Contact & Support
- About IEEE Xplore
- Accessibility
- Terms of Use
- Nondiscrimination Policy
- Privacy & Opting Out of Cookies
A not-for-profit organization, IEEE is the world's largest technical professional organization dedicated to advancing technology for the benefit of humanity. © Copyright 2024 IEEE - All rights reserved. Use of this web site signifies your agreement to the terms and conditions.

Manufacturing Technology journal in the Web of Science is indexing. Since 2020 all articles have been indexed. See on: https://www.webofscience.com/wos/

EDITORS INFO:
Authors must provide the ORCID number of all authors in the manuscript. See Instructions for authors . Registration is available on: https://orcid.org/
Current issue
Manufacturing technology journal, 2024 (vol. 24), issue 2, microtexturing for enhanced machining: evaluating tool performance in laser-processed cutting inserts, ondrej bilek, jan ondrik, petr janik, tomas kautsky.
This article explores the significance of microtexturing on cutting tools for improved tribological performance and reduced friction in machining operations. Drawing inspiration from biomimetic structures, the study focuses on laser surface microtexturing and evaluates its impact on cutting forces and tool wear. Experiments involve microtextures of dots with a specific emphasis on a fiber laser-processed pattern. While long-term tests reveal the formation of negative protrusions on the textured tools, reduced variability in cutting forces suggests potential benefits for stable machining processes and increased tool longevity. The findings underscore...
A Unique Numerical Model to Evaluate the Influence of Adherends’ Misalignment on Adhesive Joint Strength
Andrea corrado, wilma polini.
Industry 4.0 needs to have a digital representation of the real manufacturing and assembly processes to foresee the effects of modifications on equipment, tools and processes. Assembly processes often use adhesive to keep together the components because it has many advantages. The simplest example of adhesive assembly is a single lap joint. In the literature, the attention is focused on nominal adhesive assemblies, that do not represent the real products and that are tested to evaluate the product’s strength. Therefore, the obtained mechanical performances are far from those connected with the real products. The present work takes into account...
The Effect of Employing an Optimal Web Velocity Profile on Transverse Vibrations in Roll-to-Roll Manufacturing
Kadhim a. jabbar.
The quality of web products is significantly affected by the running velocity of a process line, especially during the stages of start-up and shutting down of a web processing line. At these stages, a remarkable transverse variation (web flutter) are observed due to employing improper input velocity. Web flutter may cause some web defects such as wrinkles, poor printing and even web breakage. Therefore, employing an optimal web velocity profile is crucial to minimize web transverse vibrations during the transport of the web through different processing sections in a web process line. In this paper, an optimal velocity profile along with common velocity...
Carbide Twist Drill Spiral Groove Abrasive Flow Polishing and Abrasive Flow Analysis
Tian ji, lintao lu, boming ren, guihong bian, shengli huang.
This paper carries out the simulation of abrasive flow for twist drill spiral grooves and the experimental study of abrasive flow polishing. The flow of abrasive in spiral groove in abrasive flow polishing twist drill was analyzed by CFD using FLUENT software. Different inlet speeds and abrasive concentrations were used as parameters for simulation calculations to obtain the state parameters of dynamic pressure and abrasive velocity in the flow channel, and to analyse their effects on the abrasive flow in the spiral groove. The analysis results show that the dynamic pressure in the twist drill spiral groove increases with the increase of inlet speed,...
Analysis of the Impact of Modernization of Machinery on the Quality of Castings Using Quality Management Tools
Krzysztof knop, pavol gejdoš.
Today's manufacturing industry, especially in the context of the metals industry, is constantly evolving towards ever more advanced technologies and efficient production practices. In this context, machinery modernization is becoming a key element in improving manufacturing processes. This article focuses on analysing the impact of machinery modernization on casting quality, using selected quality manage-ment tools. The article presents an analysis of the effects of the implementation of modern technology, automatic casting machines, on the quality of castings production. Using quality tools such as the Ishi-kawa diagram, Pareto-Lorenz and the FMEA...
Research and Dynamic Analysis of a Cable Reel Device Based on Constant Tension
A constant tension cable reel based on planetary gear transmission is introduced. The parameters of the mechanism are determined to analyze the speed and torque of the transfer mechanism. The relationship between the thread pitch and cable type show that different cable models require different parameters for the constant tension cable reel. The mechanism is designed to automatically adjust the force required for cable pulling and maintain a constant maximum tension. Then the relationship between the moment and speed of each output shaft is analyzed, and the operation mode of the cable reel was explained. The experimental results show that the proposed...
Microstructure and Mechanical Properties AlSi7Mg Alloy with Sr, Al and AlSi7Mg
Tomasz lipiński.
Strength and malleability are important reasons for increasing applications of Al-Si alloys. Mechanical properties of Al-Si cast alloys depend not only on chemical composition but, more importantly, on microstructural features such as morphologies of dendritic α-rich in Al, eutectic β-rich in Si particles and other intermetallics that are present in the microstructure. The microstructure of an unmodified hypoeutectic AlSi7Mg alloy is responsible for the alloy's low strength parameters, and it limits the extent of practical applications. The mechanical properties of hypoeutectic silumins can be improved through chemical modification as well...
Microstructure and Properties of Natural Alloy Prepared by Aluminothermic Reduction of Deep-Sea Nodules and Processed by Rapid Solidification
Alena michalcová, matouš orlíček, pavel novák.
This paper explores the investigation of a natural alloy processed using the rapid solidification tech-nique. The study involves the reduction of manganese nodules through aluminothermy with a 20 wt. % excess of aluminum, followed by further processing of the resulting alloy using the melt-spinning process. The obtained melt-spun ribbons were subjected to a comprehensive analysis, including X-ray diffraction, scanning electron microscopy for microstructure observation, and EDS analysis for local chemical composition. The research unveiled that the rapidly solidified ribbons consist of several key phases, including β-Mn, the Heusler phase Mn2FeSi,...
Roughness of Face-Milled Surface Topography in Directions Relative to the Feed Movement
Antal nagy, jános kundrák.
By achieving the accuracy and roughness requirements imposed on the connecting surfaces of machine components –the topography created during machining – it is guaranteed to meet the operational requirements. We cannot ignore the fact that if connected milled plane surfaces move in different directions relative to each other during operation, there may be different contact conditions caused by the unevenness of the topography. The direction-dependent roughness irregularities and functional characteristics of the topography are not sufficiently explored, thus in this work we examine the roughness and its deviations by assuming displacements...
The Manufacturing of Environmental Barrier Coatings by HV-APS Plasma Spraying Using Er 2 O 3 and SiO 2 Powder Mixture
Paweł pędrak, tadeusz kubaszek, barbara kościelniak, marek góral, mateusz micał.
Over the last decades, nickel-based superalloys with TBC coatings have been used as the main material for hot section turbine parts. The next step in the development of engines and increasing the combustion temperature is the use of Ceramic Matrix Composites (CMC). Nevertheless, in the presence of water vapour or molten salts, accelerated degradation of substrate material. This problems can be pre-vented by additional layers or coatings produced on its surface, or combinations of layers and coatings that form Environmental Barrier Coatings (EBCs). The aim of the research was the preparation of sam-ples of a mixture of erbium oxide powders with silicon...
Analysis of Extrusion Process Parameters in PLA Filament Production for FFF Technology
Vojtech senkerik, martin bednarik, vaclav janostik, michaela karhankova, ales mizera.
Additive technologies are becoming a common part of not only prototype production, but also piece or small series production. However, the choice of technology and material plays a key role in the applicability of the manufactured parts. The most widespread type of additive technology is FFF technology, which consists of applying a fused plastic string in single layers. The resulting mechanical properties of parts produced using this technology depend not only on the material and structure selected, but also on the process parameters used in the printing process itself. This study deals with the production of filament from PLA, which is the primary...
The Effect of TiO 2 Layers on the Surface Properties of Materials
Jana šulcová, iveta papučová, jana pagáčová, andrej dubec, andrea feriancová, maroš dedinský, peter sukeľ.
One of the ways to improve or change the surface properties of materials is to apply thin layers. TiO2-based layers are used to protect surfaces against wear or atmospheric and thermal effects (anti-corrosion, anti-abrasive and anti-static layers). They are also used in optical coatings, on windows or glasses (anti-reflective, self-cleaning and conductive transparent layers), in healthcare and in households to ensure the cleanliness of surfaces. The work deals with the effect of TiO2 layers on the surface properties of selected substrates. The layers were prepared by the sol-gel method using the dip-coating technique on glass and stainless steel. The...
Optimization of Process Parameters for a Vertical Shaft Impact Crusher through the CFD-DEM Method
Ke sun, limei zhao, qitao long.
In this study, the process parameters of a vertical shaft impact (VSI) crusher are optimized. Different feed size distributions, material physical properties, and product size distribution requirements are considered to determine the optimal material particle bond cleavage ratio. First, a numerical model is developed to simulate the crushing effect by adopting a CFD-DEM method. Then, the relationship between the crushing effect and the rotor speed, feed size distribution, and feed rate is revealed by analyzing the bond cleavage ratio of smaller-size distribution feed crushing to the specified particle size. The optimized working parameters of the crusher...
The Effect of Strain Rate on the Friction Coefficient
Petr svoboda, miroslav jopek.
The Male and Cockroft ring compression test is one of the methods used to determine the coefficient of friction in forming. This method can be used to determine the coefficient of friction without the need to measure the force. This paper describes the results of the Male and Cockroft ring compres-sion test for the Hardox 450 material at different strain rates. The experiment was performed on ZD40 hydraulic press and CFA-80 pneumatic die hammer at the Faculty of Mechanical Engineering of Brno University of Technology. The test results were recorded in a calibration diagram. The results show that the strain rate has a significant effect on the coefficient...
Tribological Properties of 3D Printed Materials in Total Knee Endoprosthesis
Matus varhanik, josef sedlak, zbynek studeny, patricia janigova, felicita chromjakova.
The submitted paper deals with biotribological contact in total knee arthroplasty. The goal was to evaluate the influence of the metal component production technology on tribological parameters in defined environments. The reference sample was a standard available test ball made of the subject material, used in testing tribological properties by the "Ball on Pin" method. The preparation of the experiment consisted in the production of test disks from UHMWPE material and the production of a metal test component with a spherical surface. The condition of the experiment and the basis of this contribution is to compare the properties of conventionally...
Research on Linkage Accuracy of "Baby Hanging Basket" Five-axis Precision Machine Tool
Yuanyuan wu, huiling an, bo li, hua zhang, lai hu.
The "baby hanging basket" five-axis precision machine tool (BHBFPMT) studied in this study is mainly used to process open impeller and closed impeller in aerospace field. However, the linkage accuracy (LA) measurement of five-axis machine tool is one of the important detection means to ensure the tolerance requirements of precision parts. The mathematical model of linkage accuracy (LA) of "baby hanging basket" five-axis precision machine tool (BHBFPMT) was established. The accuracy of X, Y, Z, B and C axes was measured, respectively. Combined with the measurement results, a pulse compensation method was proposed to compensate the accuracy. The linkage...
Design Method of Cam Five-bar Paper Picking Mechanism of Packaging Machine Based on Position and Orientation Constraints
Ming-rui xue, jun ye, hong-qian hu.
The work aims to present a design method of cam five-bar paper taking mechanism of packaging machine based on position and orientation constraints to better meet the position and orientation requirements of the end paper taking actuator in the high-speed paper picking process. At the first stage, according to the given ideal position and orientation requirements of the end paper taking actuator, the mathematical model of the five-bar mechanism satisfying the position and angle constraints is established by using the kinematic mapping theory, and two cams are used to constrain the two freedom of the five-bar mechanism to obtain the cam five-bar paper...
Research on Piston Avoidance Valve Pit Milling Method
Changlong zhao, hongnan ma, qinxiang zhao, xiaoyu jia, haifeng zhang.
In order to improve the processing efficiency and surface quality of the piston avoidance pit, reduce labor costs, and make the processing of the piston avoidance pit meet the modern production re-quirements, it is realistic and feasible to combine Pro/E and Mastercam software to complete the processing of the piston avoidance pit. Two different kinds of piston pits are selected for machining, and the 3D model of the piston pits is established by Pro/E software, and the process preparation and parameter setting are realized by Mastercam software, and the NC machining simulation is con-verted into NC code to realize the machining of the piston pits;...
Cornell Chronicle
- Architecture & Design
- Arts & Humanities
- Business, Economics & Entrepreneurship
- Computing & Information Sciences
- Energy, Environment & Sustainability
- Food & Agriculture
- Global Reach
- Health, Nutrition & Medicine
- Law, Government & Public Policy
- Life Sciences & Veterinary Medicine
- Physical Sciences & Engineering
- Social & Behavioral Sciences
- Coronavirus
- News & Events
- Public Engagement
- New York City
- Photos of the Week
- Big Red Sports
- Freedom of Expression
- Student Life
- University Statements
Around Cornell
- All Stories
- In the News
- Expert Quotes
- Cornellians
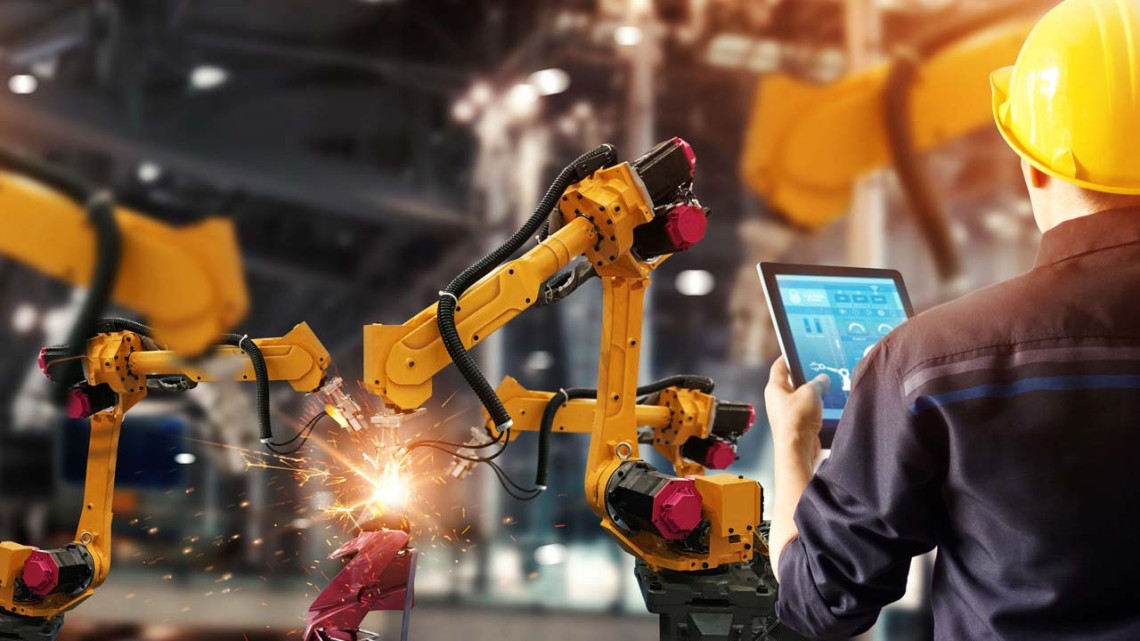
News directly from Cornell's colleges and centers
Research: Technology is changing how companies do business
By sarah mangus-sharpe.
