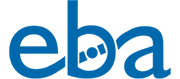

TQM Tools for Effective Problem Solving and Root Cause Analysis
TQM tools have been around for more than 50 years, and revolutionised the concept of quality and process conformity. They are still used today, and successful companies appreciate that building quality into the process is the only way to be competitive.
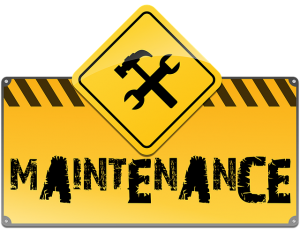
More than just quality control
Quality control traditionally focused on 100% inspection. That is, the Inspection process catches the rejects at the end of the line or process, before the product gets shipped to the customer.
The problem is, 100% inspection is only 70% efficient. There are guaranteed to be parts that get through the net and passed onto the customer!
Prevention is better than cure
It makes sense, therefore to focus on building quality into every process, whereby it is each operator’s task to pass quality product onto the next customer in the process.
Stop the line authority is critical, whereby the operators should be able to stop production to highlight a fault, address that fault as a team, and then eliminate the issue, carrying on with production only when the issues has been resolved.
Measuring process performance is also critical then– understanding real time performance allows management and operators to address those issues and defects instantly or as close to this as possible.
TQM tools and their implementation, capitalises on the involvement of management, workforce, suppliers, and even customers, in order to meet or exceed customer expectations, building quality into the process.
Some specialists highlight nine common TQM practices being:
- cross-functional product design,
- process management,
- supplier quality management,
- customer involvement,
- information and feedback,
- committed leadership,
- strategic planning,
- cross-functional training,
- Employee involvement.
Culture, Culture, Culture…
Like any strategy, it works if it becomes embedded into the fabric of the firm. This takes time and patience and indeed effort. Perseverance will eventually pay and slowly but surely, TQM principles will systematically be utilised on a day to day basis, driving problems out of the business for good.
Effective TQM should be seen as not a system but a way of working, which identifies quality problems before they happen, and on the odd occasion when issues and defects do arise (hey, nothing’s perfect!), they are quickly identified at source, contained, so they are not passed to the customer, and then systematically eradicated to prevent reoccurrence.
In true nature of preventing rather than curing problems, some of the most popularly used TQM Tools are as follows:
- Fishbone Diagrams
- Histogram charts
- Pareto Diagrams
- PDCA Cycle (Which TQM is built around)
- Process Flow Charts
- Process Control Chart
Other Related Articles
- Six Sigma Tools
- Lean Manufacturing Principles
- 5 Step Approach
- Failure Mode effects Analysis (FMEA)


Guide: Total Quality Management (TQM)
Author: Daniel Croft
Daniel Croft is an experienced continuous improvement manager with a Lean Six Sigma Black Belt and a Bachelor's degree in Business Management. With more than ten years of experience applying his skills across various industries, Daniel specializes in optimizing processes and improving efficiency. His approach combines practical experience with a deep understanding of business fundamentals to drive meaningful change.
Implementing Total Quality Management means adopting a philosophy where excellence in operations and customer service is a constant goal, achieved through an organization-wide commitment to continual improvement. It’s a strategy that doesn’t just look at the end product but involves every employee in a collaborative effort to refine processes, enhance efficiency, and elevate the customer experience. This approach doesn’t compartmentalize quality as a departmental responsibility but integrates it into the fabric of the organizational culture, making it everyone’s priority. TQM transforms the traditional management model into a participative and process-oriented culture, ensuring that quality improvement is not a one-time project but an ongoing pursuit of perfection.
What is Total Quality Management (TQM)?
Total Quality Management involves a comprehensive management approach centred around the principle of continuous improvement across all facets of an organization. It underscores the importance of quality not just as a metric for products or services but as a fundamental element that influences customer satisfaction and the overall performance of the business. TQM is distinctive in its inclusive nature, requiring active participation from every level within the organization. This means that everyone from the CEO to entry-level employees is involved in the process of identifying areas for improvement, suggesting changes, and implementing solutions that enhance the quality of the organization’s output. By integrating the efforts of all employees, TQM fosters a culture of quality awareness and improvement, aiming to create an environment where excellence in quality becomes a continuous pursuit, deeply embedded in the organizational fabric and mindset.
What are the Principles of Total Quality Management?
Total Quality Management, or TQM, is like a set of important rules that help make everything a company does really good and keep making it better over time. Here’s what these rules are all about:
Customer Focus
The idea of customer focus is like making sure everything a company does is aimed at making customers happy and meeting what they want or need. It’s like when a chef tastes the food to make sure it’s just right for the guests. Companies listen to what customers say, good or bad, and use that feedback to make their products or services better. This way, they keep customers coming back and attract new ones too.
Total Employee Involvement
Total employee involvement means everyone who works at the company, no matter their job, gets to help make things better. It’s like a sports team where every player, not just the stars, has a role in winning the game. When everyone shares their ideas and works together, they feel like they’re part of something big and are more likely to care about their work and do a good job.
Process Approach
Using a process approach is like following a recipe to bake a cake. Instead of just throwing ingredients together and hoping for the best, you follow steps that make sure the cake turns out great every time. In a company, this means organizing work into clear steps and making sure everything is done right at each step to get the best final result.
Integrated System
An integrated system is when all the different parts of a company, like sales, production, and customer service, work together like a well-oiled machine. It’s like a relay race where each runner passes the baton smoothly to the next. This teamwork across departments helps the company work efficiently and reach its quality goals.
Strategic and Systematic Approach
This principle is about making a game plan for quality. It’s like mapping out a route before a road trip to make sure you get to your destination. The company sets clear goals for quality and checks regularly to see how they’re doing. This way, they can stay on track or change course if needed to keep improving.
Continuous Improvement
Continuous improvement, or making things better bit by bit, is like leveling up in a video game. Each level challenges you to get a little better. In a company, this means always looking for ways to make products, services, or how work is done a little better. It’s about not settling for “good enough” and always striving for “even better.”
Fact-Based Decision Making
Making decisions based on facts is like using a map and compass when hiking. It helps you choose the best path based on the actual terrain and direction, not just a guess. Companies collect data and analyze it to make informed decisions. This way, they’re more likely to succeed because their choices are grounded in reality.
Communications
Good communication is like having a clear and open conversation. It means making sure everyone in the company knows what’s going on, understands the quality goals, and knows how they can contribute. It’s about making sure messages are clear, so everyone is on the same page and can work together effectively.
What are the Steps that Should be Taken to Implement TQM?
Implementing Total Quality Management is a journey that transforms the way an organization operates, focusing on quality in every aspect of its business. Let’s delve into
the detailed process of implementing TQM.
Step 1: Commitment from Top Management
Leadership commitment is not just the first step; it’s the foundation of TQM. Imagine the leaders as the captains of a ship who decide the course and inspire the crew. They must wholeheartedly believe in the value of TQM and be willing to lead by example. This means allocating resources—time, money, and people—to support TQM initiatives. They also set the tone for a culture that prioritizes quality, where every employee feels responsible for maintaining high standards.
Step 2: Define Vision, Mission, and Goals

Step 3: Employee Training

Step 4: Quality Improvement Teams

Step 5: Develop Quality Measures

Step 6: Continuous Assessment and Improvement

Implementing TQM is a transformative process that changes how an organization operates. It requires commitment, clarity of purpose, education, teamwork, measurement, and an unwavering focus on continuous improvement. When done correctly, it leads to higher quality, greater customer satisfaction, and improved performance across the board.
Benefits of Total Quality Management
The implementation of Total Quality Management offers a range of benefits that can significantly transform an organization. These benefits touch on various aspects of the business, from the quality of products and services to the overall operational efficiency and employee morale. Let’s explore these benefits in detail.
Improved Quality
The most direct outcome of TQM is the enhanced quality of products and services. By focusing on quality in every step of production and service delivery, organizations can significantly reduce errors, defects, and inconsistencies. This leads to products and services that not only meet but often exceed customer expectations. Higher quality translates into greater customer satisfaction, fostering loyalty and encouraging repeat business, which is vital for long-term success.
Increased Efficiency
TQM encourages organizations to examine their processes closely and continuously seek ways to make them more efficient. This involves streamlining operations, optimizing workflows, and eliminating any activities that do not add value. By doing so, organizations can accomplish more with less effort and resources, reducing turnaround times and increasing the capacity to deliver products and services faster and more reliably.
Reduced Costs
Hand in hand with increased efficiency, TQM helps organizations cut costs. By identifying and eliminating waste in processes—such as excess inventory, unnecessary steps, or rework—organizations can significantly lower their operational expenses. Furthermore, by improving quality, businesses reduce the costs associated with defects, such as rework, refunds, and returns, further contributing to financial health and stability.
Employee Satisfaction
TQM places a strong emphasis on involving employees at all levels in quality improvement efforts. This participatory approach not only leverages the collective knowledge and skills of the workforce but also fosters a sense of ownership and pride in their work. When employees see the impact of their contributions to the organization’s quality goals, it boosts their job satisfaction and motivation. A satisfied and motivated workforce is more productive, innovative, and committed to the organization’s success.
Competitive Advantage
In today’s competitive marketplace, quality can be a significant differentiator. Organizations that successfully implement TQM principles can achieve higher standards of quality and reliability in their products and services. This excellence in quality can set them apart from competitors, attracting more customers and enabling them to command premium prices. Moreover, a reputation for quality can enhance the organization’s brand and market position, contributing to long-term competitiveness and growth.
Total Quality Management is much more than a set of techniques or procedures; it’s a holistic approach that infuses quality into every aspect of an organization’s operations and culture. By adopting TQM, organizations commit to a path of continuous improvement, where the pursuit of excellence is a constant goal. The benefits of TQM—improved quality, increased efficiency, cost reduction, employee satisfaction, and competitive advantage—are substantial. These advantages highlight why TQM is not just a good practice but a strategic necessity for organizations aiming for long-term success and excellence. The journey toward total quality is ongoing, requiring dedication and commitment at all levels of the organization, but the rewards are well worth the effort.
- Sallis, E., 2014. Total quality management in education . Routledge.
- Ahire, S.L., Landeros, R. and Golhar, D.Y., 1995. Total quality management: a literature review and an agenda for future research. Production and Operations management , 4 (3), pp.277-306.
Q: What is Total Quality Management (TQM)?
A: Total Quality Management (TQM) is a comprehensive management approach focused on continuous improvement in all aspects of an organization, aiming to ensure that every single process, product, or service meets or exceeds customer expectations. It involves the participation of all employees and encompasses the entire organization.
Q: How does TQM improve customer satisfaction?
A: TQM improves customer satisfaction by prioritizing the quality of products and services. It involves understanding customer needs and feedback, and then using this information to make continuous improvements. This ensures that the products or services not only meet but often exceed customer expectations, leading to higher satisfaction levels.
Q: Can small businesses implement TQM?
A: Yes, small businesses can implement TQM. While the scale of implementation may differ compared to larger organizations, the principles of continuous improvement, customer focus, and employee involvement are applicable and beneficial for businesses of any size. Implementing TQM can help small businesses improve quality, efficiency, and competitiveness.
Q: What role do employees play in TQM?
A: Employees play a crucial role in TQM as it requires the involvement and collaboration of everyone in the organization, from top management to front-line staff. Employees contribute to continuous improvement efforts, identify areas for improvement, and are involved in problem-solving. Their participation fosters a sense of ownership and commitment to the quality goals of the organization.
Q: How long does it take to see the benefits of implementing TQM?
A: The time it takes to see the benefits of implementing TQM can vary depending on the size of the organization, the current state of its processes, and the commitment level of its employees and management. Generally, some improvements can be seen relatively quickly, within a few months, but achieving a full transformation and realizing the comprehensive benefits of TQM is a long-term endeavor that can take several years. Continuous improvement is an ongoing process, so benefits can continue to grow over time.

Daniel Croft
Daniel Croft is a seasoned continuous improvement manager with a Black Belt in Lean Six Sigma. With over 10 years of real-world application experience across diverse sectors, Daniel has a passion for optimizing processes and fostering a culture of efficiency. He's not just a practitioner but also an avid learner, constantly seeking to expand his knowledge. Outside of his professional life, Daniel has a keen Investing, statistics and knowledge-sharing, which led him to create the website www.learnleansigma.com, a platform dedicated to Lean Six Sigma and process improvement insights.
Free Lean Six Sigma Templates
Improve your Lean Six Sigma projects with our free templates. They're designed to make implementation and management easier, helping you achieve better results.
Was this helpful?
- Business Management
Total Quality Management (TQM): Driving Success with a Transformative Approach
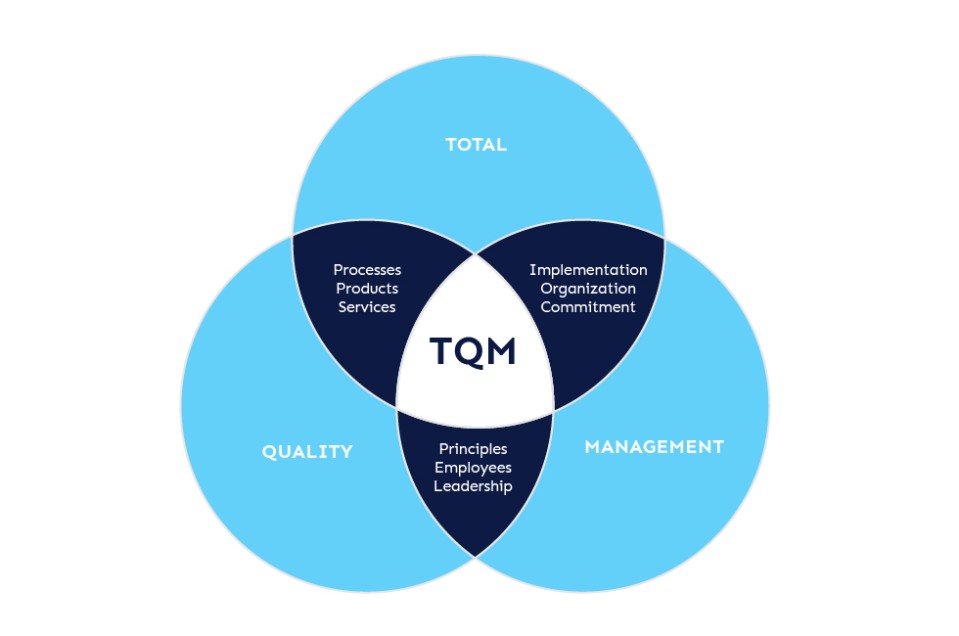
Imagine a business world where quality is not just a goal but a way of life—a perpetual journey of improvement that infiltrates every aspect of an organization. This captivating management philosophy is none other than Total Quality Management (TQM), a transformative approach designed to revolutionize the quality of products, services, and processes within your company. By embracing continuous, organizations can view each step as a problem-solving process—systematically exploring and analyzing operations. The aim is to identify the root causes of any issues, implementing targeted corrective actions to eliminate shortcomings and safeguard against their recurrence.
OVERVIEW
So, what exactly is TQM and how can it propel your organization to new heights of success?
What is Total Quality Management?
TQM is more than a mere buzzword; it's a comprehensive system that permeates every level and function of your business . At its core lies the unwavering commitment and involvement of all employees, making it a truly collaborative endeavor. With TQM, the entire organization rallies under the banner of quality improvement, recognizing that the pursuit of excellence is an ongoing problem-solving process.
The essence of TQM lies in the belief that meeting customer requirements is the ultimate objective of any organization. By embracing continuous improvement, TQM empowers your team to identify and address areas for enhancement across all processes. As these improvements take root, they ripple through the entire organization, directly impacting the quality of your products or services.
But TQM doesn't stop there—it extends its influence beyond your internal operations and into the competitive market landscape. By embracing a series of organizational changes and leveraging powerful tools, TQM unlocks the full potential of your processes and products. The result? Enhanced efficiency, superior performance, heightened flexibility, and, ultimately, a significant competitive advantage that sets your business apart.
To fully embrace TQM, both management and employees must undergo a paradigm shift in their thinking and behavior. This fundamental transformation requires a collaborative effort, as well as structural and organizational adjustments. At the heart of TQM lies strategic control over quality by top management, complemented by the promotion of a quality-oriented mindset among employees. Together, these elements foster a proactive approach to preventing quality-related issues in your products, processes, and operations.
TQM, also known as Total Quality Control, is a dynamic management and implementation philosophy that harnesses the human and material resources of your organization to achieve defined goals in the most effective manner. By tapping into the hidden reserves and capabilities of every employee, TQM continuously improves the quality of your processes, products, and services . With a satisfied customer as the ultimate goal, TQM not only elevates your organization's reputation but also drives down costs, positioning you for long-term success.
Enter Kaizen—an evocative term originating from Japan, which literally means "change for the better." At its core, Kaizen embodies the principle of continuous improvement —a holistic, long-term process seamlessly integrated at every level of your company. With Kaizen, your organization unlocks the immense power of knowledge, experience, and skills residing within your talented workforce. This wealth of "hidden" knowledge already exists within your organization; it simply requires the removal of obstacles for it to circulate freely among your colleagues.
Building upon this foundation, continuous improvement rests upon two pivotal pillars. First, systematic selection and repetition of improvements , driven by scientific and professional knowledge, ensure that your organization is constantly advancing. Second, the relentless pursuit of waste elimination —activities that fail to add value—becomes the driving force behind your improvement initiatives.
What are the principles of TQM?
At the heart of Total Quality Management (TQM) lie four powerful principles, each serving as a guiding light on the path to organizational excellence. Let's delve into these principles and uncover how they can revolutionize your organization.
TQM begins with the fundamental principle that an organization thrives when all its parts work together towards shared goals. Recognizing that every individual, at every level of the organization, and every activity impacts and is influenced by others, TQM fosters a harmonious synergy that propels your organization forward . Ultimately, the driving force behind your organization's existence and operation is the satisfaction of customer requirements and needs.
- The first principle of TQM is Customer Focus . Placing utmost importance on understanding and meeting customer needs and expectations, TQM positions the customer at the core of all activities. By actively listening to customers, conducting market research, and continuously enhancing customer experiences, organizations can deliver products and services that genuinely satisfy their customers.
- Next, TQM emphasizes Continuous Improvement —a culture of perpetual advancement. Through rigorous assessment and refinement of processes, products, and services, organizations embark on a relentless pursuit of excellence. By utilizing quality tools and techniques, they identify areas for improvement, implement changes, and measure the results. This commitment to continuous improvement enables organizations to stay ahead of the competition and meet ever-evolving customer demands.
- TQM also recognizes the vital role of Employee Empowerment and Involvement . Employees are considered valuable assets, integral to the organization's success. TQM fosters teamwork, collaboration, and active participation in decision-making processes. By empowering employees and nurturing a culture of ownership, organizations tap into the knowledge, skills, and creativity of their workforce to drive quality improvement initiatives.
- Process Orientation is another key principle of TQM. It emphasizes understanding and managing processes effectively. Through process mapping, analysis, and identification of areas for improvement, organizations eliminate waste, reduce errors, and optimize efficiency. This process-oriented approach ensures that work is carried out systematically, leading to consistent and high-quality outcomes.
- Data-Driven Decision Making is a cornerstone of TQM. It stresses the use of data and facts to inform decision-making. Organizations collect and analyze data related to quality performance, customer feedback, and process metrics. This data-driven approach enables informed decision-making, identifies areas for improvement, and ensures changes are based on objective evidence rather than assumptions.
- TQM places importance on forging strong Supplier Relationships. Collaborating closely with suppliers to ensure the quality of incoming materials and services, organizations foster mutual trust, collaboration, and continuous improvement. By creating a seamless supply chain, they deliver high-quality products or services to customers.
- Lastly, Leadership Commitment is paramount in TQM. Strong leaders set the vision, establish quality policies, and cultivate a culture that fosters a commitment to quality and continuous improvement. They provide the necessary resources, training, and support to drive TQM initiatives throughout the organization.
By embracing these principles, you establish a solid foundation for a thriving organization—one that excels in quality, customer satisfaction, and continuous improvement. TQM empowers you to make data-driven decisions, forge strong supplier relationships, and nurture a culture of leadership commitment. Embarking on a transformative journey, you elevate your organization to new heights of excellence, where you outshine the competition and become a beacon of success.
What are the Characteristics of Total Quality Management?
Total Quality Management (TQM) is not just a concept; it's a set of characteristics that define its implementation and practice within organizations. These characteristics form the very essence of TQM, creating a framework for achieving excellence . Let's delve into the essential characteristics of TQM that set the stage for organizational success.
- First and foremost, TQM is strategically oriented. It aligns with an organization's vision, mission, and overall strategy. Quality is not an afterthought but an integral part of the organization's goals and objectives. TQM ensures that quality is woven into the fabric of the organization, driving business success and creating a competitive edge.
- Customer focus is another vital characteristic of TQM. It places a strong emphasis on understanding and meeting the needs and expectations of both internal and external customers. TQM organizations prioritize listening to customers, gathering feedback, and continuously improving products, services, and processes to enhance customer experiences. By putting the customer at the heart of their operations, organizations can build strong relationships and loyalty.
- TQM requires a deep-rooted commitment to quality from every employee. It goes beyond mere compliance and instills a mindset of continuous improvement. TQM organizations foster a culture where each employee takes personal ownership and accountability for delivering high-quality outcomes. This commitment to quality permeates every level of the organization, creating a shared responsibility for excellence.
- An analytical approach to decision-making and problem-solving is inherent in TQM. It relies on data and facts to drive informed decisions and solve problems systematically. TQM organizations utilize various quality tools, techniques, and statistical methods to benchmark performance, monitor effectiveness, and drive continuous improvement. This analytical mindset ensures that decisions are based on evidence and leads to more effective outcomes.
- TQM is not a short-term fix; it requires a long-term orientation and commitment. It represents a fundamental shift in how organizations conduct business. TQM organizations understand that building a culture of quality excellence takes time and perseverance. They embrace a long-term perspective, nurturing a new organizational culture that prioritizes quality, continuous improvement, and customer satisfaction.
- Teamwork plays a crucial role in TQM. It fosters collaboration, cooperation, and communication among employees and teams. TQM organizations promote a culture where individuals work together, share knowledge and expertise, and support one another to achieve common quality goals. By harnessing the power of teamwork, organizations can leverage the collective intelligence and skills of their employees.
- Continuous improvement lies at the core of TQM. It is a never-ending journey of seeking opportunities for enhancement. TQM organizations encourage employees to proactively identify areas for improvement, implement changes, and monitor the results. This commitment to continuous improvement ensures that organizations stay competitive, adapt to changing market needs, and deliver increasing value to customers.
- Education and training are vital in developing the knowledge and skills necessary for quality excellence. TQM organizations invest in employee development, providing the necessary training and resources to understand and implement TQM principles effectively. By fostering a culture of continuous learning and improvement, organizations empower their employees to excel in their roles and contribute to the overall success of the organization.
- TQM emphasizes the unity of purpose. It aligns individual and team goals with the overall quality objectives of the organization. TQM organizations ensure that everyone understands and shares the same commitment to quality excellence. This unity of purpose creates a sense of cohesion and synergy, driving the organization towards its quality goals.
- Lastly, TQM actively involves and empowers employees at all levels. It recognizes that involving employees in decision-making and problem-solving processes increases the likelihood of making good decisions and implementing effective solutions. TQM organizations value employee contributions, encouraging them to share their ideas, expertise, and creativity. By empowering employees, organizations tap into their full potential, driving innovation and continuous improvement.
By embracing these characteristics, organizations can establish a TQM culture that drives continuous improvement, customer satisfaction, and organizational excellence. TQM becomes ingrained in the organization's DNA , shaping its operations, decision-making processes, and overall success. Embrace the power of TQM, and unlock the full potential of your organization.
What is Total Quality Management Pyramid?
The Quality Management Pyramid is more than just a visual representation; it's a roadmap to excellence within organizations . This framework illustrates the hierarchy of quality management activities, guiding organizations on their journey to improved quality and customer satisfaction. Let's explore the three levels of the pyramid and uncover the secrets to effective quality management.
At the foundation level, we find the core principles and concepts that lay the groundwork for success . This level sets the direction and culture for quality management within the organization. It encompasses essential elements such as leadership commitment, customer focus, employee involvement, and process orientation. By embracing these foundational pillars, organizations create a solid base for their quality management practices.
Moving up the pyramid, we reach the middle level, which represents the operational aspects of quality management . Here, organizations focus on implementing practical actions to monitor, control, and improve processes and products. Quality planning, process control, data analysis, measurement, and corrective and preventive actions take center stage. This level ensures that quality objectives are translated into tangible actions and that processes are effectively managed to achieve the desired quality outcomes.
Finally, at the top level of the pyramid, we encounter the strategic aspect of quality management . This level involves higher-level decision-making and strategic planning to align quality management with the organization's overall objectives. Here, organizations set quality goals, define quality policies, establish performance indicators, conduct management reviews, and foster continuous improvement. The top-level ensures that quality management is seamlessly integrated into the organization's overarching strategy, contributing to long-term success.
The Quality Management Pyramid offers a h olistic view of quality management, recognizing the interconnectedness of its different elements . It serves as a reminder that effective quality management requires a comprehensive approach, starting from foundational principles, extending to operational implementation, and aligning with strategic goals. By following the roadmap provided by the Quality Management Pyramid, organizations can navigate their way to improved quality, customer satisfaction, and organizational excellence.
What Makes Total Quality Management Relevant and Important in Today's Business Landscape
Total Quality Management (TQM) emerges as a cornerstone of success in today's dynamic and ever-evolving business landscape. Its relevance and importance stem from the multitude of benefits it offers organizations across sectors and industries.
One of the primary reasons TQM is relevant today is its ability to create a culture of continuous improvement . TQM focuses on enhancing processes, products, and services through a systematic approach that encourages ongoing evaluation and refinement. In an era where competition is fierce, organizations that embrace TQM can adapt to changing market demands, identify areas for improvement, and stay ahead of their competitors.
Moreover, TQM recognizes the significance of the human element in organizational success . It goes beyond merely optimizing processes and involves engaging employees at every level. By nurturing an inclusive work environment that empowers individuals, encourages collaboration, and values their ideas and expertise, TQM ignites a flame within the workforce. Engaged employees become more committed, innovative, and proactive, leading to enhanced productivity and improved outcomes that epitomize excellence. TQM recognizes that people are the driving force behind any organization, and their involvement and satisfaction directly impact the quality of products and services delivered.
In addition to its impact on organizational culture, TQM stands as a guardian angel in an unpredictable world , mitigating risks and safeguarding organizations from potential pitfalls. By implementing foolproof quality control processes, organizations proactively address quality concerns and ensure that products and services consistently meet or exceed customer expectations. This approach not only minimizes the likelihood of defects or failures but also helps organizations adhere to regulations and standards, avoiding legal liabilities and reputational damage.
By adopting TQM principles, organizations can achieve numerous benefits, including increased customer satisfaction, improved operational efficiency, reduced costs, enhanced brand reputation, and sustained business growth. TQM acts as a guiding philosophy that permeates every aspect of an organization , fostering a culture of excellence and continuous improvement.
How does Total Quality Management helps organizations grow?
Total Quality Management (TQM) plays a crucial role in facilitating the growth of organizations in several ways:
- Improved Customer Satisfaction: TQM focuses on understanding and meeting customer needs and expectations. By consistently delivering high-quality products and services, organizations can enhance customer satisfaction. Satisfied customers are more likely to become repeat customers, provide positive reviews, and recommend the company to others. This leads to increased customer retention, expanded market share, and accelerated business growth.
- Enhanced Operational Efficiency: TQM emphasizes the identification and elimination of waste, inefficiencies, and defects in organizational processes. Through continuous improvement efforts, organizations can streamline their operations, optimize workflows, and enhance overall efficiency. This results in improved productivity, reduced costs, and the ability to allocate resources effectively. Increased operational efficiency enables organizations to scale their operations and handle growing demands efficiently.
- Employee Engagement and Empowerment: TQM promotes a culture of employee involvement, empowerment, and continuous learning. Engaged employees are more motivated, innovative, and committed to the success of the organization. By providing employees with the tools, training, and autonomy to contribute to quality improvement initiatives, organizations tap into their full potential. Engaged and empowered employees become valuable assets who drive growth through their dedication, creativity, and contributions.
- Strengthened Supplier Relationships: TQM extends beyond the organization's boundaries to include suppliers and other external stakeholders. By collaborating closely with suppliers and ensuring their adherence to quality standards, organizations build strong and reliable supplier relationships. These relationships contribute to the overall quality of the end product or service. Reliable suppliers enable organizations to meet customer demands promptly, maintain consistent quality, and support business growth.
- Continuous Improvement and Innovation: TQM fosters a culture of continuous improvement and innovation within organizations. Through ongoing evaluation, analysis of data, and feedback from customers and employees, organizations identify areas for enhancement. By embracing a mindset of continuous improvement, organizations can adapt to changing market dynamics, identify emerging opportunities, and stay ahead of competitors. Continuous improvement and innovation are key drivers of business growth and long-term sustainability.
- Positive Reputation and Brand Image: TQM helps build a positive organizational reputation and brand image. When customers perceive a company as consistently delivering high-quality products and services, it enhances their trust and confidence. A positive reputation and brand image attract new customers, enhance market share, and differentiate the organization from competitors. A strong reputation is a valuable asset that contributes to business growth and success.
By implementing Total Quality Management, organizations strive to enhance customer satisfaction, reduce waste and defects, improve operational efficiency, increase employee morale, and achieve long-term success. TQM is not a one-time initiative but an ongoing process that requires sustained effort and commitment from all levels of the organization.
Why does Total Quality Management fail?
While Total Quality Management (TQM) can bring significant benefits to organizations, there are several reasons why it may fail to deliver the desired outcomes. Some common factors that can contribute to the failure of TQM implementation include:
- Lack of Leadership Commitment: TQM requires strong leadership commitment and support at all levels of the organization. If top management fails to prioritize and actively engage in TQM initiatives, it can lead to a lack of direction, inadequate resource allocation, and a lack of motivation among employees.
- Inadequate Employee Involvement: TQM relies on active employee participation and empowerment. If employees are not adequately involved or do not understand the principles and benefits of TQM, the implementation may lack buy-in and enthusiasm. Without employee involvement, TQM initiatives may encounter resistance or fail to generate sustainable improvements.
- Poor Communication and Training: Effective communication is essential for successful TQM implementation. If there is a lack of clear and consistent communication about TQM goals, processes, and expectations, employees may not fully understand their roles or the benefits of TQM. Insufficient training and development programs can also hinder employees' ability to implement TQM practices effectively.
- Inadequate Measurement and Feedback Systems: TQM relies on data-driven decision-making and continuous improvement. If organizations do not establish effective measurement systems or fail to collect and analyze relevant data, they may lack the insights necessary to identify improvement opportunities and measure progress accurately. Without proper feedback mechanisms, organizations may struggle to make informed adjustments and sustain TQM efforts.
- Overemphasis on Tools and Techniques: TQM is not just about implementing tools and techniques but requires a holistic approach. If organizations focus solely on adopting TQM tools without addressing cultural, behavioral, and systemic issues, it can lead to a superficial implementation that fails to bring about lasting change.
- Lack of Integration with Business Strategy: TQM should align with the organization's overall business strategy and objectives. If TQM initiatives are implemented in isolation from the strategic direction of the organization, they may lack relevance and fail to gain support from key stakeholders.
- Resistance to Change: Implementing TQM often requires significant changes in processes, roles, and behaviors. Resistance to change from employees or organizational inertia can impede the successful implementation of TQM initiatives. Without addressing resistance and providing support during the transition, TQM efforts may struggle to gain traction.
- Unrealistic Expectations and Short-term Focus: TQM is a long-term approach to quality improvement. If organizations have unrealistic expectations for immediate results or focus solely on short-term gains, they may abandon TQM initiatives prematurely or fail to invest sufficient time and resources for sustainable change.
It's important to note that while TQM can face challenges and potential failure, addressing these factors through effective planning, communication, leadership, and sustained commitment can increase the chances of successful implementation and reap the benefits of TQM.
Should Total Quality Management be Measured?
Measuring TQM is crucial for assessing effectiveness, monitoring performance, identifying improvement opportunities, enhancing decision-making, demonstrating accountability, driving continuous improvement, and benchmarking against industry standards. It provides a framework for organizations to track their progress, align their efforts, and continuously strive for excellence in quality management.
Measuring Total Quality Management (TQM) is essential for several reasons:
- Assessing Effectiveness: Measuring TQM allows organizations to evaluate the effectiveness of their quality management practices and initiatives. It provides insights into how well TQM principles and processes are being implemented and whether they are delivering the desired outcomes. Measuring TQM helps organizations identify strengths, weaknesses, and areas for improvement in their quality management systems.
- Monitoring Performance: TQM measurement provides a means to monitor performance against established quality objectives, targets, and benchmarks. It allows organizations to track progress over time and compare their performance to industry standards or competitors. Monitoring TQM performance helps organizations identify deviations, trends, and areas requiring attention to ensure continuous improvement.
- Identifying Improvement Opportunities: Measuring TQM helps organizations identify areas for improvement and potential quality gaps. By analyzing performance metrics, organizations can pinpoint specific processes, systems, or areas where quality improvements are needed. It provides a basis for making data-driven decisions and prioritizing improvement efforts to enhance overall quality and operational effectiveness.
- Enhancing Decision-making: TQM measurement provides meaningful data and information that supports informed decision-making. By having access to accurate and timely quality-related data, organizations can make better decisions related to process improvements, resource allocation, customer satisfaction strategies, supplier management, and risk mitigation. TQM measurement enables organizations to make decisions based on objective evidence rather than assumptions or guesswork.
- Demonstrating Accountability: Measuring TQM enables organizations to demonstrate their accountability to stakeholders, including customers, employees, suppliers, and regulatory bodies. It provides evidence of the organization's commitment to quality and its ability to meet customer expectations. By transparently measuring and reporting on TQM performance, organizations can build trust and credibility with stakeholders, which is vital for long-term success.
- Driving Continuous Improvement: TQM measurement is closely tied to the principle of continuous improvement. By measuring TQM, organizations can identify opportunities for ongoing enhancements, set new targets, and track the impact of improvement initiatives. It creates a feedback loop that encourages the organization to continuously strive for higher levels of quality and performance.
- Benchmarking and Learning: Measuring TQM allows organizations to benchmark their performance against industry standards, best practices, or competitors. It provides insights into where the organization stands relative to others in terms of quality and can reveal opportunities for learning and adopting innovative practices. Benchmarking helps organizations identify areas for improvement and adopt proven strategies to enhance their TQM practices.
How can Total Quality Management be measured?
Total Quality Management (TQM) can be measured using various quantitative and qualitative metrics. These measurements provide insights into the effectiveness of TQM implementation and the organization's overall quality performance.
Here are some commonly used methods and metrics for measuring TQM:
- Customer Satisfaction: Customer satisfaction surveys, feedback mechanisms, and Net Promoter Score (NPS) can measure the level of satisfaction customers have with the organization's products or services. This metric helps gauge the effectiveness of TQM in meeting customer expectations and delivering high-quality experiences.
- Defect Rate: The defect rate measures the number or percentage of defects or non-conformities in products or services. It indicates the level of quality achieved and the effectiveness of TQM processes in preventing and addressing defects.
- Process Efficiency and Cycle Time: Metrics such as cycle time, lead time, and process efficiency ratios (e.g., productivity, utilization) can assess the effectiveness of TQM in improving operational processes and reducing waste. It measures the time taken to complete a process or deliver a product/service, helping identify areas for improvement.
- Cost of Quality (COQ): COQ measures the costs incurred due to poor quality, including prevention costs, appraisal costs, internal failure costs, and external failure costs. By tracking COQ, organizations can evaluate the effectiveness of TQM in reducing costs associated with quality issues and rework.
- Employee Engagement: Surveys, feedback mechanisms, and employee satisfaction metrics can assess the level of employee engagement and their perception of TQM implementation. Engaged employees are more likely to contribute to quality improvement efforts and align with TQM principles.
- Supplier Performance: Metrics related to supplier quality, such as on-time delivery, defect rate, and adherence to specifications, can measure the effectiveness of TQM in managing supplier relationships and ensuring high-quality inputs.
- Continuous Improvement Initiatives: Tracking the number of implemented improvement projects, cost savings or revenue generated from improvement initiatives, and the effectiveness of corrective and preventive actions can indicate the success of TQM in driving continuous improvement.
- Audit Results: Regular quality audits can assess adherence to TQM processes and identify areas of non-compliance or improvement. Audit findings and their resolution rates can provide insights into the effectiveness of TQM implementation.
- Regulatory Compliance: Compliance with industry standards, regulations, and certifications (e.g., ISO 9001) can be measured to assess the effectiveness of TQM in meeting regulatory requirements and maintaining quality standards.
- Benchmarking: Comparing the organization's performance against industry benchmarks, best practices, or competitors' quality metrics can provide insights into the effectiveness of TQM and identify areas for improvement.
It's important to establish a balanced set of metrics that align with organizational goals, customer requirements, and the principles of TQM. The selected metrics should be regularly tracked, analyzed, and used to drive continuous improvement and strategic decision-making.
Which Total Quality Management System?
There are several Total Quality Management (TQM) systems or frameworks that organizations can adopt to implement quality management practices.
Here are a few widely recognized TQM systems:
- ISO 9000: The ISO 9000 series is a set of international standards developed by the International Organization for Standardization (ISO). These standards provide guidelines for implementing a quality management system that focuses on customer satisfaction, process efficiency, and continuous improvement. ISO 9001 certification is a globally recognized standard that demonstrates an organization's commitment to quality management.
- Six Sigma: Six Sigma is a data-driven methodology that aims to minimize defects and variation in processes to achieve near-perfect quality. It involves defining, measuring, analyzing, improving, and controlling processes to reduce errors and waste. Six Sigma uses statistical tools and techniques to drive process improvement and achieve higher levels of quality.
- Lean Manufacturing: Lean manufacturing, also known as Lean or Lean Production, is a systematic approach to process improvement that emphasizes waste reduction, improved efficiency, and value creation. It focuses on eliminating non-value-added activities, optimizing flow, and maximizing customer value. Lean principles, such as Just-in-Time (JIT) production and Continuous Flow, aim to streamline processes and improve overall quality.
- Total Quality Control (TQC): Total Quality Control is a Japanese approach to TQM that emphasizes employee involvement, teamwork, and continuous improvement. TQC focuses on defect prevention rather than detection and encourages the use of quality circles, employee empowerment, and statistical process control to drive quality improvements.
- Baldrige Excellence Framework: The Baldrige Excellence Framework is a performance excellence model developed by the U.S. Department of Commerce. It provides a framework for assessing and improving organizational performance in multiple areas, including leadership, strategy, customer focus, measurement and analysis, workforce engagement, operations, and results. The framework emphasizes a systems approach and continuous improvement.
It's important to note that organizations may choose to adopt and tailor these TQM systems or frameworks based on their specific needs and industry requirements. The selection of a TQM system depends on factors such as organizational goals, industry standards, regulatory compliance, and customer expectations.
Steps to Implementing a Total Quality Management System
Implementing a Total Quality Management (TQM) system requires careful planning and execution. While the specific steps may vary depending on the organization and its unique context, here is a general framework that can guide the implementation process:
- Commitment from Top Management: Obtain commitment and support from top management to drive the implementation of TQM. They should communicate the importance of quality and set clear quality objectives for the organization.
- Establish a Cross-Functional Team: Form a cross-functional team consisting of representatives from different departments or areas within the organization. This team will be responsible for coordinating and overseeing the TQM implementation process.
- Assess Current State: Conduct a thorough assessment of the organization's current quality management practices, processes, and systems. Identify strengths, weaknesses, and areas for improvement.
- Define Quality Policy and Objectives: Develop a quality policy statement that reflects the organization's commitment to quality. Set measurable quality objectives aligned with the organization's strategic goals.
- Develop a TQM Plan: Create a detailed plan outlining the steps, activities, and timeline for implementing TQM. Define roles and responsibilities, allocate necessary resources, and establish key performance indicators to track progress.
- Training and Awareness: Provide training and awareness programs to employees at all levels about TQM principles, practices, and their role in implementing and sustaining quality initiatives. This ensures that everyone understands the importance of quality and their contribution to its success.
- Establish Quality Metrics and Measurement Systems: Identify appropriate quality metrics and establish measurement systems to monitor and evaluate the organization's performance against the defined quality objectives. This includes collecting relevant data, analyzing it, and using it to drive decision-making and improvement efforts.
- Foster Employee Involvement: Encourage and empower employees to actively participate in quality improvement initiatives. Establish mechanisms for capturing and implementing their suggestions, ideas, and feedback. Create cross-functional teams or quality circles to facilitate collaboration and problem-solving.
- Continuous Improvement Processes: Implement processes for continuous improvements, such as regular quality audits, management reviews, and corrective action systems. Continuously monitor and analyze data, identify areas for improvement, and implement appropriate actions to enhance quality and address any issues or non-conformities.
- Supplier Management: Establish effective supplier management processes, including supplier selection, evaluation, and collaboration. Ensure that suppliers adhere to quality standards and work closely with them to achieve mutual quality goals.
- Communicate and Celebrate Achievements: Regularly communicate the progress, successes, and challenges of TQM implementation to all stakeholders. Celebrate achievements, recognize employee contributions, and create a culture of continuous learning and improvement.
- Review and Adapt: Conduct periodic reviews of the TQM system to assess its effectiveness and identify areas for refinement. Adapt the system as needed to align with changing organizational needs, industry standards, and customer expectations.
Remember, implementing TQM is an ongoing process that requires continuous commitment, monitoring, and improvement. It is essential to foster a culture that values quality, encourages employee involvement, and embraces the principles of TQM for long-term success.
In a world where businesses strive to outshine their competition and meet the ever-increasing demands of customers, Total Quality Management (TQM) emerges as a guiding light, illuminating the path to unrivaled growth and success. Embracing Total Quality Management is a game-changer for organizations aspiring to thrive in today's competitive landscape. By putting customers first, empowering employees, fostering continuous improvement, and nurturing strategic partnerships, TQM paves the way for organizations to surpass their goals, outshine their competitors, and cement their position as industry leaders. So, embark on the TQM journey, embrace continuous improvement, and witness the transformation that awaits your organization. Quality will become ingrained in your DNA, setting you apart from the competition and propelling you towards sustained success. It's time to unleash the power of TQM and drive your organization to new heights.
What are your thoughts on the subject above? Feel free to post a comment or start a discussion.
TAGS: Total Quality Management, TQM, Excellence, Long-term success, Competitive business landscape, Customer-centric culture, Empowering employees, Continuous improvement, Strong relationships with suppliers, Operational excellence, Customer satisfaction, Reputable brand image, Sustainable growth, Prosperity, Ever-evolving business landscape, Changing customer demands, Relentless competition, Voice of the customer, Exceeding expectations, Process improvement, Waste elimination, Operational efficiency, Streamlined workflows, Resource utilization, Cost reduction, Collaboration, Engagement, Employee involvement, Morale boost, Positive work environment, Implementation challenges, Top management support, Effective communication, Comprehensive training, Measurement systems, Progress tracking, Data-driven decisions, Strategy adaptation, Patience, Perseverance, Continuous learning, Organizational excellence, Game-changer, Thriving in competition, Customer priority, Strategic partnerships, Exceeding goals, Industry leaders, Transformation, Unparalleled achievements.
Brochure - Vol. 1 (2...