A new study from the Cornell SC Johnson College of Business advances understanding of the U.S. production chain evolution amidst technological progress in information technology (IT), shedding light on the complex connections between business IT investments and organizational design. Advances in IT have sparked significant changes in how companies design their production processes. In the paper " Production Chain Organization in the Digital Age: Information Technology Use and Vertical Integration in U.S. Manufacturing ," which published April 30 in Management Science, Chris Forman , the Peter and Stephanie Nolan Professor in the Dyson School of Applied Economics and Management , and his co-author delved into what these changes mean for businesses and consumers.
Forman and Kristina McElheran, assistant professor of strategic management at University of Toronto, analyzed U.S. Census Bureau data of over 5,600 manufacturing plants to see how the production chains of businesses were affected by the internet revolution. Their use of census data allowed them to look inside the relationships among production units within and between companies and how transaction flows changed after companies invested in internet-enabled technology that facilitated coordination between them. The production units of many of the companies in their study concurrently sold to internal and external customers, a mix they refer to as plural selling. They found that the reduction in communication costs enabled by the internet shifted the mix toward more sales outside of the firm, or less vertical integration.
The research highlights the importance of staying ahead of the curve in technology. Companies that embrace digital technologies now are likely to be the ones that thrive in the future. And while there are still many unanswered questions about how these changes will play out, one thing is clear: The relationship between technology and business is only going to become more and more intertwined in the future.
Read the full story on the Cornell SC Johnson College of Business news site, BusinessFeed.
Media Contact
Media relations office.
Get Cornell news delivered right to your inbox.
You might also like
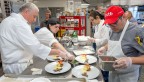
Gallery Heading
Design for manufacturing and assembly methods in the product development process of mechanical products: a systematic literature review
- Critical Review
- Open access
- Published: 14 March 2022
- Volume 120 , pages 4307–4334, ( 2022 )
Cite this article
You have full access to this open access article
- Giovanni Formentini ORCID: orcid.org/0000-0002-2321-6723 1 ,
- Núria Boix Rodríguez 1 &
- Claudio Favi 1
13k Accesses
20 Citations
Explore all metrics
This article has been updated
The design for manufacturing and assembly (DFMA) is a family of methods belonging to the design for X (DfX) category which goal is to optimize the manufacturing and assembly phase of products. DFMA methods have been developed at the beginning of the 1980s and widely used in both academia and industries since then. However, to the best of the authors’ knowledge, no systematic literature reviews or mapping has been proposed yet in the field of mechanical design. The goal of this paper is to provide a systematic review of DFMA methods applied to mechanical and electro-mechanical products with the aim to collect, analyse, and summarize the knowledge acquired until today and identify future research areas. The paper provides an overview of the DFMA topic in the last four decades (i.e., from 1980 to 2021) emphasizing operational perspectives such as the design phase in which methods are used, the type of products analysed, the adoption of quantitative or qualitative metrics, the tool adopted for the assessment, and the technologies involved. As a result, the paper addresses several aspects associated with the DFMA and different outcomes retrieved by the literature review have been highlighted. The first one concerns the fact that most of the DFMA methods have been used to analyse simple products made of few components (i.e., easy to manage with a short lead-time). Another important result is the lack of valuable DFMA methods applicable at early design phases (i.e., conceptual design) when information is not detailed and presents more qualitative than quantitative data. Both results lead to the evidence that the definition of a general DFMA method and metric adaptable for every type of product and/or design phase is a challenging goal that presents several issues. Finally, a bibliographic map was developed as a suitable tool to visualize results and identify future research trends on this topic. From the bibliometric analysis, it has been shown that the overall interest in DFMA methodologies decreased in the last decade.
Similar content being viewed by others
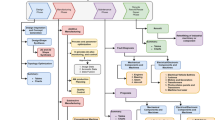
A comprehensive literature review of the applications of AI techniques through the lifecycle of industrial equipment
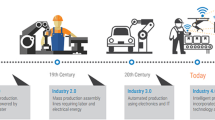
Literature review of Industry 4.0 and related technologies
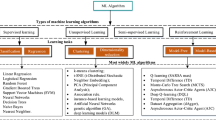
Applications of artificial intelligence in engineering and manufacturing: a systematic review
Avoid common mistakes on your manuscript.

1 Introduction
The design for manufacturing and assembly (DFMA) is a family of methods belonging to the design for X (DfX) category which goal is to optimize the manufacturing and assembly phase of a product. DfX methodologies are used to improve specific aspects of the product under development. The X is generally substituted with the optimization goal, and these methodologies are used to support the product development process (PDP). DFA is a systematic procedure aiming at the reduction of assembly time through the following actions: (i) reduction of the overall number of components in a given assembly and (ii) elimination of critical assembly tasks [ 1 ]. DFM is an engineering practice that seeks the simplification of the manufacturing process for cost reduction of a given component through the following actions: (i) selection of raw material type, (ii) selection of raw material geometry, (iii) definition of dimensional and geometrical tolerances, (iv) definition of roughness, (v) characterization of specific shape constraints based on the manufacturing process, and (vi) selection of secondary processing such as finishing [ 2 ].
DFMA methods have been around for many years. The first DFMA method is dated back to the 1980s since it was noticed that a positive impact is obtainable on the overall costs if the manufacturing and assembly phases were challenged. Among the several methods developed on this aim, three approaches have been mainly used in both academia and industry: (i) Boothroyd and Dewhurst (B&D) [ 3 ], (ii) Hitachi [ 4 ], and (iii) Lucas method [ 5 ]. Despite the quite long history of this subject, only a few papers present a literature review about DFMA methods. For instance, Gao et al. [ 6 ], Ginting et al. [ 7 ], and Wasim et al. [ 8 ] proposed a review of DFMA methods in the building sector which shows different features compared with the mechanical products considered in this review. Regarding mechanical products, four reviews were focused on DFM methods [ 9 , 10 , 11 , 12 ], six on DFA methods [ 13 , 14 , 15 , 16 , 17 , 18 ], and four on DFMA methods [ 19 , 20 , 21 , 22 ]. By the analysis of these works, three main limitations have been identified. The first one concerns the fact that the majority of reviews are dated (conducted more than 15 years ago), and missing information about current DFMA methods and trends is noticed. The second one deals with the fact that some reviews have been published in conference proceedings and only limited outcomes are provided. Finally, the third limitation concerns the review methodology. The available reviews lack a systematic approach, not allowing the reproducibility and replicability of the review process. Although DFMA methods are widely used in both industrial and academic fields, there are no recent reviews on this topic for mechanical applications.
The goal of this paper is to provide a systematic review of DFMA methods applied to mechanical products. The systematic review was conducted to collect, analyse, and summarize the knowledge acquired until today, as well as to identify future research areas, following the results of relevant research works on this subject to answer specific research questions. Two clusters of research questions were identified by the authors: general questions (GQs), and focused questions (FQs). Each cluster presents a list of questions that are used to drive the review and to identify specific topics associated with the DFMA subject. The following topics were covered by this review: (i) the industrial fields and the type of products covered by DFMA methods, (ii) the mapping of the DFMA methods in relation to the product development phases, (iii) the identification of trends and challenges for DFMA methods, (iv) the metrics used to analyse the results of DFMA methods, (v) the design tools implemented in compliance with DFMA methods, and (vi) the use of Industry 4.0 enabling technologies in the development of DFMA methods.
In the following section, Sect. 2 , the method proposed to perform the systematic mapping is described in detail along with the chosen research questions. Then in Sect. 3 , the outcome of the performed review is reported showing data used to answer the research questions. Section 4 explaining the limitations of the proposed review is presented, followed by a discussion of the obtained results in Sect. 5 . Finally, the last section, Sect. 6 , summarizes the outcome of the review and highlights future research trends for DFMA methods.
2 Materials and methods
The method used to conduct the study is composed of five phases: (i) definition of the research questions, (i) definition of the search process, (iii) definition of criteria for article selection, (iv) execution of data extraction and classification, and (v) execution of the analysis The following part of this section describes each phase in detail, including how the literature review was performed.
2.1 Definition of research questions
For the development of this review, the following questions were obtained with a top-down approach. Research questions concerning DFMA methods were divided into two clusters GQs and FQs. The first cluster gives an overview of the research field, providing specific application fields and design phases in which DFMA methods have been applied the most, including future challenges of the studies that employ DFMA methods. The second cluster analyses technical aspects of DFMA methods, such as the method type, the tool used for computational reasons, and if Industry 4.0 enabling technologies were implemented. Table 1 reports the research questions defined for this review.
2.2 Definition of search process
Since the first research activities and applications about DFMA methods are dated back to the early 1980s, this review was conducted considering all papers published between 1980 and 2021. The research process was performed on four databases: (i) Scopus, (ii) Elsevier, (iii) Taylor & Francis, and (iv) Emerald, which were considered the most coherent publishers in the engineering sciences by the authors. The queries were filtered by authors, abstract, and keywords, when possible. Table 2 summarizes the filtering items used for each database.
The definition of keywords was performed iteratively due to the high number of papers resulting from the first database querying. To obtain a manageable number of articles, three filtering steps were performed as reported in Fig. 1 . Initially, general keywords such as “Design,” “Manufacturing,” “Assembly,” and “for” were collected with the operator “AND.” Moreover, to broaden the research and mitigate possible errors, synonyms were considered (i.e., “Manufacturability,” “Production,” “Manufacture,” “Assemblability,” and “Installation”). The second step was performed to narrow results, and the two keywords “Assembly” and “Manufacturing” were combined using the operator “AND” (e.g., “Assembly AND Production,” “Assembly AND Manufacture”). Finally, the last filtering step consisted in the introduction of new keywords to reduce the overall number of results trying to target only mechanical-related articles. The acronyms “DFA,” “DFM,” and “DFMA” were added to the previous keywords with the operator “AND.”
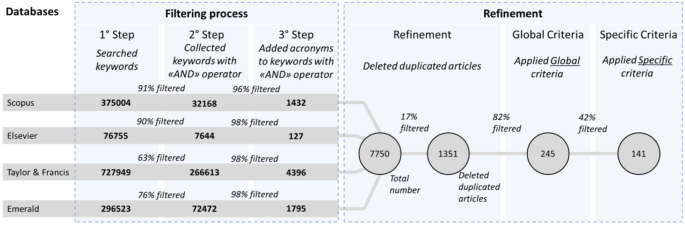
Filtering process and refinement steps
2.3 Definition of criteria for article sorting
After the initial search process, articles were skimmed with a three-step process: (i) identification and elimination of duplicated articles, (ii) use of global exclusion criteria to select articles related to the field of interest, and (iii) use of specific criteria (SC) to select only the most representative articles. Both criteria (GC and SC) used for the exclusion process are reported in Table 3 .
A quality assessment process was not performed, and all the retrieved papers were kept for the review process. At the end of the article selection, 141 articles were kept and analysed. The overall selection process is represented in Fig. 1 .
2.4 Execution of data extraction and classification
Data extraction and classification allowed for retrieving key information from the articles selected for the analysis using a structured framework. The data extraction framework (Table 4 ) is composed of items according to the type of research question they are answering.
2.5 Execution of analysis
The execution of analysis was performed with the help of the framework provided in the previous step (Table 4 ). In relation to the general questions, the first topic concerns the identification of the specific field in which DFMA methods have been applied for years. Fields were divided into general (i.e., electronic, and mechanical) and specific (i.e., sensors, automotive aerospace, industrial). To further support this classification, the product complexity was identified. In this paper, a product is considered complex if it has a medium-long lead time and it is difficult to handle (i.e., due to weight, dimensions, or a high number of components), while a simple product has a short lead time and is made by few components (i.e., less than sixty). The second topic concerns the identification of the design phase in which DFMA is applied (i.e., conceptual design, embodiment design, and detail design). The detail design phase presents the most accurate and complete information regarding the product, while the conceptual design phase presents most generic data (e.g., functional information, product architecture). The third topic concerns the identification of future trends and challenges of DFMA methods in relation to the application field, product complexity, and design phase previously investigated.
On the other hand, in relation to the focused questions, the first topic refers to the DFMA method type, which can be quantitative or qualitative. A method is considered quantitative when it provides a numerical evaluation (e.g., the B&D DFMA method), while a method is qualitative when it provides suggestions and guidelines, not directly linked to numbers or mathematical equations (e.g., heuristics, guidelines). The second topic tackles the computational tool used to perform DFMA analysis. Three different types of tools were identified for this purpose: spreadsheets, software, and graph. The third topic analyses the application of advanced technologies with DFMA methods (i.e., the ones that currently characterize the enabling technologies of Industry 4.0).
2.6 Bibliometric analysis
A bibliometric analysis was performed to understand when and where papers regarding DFMA methods have been published. The analysis was performed considering four decades, and the overall result is shown in Fig. 2 . An exception was made for the last decade (i.e., D4) which considers a time span ranging from 2010 to 2021 to include all the latest publications. The first decade includes only four papers and it appears to be the lowest in terms of publications, while the second decade presents a high number of papers (48). The third decade presents 30 papers published for the DFMA field, and finally, the latest decade presents the highest number of papers, which is 59. Although the graph shows a scattered distribution of papers, ranging from 0 to 8 for each year, the mean value for the last three decades is approximately 4.3. This result highlights a homogeneous distribution of paper over time about DFMA.