Difference between P...

Total Quality Manage...

Brochure - Vol. 2 (2...

- Process Management
- Digital Era Trends
- Human Resources Management
- Contributor Corner
- Media Storytelling News
- Yearly Brochures
- Education Center
- Community Member Profiles: Companies
- Community Member Profiles: Individuals
Leave A Comment
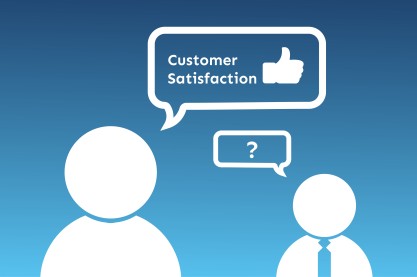
Benefits of Customer Relationship Manage...
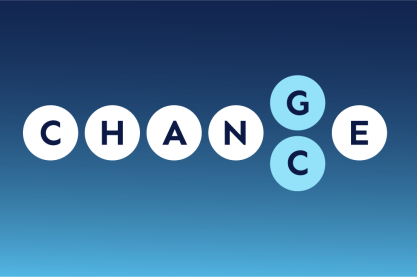
Embracing Change: The Key to Business Re...
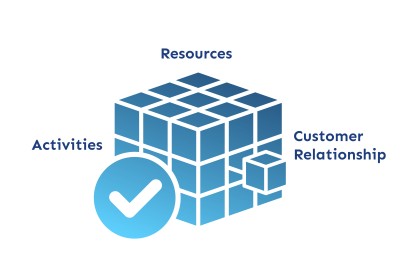
Business System Modeling
Are you interested in a journey on your way towards optimum success with us as your indispensable partner, request a quote, thank you, your message has been sent successfully.
Please fill out the form below and we'll contact you as soon as possible!
Almost there...
By using Optimod.net, you agree to our Cookie Policy.
Popular Searches
Your previous searches, recently visited pages.
Content added to Red Folder
Removed from Red Folder
Management Tools
Total Quality Management
Total Quality Management (TQM) is an organization-wide, customer-focused mindset and data-driven approach to eliminating, reducing, or preventing errors.
- January 31, 2023

What Is Total Quality Management (TQM)?
Total Quality Management (TQM) is an organization-wide, customer-focused mindset and data-driven approach to eliminating, reducing, or preventing errors. Total Quality Management emphasizes a whole-company approach across functions and departments. Senior leadership leads TQM through goal setting, training, and effective communication.
Usage and satisfaction among survey respondents
A fundamental part of TQM is assessing and redefining processes, monitoring performance, and using the results to drive further improvements. Improvement ideas should be identified holistically beyond function-specific activities. Each area should feel accountable for the overall quality of the final product or service. This creates a virtuous cycle of continuous improvement that boosts production, customer satisfaction, and profits.
How Is Total Quality Management Implemented?
To succeed, TQM requires companies to:
- Understand present and future customer needs
- Map the critical processes through which the organization meets its customers’ needs
- Identify the key problem areas in processes and work on them until they approach zero-defect levels
- Design products and services that cost-effectively meet or exceed customer needs
- Assess current culture and quality management systems
- Identify core values and principles and communicate them across the organization
- Train and coach employees on new processes and problem-solving techniques
- Develop effective measures of product and service quality
- Create incentives linked to quality goals
- Promote a zero-defect philosophy across all activities
- Encourage management to lead by example
- Develop feedback mechanisms to ensure continuous improvement
Related Topics
Quality Management System
Continuous Improvement
Quality Assurance
What Are Common Uses of Total Quality Management?
TQM improves profitability by focusing on quality improvement and addressing associated challenges within an organization.
TQM can be used to:
- Increase productivity
- Lower scrap and rework costs
- Improve product reliability
- Decrease time-to-market cycles
- Decrease customer service problems
- Increase competitive advantage
ASQ. https://asq.org/
Camison, Cesar. “Total Quality Management and Cultural Change: A Model of Organizational Development.” International Journal of Technology Management 16, nos. 4-6, 1998, pp. 479–493.
Choi, Thomas Y., and Orlando C. Behling. “Top Managers and TQM Success: One More Look After All These Years.” Academy of Management Executive, February 1997, pp. 37–47.
Goetsch, David L., and Stanley B. Davis. Quality Management for Organizational Excellence: Introduction to Total Quality. 8th ed. Prentice Hall, 2015.
Grant, Robert M., Rami Shani, and R. Krishnan. “TQM’s Challenge to Management Theory and Practice.” MIT Sloan Management Review , Winter 1994, pp. 25–35.
Imai, Masaaki. Kaizen: The Key to Japan’s Competitive Success. Random House, 1986.
Juran, J. M. Juran's Quality Handbook: The Complete Guide to Performance Excellence, Seventh Edition . McGraw Hill, 2016.
Kiran, D. R. Total Quality Management: Key Concepts and Case Studies. Butterworth-Heinemann, 2016.
Malcolm Baldrige National Quality Award. www.nist.gov/baldrige
Oakland, John S., and Robert J. Oakland. Total Quality Management and Operational Excellence: Text with Cases . Routledge, 2020.
Walton, Mary. The Deming Management Method . Perigee, 1988.

Management Tools & Trends 2023
On the 30th anniversary of our survey, managers seem surprisingly upbeat.
- Business Process Redesign
- Lean Six Sigma
- Management Tools & Trends
- Performance Improvement
- Service Design & Operations
How We've Helped Clients
Performance improvement lean six sigma improves plant performance and cuts costs, performance improvement lean six sigma solves a commercial bank's growth problem, performance improvement streamlining engine assembly boosts output, ready to talk.
We work with ambitious leaders who want to define the future, not hide from it. Together, we achieve extraordinary outcomes.
Contact Bain
How can we help you?
- Business inquiry
- Career information
- Press relations
- Partnership request
- Speaker request
Learn how to solve the skills gap
AI-Powered Digitization - CreatorPro
- Connected Work Instructions
Continuous Improvement
- Operational Training
- Transformation Services
View All Features
- Consumer Packaged Goods
- Food and Beverage
Heavy Equipment
- Pharmaceuticals + Biotechnology
- Resource Library

- AI-Powered Process Digitization - CreatorPro
- All Features
- Heavy Machinery

Mastering Total Quality Management in Manufacturing (TQM) | Strategies and Insights
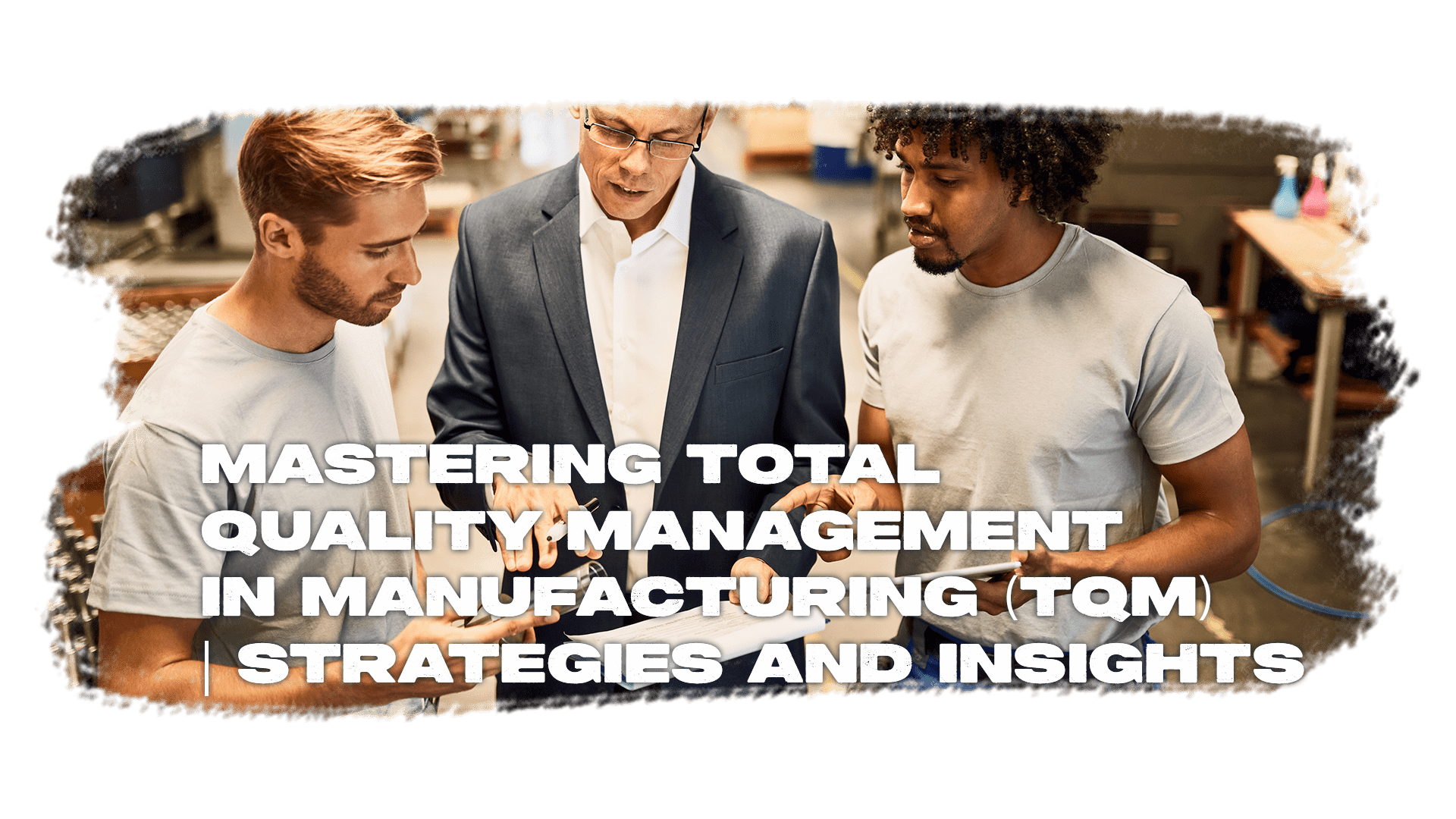
If there’s one consistent thread that unites every manufacturer worldwide, it’s quality. The need to produce a quality product that meets or exceeds the needs and expectations of customers is a driving force in manufacturing.
Table of Contents
1. Benefits of Implementing TQM
2. TQM & Innovation
3. Challenges & Pitfalls of TQM Implementation
4. TQM Implementation Strategies
5. Customer Centric Approach
6. Building a TQM Culture
7. Quality Metrics & Performance Measurement
8. Supplier Quality Management
9. Employee Training & Development
10. TQM Tools & Techniques
11. TQM & Continuous Improvement
12. Final Thoughts
Total Quality Management is a systematic approach that aims to improve the quality of a product or service. Sounds simple enough. If a company wants to produce the highest quality product possible, it must make a dedicated effort.
According to the ASQ Quality Glossary , quality management is "the application of a quality management system in managing a process to achieve maximum customer satisfaction at the lowest overall cost to the organization while continuing to improve the process."
This definition hits all the marks related to TQM. A systematic implementation that focuses on the customer and strives for continuous improvement.
What many organizations miss is that the need for a structure that supports quality must be present throughout every level of the business.
Businesses can implement TQM in all areas of an organization, including manufacturing, service, administration, and beyond.
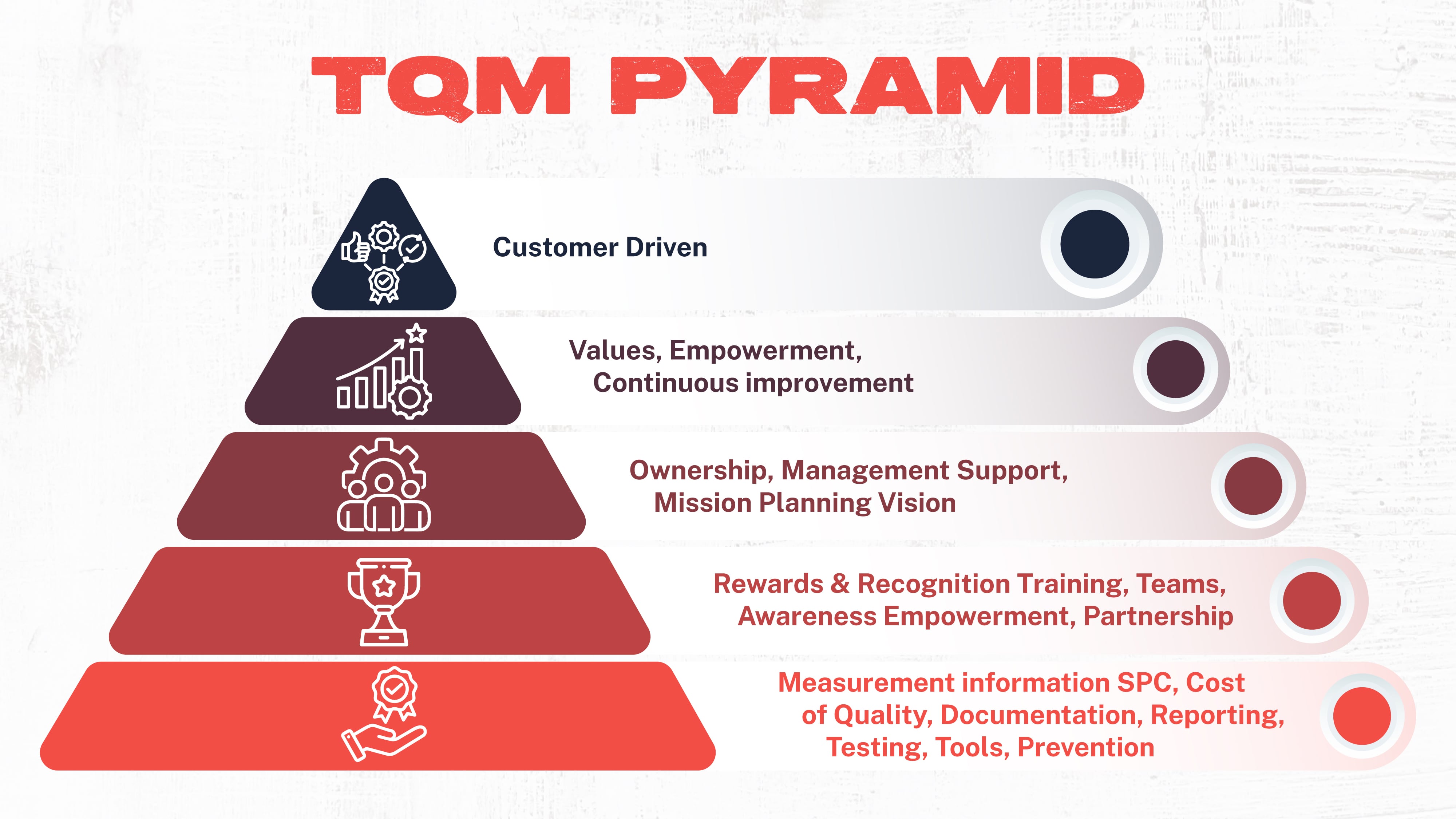
And secondly, quality should be intertwined with the customer experience. TQM focuses specifically on customer satisfaction and continuous improvement.
This article will clearly define total quality management and offer some strategies and insights into how to make it work effectively for an organization.
Benefits of Implementing TQM
It would be hard to deny the benefits of a process that improves manufacturing quality.
Total quality management is an approach that is incredibly effective in this task. But more than enhancing the quality, TQM also helps manufacturers reduce costs and boost customer satisfaction. And that's just the beginning.
As for the manufacturing industry, research shows that quality could make a definitive difference. A return focus on growth and competitiveness within the key sectors would restore 1.5 million manufacturing jobs to the U.S.
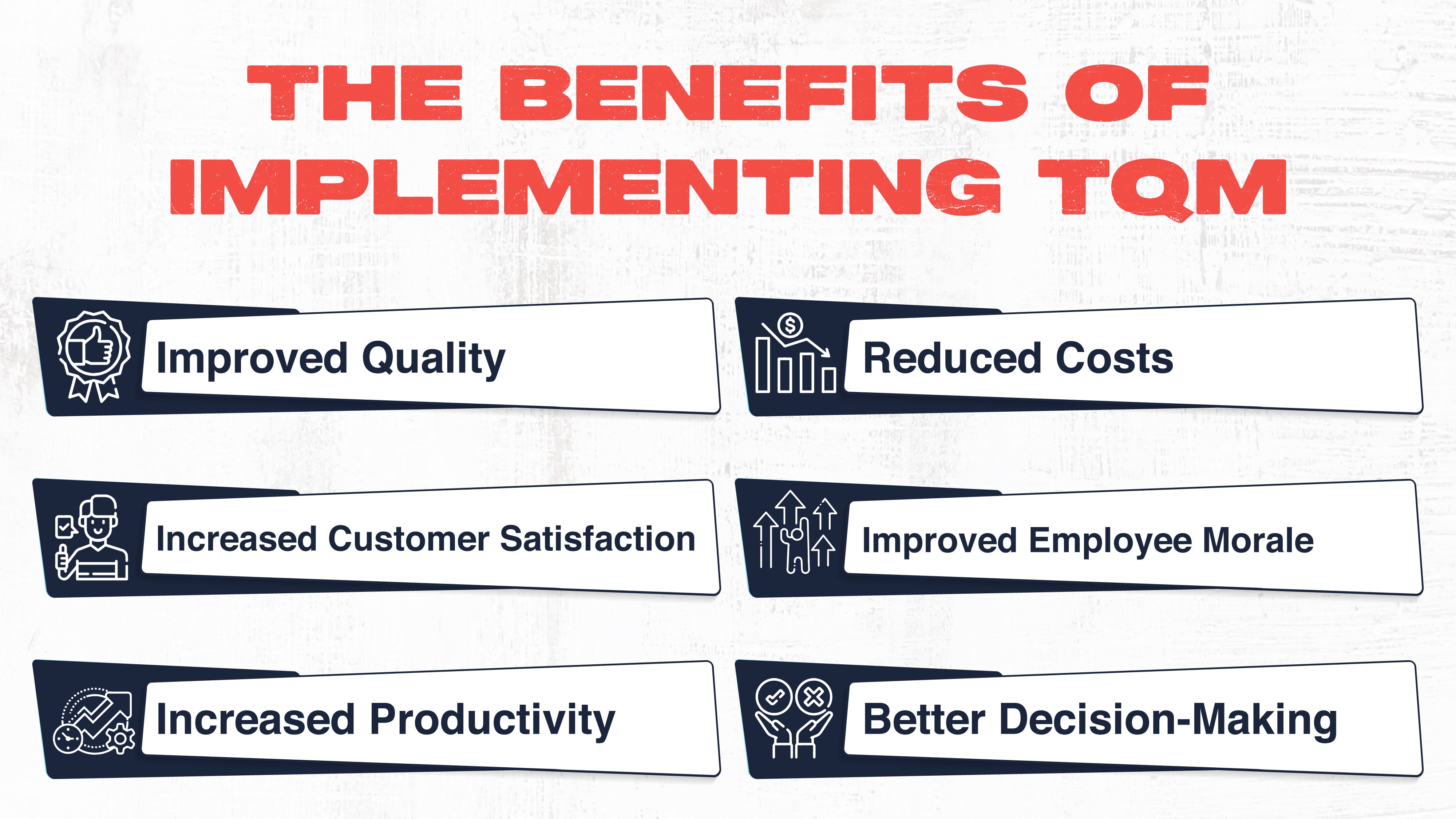
Improved Quality
Putting systems in place to bolster the quality of products and services would have a far-reaching effect on the overall quality of the outcomes. Quality should be first and foremost at every production plant to remain competitive and keep customers happy.
Reduced Costs
Low-quality products can result in defects, which waste resources, materials , and time. A focus on reducing the potential for faults means manufacturers can cut costs by reducing or eliminating these losses.
Increased Customer Satisfaction
Customers demand quality products. With the market's competition, customers won’t be willing to settle for “almost” or “good enough.” Providing the highest-quality product possible will keep customers satisfied and returning for more.
Improved Employee Morale
There is a direct correlation between quality management and employee morale. Employees want to feel as if their jobs are providing something positive. Working for a company that cuts corners and provides a less-than-satisfactory product will damage employee morale and productivity in the long run.
Increased Productivity
When less time is spent mitigating the fallout from mistakes and dealing with defective products, the business can spend more time on other production tasks.
Better Decision-Making
A total quality management system incorporates everyone and everything within an organization. It relies on complex data, input from workers and supervisors, and statistical analysis. All this information can only help companies make more intelligent, more informed decisions.
TQM & Innovation
Total Quality Management requires an approach that encompasses an organization. Based on the principle of continuous improvement, TQM can help spark innovation within that organization by drawing on the ideas and problem-solving abilities of its most incredible resource – people.
Too many manufacturers put all their time and energy into improving processes and boosting productivity. The drive for those at the big table is always to do more with less.
And while this is the basis of business, a narrow-minded view focused on the numbers can often miss out on the creativity of the people on the front lines.
TQM puts people, and their creativity, at the forefront of problem-solving. With a focus on the needs and wants of the customer, TQM helps organizations pinpoint where those problems lie.
By leaning on and empowering the people within an organization, it allows for learning, creativity, and innovation to figure out how to build something better.
Challenges & Pitfalls of TQM Implementation
Poor implementation of a total quality management system can do more harm than good. The same can be said of virtually any program put in place at an organization without careful planning.
If everyone on the team isn’t on board, getting things moving in the right direction can be hard. And when it comes to quality management, involvement from every employee is essential for success.
Below are a few common challenges and pitfalls that manufacturers face when implementing a TQM system and why companies should be careful when starting a new quality program.
Failure from Management
All good internal programs at any business must start from the top. Management, executives, supervisors, and even the CEO must all play their part in setting the example.
And it comes down to this: do employees understand the why and how of the TQM system, and do they know how to play their part in a successful outcome? Managers must ensure they’re answering these questions.
Inadequate Employee Involvement
Without proper leadership, employees might push back against any new program. Employee push back is especially true if they lack the proper training and education.
Organizations that simply throw a bunch of new rules and regulations at employees without explaining the benefit to everyone within the company will find that employees may not take the changes seriously.
Poor Communication
At the heart of the TQM is communication between all levels of an organization. Employees must be free to express their opinions and come to managers with problems without fearing retribution or dismissal.
Managers must communicate back with employees regarding problem-solving techniques. And above all, organizations must communicate with the customer.
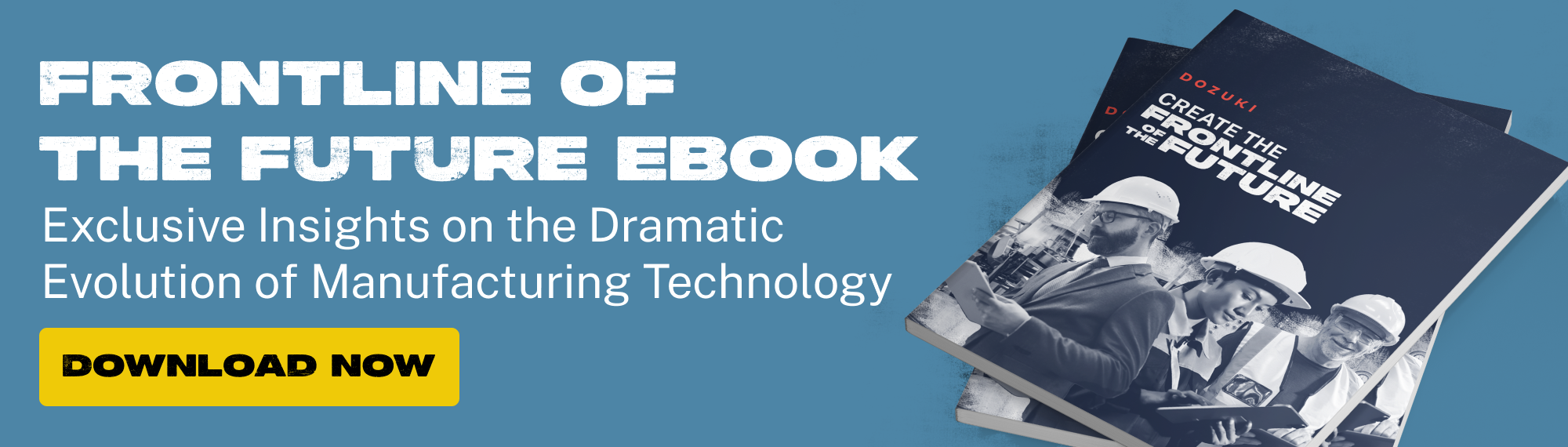
TQM Implementation Strategies
TQM is hard to define because it can look different depending on the specific company and its needs.
So, how exactly does an organization implement a total quality management system, especially when the TQM varies from company to company?
Below is a step-by-step guidebook to doing precisely that.
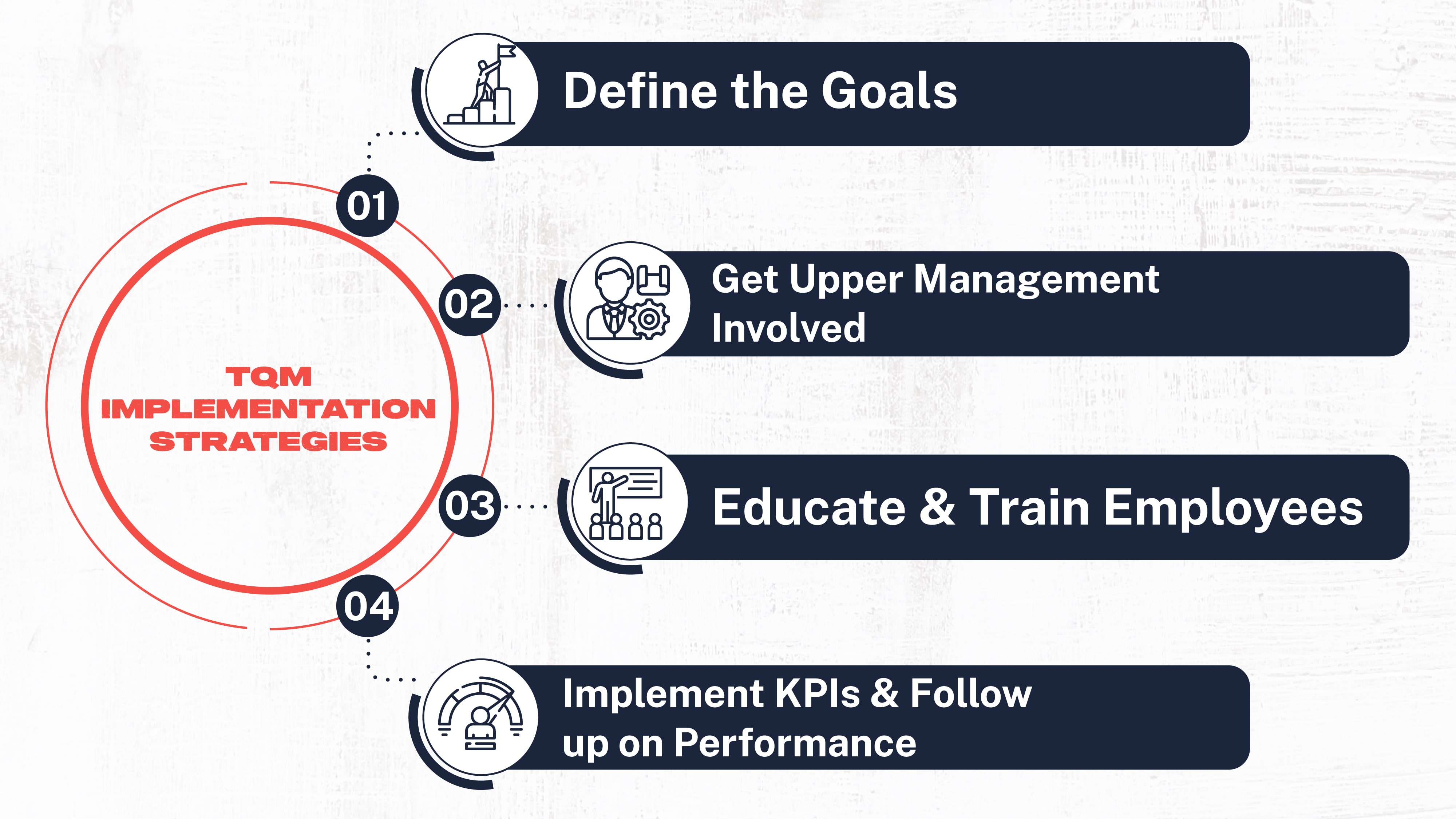
- Define the Goals
When kickstarting any new system or program, the first step should always be to figure out why. When it comes to TQM, the end goal is the customer.
But the reason needs to be more specific than that. Get into the specifics and look at the complex data. Where are the shortfalls happening? What precisely isn’t working from a quality standpoint?
Secondary to these specific goals should be organizational goals. Or, put another way, cultural shifts within the organization.
How should implementing a TQM change the company's culture, vision, and values? These are the things team members must recognize and accept if the outcome is successful.
- Get Upper Management Involved
As mentioned, nothing works without buy-in from the upper management folks. A TQM cannot be a system that puts forth the idea of “do as I say, not as I do.”
If upper management isn’t playing all-in, it won’t work. And that means dedicating time, resources, and energy to meeting objectives. And it means putting that same energy into the employees.
- Educate and Train Employees
This brings us to the most essential component of the TQM – the employees. These people are actively working to produce the products that will end up in the hands of your customers. These are the people that you are relying on to get it right.
Training workers in the principles of the TQM is the first step, followed by specific training showing them how to meet goals and objectives every day. Give them the tools to succeed, or everyone will fail together.
- Implement KPIs and Follow up on Performance
Once a plan is in place and employees are trained in expectations, the next step is to follow through. Remember to include specific key performance indicators to track progress.
Key performance indicators empower employees by giving them a measuring stick for their success. Ask questions. Get feedback. And identify areas where employees can make improvements.
Customer Centric Approach
Following through on a total quality management system by measuring specific KPIs within the organization itself is a great way to test the effectiveness of the strategies. But let's remember the goal of any TQM system: a happier and more satisfied customer.
Manufacturers must take stock of their progress internally, but more important is gathering customer feedback directly. Doing so maintains that goal of continuous improvement through the eyes of the customer.
It bolsters customer loyalty and helps organizations understand the needs and expectations of their customers.
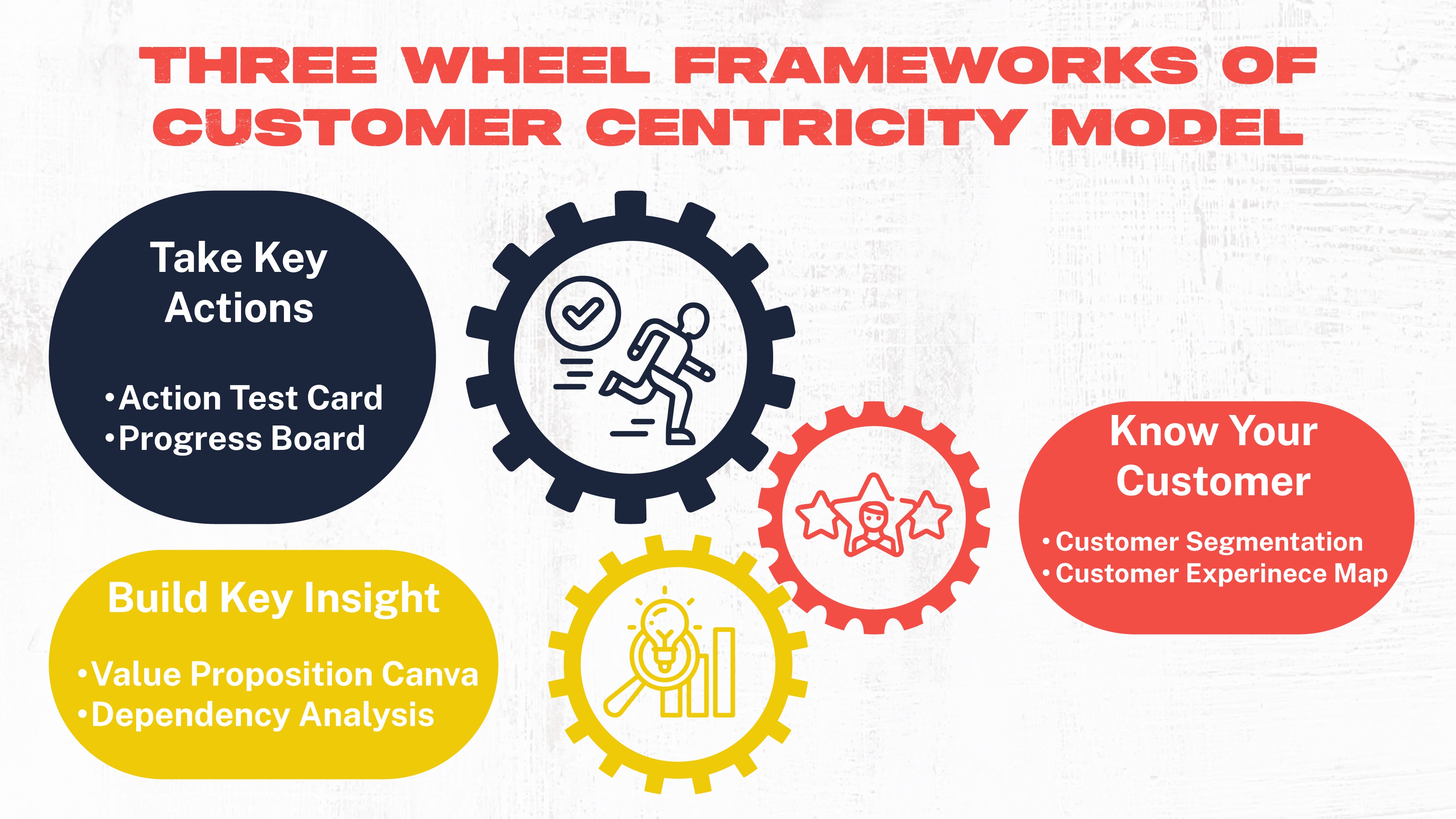
There are numerous ways to do this, and we’ve listed some ideas below.
- Social Media Monitoring
- Focus Groups
- Feedback Forms
- Testimonials
- Suggestions