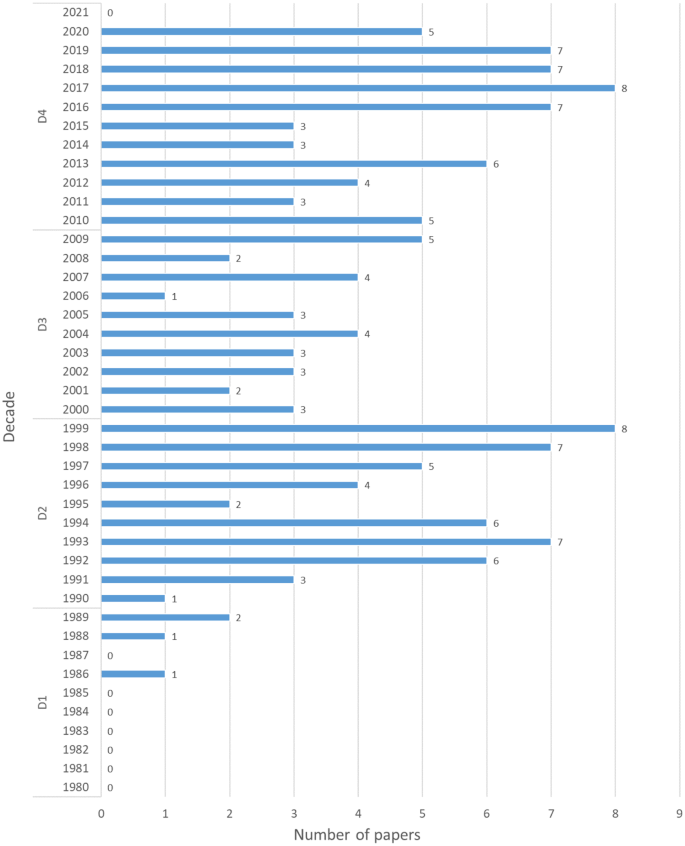
Number of papers vs. years
Both paper types published in journals and conference proceedings have been considered. Journals guarantee a stricter review process than proceedings following the time given to reviewers and the accessibility to scientific databases. Moreover, journals present more structured and mature research than conference proceedings. Additionally, a higher number of publications on conference proceedings indicate a considerable interest, since they present ongoing activities from different practitioners.
3 Results of the literature review
In this section, results of the literature review are presented following the two main groups of research questions previously identified.
3.1 Results related to the general questions
To answer the first general question, only papers in which a case study is presented have been analysed. The aim is to identify the industry’s field in which DFMA methods have been applied and the type of product analysed as a case study. On the other hand, to answer the second and the third general questions, all papers except reviews were considered. The aim is to understand in which phase DFMA methods are mainly applied, to identify the advantages/disadvantages of each design phase and to derive future research opportunities in the DFMA field.
3.1.1 Field of application and products analysed by DFMA methods
At the beginning of DFMA method development (early 1980s), articles were focusing on the conceptualization and description of DFMA methods, providing academic and exemplary case studies. During the 1990s, the application of DFMA methods in industries increased exponentially, particularly in the mechanical field. Starting from the second decade (D2), several case studies were provided to demonstrate the applicability of DFMA in mechanical and electro-mechanical products, and the same trend was confirmed in the following decades (D3 and D4). It is worth noting that most of the publications giving case studies have been implemented in the industrial field. The reason lies in the fact that several DFMA methods available in the literature are tested on generic products made of few components (i.e., dust filters, stapler, boiler) to validate the methods and their reliability. The number of papers presenting case studies in the automotive and aerospace fields is well balanced. Products analysed with DFMA methods are varying from sub-assemblies of a car (i.e., the suspension system, brake and clutch) to aircraft systems (i.e., pilot instrument panel, contactor assembly). Only a few articles tried to tackle the assemblability of a whole product; among them, Thompson et al. [ 23 ] tried to point out the relation between DFMA rules and late design changes in high-speed product development (i.e., circulator pumps for the commercial building services market). Gerding et al. [ 24 ] tackles the problem of implementing DFMA rules in long-lead-time products (i.e., aircraft), while Barbosa and Carvalho [ 25 , 26 ] proposed DFMA rules to optimize the assembly phase of an aircraft through re-design actions. Figure 3 shows the distribution of papers according to the type of product, the general field, and the specific field of application.
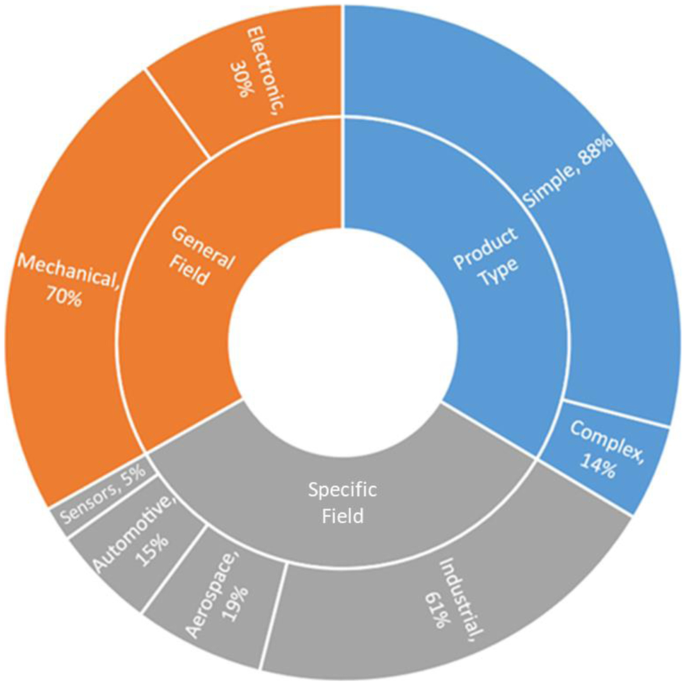
GQ1 data distribution
To understand the interest of the topic over time, the publications’ year was analysed together with the type of publication (i.e., journal or conference proceeding). Results of this analysis are summarized in Fig. 4 . Papers describing DFMA applications on both complex and simple products have increased over the years. It is interesting to notice that most of the articles proposing DFMA methods for complex products have been published in the last two decades (D3 and D4). This trend may be justified by several reasons. The first one concerns the fact that more and more industries are focusing on reaching a global improvement of their product, making the application of traditional DFMA challenging since the whole system must be considered. Another major factor in the development of DFMA methods for complex products concerns the increment of processing power that allows designers and engineers to handle a high amount of data in a limited timeframe, widening the boundary of their optimization problem from sub-parts to the whole system. The study of DFMA methods applied to simple products in the last three decades has increased as well. However, for the last decade (D4) most of the papers are published in conference proceedings and they present applications of already well-known DFMA techniques on different systems. Despite these works being useful to increase the number of case studies where DFMA methods are applied, they cannot be considered as research advancement in the DFMA methods. Other works published in conference proceedings are trying to extend DFMA principles in several ways. For example, Esterman and Kamath [ 27 ] attempted to apply DFMA to the improvement of assembly lines, Wood et al. [ 28 ] and Nyemba et al. [ 29 ] provided new design rules to cope with constraint production of the developing countries, and finally Favi et al. [ 2 ], Hein et al. [ 30 ], and Gupta and Kumar [ 31 ] included new principles and criteria for multi-objective analysis (i.e., cost, sustainability).
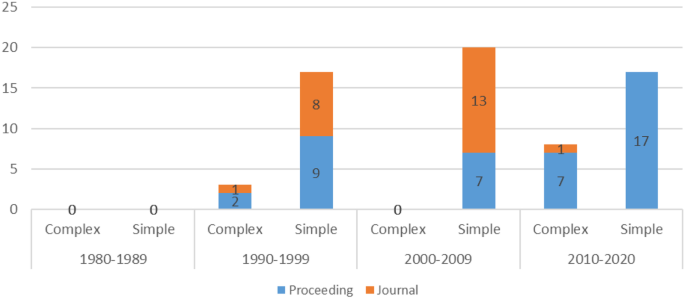
Distribution of papers per decade in relation to simple and complex products
The overall data collected about this topic are summarized in Table 7 in the Appendix . From the performed analysis, DFMA methods have been mainly applied on simple products or sub-assemblies, in which all parts are made with traditional production technologies (i.e., fusion, sheet metal stamping and bending, forging). DFMA analysis evaluates assembly solutions adopted in the analysed products. Assembly solutions are generally bolted joints, more rarely welded or riveted joints. The main goal of these analyses is to understand if it is possible to reduce the number of components which, typically, leads to a reduction of assembly time [ 19 ]. As an outcome, the typical product analysed using DFMA techniques is a simple product assembled manually with bolted joints made of less than 60 parts. Another interesting result concerns the fact that sub-assemblies are considered rather than the whole product. This result leads to the application of DFMA methodologies in a limited context (i.e., the companies which are designing and manufacturing sub-assemblies) making effective the benefits of DFMA for suppliers. In this scenario, each module (sub-assembly) is assembled with a specific assembly technology, making the overall analysis easier to manage. For instance, a car engine is assembled with bolted joints and chassis are assembled with welding technologies. If the assembly technology varies, then the DFMA analysis becomes more challenging and, consequently, the overall final improvement might not have an elevated positive impact as the sub-systems improvements might have.
3.1.2 Product design phase challenged by DFMA methods
According to Pahl et al. [ 32 ], the PDP process can be divided into conceptual design, embodiment design, and detail design. For each phase, different information and tools are available to support designers in the definition of the product. The conceptual design phase represents the initial phase of the product development process, in which only general information (e.g., product functions, product architecture) is available. The embodiment phase represents a more mature phase of a project in which a preliminary product layout is available. Generally, this design phase is linked with the use of 3D CAD drawings. Finally, the detail design phase represents the step with a higher level of detail. Specific information is available at this phase, such as the number and type of screws, assembly procedures, assembly sequence, and takt time. In this phase, detailed drawings are made to fully describe the product for the manufacturing process. Together with the information granularity, also the cost of changes varies according to the design phase in which modifications are introduced. With the aim to analyse this topic, all papers except reviews have been considered. The analysis of the literature shows that DFMA methods are mainly used during detail and embodiment design phases (Table 7 in the Appendix ). Indeed, considering the most spread DFMA methods (i.e., B&D and Lucas method), the analysis is performed starting with detailed design information. Among the analysed papers, a large part of them tried to use DFMA methods at the embodiment phase by reducing the need for specific information. For instance, Sanders et al. [ 33 ] proposed a knowledge-based system to optimize products without detailed information, while Samadhi et al. [ 34 ] tried to develop a fully automated DFMA method, linked to a 3D CAD modeller, enabling to extract data related to the product under development. The application of DFMA methods at the late design phase is in line with the idea of DFMA since most of the methodologies have been developed as a systematic approach, whose aim is to optimize the product through different design iterations (incremental improvement through product re-design). However, several problems arise working at the late design phases such as the high cost of change. Since the beginning of the advent of DFMA methods, some studies tried to move the analysis from the detail design phase to the conceptual design phase. Among these, the paper proposed by Rampersad [ 35 ] was one of the first to investigate DFMA methods from a relational point of view, to understand how design variables affect product assembly. A more recent attempt was performed by Emmatty and Sarmah [ 36 ] that tried to merge DFA and DFM techniques with product architectures analysis. Across the collected works, only two works proposed to integrate the TRIZ methodology and the DFMA to widen the solution space, which is a typical task of conceptual design [ 37 , 38 ]. The typical output of DFMA methods in the conceptual design phase is a product architecture with optimized performance in terms of assembly. Functional modules, interconnections, and related parameters are considered in the DFMA analyses to identify installation and assembly issues. For instance, the position, the attachment points, the overall number of the functional modules, and/or the interface route among modules are some of the parameters considered in the developed DFMA methods conceived for the conceptual design phase. Hence, DFMA analysis performed at the conceptual design phase focuses on the module rather than the physical components and provides product optimization through module arrangement and layout inside the product (i.e., product architecture). When DFMA analyses are conducted at the detail or embodiment design phase, the typical output is again a product with optimized assembly performances, but the focus concerns the components/parts. DFMA tools aim at improving the product assemblability by reducing the overall number of components, minimizing the number of fixations (i.e., screws, rivets), standardizing the type of fixations, reducing the part re-orientation during the manual operations, and choosing the most appropriated manufacturing technology among others. Hence, DFMA analysis performed at the embodiment/detail design phases focuses on the physical component providing a product optimization through the improvement of component shape, features geometries, and manufacturing aspects. It is interesting to notice that in the last decade, the efforts to propose DFMA methods applicable at the conceptual design phase have been increased for both simple and complex products.
3.1.3 Future challenges to address by using DFMA methods
From the extracted data, most of the papers are dealing with the improvement of simple products at the detail design phase. The analysis shows also how the DFMA evolved integrating new objectives (e.g., ergonomic and environmental aspects) and multi-attribute analysis. On the other hand, the research activity related to DFMA methods shifted towards the analysis of complex products, and an increased interest in the conceptual design phase was noticed. To cite a few, Remirez et al. [ 39 ] tried to adapt the B&D DFMA methodology to tackle the assembly issues of a solar tracker, while Mora et al. [ 40 ] adapted the design structure matrix method to work with large size products (i.e., elevators, wind turbines, solar plants, pilot plants, or petrochemical facilities). With the same aim Formentini et al. [ 41 ] provided a method to collect design guidelines to optimize the aircraft architecture at the conceptual design phases. The transition of DFMA analysis towards the early design phases emerged as a trend to be investigated in future years. This trend emphasizes the need to shift the DFMA paradigm by establishing a systematic optimization method that may be used at the conceptual stage, when degrees of freedom are larger, to achieve the right first time design [ 19 ], before moving on to the later design phases. Another aspect that characterizes DFMA studies of products with a certain complexity is the high number of data required for the analysis and computational time needed to perform the analysis. To summarize the outcome of the literature analysis, an increasing interest in the development of DFMA methods for complex products is raising in the scientific community. However, there is no evidence stating that DFMA methods provide better benefits to complex rather than simple products. Based on the revised papers, a high number of manuscripts presented applications of DFMA methods on simple products. This trend may be justified by the fact that on simple products, DFMA results can be validated and tested through product prototypes. Moreover, the application of DFMA analysis on simple products is in line with the concept of incremental innovation. In this respect, DFMA techniques were applied to product sub-systems (or sub-assemblies, which indirectly provides an overall optimization of the product. The application of DFMA analysis on the entire product, especially when it is complex, may generate different outputs and might lead to radical innovation in terms of assembly performances. To date, there is no evidence about a direct comparison (e.g., DFMA index assessment between a complex product developed with DFMA criteria and the same product in which the DFMA principles were applied to sub-assemblies. This lack lies in the needs of industry where usually sub-systems are provided by different suppliers,thus, there is no interest in investigating the product assemblability as a whole system. This perspective is currently not addressed within the literature and represents an opportunity for further research. Another upcoming challenge for DFMA is the need to integrate DFMA analysis with other design aspects (multi-objective analysis, creating engineering design methodologies that consider multiple aspects. For instance, ergonomic analysis is important to guarantee the assembly optimization of the product. Boothroyd [ 19 ] already considered the ergonomic aspect in his approach,however, it was considered in relation to the operator in the assembly line, where small products are handled. Moving towards bigger and complex products, the assembly process requires the operator to actively adapt to the working space and environment, and different ergonomic parameters need to be considered, such as working position, the access to the place where activities are performed, and ergonomic operator posture among others [ 42 ].