The avenues that manufacturers must communicate with their customers are numerous. Some customers will seek out a company with their feedback, especially if it is negative. Others will be happy to provide it if given the opportunity.
Remember that regardless of how an organization solicits feedback from the customer, the most critical part of the process is to act.
Take note of those aspects customers appreciate and value. And seek to improve or rectify those things resulting in less-than-satisfied customers.
Building a TQM Culture
We briefly mentioned company culture earlier regarding setting a goal for a total quality management system. And we’re reiterating it here because of its importance.
Quality should be at the forefront of an organization’s cultural structure and it’s vital to understand what the word “culture” really means.
A culture can be defined as a set of values, beliefs, and behaviors that a group of people commonly shares.
In terms of TQM, that culture should support the principles of a total quality management approach. Focusing on the following characteristics or goals will help instill this culture into the fabric of an organization.
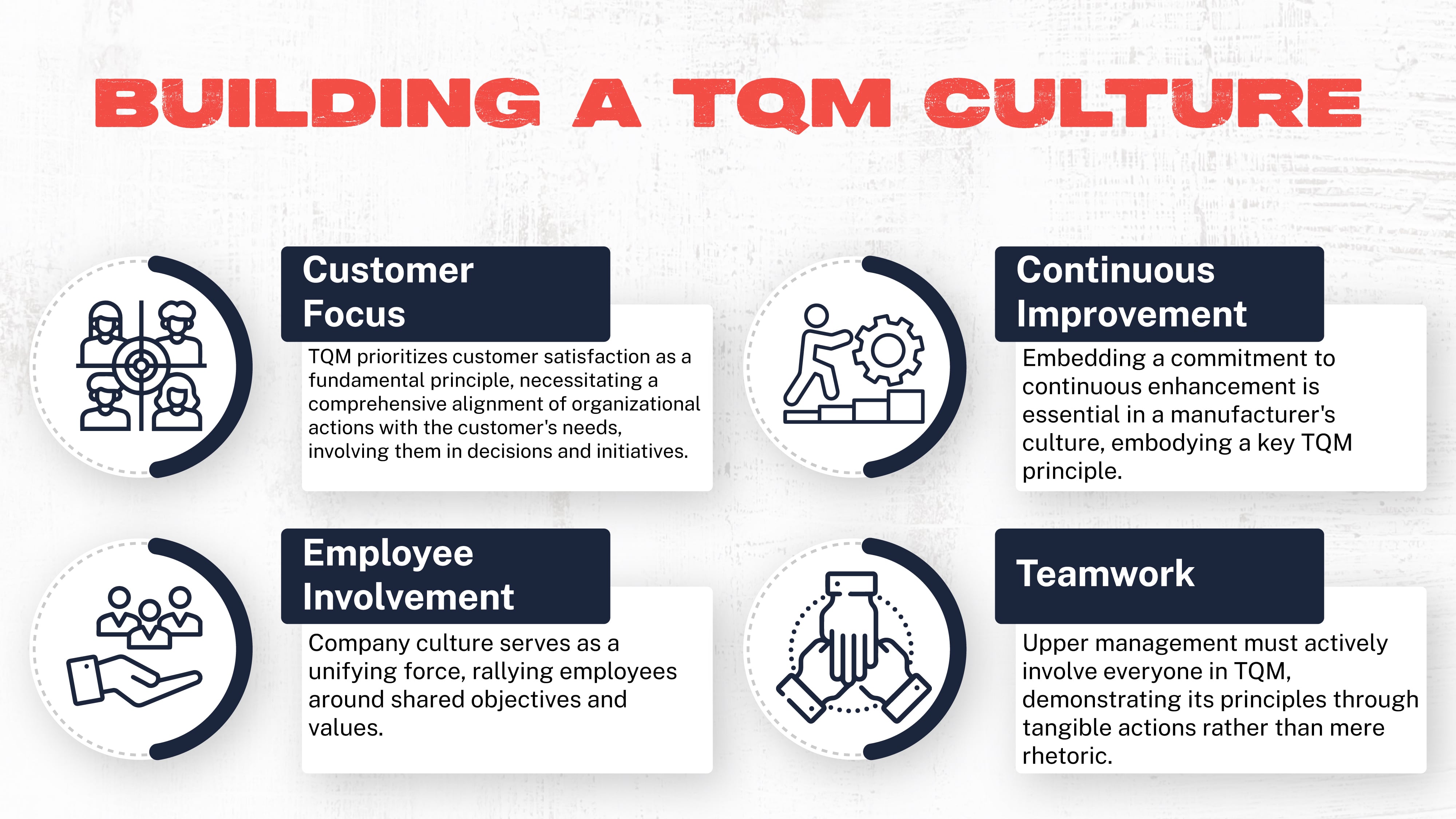
Customer Focus
Putting the customer first is a core principle of the TQM strategy. While it’s easy to draft a company vision statement that claims to do this, following through on it isn’t always as simple.
Customer focus requires consideration of every action the organization takes and its effect on the customer relationship. That means every budget cut, every employee initiative, every change in the production schedule. Include the customer as a member of the team.
A focus on continuous improvement should be at the core of every manufacturer’s culture. Striving always to find ways to improve is one of TQM's core principles.
Building this concept into an organization's fabric will profoundly affect virtually every performance indicator – increased productivity and efficiency, a higher-quality product, reduced costs, and a happier customer.
Employee Involvement
The culture of a company serves many purposes. It unites the employees under a single banner. It gives team members a common goal and vision. And it helps workers understand the positive values they’re working together to uphold.
Sometimes the idea of company culture gets lost in the jargon of business. Employees tire of hearing upper management members drone on in what they hear as "HR speak." That's why upper management needs to get everyone involved with the TQM. Employees need to see it in action, not just hear it from the higher-ups.
Quality Metrics & Performance Measurement
Every manufacturer understands the importance of KPIs. A key performance indicator is a measurable value that helps organizations visualize their success in achieving results.
Tracking KPIs is one of the most accurate and effective ways to ensure activities are aligned with a specific goal. And they're one of the most valuable ways to measure success.
Total quality management is a far-reaching goal. And because it's so hard to define, it's also hard to measure. That's why an organization needs to set specific goals within the framework of the TQM.
Those goals aren't immutable, of course. As the needs of the organization and the customer change, the plans should be revisited and realigned. But the overarching goal remains to provide a higher quality product for the customer.
Organizations can better track their progress by setting goals and defining specific KPIs related to those goals. And they can more easily identify those areas that need improvement. Below are a few helpful KPIs that relate directly to TQM.
- Customer Satisfaction
- Employee Engagement
- Process Efficiency
- Defect Rate
Supplier Quality Management
When discussing a total quality management system, remember that the quality of a product or service is dependent on every step in the production process. But what about those factors that lie outside of the factory floor?
The supply chain itself is an essential component of any TQM because it directly affects the quality of the outcome.
Does the TQM extend, then, to the supply chain and suppliers? It does. Bringing a focus on quality to the supply chain helps companies ensure that their products and services meet employee expectations.
And it provides that only the highest quality resources and materials are used in the production process, minimizing the risk of defects.
Applying TQM to the supply chain can initially seem tricky until organizations remember that many of the same techniques used on the factory floor can serve a similar purpose here. For example:
- Process Mapping
- Root Cause Analysis
- Corrective Action Plans
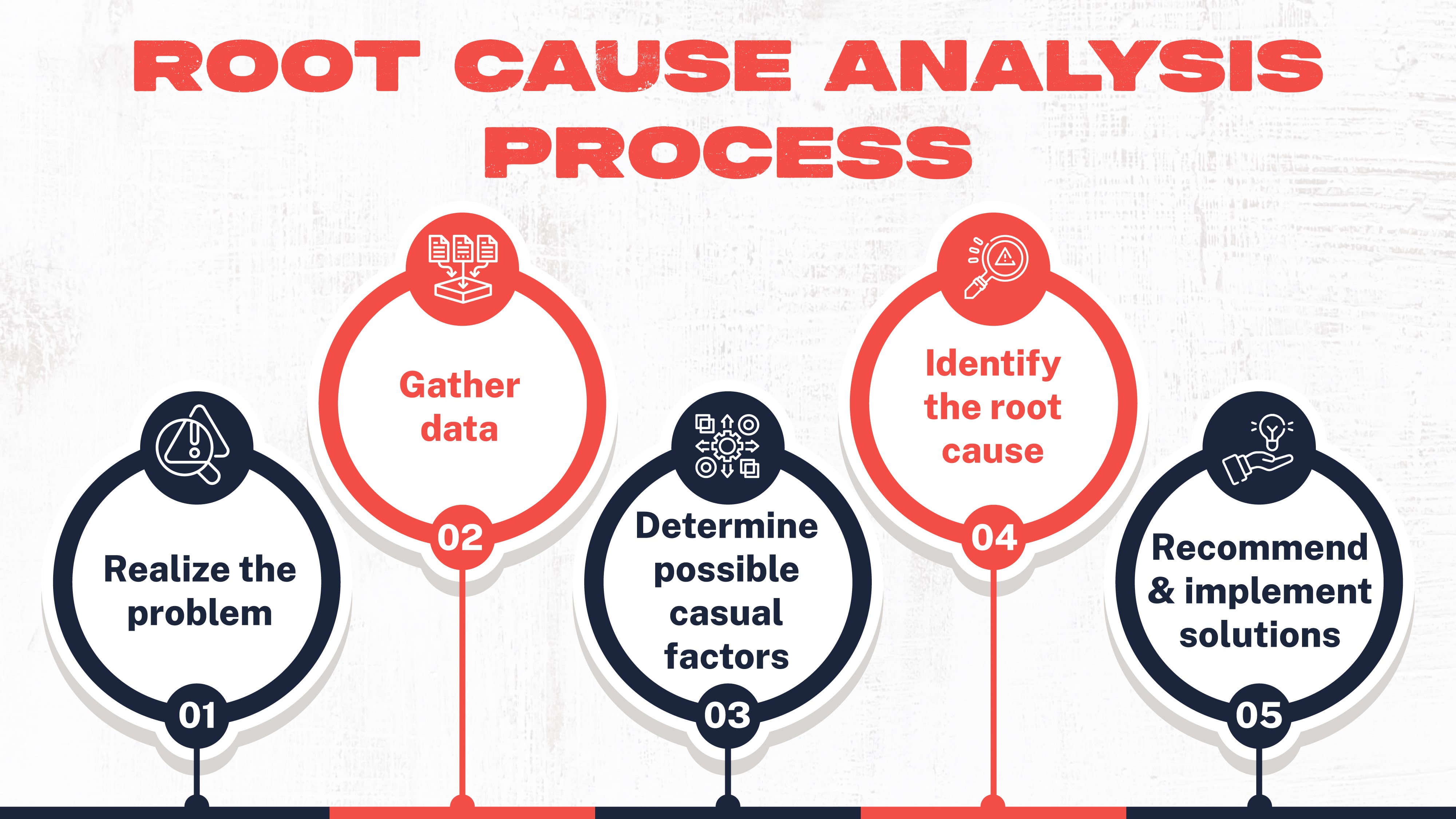
These tools are designed to uncover problems in a process and find a solution. Applying this kind of systematic problem-solving to issues within the supply chain can provide a significant benefit in the form of better overall performance and an improved ability to gain a competitive advantage.
Employee Training & Development
Employees are the backbone of the manufacturing industry. That’s a known fact. But within the structure of the total quality management system, employees are the fuel that makes the machine run.
Sure, you can put a plan in place for virtually anything, quality included. But without employee participation, that system is simply a stand-in – accomplishing little and just getting in the way.
However, if employees are considered a vital component of a TQM, everyone benefits.
TQM Benefits Employees
Employees allowed to operate within a company culture that prides on quality, thrive.
Employees are more engaged and motivated with their work when provided with the authority and responsibility to make decisions, which is at the core of the TQM. Employees working to bring a higher quality to their jobs are more satisfied overall and more productive within their roles.
The caveat is that this is true with proper training and development. Instilling the principles of the TQM into a labor force must start from the onboarding process and continue through the training process – and even further.
Employees who are provided the opportunity to learn, and apply what they have learned, will return the favor to the organization.
TQM Benefits the Organization
This concept of employee development goes both ways. TQM directly benefits employees. Employees, in turn, use the TQM system to benefit the company and its customers directly.
Given the proper framework and the tools to get the job done, employees can help create that culture of continuous improvement, learning to identify and solve problems to improve quality outcomes.
TQM Tools & Techniques
Instilling quality into every level of an organization is the goal of total quality management. The overarching principles should be instilled at the highest level and included as a sticking point within the company culture.
However, many organizations need help figuring out how to implement a quality management system in the right places.
Thankfully, manufacturers can use many tools, techniques, and methods to help improve the quality of their products and services.
Knowing which tools to use and where to use them will require a careful examination of the specific needs and requirements of the business and its customers.
Below are some of the most valuable tools when it comes to TQM.
- Cause-and-Effect Diagrams
- Pareto Charts
- Control Charts
- Check Sheets
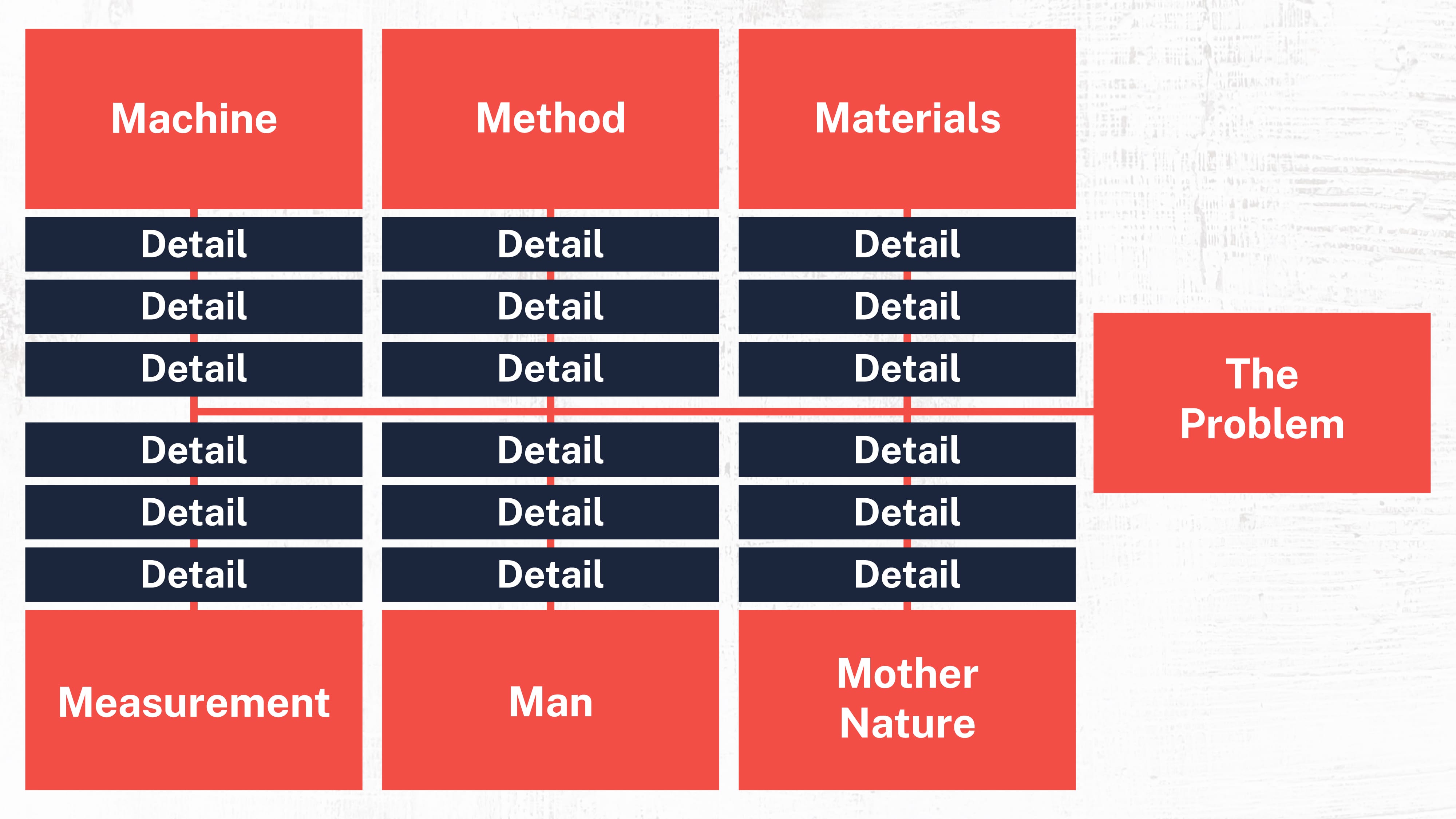
The common thread between these quality tools is visibility. Many of these types of charts and graphs rely on data.
Effectively using that data can help organizations identify what's working and what's not. Spotting snags in the system is the only way to improve.
Use the tool that best fits the specific need and matches the analyzed data type. And don’t overlook the benefits of the last two on the list: control charts and check sheets.
Yes, improving quality is dependent on identifying and solving problems. But it must also be ingrained in the daily activities of employees. Putting the right checks and controls in place reinforces this as an expected standard.
TQM & Continuous Improvement
We’ve covered the basics of total quality management, how it benefits organizations and employees, and how it centers on the customer first and foremost.
What must be reiterated is the correlation between TQM and continuous improvement. One cannot exist without the other, and both play an essential role within any manufacturing organization.
Continuous improvement is a concept that encourages companies to look for ways to be better constantly. From a quality standpoint, that means focusing on the customer experience.
Remember that a manufacturer is more than just products from a production line. It’s a complex organism of designers, suppliers, managers, engineers, maintenance technicians, forklift operators, and operators.
It’s salespeople, the marketing department, and the customer service representatives. Every single individual under the umbrella of an organization affects the quality of the overarching customer experience.
And therefore, every individual should be tasked with understanding the responsibility of their role and how it relates to quality.
Continuous improvement is only possible with the employees. And it becomes virtually impossible when an organization fails to empower employees to take ownership of their roles and outcomes.
Final Thoughts
Much has been said here about total quality management and its importance in manufacturing.
Quality management is a concept that uses tools and methods to help organizations improve the quality of their products and services. But the most important takeaway is that TQM is about more than the quality of the actual products. It’s about the quality of the customer relationship.
The customer is at the center of the universe regarding business. Every action taken within the scope of an organization should revolve around its eventual effects on the customer.
Focusing on producing quality products will create a happier and more loyal customer, as long as the guide starts with that customer. Listen to the customer. They pay the bills.