3.2 Results related to the focused question
To answer the focused questions, only a proper subset of papers was analysed for each topic with the aim to explore specific aspects related to the type of DFMA methods. These specific topics concern the type of tools used for the analysis, as well as the enabling technologies used to implement DFMA in modern industries.
3.2.1 Qualitative vs. quantitative DFMA methods
DFMA methods can be clustered into different categories: qualitative and quantitative. A method is considered quantitative when it provides numbers and indicators (i.e., metrics) to evaluate the goodness of a product from the assembly and manufacturing point of view. According to this definition, quantitative methods have been widely used as engineering design tools [ 11 ]. An example of the DFMA quantitative method is the B&D method. On the other hand, a method is considered qualitative when it provides an evaluation of the product manufacturability and assemblability using design practice derived from experience. Qualitative methods are usually providing design suggestions, rules, and guidelines without the adoption of numerical metrics. Dealing with the study of qualitative vs. quantitative DFMA methods, the analysis was performed looking at all papers except the reviews and papers oriented to the plant management. Results show that three quarters of the papers are proposing quantitative approaches, while only a one quarter studied qualitative approaches. Among all, only two papers tried to provide a method that can be considered both qualitative and quantitative [ 43 , 44 ]. Table 5 reports the main types of information required to perform DFMA analysis, in relation to quantitative and qualitative methods. Despite some inputs being shared among quantitative and qualitative methods (e.g., number of parts), the main outputs are different.
From the performed analysis, the most-used inputs for DFMA indices are assembly time (s), material cost ($), and number of parts (#). DFMA indices for quantitative methods have all the same root, which is providing a score based on the identified product parameters (input data). According to the type of parameters and the developed method, the DFMA index can assume a different meaning. For instance, the most popular DFA index from the B&D approach (also known as design efficiency) is computed by the following equation [ 19 ]:
NM = theoretical number of parts is an estimation concerning the number of essential parts of the product derived by the optimization process proposed by the method,
TM = total assembly time is the overall assembly time of the product measured with experimental tests.
The DFA index gives an overall assessment of the product assemblability performance (dimensionless index). The DFA index can be applied to different products, and it is based on values derived from standardized tables. Differently from DFA index, the total grade indices allow considering both DFA (total grade of the assembly) and DFM (total grade of the part) [ 45 ]. The method identified a list of product parameters for the manufacturing assessment (billet, work material, features, machine accessibility, etc.) and for the assembly assessment (i.e., billet dimension, part handling, assembly fixtures, tolerance and clearance) providing a weight for each parameter (from 0 to 10). Following a value engineering approach, a score of 0 is assigned if the parameter is not critical for the manufacturing/assembly, while 1 is assigned if the parameter affects the manufacturing/assembly process. Total grade indices are obtained by multiplying the weight of each parameter with the score associated with the considered parameter and finally by making an overall sum. The lower the total grade of the part and the assembly is, the more efficient the product is from the manufacturing and assembly perspectives. Both DFA index and total grade of the assembly/part are quantitative.
Regarding qualitative DFMA methods, the general outcome is a list of items (i.e., rules, graph, guidelines) in which design suggestions to improve product manufacturability and assemblability are collected. For instance, the design structure matrix (DSM) is a well-known tool to represent product architectures. DSM representation helps designers to create products with enhanced manufacturing and assembly properties. Qualitative DFMA methods can also provide a performance index, which is used to assess the improvement obtained by the implemented design actions. According to the method used, the performance index is derived using different inputs (e.g., the initial number of components/final number of components, initial cost/final cost) and it provides a rough estimation of the benefits introduced by the implementation of the design guidelines.
Regardless the fact that a DFMA index is quantitative or qualitative, the analysis showed that DFMA indices can be divided into two groups: time-based and feature based. Time-based DFMA indices rely on tables to convert time-related assembly parameters into scores. Tables are derived through extensive experiments. The main drawback of these indices is the complexity to personalize these tables on a specific product (e.g., complex products). On the other hand, feature-based DFMA indices rely on tables to convert assembly-related features into scores. Tables are derived through knowledge formalization techniques. These types of indices allow personalising tables on the product analysed but require a great effort to be set up and they may be subjected to bias. As an outcome of the literature review, the definition of a general DFMA index which can be adopted for every type of product or system can present several issues. A trade-off among analysis accuracy, available time, and availability of data must be reached and the proper DFMA index selected accordingly.
Another interesting area of investigation regards the type of DFMA method versus the design phase at which it is used. Figure 5 presents the data collected from the analysis of the qualitative/quantitative DFMA methods versus the design phase.

Distribution of quantitative and qualitative methods in relation to the design phase
Quantitative methods appear to be widely used at the late design phase. This result is in line with the available information, which is mainly numerical. Moving towards the early design phase (i.e., conceptual design), a great effort was done to develop new methods to study manufacturing and assembly aspects with less information. Among the DFMA methods focusing on the early stage of the design process, the majority of them are quantitative. This is an interesting outcome since no quantitative information is available in this design phase. For instance, Jung and Billatos [ 46 ] examined some elements of intelligent design systems to assess manufacturability of a product through the development of a knowledge based expert system for assembly. The knowledge base has been acquired from design for assembly along with axiomatic design concepts with emphasis on the conceptual design stage where the structure of the product as a whole is considered. Dagman and Söderberg [ 47 ] proposed to use axiomatic design principles to analyse and improve product architecture by the assessment of manufacturing, assembly, and disassembly parameters during the early design phase. Both methodologies, which are based on axiomatic design, are quantitative and use matrices to link functional requirements with design parameters. Favi et al. [ 48 ] proposed a method to perform a multi-objective optimization in terms of assembly, materials, processes, costs, and times at the conceptual design phase. The analysis was performed at the product architecture level, using product modules and design solutions derived with the help of the morphological matrix. In the mentioned work, all parameters required for performing the DFMA analysis were supposed from an already existing product. A similar approach was proposed by Formentini et al. [ 41 ], Favi et al. [ 49 ], and Bouissiere et al. [ 50 ] for the study of product architecture assembly performances for systems installation of a commercial aircraft.
3.2.2 Tools used to support DFMA methods
Concerning the development of engineering tools able to support the DFMA analysis of mechanical products, only a subset (74) of papers addressed this topic. Three different types of tools were identified by the analysis of the literature: graph, software, and spreadsheets. Each tool was further classified according to the aim of the analysis: (i) redesign suggestions, (ii) guidelines collection, (iii) metrics computations, and (iv) method integration. Redesign suggestions tool allows at the identification of redesign actions to improve the assemblability and manufacturability of the product under analysis. Guideline’s collection tool aims at transforming implicit knowledge into explicit one. Metric computation tool consists of the automatization of the computation of assembly and manufacturing parameters, and method integration tool describes the link with other engineering methods (i.e., FEM analysis). From the performed review, a dedicated software system is the main used tool, followed by spreadsheets and graphs (see Fig. 6 ). By the analysis of the type of software, research works presenting case studies are more willing to use commercial DFMA software (e.g., B&D commercial software) than an ad hoc developed software tool. Among commercial software tools, most of them were developed for metrics computations (i.e., assembly time, required assembly steps). The same trend is noticed for the spreadsheets. Only two papers are making use of graphs as tool for DFMA analysis. For example, Wu and O’Grady [ 51 ] suggested to use Petri-Nets to model CE aspects and make the application of DFMA techniques leaner, while Hsu and Lin [ 52 ] used graphs to integrate DFA, assembly functional presentation, and problem recommendation–driven mechanism. According to the performed analysis, spreadsheets and ad hoc software appear to be the most used tools. The use of spreadsheets lies in the accessibility and straightness in their use. They are the best choice when a method is not consolidated and only a few analyses were performed. Additionally, the software has been widely used to implement the DFMA method. Two types of software have been identified in the analysis: (i) ad hoc developed software and (ii) commercially available software. Generally, the development of software implies a greater effort in terms of time than commercial software or spreadsheets. The commercial software tools identified during the review concern both design tools and simulations tools (i.e., DFMA ® Boothroyd Dewhurst Software, Tecnomatix Dynamo, and Flexible Line Balancing Software). In other cases, the analysis was performed retrieving information from CAD tool, but no information was provided regarding the DFMA software used [ 53 , 54 ]. Moreover, it is interesting to analyse the use of tools versus the type of publication. Figure 6 shows that the use of spreadsheets is higher in the conference proceeding publications than the journal ones. Spreadsheets are mainly used to perform isolated analyses, while ad hoc software tools were developed to include methodological aspects within the novel DFMA framework which are more suitable for journal publications. Table 7 in the Appendix reports a summary of the outcomes related to this topic.
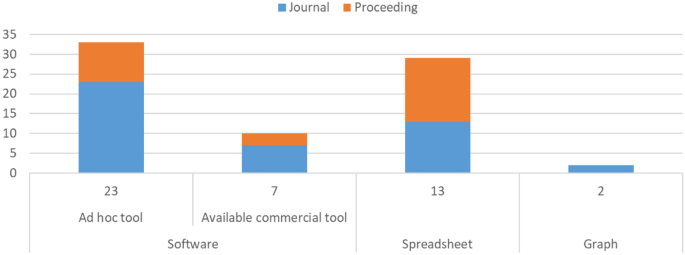
Tool vs. number and type of publication
3.2.3 Industry 4.0 enabling technologies challenging DFMA methods
The advances in Industry 4.0 provide both challenges and opportunities for digital manufacturing and assembly systems. Industry 4.0 aims at the development of a new generation of smart factories grounded on the manufacturing and assembly process digitalization. Most of the Industry 4.0 enabling technologies are related to digitization, data management, and connectivity, and they are dependent on solid data acquisition technologies. For the purpose of this review, not all the enabling technologies have been considered (Fig. 7 ) due to different reasons.
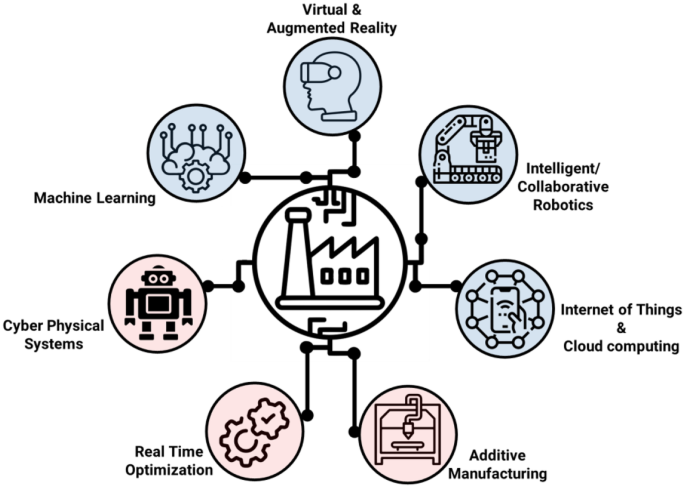
Enabling technology for Industry 4.0 (blue included in the review; red excluded)
The “additive manufacturing” technology was not studied since design methods called “design for additive manufacturing” have been specifically developed to consider this technology and they are not the goal of this review. The interested reader can find further information regarding DFAM methods in the review proposed by Wiberg et al. [ 152 ]. “Real-time optimization” and “cyber-physical systems” were not considered since they are mainly focusing on plant management rather than product design. For the aim of this review only “machine learning and AI,” “virtual and augmented reality,” “intelligent/collaborative robotics,” and “Internet of Things and cloud computing” were examined. In addition, a more detailed list of tools was identified for the technology “machine learning and AI,” including (i) expert system, (ii) fuzzy logic, (iii) genetic algorithm, and (iv) constraint-network approach. Among all the papers, only a few papers addressed the technology “machine learning and AI” proposing the use of the mentioned tools for the development of DFMA methods. The common goal of the analysed works is to eliminate the need for expertise to perform an assembly oriented design choice. The use of mathematical artefacts (e.g., artificial intelligence, genetic algorithms, expert system, fuzzy logic) allowed the collection of existing knowledge and the development of an automated system for knowledge sharing. Referring to the technology “virtual and augmented reality,” the idea was to use this technology in helping designers with the mock-up creation at the embodiment design phase facilitating the analysis of assembly operations (i.e., ergonomics). As regard the technology “Internet of Things and cloud computing,” only two discussed the applicability of these technologies for the DFMA analysis. Both manuscripts tried to move DFMA analysis in a cloud environment to get access to more case studies, more data, and the possibility to share assembly/manufacturing knowledge on past projects. Finally, even though there are several papers presenting methodologies to consider automatic assembly, no papers were found for the technology “intelligent/collaborative robotics.” Automatic assembly was generally not analysed through the means of DFMA, and the design of robotic cells and lines is usually customized to build a specific product and/or product family [ 104 ]. Industry 4.0 technologies brought a new paradigm for industries and manufacturing companies including a different way to collect, process, and elaborate data, as well as the production of customized products. The idea ground pinning the adoption of these technologies for DFMA purposes is to reduce the risk of implementing wrong design actions, and it helps to select the right modification among a pool of options. For example, Internet of Things can support DFMA analysis collecting data through several sensors placed directly on the product or the assembly line. Machine learning techniques can make use of past data, and the analysis of implemented design actions to suggest the right design action to implement in a given time. Machine learning processes can be used also to drive the product optimization following a multi-objective analysis to address different design goals (i.e., DfX). The cloud computing can open new possibilities in terms of data sharing by using virtual servers to collect and process data. The idea of cloud computing is in line with the concept of open manufacturing introduced by Kusiak [ 153 ] allowing different stakeholders to share data and optimize the manufacturability of their products in different contexts and countries.
As previously introduced, virtual and augmented reality can enable the investigation of ergonomic aspects during the assemblability process and the optimization of manual assembly operations. Exploring the product in a virtual environment, it is possible to highlight ergonomic issues (i.e., wrong operator position, impossibility to access to a particular product area) and solve them before the product is finalized. Moreover, operators can be trained before the product is physically available, reducing the time required for the in-process learning curve, cost of training, and consequently time to market.
By following the bibliometric analysis, the majority of works introducing Industry 4.0 enabling technologies are dated in the second and the third decades (D2 and D3). At that time, the concept of Industry 4.0 had not yet been formalized; therefore, all these studies can be considered as preparatory for the paradigm shift brought by the advent of Industry 4.0. When the concept of Industry 4.0 was introduced (beginning of 2010), the application of enabling technologies in relation to manufacturing and assembly aspects took a different research angle (from the product to the production site, i.e., plant management and production). This outcome has been validated by performing quick research with keywords “Industry 4.0 Design for Assembly” on main scientific databases. The retrieved papers are not focused on the design aspects of product assemblability anymore, but rather on the management of the assembly line and production site. In conclusion, traditional DFMA methods were not deeply investigated in relation to the Industry 4.0 enabling technologies.
4 Limitations
The literature analysis performed and presented in this paper shows few limitations that may affect the scope of the results and deserve to be introduced. The research process was performed systematically, identifying parameters and criteria to mitigate possible bias. The main limitation is identified by the adoption of a filtering process which uses criteria defined by the authors. For example, the exclusion criteria SC1 (articles not available for download) is not scientific and repeatable. In fact, according to the type of database and the institution’s accessibility, some articles excluded by the authors may be available for other users. In addition, this review focuses on scientific articles (both journal and conference papers), not considering, for example, thesis, book chapters, technical reports, commercial tools, and patents. Since DFMA is considered an applied science in the field of engineering, some interesting works developed outside the boundaries of the academic community could be excluded from this analysis. Finally, due to the high number of articles found, no other sampling techniques (e.g., snowball sampling) have been used to derive articles other than the one described.
5 Discussion
Through the analysis of the results related to general questions, it is possible to draw a discussion about the DFMA research done during the years. The critical analysis of results showed that DFMA methods have been mainly used for products made of few components and assembled with the same technology (i.e., bolted, welded). This outcome is in line with the idea of the early DFMA methods (e.g., Lucas, B&D) where an analysis of the assembly process is required for a given product to understand if can be optimized by eliminating/merging parts. Another interesting result considers the area in which DFMA methods are applied. Since this review is focused on DFMA methods for mechanical products, most of the presented case studies refer to the mechanical and electro-mechanical fields. In this scenario, only a few papers tried to tackle complex products (i.e., long lead time, heavy products, and characterized by a high number of parts). Several limitations were observed when a traditional DFMA method is applied to complex products such as the management of a high number of information as well as the inconsistency between manufacturability and parts integration which is the cornerstone of the DFMA.
The critical analysis of results in relation to the focused questions showed that regardless of the design phase at which DFMA methodologies were implemented, a continuous effort to derive quantitative methods was done since the beginning. Quantitative indices allow determining the performance of manufacturability and assembly for decision-making purposes. In addition, the use of numerical indices leads to a possible comparison between design alternatives, assessing the benefits introduced by novel design solutions. It was observed that the use of metrics and indices is suitable for the late design phases (embodiment and detail design) when numerical parameters are available with lower uncertainty. On the other hand, the assessment of quantitative results during the early phases of the PDP (conceptual design) requires defining specific boundaries and criteria for the field of interest. This limitation may affect the design solution space and the overall optimization process. This result leads to an open question “Is it possible to create quantitative DFMA methods applicable at the conceptual design phase, without limiting the available solution space?”.
The bibliometric study revealed the evolution of DFMA approaches’ interest through time (Fig. 8 ). The analysed works covered both conference proceedings and journals, showing an active interest in the subject by industries and academia. Results show that D2 and D4 present the highest production of papers. For the D3 decade, it seems that the interest in the DFMA subject decreased. This trend is primarily caused by the change of topics and paradigms associated with DFMA, creating a pool of methods very similar but with different names (i.e., installation, system integration, design for additive manufacturing). In the recent decade (D4), there was a rise in the overall number of publications compared to the previous periods. The reason may be the increase in publication rate in the scientific world; indeed, the National Science Board reported a study showing that the global research output grew about 4% annually over the last 10 years [ 154 ]. In conclusion, it is hard to claim that the research interest in DFMA methods increase in the last decade compared with the previous ones.
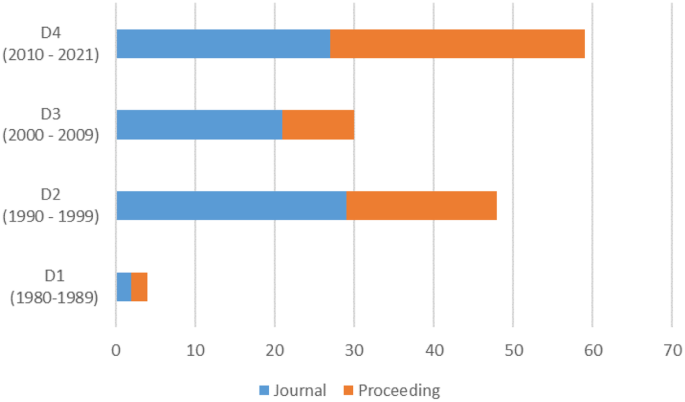
Overall distribution of papers (journal and conference proceedings) per decades
A map was developed utilizing a bubble graph to analyse and show interest in the DFMA issue through time and discover future trends (Fig. 9 ). The considered topics are collected in Table 6 .
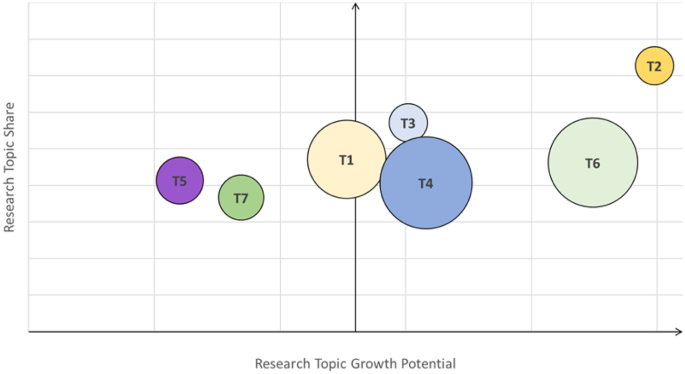
Bubble graph results (research topic share vs. research topic growth potential)
The size of the bubble represents the total number of publications for each topic during the period under consideration (i.e., decade D4). The Research Topic Share (RTS) is computed considering the overall number of papers divided for the number of papers of the last decade for a given topic. The Research Topic Growth Potential (RTGP) was computed by applying the least square method in relation to the number of publications per topic and year of the last decade (i.e., decade D4).
The graph is divided into two areas. The right side collects topics that have not been widely studied in the literature but are of high interest, while the left side reflects topics which are losing interest. According to the bubble graph, topics which have potential interest for further investigation are the topics T2 and T6 (i.e., DFMA methods applied to complex products and quantitative DFMA methods). The bubble size of T2 is small, and only a few papers are present in the literature that describes DFMA methods applicable to complex products. However, although many publications in the literature provide quantitative approaches (large bubble), this topic remains of interest, and the bubble T6 is on the right side of the graph when compared with qualitative methods (bubble T7). Another topic which is gaining interest is the development of DFMA methods applicable at early design phases (i.e., conceptual phase). This is represented by the bubble T3, which is small in size (i.e., few papers available in the literature) but located on the upper part of the right side of the graph. However, there is still a strong interest in DFMA methods applicable at late design phases (bubble T4 — embodiment and detail) confirmed by the number of papers developed on this topic. DFMA method applicable to simple products (T1) is a topic that is losing interest. Finally, it appears that the connection between DFMA methodologies and CAD systems is no longer of importance, and only a few papers in the last decade have been published on this topic. The reason could be technical and linked with the advent of the CAD systems that started to become popular at the beginning of the 1990s when numerous attempts were made to combine DFMA analysis with CAD systems. CAD tools are now widely used engineering systems for manufacturing industries, and research has shifted to other areas.
6 Conclusion
DFMA methods are widely used and well known in industries as in academia. To the best of the authors’ knowledge, no recent review on this topic was found, and the only papers that proposed a review of DFMA methods are dated and missing systematic analysis. The goal of this paper is to provide a systematic review of DFMA methods in the field of mechanical design. The review was conducted following the systematic approach. The papers were gathered from four databases (Scopus, Elsevier, Taylor & Francis, and Emerald), and a filtering approach was developed to exclude common review paper flaws. The obtained articles were categorized and analysed to answer the research questions proposed. Results show that DFMA methods have been mainly applied to simple products during the late design phase. This trend is in line with the early aim of DFMA methods, which is the optimization of product manufacturability and assemblability by considering a given technology. A few works attempted to shift the use of DFMA approaches from detailed to conceptual design phases. With this aim, it is required a change in the DFMA paradigm, moving from a systematic approach to a First Time Right method. The main tools used to do DFMA analysis are spreadsheets and ad-hoc software, which are often linked to CAD systems. Only a few authors have investigated the adoption of enabling technologies for Industry 4.0 for developing new DFMA approaches, such as artificial intelligence and virtual reality. This result leads to an important outcome which is the possibility to close the gap between design and manufacturing departments in modern industries following the Industry 4.0 paradigm. According to the articles reviewed, it is worth noting that performing DFMA analysis early in the design process could result in benefits such as increased solution space. Finally, research interest in DFMA approaches has dropped significantly in recent years, and this field needs to be revitalized. There are two possible reasons for this finding. The first one concerns the loss of appeal for young scholars in developing DFMA for consolidated manufacturing and assembly technologies. In this regard, the focus of researchers moved towards new technologies (i.e., additive manufacturing), and new challenges (i.e., system integration). The second one concerns the adoption of novel approaches able to suggest the right design the first time, proposing a multi-objective optimization of the product when the manufacturability is only one of the targets to be optimized.
The proposed work presents some limitations typical of review studies. The main limitation is identified in the filtering process. The exclusion of non-academic works (i.e., technical reports, commercial software) might have had led to the exclusion of relevant papers.
Availability of data and material
Not applicable.
Code availability
Change history, 20 july 2022.
Missing Open Access funding information has been added in the Funding Note.
Boothroyd G (1987) Design for assembly—the key to design for manufacture. Int J Adv Manuf Technol 2(3):3–11
Article Google Scholar
Favi C, Germani M, Mandolini M (2016b) A multi-objective design approach to include material, manufacturing and assembly costs in the early design phase. Procedia CIRP 52:251–256. https://doi.org/10.1016/j.procir.2016.07.043
Boothroyd G, Dewhurst P (1987) Product design for assembly. Boothroyd Dewhurst Incorporated
Leaney PG, Wittenberg G (1992) Design for assembling: the evaluation methods of Hitachi, Boothroyd and Lucas. Assem Autom
Lucas Engineering Systems Ltd (1993) Design for manufacture and assembly practitioners Manual, Version 10
Gao S, Jin R, Lu W (2020) Design for manufacture and assembly in construction: a review. Build Res Inf 48(5):538–550
Ginting R, Ishak A, Malik AF (2020) Product development and design with a combination of design for manufacturing or assembly and quality function deployment: a literature review. In: AIP Conference Proceedings, vol 2217, No 1. AIP Publishing LLC, p 030159
Wasim M, Vaz Serra P, Ngo TD (2020) Design for manufacturing and assembly for sustainable, quick, and cost-effective prefabricated construction—a review. Int J Constr Manag 1–9
Kuo TC, Zhang HC (1995) Design for manufacturability and design for “X”: concepts, applications, and perspectives. In: Seventeenth IEEE/CPMT International Electronics Manufacturing Technology Symposium. ‘Manufacturing Technologies-Present and Future’. IEEE, pp 446–459
Youssef MA (1994) Design for manufacturability and time-to-market, part 1: theoretical foundations. Int J Oper Prod Manag
Stoll HW (1986) Design for manufacture: an overview. ASME Appl Mech Rev 39(9):1356–1364. https://doi.org/10.1115/1.3149526
Carlsson M, Egan M (1994) Design for producibility in Swedish manufacturing industries. World Class Design to Manufacture
Sackett PJ, Holbrook AEK (1988) DFA as a primary process decreases design deficiencies. Assem Autom
Kuo TC, Huang SH, Zhang HC (2001) Design for manufacture and design for ‘X’: concepts, applications, and perspectives. Comput Ind Eng 41(3):241–260
Bogue R (2012) Design for manufacture and assembly: background, capabilities, and applications. Assem Autom