Written by Dozuki
Founded in 2011, Dozuki has been the leader in connected worker solutions for over a decade. We’ve helped hundreds of companies plan, implement, and scale our frontline digital transformation solution.
Related Posts
Quality assurance in manufacturing: an in-depth guide to achieve customer confidence.
It’s time to talk about quality. In this industry, quality is everything, and competition between manufacturers is fierce. Table of Content 1. Key Principles of Quality...

Overcoming Manufacturing Lead Time | What Is Lead Time & How To Reduce It?
Manufacturing companies rely on their ability to get products to customers quickly and efficiently. If it’s one thing customers are not, it’s understanding when it comes to...
Identifying Defects: How Root Cause Analysis Will Save Manufacturing
Manufacturing companies work hard to build a lean culture. The never-ending march toward the ideal of perfection through the motto of continuous improvement requires constant...
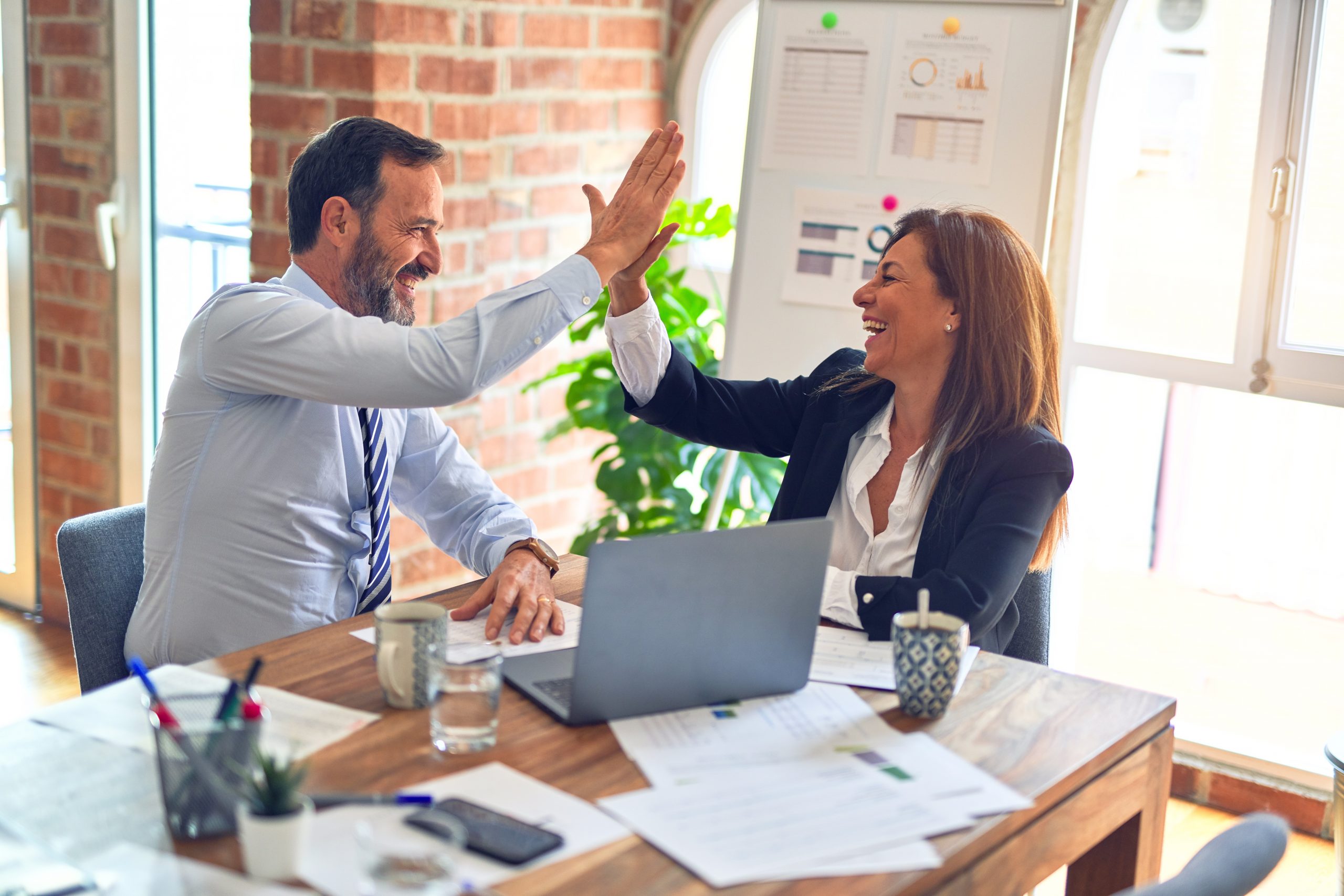
The Eight Elements of TQM
Published: February 26, 2010 by Nayantara Padhi
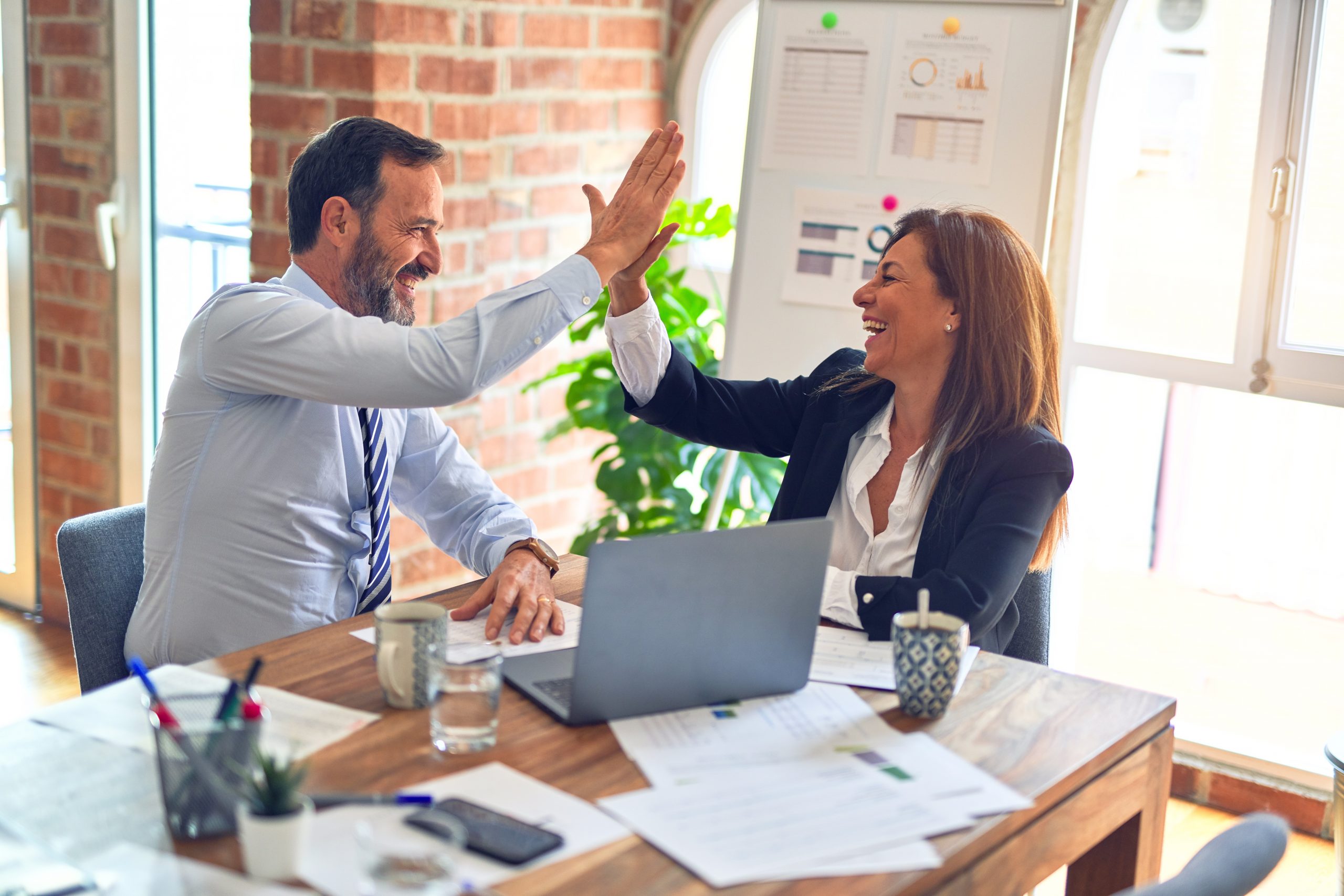
Total Quality Management (TQM) is a management approach that originated in the 1950s and has steadily become more popular since the early 1980s. Total quality is a description of the culture, attitude and organization of a company that strives to provide customers with products and services that satisfy their needs. The culture requires quality in all aspects of the company’s operations, with processes being done right the first time and defects and waste eradicated from operations.
To be successful implementing TQM, an organization must concentrate on the eight key elements:
- Recognition
- Communication
This paper is meant to describe the eight elements comprising TQM.
Key Elements
I. Foundation TQM is built on a foundation of ethics, integrity and trust. It fosters openness, fairness and sincerity and allows involvement by everyone. This is the key to unlocking the ultimate potential of TQM. These three elements move together, however, each element offers something different to the TQM concept.
1. Ethics – Ethics is the discipline concerned with good and bad in any situation. It is a two-faceted subject represented by organizational and individual ethics. Organizational ethics establish a business code of ethics that outlines guidelines that all employees are to adhere to in the performance of their work. Individual ethics include personal rights or wrongs.
2. Integrity – Integrity implies honesty, morals, values, fairness, and adherence to the facts and sincerity. The characteristic is what customers (internal or external) expect and deserve to receive. People see the opposite of integrity as duplicity. TQM will not work in an atmosphere of duplicity.
3. Trust – Trust is a by-product of integrity and ethical conduct. Without trust, the framework of TQM cannot be built. Trust fosters full participation of all members. It allows empowerment that encourages pride ownership and it encourages commitment. It allows decision making at appropriate levels in the organization, fosters individual risk-taking for continuous improvement and helps to ensure that measurements focus on improvement of process and are not used to contend people. Trust is essential to ensure customer satisfaction. So, trust builds the cooperative environment essential for TQM.
II. Bricks Basing on the strong foundation of trust, ethics and integrity, bricks are placed to reach the roof of recognition. It includes:
4. Training – Training is very important for employees to be highly productive. Supervisors are solely responsible for implementing TQM within their departments, and teaching their employees the philosophies of TQM. Training that employees require are interpersonal skills, the ability to function within teams, problem solving, decision making, job management performance analysis and improvement, business economics and technical skills. During the creation and formation of TQM, employees are trained so that they can become effective employees for the company.
5. Teamwork – To become successful in business, teamwork is also a key element of TQM. With the use of teams, the business will receive quicker and better solutions to problems. Teams also provide more permanent improvements in processes and operations. In teams, people feel more comfortable bringing up problems that may occur, and can get help from other workers to find a solution and put into place. There are mainly three types of teams that TQM organizations adopt:
A. Quality improvement teams or excellence teams (QITs) – These are temporary teams with the purpose of dealing with specific problems that often recur. These teams are set up for period of three to twelve months. B. Problem solving teams (PSTs) – These are temporary teams to solve certain problems and also to identify and overcome causes of problems. They generally last from one week to three months. C. Natural work teams (NWTs) – These teams consist of small groups of skilled workers who share tasks and responsibilities. These teams use concepts such as employee involvement teams, self-managing teams and quality circles. These teams generally work for one to two hours a week.
6. Leadership – It is possibly the most important element in TQM. It appears everywhere in organization. Leadership in TQM requires the manager to provide an inspiring vision, make strategic directions that are understood by all and to instill values that guide subordinates. For TQM to be successful in the business, the supervisor must be committed in leading his employees. A supervisor must understand TQM, believe in it and then demonstrate their belief and commitment through their daily practices of TQM. The supervisor makes sure that strategies, philosophies, values and goals are transmitted down through out the organization to provide focus, clarity and direction. A key point is that TQM has to be introduced and led by top management. Commitment and personal involvement is required from top management in creating and deploying clear quality values and goals consistent with the objectives of the company and in creating and deploying well defined systems, methods and performance measures for achieving those goals.
III. Binding Mortar 7. Communication – It binds everything together. Starting from foundation to roof of the TQM house, everything is bound by strong mortar of communication. It acts as a vital link between all elements of TQM. Communication means a common understanding of ideas between the sender and the receiver. The success of TQM demands communication with and among all the organization members, suppliers and customers. Supervisors must keep open airways where employees can send and receive information about the TQM process. Communication coupled with the sharing of correct information is vital. For communication to be credible the message must be clear and receiver must interpret in the way the sender intended.
There are different ways of communication such as: A. Downward communication – This is the dominant form of communication in an organization. Presentations and discussions basically do it. By this the supervisors are able to make the employees clear about TQM. B. Upward communication – By this the lower level of employees are able to provide suggestions to upper management of the affects of TQM. As employees provide insight and constructive criticism, supervisors must listen effectively to correct the situation that comes about through the use of TQM. This forms a level of trust between supervisors and employees. This is also similar to empowering communication, where supervisors keep open ears and listen to others. C. Sideways communication – This type of communication is important because it breaks down barriers between departments. It also allows dealing with customers and suppliers in a more professional manner.
IV. Roof 8. Recognition – Recognition is the last and final element in the entire system. It should be provided for both suggestions and achievements for teams as well as individuals. Employees strive to receive recognition for themselves and their teams. Detecting and recognizing contributors is the most important job of a supervisor. As people are recognized, there can be huge changes in self-esteem, productivity, quality and the amount of effort exhorted to the task at hand. Recognition comes in its best form when it is immediately following an action that an employee has performed. Recognition comes in different ways, places and time such as,
- Ways – It can be by way of personal letter from top management. Also by award banquets, plaques, trophies etc.
- Places – Good performers can be recognized in front of departments, on performance boards and also in front of top management.
- Time – Recognition can given at any time like in staff meeting, annual award banquets, etc.
We can conclude that these eight elements are key in ensuring the success of TQM in an organization and that the supervisor is a huge part in developing these elements in the work place. Without these elements, the business entities cannot be successful TQM implementers. It is very clear from the above discussion that TQM without involving integrity, ethics and trust would be a great remiss, in fact it would be incomplete. Training is the key by which the organization creates a TQM environment. Leadership and teamwork go hand in hand. Lack of communication between departments, supervisors and employees create a burden on the whole TQM process. Last but not the least, recognition should be given to people who contributed to the overall completed task. Hence, lead by example, train employees to provide a quality product, create an environment where there is no fear to share knowledge, and give credit where credit is due is the motto of a successful TQM organization.
About the Author
Nayantara Padhi
What is Total Quality Management?
How does total quality management (tqm) work, the key players in total quality management: customers, suppliers, and employees, implementing tqm principles and processes, history of total quality management, what are the principles of total quality management (tqm), customer focus, leadership commitment, employee involvement, process-oriented approach, continuous improvement, evidence-based decision making, supplier relationships, the seven basic tools of total quality management, examples of total quality management in action, related resources, total quality management (tqm).
A comprehensive approach to organizational management that emphasizes the continual pursuit of quality and operational excellence
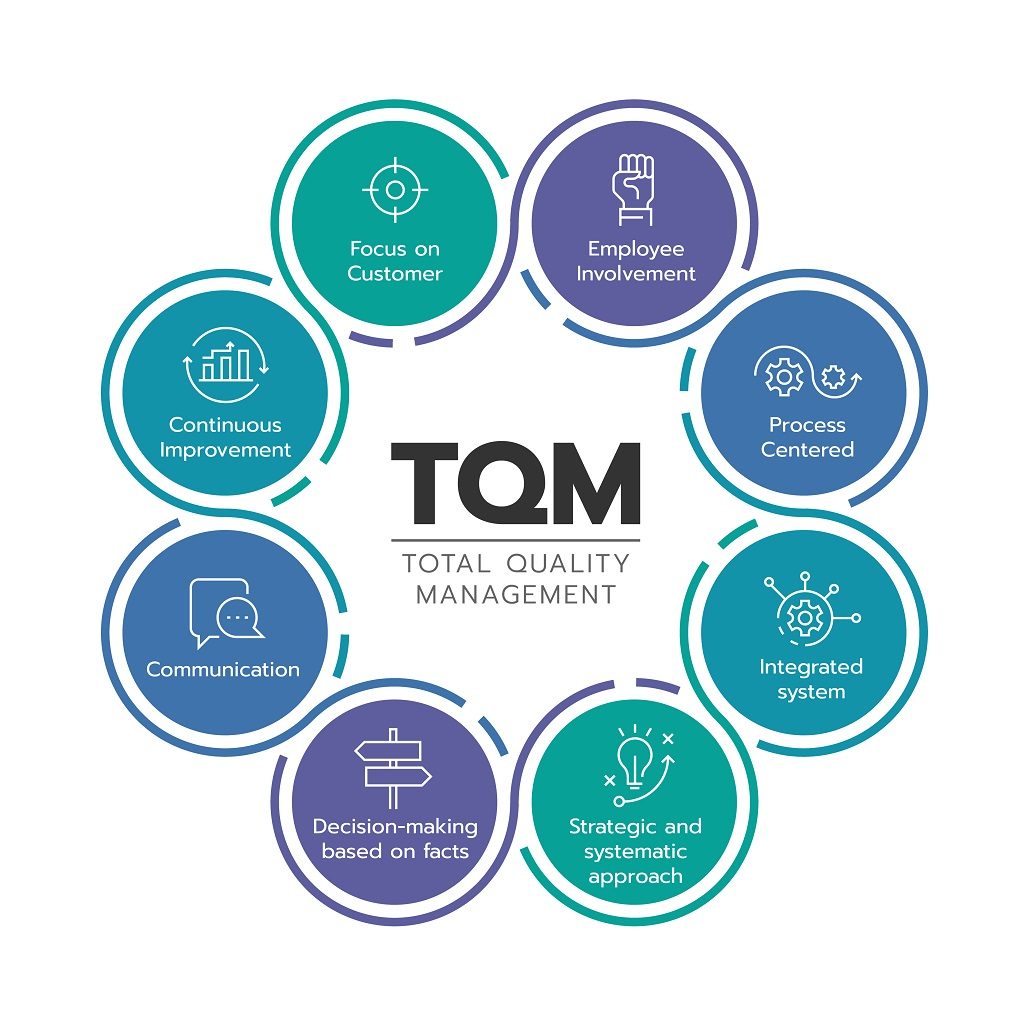
A commonly known quality management approach is Total Quality Management (TQM). This philosophical approach focuses on leading and achieving quality excellence in every aspect of an organization. It emphasizes continuous improvement , involving all employees in the pursuit of customer satisfaction .
TQM fosters a culture where quality is ingrained, encouraging teamwork , proactive problem-solving , and a commitment to excellence . By integrating quality into all processes and departments, TQM aims to eliminate defects, streamline operations, reduce waste, and enhance overall performance, ensuring long-term success and competitiveness in the market.
Key Highlights
- Total Quality Management (TQM) emphasizes continuous improvement, involving all employees in achieving quality excellence. It fosters a culture of ingrained quality, teamwork, proactive problem-solving, and commitment to excellence, aiming to eliminate defects, reduce waste, and enhance overall performance.
- TQM focuses on customer satisfaction, employee involvement, process-oriented approaches, continuous improvement, evidence-based decision-making, supplier relationships, and leadership commitment to drive a culture of quality excellence.
- TQM requires strong leadership commitment, systematic processes, and employee engagement. Real-world examples like Toyota Production System (TPS), Motorola’s Six Sigma, and healthcare sector applications illustrate TQM’s impact on quality enhancement in various industries.
Total Quality Management involves continuous improvement , leveraging data and metrics to make informed decisions, fostering a culture of teamwork and innovation, and aligning strategies with customer needs. Among the primary TQM principles is customer satisfaction – in other words, meeting and exceeding customer needs.
Quality is integral in every aspect of operations , with the goal of striving for excellence in products, services, and internal processes while adapting to evolving market demands. Satisfied customers is the outcome of such a quality-integrated system.
Related to TQM is the concept of Kaizen , a Japanese term for “continuous improvement.” This concept emphasizes incremental changes made by every employee. It’s ideal for organizations looking to instill a culture of constant, small-scale improvements. Kaizen encourages employee engagement , fosters creativity , and is effective in workplaces where innovation and adaptability are paramount .
In Total Quality Management (TQM), customers , suppliers , and employees play pivotal roles as key stakeholders contributing to quality assurance and quality control in an organization.
Customer focus is central ; customer satisfaction steers the direction of quality standards. Understanding the feedback they provide on-demand products, preferences, and experiences is fundamental to delivering products or services that surpass expectations.
Suppliers represent another critical element. They provide the raw materials and inputs necessary for a production process or insight into the planning phase of the overall manufacturing processes, directly impacting the quality of the final output. Collaborating closely with suppliers ensures consistency and reliability in the inputs, thus influencing the quality of the end product or service.
Employees must be on the same page as top management to properly apply total quality management tools. Examples include the integration of each production process as a holistic view of the overall manufacturing processes. The widely agreed-upon approach to TQM helps build integrated systems that foster customer satisfaction.
Empowering and engaging employees at all levels fosters a culture where everyone contributes ideas, innovation, and efforts toward achieving superior quality, ultimately benefiting the customers and the organization as a whole.
TQM processes are used to improve processes, instill an organizational commitment to quality assurance and quality control, and dedication to continuous improvement that materially drives customer satisfaction.
Implementing TQM requires strong leadership commitment to drive cultural change . Clear objectives aligned with the organization’s mission and vision are set, and resources are allocated for training and skill development.
Total Quality Management involves engaging employees at all levels, with effective communication that fosters a sense of ownership and empowerment. It relies on systematic data collection and analysis (such as benchmarking) to foster feedback loops for evidence-based decision-making (also known as the Plan-Do-Act-Check cycle of Kaizen).
Engagement of people is another one of a handful of total quality management principles. Effective communication is vital, ensuring everyone understands their role in achieving quality goals, promoting transparency, and encouraging collaboration across departments.
Total Quality Management (TQM) originated in the early 20th century with statistical quality control methods in manufacturing. However, its systematic development gained prominence post-World War II.
A key influencer is Dr. W. Edwards Deming, who introduced principles focusing on statistical methods, process improvement, and employee involvement.
Japan notably embraced TQM in its post-war reconstruction era, propelling the nation’s economic resurgence by applying Deming’s principles. Japan’s success in quality and productivity spurred global interest in TQM during the 1980s.
Western countries implement total quality management in response to intense market competition. Alongside the economic shift beyond the manufacturing sector, the versatile approach was adopted in a variety of service sectors, such as healthcare.
Today, TQM is the foundation of many quality approaches, emphasizing customer-centricity, continual improvement, and organizational excellence, influencing operational strategies worldwide.
The American Society of Quality (ASQ) is an international organization sought by companies seeking to implement strong quality management systems. The international organization advocates for the ISO 9000 family of standards ,
Total Quality Management (TQM) encompasses a set of fundamental guidelines aimed at fostering a culture of quality excellence within an organization. The American Society of Quality (ASQ) outlines seven principles within their strategic and systematic approach (ISO 9000).
Understanding, meeting, and exceeding customer expectations is at the core of TQM. With proper training, TQM focuses on an enduring organizational culture to anticipate and respond to customer input and feedback (i.e., customer satisfaction) as the key concept to remain competitive.
Active management participation to demonstrate their dedication and involvement in championing quality management initiatives throughout the entire organization. To achieve success, the core values of delivering quality are inherent in TQM strategies.
Encourage and empower employees at all levels to contribute ideas and efforts in a continuous effort to achieve quality improvement. Total employee involvement integrates quality throughout the production cycle. Quality-related issues and other immediate process issues are addressed promptly.
Emphasizing systematic and structured methods for achieving quality goals. The systematic approach to process improvements is customer-focused, with quality planning to improve service quality throughout the customer journey.
The core component of TQM is the commitment to delivering quality and the continuous effort to improve the quality of products and services. TQM strives to achieve excellence and total quality control as part of the strategic plan of optimizing and improving processes.
Tools must collect and apply accurate data and rigorous analysis to drive informed decisions. Basic tools and organizational performance data used by TQM practices can span cross-functional teams.
Supply chain management is a critical component of modern quality control. Companies collaborate closely with suppliers to ensure joint quality planning, from basic raw materials and inputs, as part of an integrated system of business processes and production processes.
These principles collectively aim to cultivate a culture where quality is everyone’s responsibility, striving for excellence and continuous advancement in all aspects of the organization to meet or exceed customer expectations.
The American Society of Quality (ASQ) attributes attributes “the basic seven” tools of quality, sometimes known as 7 QC (Quality Control) tools, to Kaoru Ishikawa . These quality management tools are instrumental in analyzing data, identifying problems, understanding processes, and making informed decisions to improve quality within an organization.
| Visual tools to identify and analyze contributing to a or . |
| Simple forms or charts to and data systematically, facilitating easy analysis. |
| Statistical graphs and track , distinguishing between common causes and assignable causes of variations. |
| Common graph for data , helping users identify variations and patterns in a dataset. |
| to display factors in of , useful to highlight the most significant issues. |
| A visualizes the relationships between two variables to identify correlations or trends. |
| Diagrams illustrating the , aiding in understanding and optimizing workflows. |
Often cited as a prime example of TQM, , it emphasizes continuous improvement, elimination of waste, and respect for people. It includes practices like manufacturing and Kaizen (continuous improvement) to enhance quality and efficiency in manufacturing processes. | |
Motorola developed the . It is a quality management technique focused on reducing defects and variation in processes. This management system and approach to process thinking have been widely adopted by other industries to drive quality improvement | |
Hospitals and healthcare institutions implement TQM principles to enhance patient care, reduce medical errors, and streamline processes. For example, using improves efficiency in emergency room operations or in reducing patient waiting times. |
Thank you for reading CFI’s guide to Total Quality Management (TQM). To keep learning and developing your knowledge base, please explore the additional relevant resources below:
- Quality Management
- Decision Analysis (DA)
- Supply Chain
- See all management & strategy resources
- Share this article
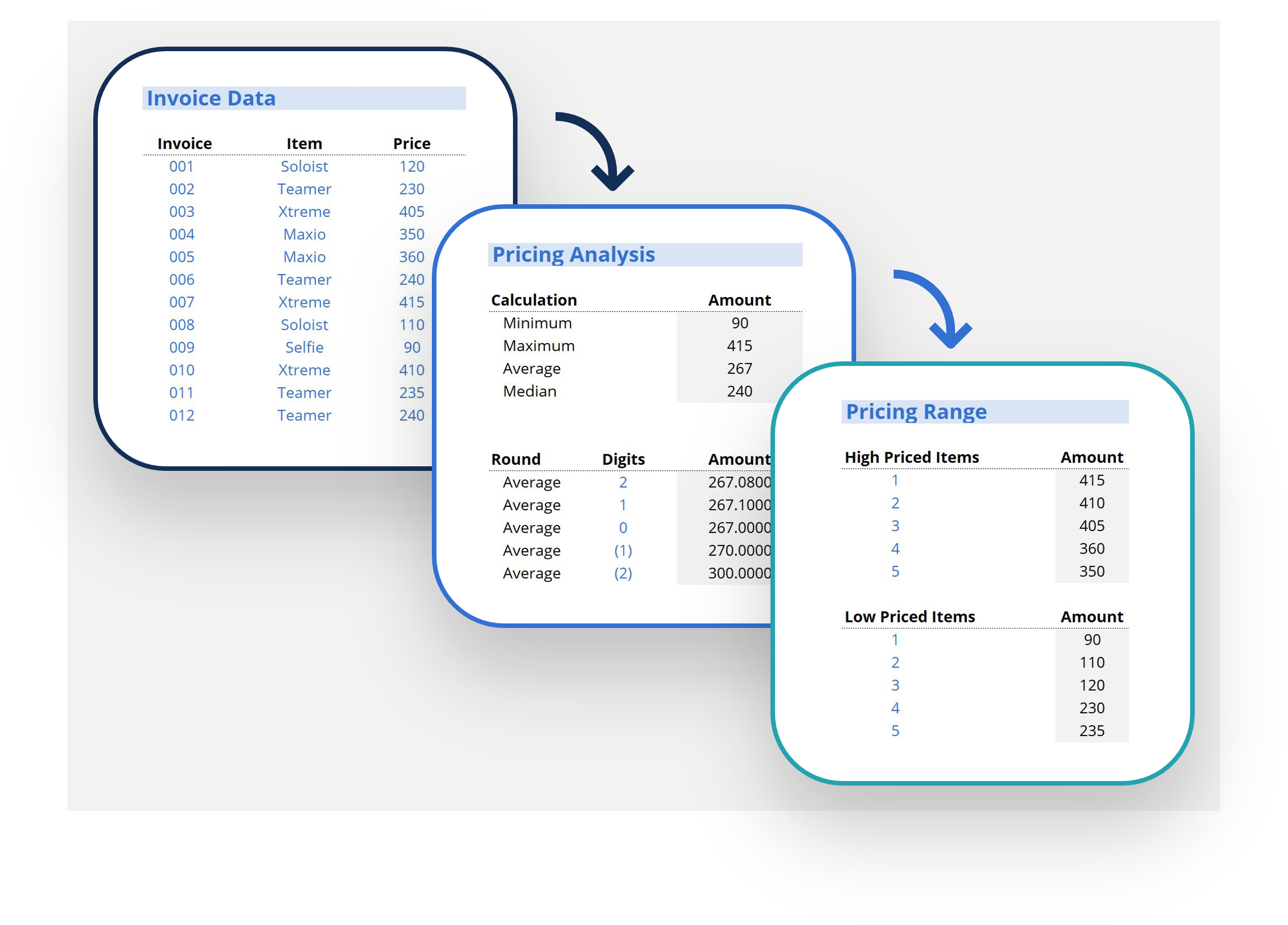
Create a free account to unlock this Template
Access and download collection of free Templates to help power your productivity and performance.
Already have an account? Log in
Supercharge your skills with Premium Templates
Take your learning and productivity to the next level with our Premium Templates.
Upgrading to a paid membership gives you access to our extensive collection of plug-and-play Templates designed to power your performance—as well as CFI's full course catalog and accredited Certification Programs.
Already have a Self-Study or Full-Immersion membership? Log in
Access Exclusive Templates
Gain unlimited access to more than 250 productivity Templates, CFI's full course catalog and accredited Certification Programs, hundreds of resources, expert reviews and support, the chance to work with real-world finance and research tools, and more.
Already have a Full-Immersion membership? Log in