Booker JD, Swift KG, Brown NJ (2005) Designing for assembly quality: strategies, guidelines, and techniques. J Eng Des 16(3):279–295
Xia P, Lopes AM, Restivo MT (2013a) A review of virtual reality and haptics for product assembly: from rigid parts to soft cables. Assem Autom
Xia P, Lopes AM, Restivo MT (2013b). A review of virtual reality and haptics for product assembly (part 1): rigid parts. Assem Autom
Boothroyd G (1994) Product design for manufacture and assembly. Comput Aided Des 26(7):505–520
Agyapong-Kodua K, Darlington R, Ratchev S (2013) Towards the derivation of an integrated design and manufacturing methodology. Int J Comput Integr Manuf 26(6):527–539
Battaïa O, Dolgui A, Heragu SS, Meerkov SM, Tiwari MK (2018) Design for manufacturing and assembly/disassembly: joint design of products and production systems
Naiju CD (2021) DFMA for product designers: a review. Materials Today: Proceedings
Thompson MK, Jespersen IKJ, Kjærgaard T (2018) Design for manufacturing and assembly key performance indicators to support high-speed product development. Procedia CIRP 70:114–119
Gerding E, Granberry M, Parker R (1998) Keys to successfully implementing design for manufacturing and assembly (DFMA) techniques to an existing production program. In: AIAA and SAE, 1998 World Aviation Conference. p 5595
Barbosa GF, Carvalho JD (2013) Design for manufacturing and assembly methodology applied to aircrafts design and manufacturing. IFAC Proceedings Volumes 46(7):116–121
Barbosa GF, Carvalho J (2014) Guideline tool based on design for manufacturing and assembly (DFMA) methodology for application on design and manufacturing of aircrafts. J Braz Soc Mech Sci Eng 36(3):605–614
Esterman Jr M, Kamath K (2010) Design for assembly line performance: the link between DFA metrics and assembly line performance metrics. In: International Design Engineering Technical Conferences and Computers and Information in Engineering Conference, vol 44144. pp 73–84
Wood AE, Wood CD, Mattson CA (2014) Application and modification of design for manufacture and assembly principles for the developing world. In: IEEE Global Humanitarian Technology Conference (GHTC 2014). IEEE, pp 451–457
Nyemba WR, Muzoroza RK, Chikuku T, Mbohwa C (2017) Unlocking the economic value and potential of design for manufacture and assembly in a developing country for sustainability. In: 2017 IEEE International Conference on Industrial Engineering and Engineering Management (IEEM). IEEE, pp 1817–1821
Hein PH, Voris N, Dai J, Morkos BW (2018) Identifying failure modes and effects through design for assembly analysis. In: ASME 2018 International Design Engineering Technical Conferences and Computers and Information in Engineering Conference. American Society of Mechanical Engineers Digital Collection
Gupta M, Kumar S (2019) Design efficiency analysis towards product improvement using DFMA. In: 2019 8th International Conference on Modeling Simulation and Applied Optimization (ICMSAO). IEEE, pp 1–6
Pahl G, Beitz W, Feldhusen J, Grote K-H (2007) Engineering design: a systematic approach. Springer Science & Business Media
Sanders D, Tan YC, Rogers I, Tewkesbury GE (2009) An expert system for automatic design‐for‐assembly. Assem Autom
Samadhi TA, Ma’ruf A, Toha IS (2018) A framework for the development of automatic DFA method to minimize the number of components and assembly reorientations. In IOP Conference Series: Materials Science and Engineering, vol 319, no 1. IOP Publishing, p 012083
Rampersad HK (1996) Integrated and assembly-oriented product design. Integr Manuf Syst
Emmatty FJ, Sarmah SP (2012) Modular product development through platform-based design and DFMA. J Eng Des 23(9):696–714
Bariani PF, Berti GA, Lucchetta G (2004) A combined DFMA and TRIZ approach to the simplification of product structure. Proc Inst Mech Eng B J Eng Manuf 218(8):1023–1027
Cakir MC, Cilsal OO (2008) Implementation of a contradiction-based approach to DFM. Int J Comput Integr Manuf 21(7):839–847
Remirez A, Ramos A, Retolaza I, Cabello M, Campos M, Martinez F (2019) New design for assembly methodology adapted to large size products: application on a solar tracker design. Procedia CIRP 84:468–473
Mora B, Retolaza I, Campos MA, Remirez A, Cabello MJ, Martinez F (2020) Development of a new design methodology for large size products based on DSM and DFMA. In: Proceedings of the Design Society: DESIGN Conference, vol 1. Cambridge University Press, pp 2315–2324
Formentini G, Favi C, Bouissiere F, Cuiller C, Dereux PE, Guillaume R, Malchair C (2020) Extrapolation of design guidelines during the conceptual design phase: a method to support product architecture design. In: Proceedings of the Design Society: DESIGN Conference, vol 1. Cambridge University Press, pp 857–866
Judt D, Lawson C, Lockett H (2020) Experimental investigation into aircraft system manual assembly performance under varying structural component orientations. Proc Inst Mech Eng B J Eng Manuf 234(4):840–855
Sik Oh J, O’grady P, Young RE (1995) A constraint network approach to design for assembly. IIE Trans 27(1):72–80
Gupta S, Okudan GE (2008) Computer-aided generation of modularised conceptual designs with assembly and variety considerations. J Eng Des 19(6):533–551
Harik RF, Sahmrani N (2010) DFMA+, a quantitative DFMA methodology. Computer-Aided Design and Applications 7(5):701–709
Jung JY, Billatos SB (1993) An expert system for assembly based on axiomatic design principles. J Intell Rob Syst 8(2):245–265
Dagman A, Söderberg R (2012) Toward a method for improving product architecture solutions by integrating designs for assembly, disassembly, and maintenance. In: ASME International Mechanical Engineering Congress and Exposition, vol 45196. American Society of Mechanical Engineers, pp 377–387
Favi C, Germani M, Mandolini M (2016a) Design for manufacturing and assembly vs. design to cost: toward a multi-objective approach for decision-making strategies during conceptual design of complex products. Procedia CIRP 50:275–280
Favi C, Formentini G, Bouissiere F, Cuiller C, Dereux PE, Malchair C (2019) Design for Assembly in the Conceptual Development of Aircraft Systems. In: International Conference on Design, Simulation, Manufacturing: The Innovation Exchange. Springer, Cham, pp 268–278
Bouissiere F, Cuiller C, Dereux PE, Malchair C, Favi C, Formentini G (2019) Conceptual design for assembly in aerospace industry: a method to assess manufacturing and assembly aspects of product architectures. In: Proceedings of the Design Society: International Conference on Engineering Design, vol 1, no 1. Cambridge University Press, pp 2961–2970
Wu T, O’Grady P (1999) A concurrent engineering approach to design for assembly. Concurr Eng 7(3):231–243
Hsu HY, Lin GC (1998) A design-for-assembly-based product redesign approach. J Eng Des 9(2):171–195
Azevedo JGD, Arantes Filho AC, Costa LEVLD (2015) Fins module conception of the microsatellite launch vehicle based on design for manufacture and assembly method. J Aerosp Technol Manag 7(1):93–100
Robinson T, Friel I, Armstrong CG, Murphy A, Butterfield J, Price M, Marzano A (2018) Computer-aided design model parameterisation to derive knowledge useful for manufacturing design decisions. Proc Inst Mech Eng B J Eng Manuf 232(4):621–628
Gerhardt DJ, Hutchinson WR, Mistry DK (1991) Design for manufacture and assembly: case studies in its implementation. Int J Adv Manuf Technol 6(2):131–140
Matterazzo JP, Ardayfio DD (1992) Application of design for manufacture to the development of a new front suspension system (No. 922124). SAE Technical Paper
Ardayfio DD, Opra JJ (1992) Brake and clutch pedal system optimization using design for manufacture and assembly (No. 920774). SAE Technical Paper
De Fazio TL, Edsall AC, Gustavson RE, Hernandez J, Hutchins PM, Leung HW, ... Whitney DE (1993) A prototype of feature-based design for assembly
Jared GE, Limage MG, Sherrin IJ, Swift KG (1994) Geometric reasoning and design for manufacture. Comput Aided Des 26(7):528–536
Changchien SW, Lin L (1996) A knowledge-based design critique system for manufacture and assembly of rotational machined parts in concurrent engineering. Comput Ind 32(2):117–140
Kusiak A, He DW (1997) Design for agile assembly: an operational perspective. Int J Prod Res 35(1):157–178
Article MATH Google Scholar
Liang WY, O’Grady P (1997) Genetic algorithms for design for assembly: the remote constrained genetic algorithm. Comput Ind Eng 33(3–4):593–596
Barnes CJ, Dalgleish GF, Jared GEM, Swift KG, Tate SJ (1997) Assembly sequence structures in design for assembly. In: Proceedings of the 1997 IEEE International Symposium on Assembly and Task Planning (ISATP'97)-Towards Flexible and Agile Assembly and Manufacturing. IEEE, pp 164–169
Herrera A (1997) The effectiveness of design for manufacturing and assembly as applied to the design of the AH64D Helicopter. SAE transactions 346–352
Herrera A (1998) Design for manufacture and assembly, makes a difference among the boeing lean design initiatives (No. 981873). SAE Technical Paper
Ardayfio DD (1998) Improved design for manufacture in minivan body systems (No. 980748). SAE Technical Paper
Daabub AM, Abdalla HS (1999) A computer-based intelligent system for design for assembly. Comput Ind Eng 37(1–2):111–115
Appleton E, Garside JA (2000) A team-based design for assembly methodology. Assem Autom
Choi AC, Guda P (2000) Product design enhancement by integration of virtual design and assembly analysis tools. Assem Autom
Wang JH, Trolio M (2001) Using clustered assembly elements in the estimation of potential design for assembly benefits. Int J Prod Res 39(9):1885–1895
Hsu HY, Lin GC (2002) Quantitative measurement of component accessibility and product assemblability for design for assembly application. Robot Comput Integr Manuf 18(1):13–27
Edwards KL (2002) Towards more strategic product design for manufacture and assembly: priorities for concurrent engineering. Mater Des 23(7):651–656
Stauffer L, Rule R, Ren H (2003) A template for design for manufacture guidelines. In: ASME 2003 International Design Engineering Technical Conferences and Computers and Information in Engineering Conference. American Society of Mechanical Engineers Digital Collection, pp 35–42
Swift KG, Brown NJ (2003) Implementation strategies for design for manufacture methodologies. Proc Inst Mech Eng B J Eng Manuf 217(6):827–833
Bramall DG, McKay KR, Rogers BC, Chapman P, Cheung WM, Maropoulos PG (2003) Manufacturability analysis of early product designs. Int J Comput Integr Manuf 16(7–8):501–508
Coma O, Mascle C, Balazinski M (2004) Application of a fuzzy decision support system in a design for assembly methodology. Int J Comput Integr Manuf 17(1):83–94
Sulistiyowati WIWIK, Sari IKAS (2018) A new redesign idea for dust filter tool used in gerandong crackers manufacturing process based on Root Cause Analysis (RCA) and Design For Assembly (DFA) approach. J Eng Sci Technol 13(5):1384–1395
Google Scholar
Shetty D, Coimbatore V, Campana C (2005) Design methodology for assembly and disassembly based on rating factors. In: ASME International Mechanical Engineering Congress and Exposition, vol 42231. pp 575–581
Chang GA, Su CC, Priest JW (2006) CBR-DFMA: a case-based system used to assembly part design in the early design stage. In: ASME International Mechanical Engineering Congress and Exposition, vol 47748. pp 177–186
Xiao A, Seepersad CC, Allen JK, Rosen DW, Mistree F (2007) Design for manufacturing: application of collaborative multidisciplinary decision-making methodology. Eng Optim 39(4):429–451
Kazmer D, Roser C (2007) Analysis of design for global manufacturing guidelines. In: International Design Engineering Technical Conferences and Computers and Information in Engineering Conference, vol 48051. pp 901–911
Ma X, Kim M (2008) A systematic design for assembly method through the combination of subassemblies in product family. In: 2008 International Conference on Smart Manufacturing Application. IEEE, pp 261–266
Selvaraj P, Radhakrishnan P, Adithan M (2009) An integrated approach to design for manufacturing and assembly based on reduction of product development time and cost. Int J Adv Manuf Technol 42(1–2):13–29
Giudice F, Ballisteri F, Risitano G (2009) A concurrent design method based on DFMA—FEA integrated approach. Concurr Eng 17(3):183–202
Heemskerk C, de Baar M, Elzendoorn B, Koning J, Verhoeven T, de Vreede F (2009) Applying principles of design for assembly to ITER maintenance operations. Fusion Eng Des 84(2–6):911–914
Mo J, Cai J, Zhang Z, Lu Z (1999) DFA-oriented assembly relation modelling. Int J Comput Integr Manuf 12(3):238–250
Samy SN, ElMaraghy H (2010) A model for measuring products assembly complexity. Int J Comput Integr Manuf 23(11):1015–1027
Sarmento A, Marana E, Catalpa GF, Stoeterau R (2011) Design for assembly study case: automotive fuel intake cover (No. 2011–36–0046). SAE Technical Paper
Owensby E, Shanthakumar A, Rayate V, Namouz E, Summers JD (2011) Evaluation and comparison of two design for assembly methods: subjectivity of information inputs. In: International Design Engineering Technical Conferences and Computers and Information in Engineering Conference, vol 54860. pp 721–731
Annamalai K, Naiju CD, Karthik S, Prashanth MM (2013) Early cost estimate of product during design stage using design for manufacturing and assembly (DFMA) principles. In: Advanced Materials Research, vol 622. Trans Tech Publications Ltd, pp 540–544
da Silva CES, Salgado EG, Mello CHP, da Silva Oliveira E, Leal F (2014) Integration of computer simulation in design for manufacturing and assembly. Int J Prod Res 52(10):2851–2866
Suresh P, Ramabalan S, Natarajan U (2016) Integration of DFE and DFMA for the sustainable development of an automotive component. Int J Sustain Eng 9(2):107–118
Shetty D, Ali A (2015) A new design tool for DFA/DFD based on rating factors. Assem Autom
Sarmento A, Pereira ALJ, Lima L, Rodrigues L (2015) Design for assembly and design for manufacturing study case: mid-size pickup-box reinforcement application (No. 2015–36–0141). SAE Technical Paper
Harlalka A, Naiju CD, Janardhanan MN, Nielsen I (2016) Redesign of an in-market food processor for manufacturing cost reduction using DFMA methodology. Prod Manuf Res 4(1):209–227
Naiju CD, Warrier PV, Jayakrishnan V (2017) Redesigning of shopping cart for cost reduction using DFMA. In: MATEC Web of Conferences, vol 95. EDP Sciences, p 10003
Soh SL, Ong SK, Nee AYC (2016) Design for assembly and disassembly for remanufacturing. Assem Autom
Khalqihi KI, Rahayu M, Rendra M (2017) Design local exhaust ventilation on sieve machine at PT. Perkebunan Nusantara VIII Ciater using design for assembly (DFA) approach with Boothroyd and Dewhurst method. In: IOP Conference Series: Materials Science and Engineering, vol 277, no 1. IOP Publishing, p 012011
Dochibhatla SVS, Bhattacharya M, Morkos B (2017) Evaluating assembly design efficiency: a comparison between Lucas and Boothroyd-Dewhurst methods. In: ASME 2017 International Design Engineering Technical Conferences and Computers and Information in Engineering Conference. American Society of Mechanical Engineers Digital Collection
Alkan B, Vera D, Ahmad B, Harrison R (2017) A method to assess assembly complexity of industrial products in early design phase. IEEE Access 6:989–999
Gokul Kumar K, Naiju CD (2017) Early cost estimation of hand pressure mop using design for manufacture & assembly (DFMA). Int J Mech Eng Technol 8(9):167–172
Matthews S, Leminen V, Eskelinen H, Toghyani A, Varis J (2018) Formulation of novel DFMA rules for the advancement of ergonomic factors in non-linear iterative prototype assembly. Int J Comput Integr Manuf 31(8):777–784
Volotinen J, Lohtander M (2018) The re-design of the ventilation unit with DFMA aspects: case study in Finnish industry. Procedia Manufacturing 25:557–564
Desai A (2019) Ease of product assembly through a time-based design methodology. Assem Autom
Pișta IM, Nagîț G, Merticaru V, Rîpanu MI, & Cucoș M (2019) Analyses and redesign of a technological device for automated assembly, using design for manufacturing and assembly approach. In: IOP Conference Series: Materials Science and Engineering, vol 564, no 1. IOP Publishing, p 012058
Gulo CA, Rahayu M, Martini S, Kurniawan MI (2019) Design of dust collector on sorting machine vibro mesh type using design for assembly (DFA) approach with Boothroyd and Dewhurst method in PT. Perkebunan Nusantara VIII Ciater. In: IOP Conference Series: Materials Science and Engineering, vol 528, no 1. IOP Publishing, p 012009
Butt J, Jedi S (2020) Redesign of an in-market conveyor system for manufacturing cost reduction and design efficiency using DFMA methodology. Designs 4(1):6
Mohammad NN, Rosli MF, Fadzly MK, Salikan NSM, Effendi MSM (2020) Design for manufacturing and assembly (DFMA): Redesign of Joystick. In: IOP Conference Series: Materials Science and Engineering, vol 864, no 1. IOP Publishing, p 012212
Salikan NSM, Rosli MF, Mohammad NN, Abd Rahim I, Fadzly MK (2020) Design and analysis of grass cutting machine by using DFMA method. In: IOP Conference Series: Materials Science and Engineering, vol 864, no 1. IOP Publishing, p 012213
Miles BL (1989) Design for assembly—a key element within design for manufacture. P I Mech Eng D-J Aut 203(1):29–38
Marcoux P (1989) Using process dissection to achieve design for manufacturability for electronic assemblies. In: Proceedings. Seventh IEEE/CHMT International Electronic Manufacturing Technology Symposium. IEEE, pp 126–128
Miles B (1990) Design for manufacture techniques help the team make early decisions. J Eng Des 1(4):365–371
Molloy E, Yang H, Browne J, Davies BJ (1991) Design for assembly within concurrent engineering. CIRP Ann 40(1):107–110
Eversheim W, Baumann M (1991) Assembly-oriented design process. Comput Ind 17(2–3):287–300
Kim GJ, Bekey GA, Goldberg KY (1992) A shape metric for design-for-assembly. In: ICRA. pp 968–973
Li RK, Hwang CL (1992) A framework for automatic DFA system development. Comput Ind Eng 22(4):403–413
Lee S, Kim GJ, Bekey GA (1993) Combining assembly planning with redesign: an approach for more effective DFA. In: [1993] Proceedings IEEE International Conference on Robotics and Automation. IEEE, pp 319–325
Molloy E, Yang H, Browne J (1993) Feature-based modelling in design for assembly. Int J Comput Integr Manuf 6(1–2):119–125
Rampersad HK (1993) The DFA House. Assem Autom 13(4):29–36. https://doi.org/10.1108/eb004406
Venkatachalam AR, Mellichamp JM, Miller DM (1993) A knowledge-based approach to design for manufacturability. J Intell Manuf 4(5):355–366
Bryant RV, Laliberty TJ, Lapointe LJ (1994) DICE MO-a collaborative DFMA analysis tool. In: Proceedings of 3rd IEEE Workshop on Enabling Technologies: Infrastructure for Collaborative Enterprises. IEEE, pp 96–103
Fabricius F (1994) A seven-step procedure for design for manufacture. World Class Design to Manufacture
Sehdev K, Fan IS, Cooper S, Williams G (1995) Design for manufacture in the aerospace extended enterprise. World Class Design to Manufacture
Ufford DA (1996) Leveraging commonalities between DFE and DFM/A [environmental design]. In: Proceedings of the 1996 IEEE International Symposium on Electronics and the Environment. ISEE-1996. IEEE, pp 197–200
Sturges RH, Hunt DO (1996) Acquisition time reduction through new design for assembly heuristics. J Eng Des 7(2):195–208
Taylor GD (1997) Design for global manufacturing and assembly. IIE Trans 29(7):585–597
Chawla A, Ravi Raju K, Gupta A (1998) Expert system for DFM of die cast components. Journal-Institution of Engineers India Part Mc Mechanical Engineering Division 180–185
Schmidt S (1998) Preventive optimisation of costs and quality for the total life cycle - design for manufacture, assembly, service, environment (DFMA). SAE Tech Pap 982166. https://doi.org/10.4271/982166
Aurand SS, Roberts CA, Shunk DL (1998) An improved methodology for evaluating the producibility of partially specified part designs. Int J Comput Integr Manuf 11(2):153–172
Huang GQ, Mak KL (1999) Design for manufacture and assembly on the Internet. Comput Ind 38(1):17–30
Zha XF, Lim SY, Fok SC (1999) Integrated knowledge-based approach and system for product design for assembly. Int J Comput Integr Manuf 12(3):211–237
Hart-Smith LJ (1999) Design for assembly (DFA)—the key to making parts-count reduction profitable (No. 1999–01–2281). SAE Technical Paper
Gilson JF (1999) Globalization of the design for manufacturability/assembly process within the automotive wiring assembly business
Hu W, Poli C (1999) To injection mold, to stamp, or to assemble? A DFM cost perspective
Dalgleish GF, Jared GEM, Swift KG (2000) Design for assembly: influencing the design process. J Eng Des 11(1):17–29
Brown NJ, Swift KG, Booker JD (2002) Joining process selection in support of a proactive design for assembly. Proc Inst Mech Eng B J Eng Manuf 216(10):1311–1324
van Vliet HW, van Luttervelt K (2004) Development and application of a mixed product/process-based DFM methodology. Int J Comput Integr Manuf 17(3):224–234
Kamrani A, Vijayan A (2006) A methodology for integrated product development using design and manufacturing templates. J Manuf Technol Manag
Koganti R, Zaluzec M, Chen M, Defersha FM (2007) Design for assembly: an AHP approach for automotive front end component design evaluation (No. 2007–01–0522). SAE Technical Paper
Valentinčič J, Brissaud D, Junkar M (2007) A novel approach to DFM in toolmaking: a case study. Int J Comput Integr Manuf 20(1):28–38
Das S, Kanchanapiboon A (2011) A multi-criteria model for evaluating design for manufacturability. Int J Prod Res 49(4):1197–1217
Ong SK, Chew LC (2000) Evaluating the manufacturability of machined parts and their setup plans. Int J Prod Res 38(11):2397–2415
Osorio-Gomez G, Ruiz-Arenas S (2011) Integration of DFMA throughout an academic product design and development process supported by a PLM strategy
Moultrie J, Maier AM (2014) A simplified approach to design for assembly. J Eng Des 25(1–3):44–63
Read A, Ritchie J, Lim T (2016) A UNITY sketch-based modelling environment for virtual assembly and machining to evaluate DFMA metrics. In International Design Engineering Technical Conferences and Computers and Information in Engineering Conference, vol 50084. American Society of Mechanical Engineer, p V01BT02A049
Biesek FL, Ferreira CV (2016) A model for advanced manufacturing engineering in R&D technology projects through DFMA and MRL integration. In: Transdisciplinary Engineering: Crossing Boundaries. IOS Press, pp 705–714
Wahidin LS, Tan CF, Khalil SN, Tamaldin N, Sivarao S, Hu J, Rauterberg GWM (2016) A knowledge-based architecture framework of design for assemble system (DAEx). ARPN J Eng Appl Sci 11(4):2505–2507
Favi C, Germani M, Marconi M (2017) A 4M approach for a comprehensive analysis and improvement of manual assembly lines. Procedia Manufacturing 11:1510–1518
Murali GB, Deepak BBVL, Biswal BB (2017) A novel design for assembly approach for modified topology of industrial products. Int J Performability Eng 13(7):1013
Bader A, Gebert K, Hogreve S, Tracht K (2018) Derivative products supporting product development and design for assembly. Procedia Manuf 19:143–147
Wong JH, Sturges RH (1992) An extension of design for assembly methods for large and heavy parts. In: The Third International Conference on Computer Integrated Manufacturing. IEEE Computer Society, pp 148–149
Wiberg A, Persson J, Ölvander J (2019) Design for additive manufacturing—a review of available design methods and software. Rapid Prototyp J
Kusiak A (2020) Open manufacturing: a design-for-resilience approach. Int J Prod Res 58(15):4647–4658
NSB N (2020) Research and Development: US Trends and International Comparisons. Science and Engineering Indicators 2020
Download references
Open access funding provided by Università degli Studi di Parma within the CRUI-CARE Agreement.
Author information
Authors and affiliations.
Department of Engineering and Architecture, Università degli Studi di Parma, Parco Area delle Scienze 181/A, 43124, Parma, Italy
Giovanni Formentini, Núria Boix Rodríguez & Claudio Favi
You can also search for this author in PubMed Google Scholar
Contributions
All authors contributed to the study conception and design. Material preparation, data collection, and analysis were performed by Giovanni Formentini. The first draft of the manuscript was written by Giovanni Formentini, and all authors commented on previous versions of the manuscript. All authors read and approved the final manuscript.
Corresponding author
Correspondence to Giovanni Formentini .
Ethics declarations
Ethics approval, consent to participate, consent for publication, conflict of interest.
The authors declare no competing interests.
Additional information
Publisher's note.
Springer Nature remains neutral with regard to jurisdictional claims in published maps and institutional affiliations.
Rights and permissions
Open Access This article is licensed under a Creative Commons Attribution 4.0 International License, which permits use, sharing, adaptation, distribution and reproduction in any medium or format, as long as you give appropriate credit to the original author(s) and the source, provide a link to the Creative Commons licence, and indicate if changes were made. The images or other third party material in this article are included in the article's Creative Commons licence, unless indicated otherwise in a credit line to the material. If material is not included in the article's Creative Commons licence and your intended use is not permitted by statutory regulation or exceeds the permitted use, you will need to obtain permission directly from the copyright holder. To view a copy of this licence, visit http://creativecommons.org/licenses/by/4.0/ .
Reprints and permissions
About this article
Formentini, G., Boix Rodríguez, N. & Favi, C. Design for manufacturing and assembly methods in the product development process of mechanical products: a systematic literature review. Int J Adv Manuf Technol 120 , 4307–4334 (2022). https://doi.org/10.1007/s00170-022-08837-6
Download citation
Received : 09 July 2021
Accepted : 27 January 2022
Published : 14 March 2022
Issue Date : June 2022
DOI : https://doi.org/10.1007/s00170-022-08837-6
Share this article
Anyone you share the following link with will be able to read this content:
Sorry, a shareable link is not currently available for this article.
Provided by the Springer Nature SharedIt content-sharing initiative
- Design for manufacturing
- Design for assembly
- Design for manufacturing and assembly
- Engineering design
- Product development
- Systematic review
- Find a journal
- Publish with us
- Track your research
- About Dr. Mladen Vouk
- Research Committees
- Office of Research and Innovation Fellows
- Stats and Rankings
- Awards and Honors
- Improving Research Infrastructure
- Research Initiatives
- Shared Core Research Facilities
- Interdisciplinary Initiatives
- Centers and Institutes
- Faculty Clusters
- ERA Project
- Institutional Training Grants
- Research Portal
- Partner With Us
- Centennial Campus
- Research Commercialization
- National Security Initiatives
- Research Visitors
- Staff Directory
New Technique Improves Finishing Time for 3D Printed Machine Parts
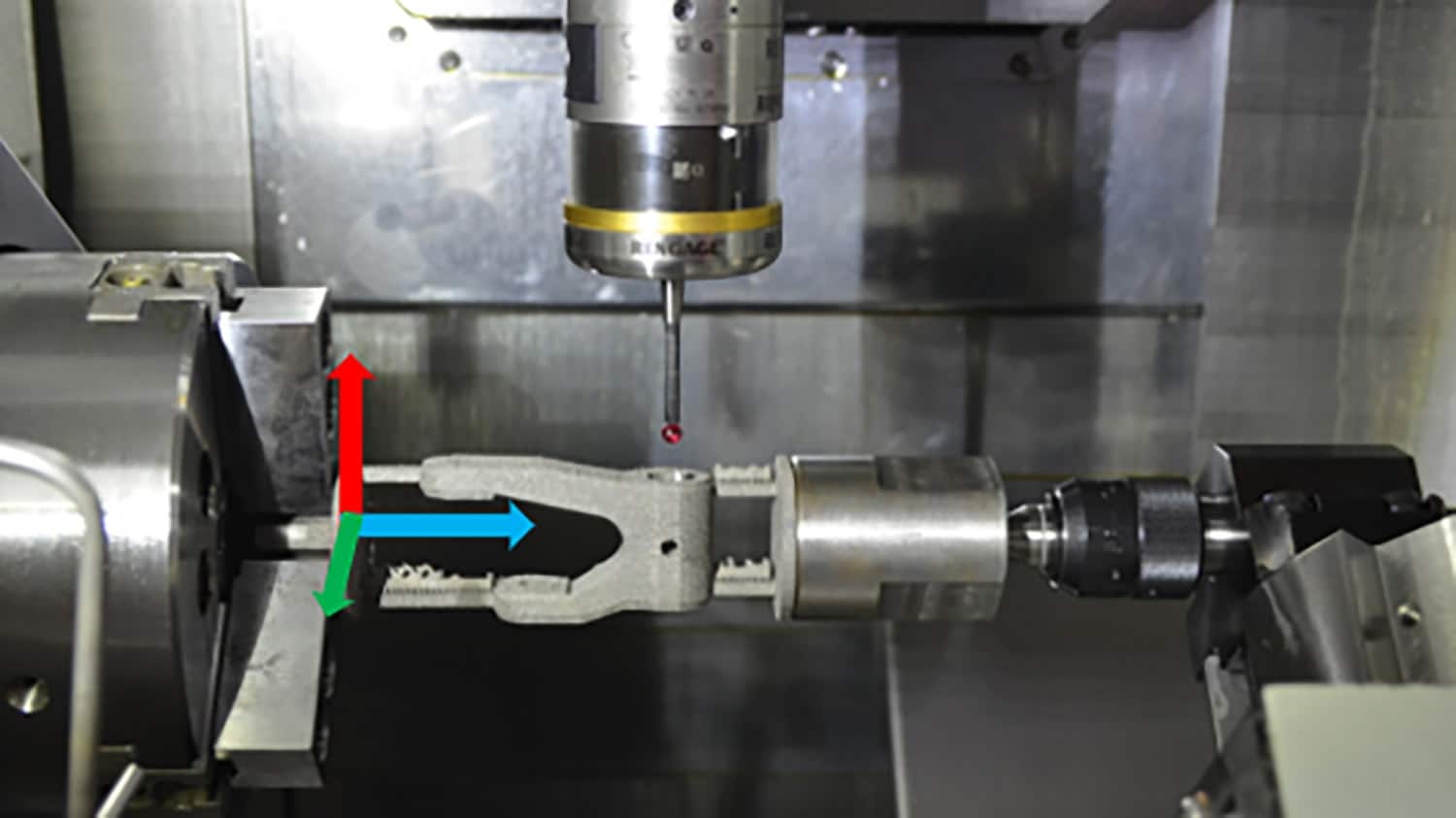
North Carolina State University researchers have demonstrated a technique that allows people who manufacture metal machine parts with 3D printing technologies to conduct automated quality control of manufactured parts during the finishing process. The technique allows users to identify potential flaws without having to remove the parts from the manufacturing equipment, making production time more efficient.