The Leading Source of Insights On Business Model Strategy & Tech Business Models

Total Quality Management (TQM) Framework In A Nutshell
The Total Quality Management (TQM) framework is a technique based on the premise that employees continuously work on their ability to provide value to customers. Importantly, the word “total” means that all employees are involved in the process – regardless of whether they work in development, production, or fulfillment.
Component | Description |
---|---|
Total Quality Management emerged in the mid-20th century and was popularized by thought leaders such as W. Edwards Deming and Joseph Juran. | |
Total Quality Management is a comprehensive approach to improving the quality of products, services, and processes within an organization. It emphasizes a customer-centric focus, continuous improvement, and employee involvement to achieve excellence in all aspects of operations. | |
– TQM places a strong emphasis on understanding and meeting customer needs and expectations. Customer satisfaction is a central goal. | |
– Organizations practicing TQM are committed to ongoing enhancement of processes and products through incremental changes. | |
– TQM encourages active participation and empowerment of employees at all levels to contribute to quality improvement. | |
– TQM promotes a process-centric approach, with a focus on identifying, analyzing, and improving key processes. | |
– Data and metrics play a crucial role in TQM, guiding decision-making and performance measurement. | |
– Collaboration with suppliers is essential to ensure the quality of incoming materials and components. | |
TQM involves the following principles and practices: | |
1. Top management demonstrates a strong commitment to quality and sets the tone for the organization. | |
2. Continuous training and skill development ensure that employees can contribute effectively to quality improvement. | |
3. Identify processes, analyze them for inefficiencies, and implement changes to enhance quality and efficiency. | |
4. Regularly gather and analyze customer feedback to make improvements based on their needs and preferences. | |
5. Collaborate closely with suppliers to ensure the quality of materials and components. | |
6. Collect and analyze data to identify trends, monitor performance, and make informed decisions. | |
– TQM has been widely applied in manufacturing industries to enhance product quality and reduce defects. | |
– It is also used in service sectors like healthcare, hospitality, and finance to improve customer experiences. | |
– Government agencies adopt TQM principles to enhance efficiency and service delivery. | |
– TQM leads to higher-quality products and services, reducing defects and errors. | |
– Enhanced customer focus results in improved customer satisfaction and loyalty. | |
– Streamlined processes and reduced waste lead to greater operational efficiency. | |
– TQM can provide a competitive edge by delivering superior quality. | |
– Implementing TQM requires significant time, effort, and resources. | |
– Employees may resist changes associated with TQM initiatives. | |
– TQM can be complex to implement and sustain in large organizations. | |
Total Quality Management is a holistic approach to achieving excellence in quality, focusing on customer satisfaction, continuous improvement, and employee involvement. It is applied in various industries to enhance quality, efficiency, and competitiveness. While it offers numerous benefits, it demands commitment and resources for successful implementation. TQM is a dynamic process that adapts to changing customer needs and market conditions. |
Table of Contents
Understanding the TQM framework
The TQM framework was developed by management consultant William Deming who introduced it to the Japanese manufacturing industry.
Today, Toyota is perhaps the best example of the TQM framework in action. The carmaker has a “customer first” focus and a commitment to continuous improvement through “total participation”.
The focus of the TQM framework is the continual improvement of all processes with an organization, irrespective of whether they have a direct impact on customer satisfaction.
Improvement comes from identifying and then removing or reducing errors that commonly occur in supply chain management, manufacturing, employee training, and customer experience.
The process of problem-solving and adding value to the customer experience is one where every individual takes an active role.
8 principles of Total Quality Management
While there is no universal approach to implementing a TQM framework, many businesses use the following eight principles. These are evergreen principles that can be applied to any industry and are incorporated in more modern management techniques.
1. Customer-focused
The TQM framework acknowledges that the customer is the final determiner of whether company processes are sufficiently high quality.
If the customer is not satisfied, then the company must refocus its efforts on understanding consumer needs and expectations on a deeper level.
2. Employee engagement
Engaged employees are empowered employees who are not fearful of losing their jobs. As a result, they have the confidence and experience to suggest and implement continuous improvement across many systems.
3. Process approach
Refining process is a fundamental component of the TQM framework. Here, refinement means processes are followed in a logical order to ensure consistency and increased productivity.
Flowcharts and visual action plans can be produced so that employees understand their responsibilities.
4. System integration
System integration means that every single employee in a company has a reasonable understanding of policies, standards, and objectives.
It is vital employees understand their roles and how they contribute to the greater success of the company – no matter how insignificant those contributions may seem.
5. Strategic and systematic approach
A business must develop strategies that are quality-centric.
Company mission statements and their associated goals and values should also reflect the quality-first approach to customer satisfaction.
6. Continual improvement
Continual improvement is important in developing a competitive advantage and also in meeting stakeholder expectations.
Toyota’s model for continual improvement places a high emphasis on employee participation, eliminating waste, and reducing bureaucracy.
These factors increase innovation and reduce costs, which ultimately flow to the consumer.
7. Decision-making based on facts
Informed decisions are derived from a deep understanding of a business’s market and its target audience.
Wherever possible, data should be collected to support employee experience and intuition concerning creating value for consumers.
8. Communication
Communication is an often overlooked yet vitally important part of any successful company.
It plays a key role in clarifying expectations while also increasing employee morale and motivation.
Communication also increases collaboration and innovation between previously separate departments in a single company.
How is TQM implemented?
TQM is implemented by following the PDCA cycle, a model that originated in the 1920s that is a core component of many modern quality frameworks.
Although the model was created by engineer and statistician Walter Shewhart, Deming was the one who was responsible for its wide distribution and so it is often called the Deming cycle.
With that said, below is a look at each of the four stages that comprise this cycle:
The most important stage where affected stakeholders come together to determine the root cause of a problem via detailed research or analysis such as the Fishbone diagram , 5 Whys , or Failure Mode and Effects Analysis (FMEA).
In the second stage, the stakeholders develop solutions to the problems identified in the planning stage.
Unlike Six Sigma , the PDCA cycle focuses more on whether employees deem a solution to be effective and less on measuring concrete gains.
Where a before-and-after check is performed to determine the effectiveness of the solution.
Any data can be compared to expected outcomes to ensure objectives are being met. Successful solutions should then be incorporated into broader processes and procedures to avoid problem recurrence.
In the context of the TQM framework, the fourth and final stage encourages decision-makers to present the results of the test to relevant stakeholders to tell them what has occurred and to chart a way forward.
TQM and the costs of quality
A fundamental component of the Total Quality Management framework is that the cost of doing something the right way is far less than doing it the wrong way and having to fix the mistake.
Nevertheless, some critics of the framework consider that the process of maintaining quality has an associated cost that cannot be recouped by the business.
To counter this view, Deming along with colleagues Joseph M. Juran and Armand V. Feigenbaum reframed the cost of quality as the cost of not producing a quality deliverable. These costs, they posited, were applicable across four categories:
- Prevention costs – or costs related to the creation of work areas that are safe and efficient. Prevention costs also encompass planning, training, and the conducting of regular reviews. The researchers noted that activities related to prevention were often allocated a minuscule amount of the company’s budget.
- External failure costs – these are costs incurred once a product has been released in the market, such as returns, repairs, recalls, or warranty claims.
- Internal failure costs – or the cost of any failure before the product has been released. Typical internal failures include faulty machinery, improper or poor quality raw materials, product design that requires multiple revisions, and scrapped product runs.
- Appraisal costs – these cover the cost of inspection and testing during the product development lifecycle, such as the evaluation of supplier materials.
Total Quality Management vs. Six Sigma