“One of the reasons people are attracted to 3D printing and other additive manufacturing technologies is that these technologies allow users to quickly replace critical machine components that are otherwise difficult to make outside of a factory,” says Brandon McConnell, co-corresponding author of a paper on the work. “And additive manufacturing tools can do this as needed, rather than dealing with supply chains that can have long wait times. That usually means using 3D printing to create small batches of machine parts on demand.” McConnell is an assistant research professor in NC State’s Edward P. Fitts Department of Industrial and Systems Engineering.
After a metal machine part is printed, it requires additional finishing and has to be measured to ensure the part meets critical tolerances. In other words, every aspect of the part must be the right size. Currently, that involves taking a part out of the relevant manufacturing equipment, measuring it, and then putting it back into the manufacturing equipment to make modest adjustments.
“This may need to be done repeatedly, and can take a significant amount of time,” McConnell says. “Our work here expedites that process.”
Specifically, the researchers have integrated 3D printing, automated machining, laser scanning and touch-sensitive measurement technologies with related software to create a largely automated system that produces metal machine components that meet critical tolerances.
Here’s how it works.
When end users need a specific part, they pull up a software file that includes the measurements of the desired part. A 3D printer uses this file to print the part, which includes metal support structures. Users then take the printed piece and mount it in a finishing device using the support structure. At this point, lasers scan the mounted part to establish its dimensions. A software program then uses these dimensions and the desired critical tolerances to guide the finishing device, which effectively polishes out any irregularities in the part. As this process moves forward, the finishing device manipulates the orientation of the printed part so that it can be measured by a touch-sensitive robotic probe that ensures the part’s dimensions are within the necessary parameters.
To test the performance of the new approach, researchers manufactured a machine part using conventional 3D printing and finishing techniques, and then manufactured the same part using their new process.
“We were able to finish the part in 200 minutes using conventional techniques; we were able to finish the same part in 133 minutes using our new technique,” McConnell says. “Depending on the situation, saving 67 minutes could be incredibly important. Time is money in most professional settings. And in emergency response contexts, for example, it could be the difference between life and death.”
The researchers note that this work focuses on printing and finishing machine parts that include circles or cylinders, such as pistons. However, the approach could be adapted for machine parts with other features.
“All of the hardware we used in this technique is commercially available, and we outline the necessary software clearly in the paper – so we feel that this new approach could be adopted and put into use almost immediately,” McConnell says. “And we are certainly open to working with partners who are interested in making use of this technique in their operations.”
The paper, “ Automatic Feature Based Inspection and Qualification for Additively Manufactured Parts with Critical Tolerances ,” is published in the International Journal of Manufacturing Technology and Management . First author of the paper is Christopher Kelly, a former graduate student at NC State who now works for Celonis, Inc. The paper was co-authored by Richard Wysk, professor emeritus in the Fitts Department of Industrial and Systems Engineering; Ola Harrysson, Edward P. Fitts Distinguished Professor in the Fitts Department of Industrial and Systems Engineering; and Russell King, the Henry L. Foscue Distinguished Professor of Industrial and Systems Engineering at NC State.
The work was done with support from the U.S. Army Research Office, under grant number W911NF1910055.
Note to Editors: The study abstract follows.
“Automatic Feature Based Inspection and Qualification for Additively Manufactured Parts with Critical Tolerances”
Authors : Christopher J. Kelly, Deloitte; Richard A. Wysk, Ola A. Harrysson, Russell E. King and Brandon M. McConnell, North Carolina State University
Published : May 1, International Journal of Manufacturing Technology and Management
DOI : 10.1504/IJMTM.2024.138337
Abstract: This work expands the capabilities of the Digital Additive and Subtractive Hybrid (DASH) system by including “geometric qualification” of mechanical products. Specifically, this research incorporates the extended Additive Manufacturing Format files (AMF-TOL) which include American Society of Mechanical Engineers (ASME) Y14.5 specifications for planes, cylinders and other features so that “in-process” inspection can be completed automatically. An example for the production of holes is provided to illustrate On-Machine-Measurement collects sample radii to estimate the size and position of finished cylindrical features. Statistical analysis was used to measure bounds for comparison to specified tolerance callouts to determine whether a part is within specification, within a user-defined level of confidence. Seven different sampling strategies were evaluated on a DASH part including the bird cage sampling strategy defined in ISO-12180. Part data was utilized to show that for large data samples no statistically significant difference in accuracy was identified for four methods. Finally, analysis shows that using the DASH process with automatic inspection is economically advantageous for low volume production runs.
This post was originally published in NC State News.
More From Office of Research and Innovation
Study explores role of epigenetics, environment in differing alzheimer’s risk between black and white communities, makerspace magic with andrea monteza, new tool pinpoints security fixes in open-source software updates.
School of Electrical and Computer Engineering
College of engineering, zheng wins best paper award for advanced packaging technologies.
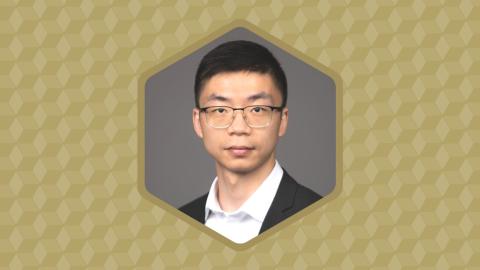
The ECE Ph.D. alumni won the award for his research on fused-silica stitch-chip technology for RF/mm-wave multichiplet modules.
Georgia Tech School of Electrical and Computer Engineering graduate Ting Zheng won an IEEE Transactions on Components, Packaging and Manufacturing Technology (TCPMT) Best Paper Award, from the Advanced Packaging Category, for his research on fused-silica stitch-chip technology.
TCPMT is the flagship journal of the IEEE Electronics Packaging Society (EPS).
He was recognized for the paper he co-authored prior to his graduation, “Benchmarking and Demonstration of Low-Loss Fused-Silica Stitch-Chips with Compressible Microinterconnects for RF/mm-Wave Chiplet-Based Modules.”
It proposes and benchmarks ‘fused-silica stitch-chips’ as an interconnect technology between neighboring RF/mm-wave chiplets. Compared to conventional advanced packaging technologies, the stitch-chips enable low-loss and broadband interconnection, provide built-in mechanical deformation capability to compensate for differing chiplets heights, and provide a path towards package size scaling for large-scale multichiplet integration.
He was advised by ECE Professor and 3D Systems Packaging Research Center Director Muhannad Bakir.
Zheng is the second student from Bakir’s Integrated 3D Systems Lab to have their research recognized. Shengtao Yu won the Intel Outstanding Student Paper Award for this paper on co-packaged optics and fiber-chiplet-connectors at the 2023 IEEE Electronic Components and Technology Conference (ECTC), which is the flagship conference of IEEE EPS.
It is a rare honor for the same research group to win paper awards in the same year from both ECTC and TCPMT.
At the end of May, Zheng, Yu and Bakir will all attend ECTC 2024 in Denver, CO to receive the ECTC and TCPMT paper awards.
Zack Winiecki

IMAGES
VIDEO
COMMENTS
Production & Manufacturing Research publishes open access research on manufacturing engineering and technology including industrial engineering and supply chain management. The main goal is to strengthen research on the dual or twin transformation of manufacturing enterprises in the sense of a digital transformation towards smart and intelligent manufacturing and, at the same time, the ...
Sustainable manufacturing processes, especially sustainable machining, was established as a key theme, including research endeavours of elimination of lubricants. Various manufacturing systems and ...
This section presents results from content analysis seeking to identify how the research is evolving, what are the main contributions and/or impacts of sustainable manufacturing for the development of Industry 4.0, which technologies are being more considered for sustainable manufacturing, and what is the research agenda for the future. 4.2.1.
This paper seeks to explore the research trends and scopes for manufacturing sustainability in Industry 4.0 with three major databases i.e., IEEE, Web of Sciences and Scopus. This paper also highlights the research trends in manufacturing area in ten different Industry 4.0 technologies and then provide the sustainability issues for manufacturing.
The top three journals are: Journal of Manufacturing Systems (17 papers), International Journal of Advanced Manufacturing Technology (12 papers) and International Journal of Production Research (11 papers). It appears that the main case studies of digital technologies implementation in industrial plants are somewhat dispersed across literature ...
In this paper, the applications of 5G in the field of industrial manufacturing will be investigated and analyzed. To access a substantial amount of quality research, the literature search is mainly conducted through Web of Science, the largest peer-reviewed research database. "5G" AND "manufacturing" is firstly used as the search keywords.
Conclusions. In this paper, a systematic and comprehensive review of the sustainable manufacturing technologies literature was undertaken in line with the research motivation and systematic literature review protocol. A total of 98 papers were identified as relevant to this review between 2015 and Sep. 2020.
Enhancing manufacturing operations with synthetic data: a systematic framework for data generation, accuracy, and utility. Vishnupriya Buggineni. Cheng Chen. Jaime Camelio. Frontiers in Manufacturing Technology. doi 10.3389/fmtec.2024.1320166. 1,115 views. Original Research. Published on 11 Jan 2024.
Sustainable manufacturing has become of great importance in various fields include manufacturing, mechanical engineering, materials science, environmental science, and energy science. In this paper, we analyzed and reviewed the research trends of sustainable manufacturing technologies and suggested future perspective. Specifically, the state-of-the-art and historical trajectory of sustainable ...
The following subsections of this literature review paper explain the theoretical context of SM, the research gap identified, the aims and the approach adopted for this work. ... Thoben KD, Wiesner SA, Wuest T. 'Industrie 4.0' and smart manufacturing-a review of research issues and application examples. Int J Autom Technol 2017; 11(1 ...
This review article explores the integration of artificial intelligence (AI) in industry 4.0 and its transformative impact on the manufacturing sector. The core principles of industry 4.0, revolving around digitalization, automation, and connectivity, are examined, emphasizing the creation of "smart factories". The article also discussed the different categories of AI, such as narrow AI ...
Hologram is a technology that makes use of a 3D image formed by a light field in a 3D space. 58 Virtual reality (VR) described the technology to create 3D images with the help of a computer and the interaction in that space with the help of electronic devices for the user to feel as if he or she has been "immersed in a synthesized environment ...
So, the main goals of the paper are: to identify the emerging digital technologies which are most suitable for digital manufacturing through reviewing research papers, white papers, industrial reports and conducting a survey. Then, to analyse the impact of identified technologies on manufacturing industry.
Quality, Properties, and Manufacturing Conditions of Parts made by Additive Technology. Katarina Monkova. Ozkan Gokcekaya. Ankit Gupta. 520 views. An innovative journal that explores all aspects of manufacturing technologies - additive processes, precision engineering, material forming, software technologies and lifecycle engineering - and th...
Digital Twin technology is an emerging concept that has become the centre of attention for industry and, in more recent years, academia. The advancements in industry 4.0 concepts have facilitated its growth, particularly in the manufacturing industry. The Digital Twin is defined extensively but is best described as the effortless integration of data between a physical and virtual machine in ...
Intelligent manufacturing, defined as the integration of manufacturing with modern information technologies such as 5G, digitalization, networking, and intelligence, has grown in popularity as a means of boosting the productivity, intelligence, and flexibility of traditional manufacturing processes. The steel industry is a necessary support for modern life and economic development, and the ...
As an outcome, a conceptual framework of sustainable manufacturing technology research was constructed to structure the knowledge acquired and to provoke future thinking. Finally, challenges and future directions were provided for both industrial and academic reader base, stimulating growth in this fruitful research stream. ... Feature papers ...
Manufacturing Technology 2024, 24(2):315-323 | DOI: 10.21062/mft.2024.030 The work aims to present a design method of cam five-bar paper taking mechanism of packaging machine based on position and orientation constraints to better meet the position and orientation requirements of the end paper taking actuator in the high-speed paper picking ...
Over the next five years, Aerojet Rocketdyne will invest $9 million in the development of powder-based additive manufacturing technolo-gies.105 These and other eforts aim to accelerate U.S. development and application of additive manufacturing technology and will likely help strengthen U.S. competitiveness.
Many of these materials exist as feedstock for metal AM machines and have seen varying levels of research into the material characteristics and properties produced using AM methods, with demonstrations of mechanical properties equal to, and sometimes exceeding those associated with typical manufacturing methods [77], [78], [79], [80].For this to be achieved, the process parameters and post ...
Additive manufacturing (AM) technology has been researched and developed for more than 20 years. Rather than removing materials, AM processes make three-dimensional parts directly from CAD models by adding materials layer by layer, offering the beneficial ability to build parts with geometric and material complexities that could not be produced by subtractive manufacturing processes. Through ...
University of Sri Jayewardenepura, Nugegoda. Abstract. This paper presents an overview and guidance for manufacturing companies which are. preparing to invest in Advanced Manufacturing Technology ...
In the paper "Production Chain Organization in the Digital Age: Information Technology Use and Vertical Integration in U.S. Manufacturing," which published April 30 in Management Science, Chris Forman, the Peter and Stephanie Nolan Professor in the Dyson School of Applied Economics and Management, and his co-author delved into what these ...
Additive manufacturing (AM), a quickly changing field, is reshaping industries by producing novel and customized materials quickly and efficiently. AM deviates from conventional subtractive processes by enabling layer-by-layer production of products with computer-aided design software. This process offers unique advantages for niche applications, such as metamaterial properties. Numerous ...
The design for manufacturing and assembly (DFMA) is a family of methods belonging to the design for X (DfX) category which goal is to optimize the manufacturing and assembly phase of products. DFMA methods have been developed at the beginning of the 1980s and widely used in both academia and industries since then. However, to the best of the authors' knowledge, no systematic literature ...
Abstract. The pursuit for improved performance in the aerospace and aviation industries has inspired the development, investigation, and research of advanced materials. Since the last few years, a lot of research on different alloys, composites and some other advanced materials has been performed to perfectly meet the needs of the aerospace ...
The paper, "Automatic Feature Based Inspection and Qualification for Additively Manufactured Parts with Critical Tolerances," is published in the International Journal of Manufacturing Technology and Management. First author of the paper is Christopher Kelly, a former graduate student at NC State who now works for Celonis, Inc.
Georgia Tech School of Electrical and Computer Engineering graduate Ting Zheng won an IEEE Transactions on Components, Packaging and Manufacturing Technology (TCPMT) Best Paper Award, from the Advanced Packaging Category, for his research on fused-silica stitch-chip technology.TCPMT is the flagship journal of the IEEE Electronics Packaging Society (EPS).