Similar to total quality management, Six Sigma also seeks to reduce errors.
The specificity of Six Sigma is that if limits govern a process error that separates good and bad process outcomes, the Six Sigma approach has a process mean (average) that is six standard deviations from each limit.
This, Motorola found, provided enough buffer for natural variation in process outcomes to fall within the lower and upper limits.
Six Sigma usually goes through the following process:
- Analyze data
- Improve processes
- Control future implementations
And with the help of the following implementation roles:
- Executive leadership
- Master Black Belts
- Black Belts
- Green Belts
Drawbacks of Using Total Quality Management (TQM):
While TQM is a powerful approach to quality improvement, it has some limitations and potential drawbacks:
1. Time-Consuming:
Implementing TQM requires a significant time investment to develop, implement, and sustain quality improvement initiatives.
2. Cultural Resistance:
Organizational culture may resist changes associated with TQM, leading to resistance from employees and management.
3. Resource-Intensive:
TQM often requires additional resources, including training, technology, and quality control processes, which can strain budgets and operational efficiency.
4. Complex Implementation:
TQM implementation can be complex, especially in larger organizations with multiple departments, making it challenging to coordinate efforts effectively.
5. Potential for Overemphasis on Metrics:
Overemphasis on metrics and data collection in TQM may lead to a focus on quantity over quality in some cases.
When to Use Total Quality Management (TQM):
TQM is valuable in various scenarios within an organization:
1. Quality Improvement:
Use TQM when aiming to improve product or service quality, reduce defects, and enhance customer satisfaction.
2. Process Optimization:
Implement TQM to optimize internal processes, increase efficiency, and reduce waste.
3. Cultural Transformation:
TQM is beneficial when an organization seeks to foster a culture of continuous improvement and quality excellence.
4. Customer-Centric Approach:
TQM helps organizations prioritize a customer-centric approach by meeting or exceeding customer expectations.
How to Use Total Quality Management (TQM):
Implementing TQM effectively involves several key steps:
1. Leadership Commitment:
Top management must commit to TQM principles and lead by example to drive cultural change.
2. Employee Involvement:
Involve all employees in quality improvement efforts, encouraging them to identify and address issues.
3. Customer Focus:
Understand customer needs and expectations, and use them as a basis for quality improvement initiatives.
4. Data-Driven Decisions:
Collect and analyze data to identify areas for improvement and make informed decisions.
5. Continuous Improvement:
Promote a culture of continuous improvement, where employees actively seek ways to enhance processes and products.
6. Training and Education:
Provide training and education to employees to ensure they have the necessary skills and knowledge for quality improvement initiatives.
7. Quality Tools and Techniques:
Utilize quality management tools and techniques such as Six Sigma, Lean, and the PDCA (Plan-Do-Check-Act) cycle.
8. Standardization:
Standardize processes and procedures to reduce variability and improve consistency.
9. Communication:
Maintain open and effective communication channels throughout the organization to share information and progress on quality initiatives.
What to Expect from Implementing Total Quality Management (TQM):
Implementing TQM can lead to several outcomes and benefits:
1. Improved Quality:
TQM initiatives lead to improved product or service quality, reduced defects, and higher customer satisfaction.
2. Increased Efficiency:
Optimized processes and reduced waste result in increased operational efficiency and cost savings.
TQM fosters a culture of continuous improvement, empowering employees to take ownership of quality.
4. Enhanced Customer Loyalty:
Meeting or exceeding customer expectations through TQM efforts builds customer loyalty and brand reputation.
5. Competitive Advantage:
TQM can provide a significant competitive advantage by delivering high-quality products and services.
6. Data-Driven Decision-Making:
TQM encourages data-driven decision-making, leading to better-informed and more effective strategies.
In conclusion, Total Quality Management (TQM) is a powerful approach to quality improvement and organizational excellence.
While it has its drawbacks and challenges, understanding when to use it and how to apply it effectively can lead to improved quality, customer satisfaction, and operational efficiency.
By following the steps outlined in the framework and recognizing its potential benefits and drawbacks, organizations can leverage TQM to achieve continuous improvement and maintain a competitive edge in their industries.
Case Studies
Automotive Industry:
- Toyota’s Lean Manufacturing: Toyota’s successful implementation of TQM principles through Lean Manufacturing has not only improved product quality but also reduced waste and increased production efficiency.
- Ford’s Six Sigma Initiatives: Ford extensively utilizes Six Sigma methodologies to enhance product quality, eliminate defects, and optimize manufacturing processes.
- Honda’s Quality Circles: Honda’s commitment to quality circles allows employees to actively participate in identifying and resolving quality-related issues, contributing to continuous improvement.
Hospitality Industry:
- Marriott International’s Customer-Centric Approach: Marriott’s TQM approach revolves around ensuring exceptional customer experiences, personalized services, and high levels of customer satisfaction.
- Ritz-Carlton’s Service Excellence: Ritz-Carlton has set industry standards for service quality by emphasizing attention to detail, employee training, and service consistency.
Aerospace Industry:
- Boeing’s Quality Control: Boeing’s aerospace products adhere to rigorous quality control standards to ensure safety, reliability, and compliance with industry regulations.
E-commerce Industry:
- Amazon’s Customer Service Excellence: Amazon’s relentless focus on customer service quality and satisfaction has made it a leader in the e-commerce industry.
Healthcare Industry:
- Mayo Clinic’s Patient-Centric Care: Mayo Clinic’s TQM approach prioritizes patient safety, medical excellence, and continuous improvement in healthcare delivery.
- Johnson & Johnson’s Product Safety: Johnson & Johnson is dedicated to ensuring the safety and quality of its healthcare products through robust quality assurance practices.
Logistics Industry:
- FedEx’s Supply Chain Efficiency: FedEx places a strong emphasis on logistics efficiency, on-time deliveries, and error reduction to maintain its industry-leading position.
Technology Industry:
- Microsoft’s Software Quality Assurance: Microsoft’s TQM practices include rigorous software testing, security measures, and continuous improvement to provide reliable and secure products.
- Apple’s Product Quality: Apple maintains high product quality standards and user experience by implementing TQM principles in product design , manufacturing, and customer support.
Airline Industry:
- Southwest Airlines’ Employee Empowerment: Southwest Airlines promotes employee engagement and empowerment, leading to exceptional customer service and operational efficiency.
Electronics Industry:
- Samsung’s Quality Assurance: Samsung ensures the quality, performance, and reliability of its electronic products through comprehensive quality assurance processes.
Coffee Industry:
- Starbucks’ Coffee Excellence: Starbucks maintains the quality of its coffee beans, beverage preparation, and customer experience across its global chain of coffeehouses.
Diverse Industry Applications:
- General Electric’s Six Sigma Success: General Electric’s extensive use of Six Sigma methodologies has resulted in substantial cost savings, process improvements, and enhanced quality control across its diverse business divisions.
- Walmart’s Supply Chain Management: Walmart leverages TQM principles in its supply chain management to reduce costs, minimize errors, and improve inventory control.
Key takeaways
- The TQM framework is an approach to long-term success by increasing customer satisfaction through the reduction or elimination of errors.
- At its core, the TQM framework emphasizes a total commitment to long-term change through a cohesive and collaborative approach to employee problem-solving.
- The TQM framework utilizes eight principles with a focus on customers, communication, employees, and incremental improvements.
Key Highlights
- TQM Overview: Total Quality Management (TQM) is a management approach that focuses on continuous improvement and the provision of value to customers. It was developed by management consultant William Deming and introduced to the Japanese manufacturing industry.
- Customer-Centric: TQM places the customer at the center of quality determination. Customer satisfaction is the ultimate measure of the effectiveness of company processes.
- Employee Engagement: Engaged employees are empowered to contribute to continuous improvement, as they are not afraid of repercussions. They actively participate in identifying and implementing improvements across various systems.
- Process Approach: TQM emphasizes refining processes to ensure consistency and increased productivity. Flowcharts and visual action plans are used to ensure logical process order.
- System Integration: All employees in a company should understand the policies, standards, and objectives. Each employee’s role and contribution to the company’s success are significant, regardless of their function.
- Strategic Approach: TQM encourages the development of quality-centric strategies, ensuring that company goals and values reflect a customer-first approach.
- Continual Improvement: TQM promotes a culture of continuous improvement, aiming to gain a competitive advantage, meet stakeholder expectations, and reduce costs.
- Data-Driven Decision-Making: Informed decisions are made by collecting data to understand the market, target audience, and customer needs, enhancing the ability to add value to the customer experience.
- Communication: Effective communication plays a pivotal role in increasing employee morale, collaboration, and innovation . It fosters a holistic understanding of the company’s objectives.
- Implementation Process – PDCA Cycle: TQM is implemented through the Plan-Do-Check-Act (PDCA) cycle, a model introduced by Walter Shewhart and popularized by Deming.
- Plan (P): Stakeholders collaborate to identify the root cause of a problem through analysis methods like Fishbone diagrams or 5 Whys.
- Do (D): Solutions to identified problems are developed and implemented based on employee feedback and effectiveness.
- Check (C): Effectiveness of solutions is assessed through before-and-after comparisons, ensuring objectives are met. Successful solutions are integrated into broader processes.
- Act (A): Results of the test are presented to stakeholders, and a plan for moving forward is charted.
- Costs of Quality: TQM emphasizes that the cost of ensuring quality is less than fixing mistakes. Critics’ concerns about quality costs are countered by viewing them as the cost of not producing quality deliverables.
- Cost Categories: Costs of quality are divided into prevention costs (creating safe and efficient work areas), external failure costs (post-release issues), internal failure costs (pre-release issues), and appraisal costs (inspection and testing).
- TQM vs. Six Sigma: TQM and Six Sigma both focus on reducing errors and continuous improvement. Six Sigma is data-driven and aims to reduce defects by setting specific process error limits (Six Sigma level).
- Key Benefits: TQM leads to long-term success by enhancing customer satisfaction through error reduction and continuous improvement. It emphasizes a collaborative approach to employee problem-solving and a commitment to change.
Companion/Related Frameworks | Description | Implications |
---|---|---|
Total Quality Management (TQM) | Total Quality Management (TQM) is a management approach focused on continuously improving the quality of products, services, and processes within an organization. It involves a systematic commitment to quality across all aspects of the organization, including leadership, employee involvement, process improvement, customer focus, and continuous learning and innovation. | TQM emphasizes a culture of quality, customer satisfaction, and continuous improvement throughout the organization. By adopting TQM principles and practices, organizations can enhance product and service quality, increase customer loyalty and satisfaction, reduce costs and waste, and drive sustainable growth and competitiveness in the marketplace. |
Six Sigma | Six Sigma is a data-driven methodology for improving business processes and reducing defects or errors in products or services. It focuses on identifying and eliminating variation and defects through rigorous statistical analysis, process optimization, and problem-solving techniques. Six Sigma aims to achieve near-perfect performance by targeting a maximum of 3.4 defects per million opportunities (DPMO). | Six Sigma complements TQM by providing a structured and data-driven approach to process improvement and quality management. By applying Six Sigma methodologies such as DMAIC (Define, Measure, Analyze, Improve, Control), organizations can identify root causes of defects, optimize processes, and achieve measurable improvements in quality, efficiency, and customer satisfaction, aligning with the principles of TQM. |
Lean Management | Lean Management, often referred to as Lean Manufacturing or Lean Enterprise, is a management philosophy focused on maximizing value and minimizing waste in operations and processes. It aims to streamline workflows, eliminate non-value-added activities, and optimize resources to deliver products or services more efficiently and effectively. Lean principles include continuous improvement, respect for people, and the pursuit of perfection. | Lean Management complements TQM by providing principles and tools to reduce waste, improve efficiency, and enhance overall organizational performance. By incorporating Lean methodologies such as value stream mapping, 5S (Sort, Set in order, Shine, Standardize, Sustain), and Kaizen (continuous improvement), organizations can achieve greater productivity, flexibility, and customer satisfaction, while aligning with the objectives of TQM. |
ISO 9000 | ISO 9000 is a series of international standards that provide guidelines and requirements for implementing quality management systems (QMS) in organizations. ISO 9001, the most well-known standard in the series, outlines criteria for establishing, implementing, maintaining, and continuously improving a QMS to ensure consistency, conformity, and customer satisfaction in product and service delivery. | ISO 9000 standards offer a framework for organizations to formalize and standardize their quality management processes and practices. By achieving ISO 9001 certification, organizations demonstrate their commitment to quality and customer satisfaction, enhance their credibility and market competitiveness, and establish a foundation for continuous improvement and organizational excellence, in alignment with the principles of TQM. |
Continuous Improvement | Continuous Improvement, also known as Kaizen or incremental improvement, is a philosophy and approach focused on making small, incremental changes to processes, products, or services over time to achieve continuous growth and enhancement. It emphasizes empowering employees, fostering a culture of innovation, and encouraging experimentation and learning to identify and implement improvements at all levels of the organization. | Continuous Improvement is a core principle of TQM, promoting a culture of ongoing learning, innovation, and adaptation to change. By embracing continuous improvement practices such as Kaizen events, quality circles, and suggestion systems, organizations can engage employees, harness their collective knowledge and creativity, and drive incremental improvements in quality, efficiency, and customer satisfaction, in alignment with the objectives of TQM. |
- Read also: Business Strategy, Examples, Case Studies, And Tools
Read Also: Continuous Innovation , Agile Methodology , Lean Startup , Business Model Innovation , Project Management .
Read Next: Agile Methodology , Lean Methodology , Agile Project Management , Scrum , Kanban , Six Sigma .
Connected Agile & Lean Frameworks

Agile Methodology

Agile Program Management

Agile Project Management

Agile Modeling

Agile Business Analysis

Agile Leadership

Andon System

Bimodal Portfolio Management

Business Innovation Matrix

Business Model Innovation

Constructive Disruption

Continuous Innovation

Design Sprint

Design Thinking

Dual Track Agile

eXtreme Programming

Feature-Driven Development

GIST Planning

ICE Scoring

Innovation Funnel

Innovation Matrix

Innovation Theory

Lean vs. Agile

Lean Startup

Minimum Viable Product

Rational Unified Process

Rapid Application Development

Retrospective Analysis

Scaled Agile

Spotify Model

Test-Driven Development

Scrum Anti-Patterns

Scrum At Scale

Stretch Objectives

Toyota Production System

Total Quality Management

Main Guides:
- Business Models
- Business Strategy
- Business Development
- Distribution Channels
- Marketing Strategy
- Platform Business Models
- Network Effects
Main Case Studies:
- Amazon Business Model
- Apple Mission Statement
- Nike Mission Statement
- Amazon Mission Statement
- Apple Distribution
More Resources

About The Author
Gennaro Cuofano
Discover more from fourweekmba.
Subscribe now to keep reading and get access to the full archive.
Type your email…
Continue reading
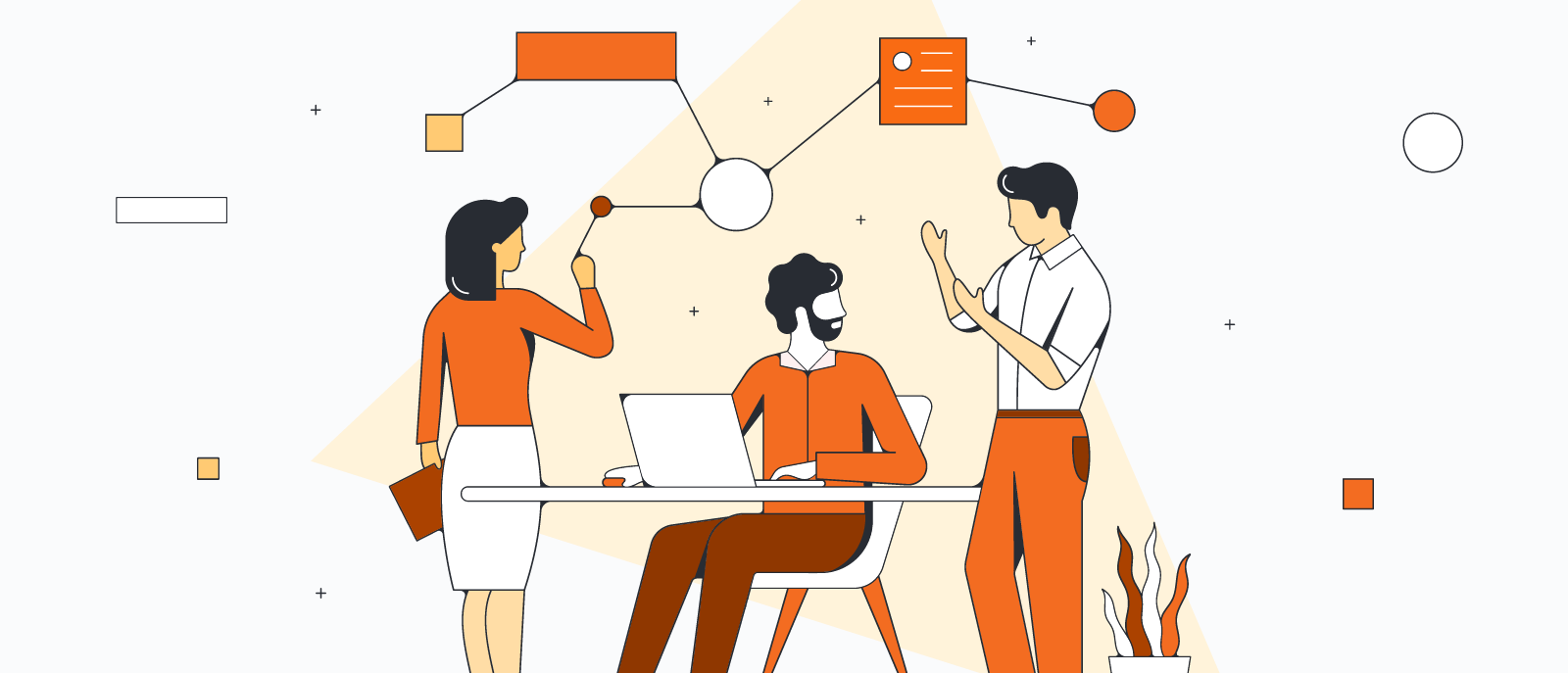
What are the 7 basic quality tools, and how can they change your business for the better?
Reading time: about 6 min
What are the 7 basic quality tools?
- Stratification
- Check sheet (tally sheet)
- Cause and effect diagram (fishbone or Ishikawa diagram)
- Pareto chart (80-20 rule)
- Scatter diagram
- Control chart (Shewhart chart)
The ability to identify and resolve quality-related issues quickly and efficiently is essential to anyone working in quality assurance or process improvement. But statistical quality control can quickly get complex and unwieldy for the average person, making training and quality assurance more difficult to scale.
Thankfully, engineers have discovered that most quality control problems can be solved by following a few key fundamentals. These fundamentals are called the seven basic tools of quality.
With these basic quality tools in your arsenal, you can easily manage the quality of your product or process, no matter what industry you serve.
Learn about these quality management tools and find templates to start using them quickly.
Where did the quality tools originate?
Kaoru Ishikawa, a Japanese professor of engineering, originally developed the seven quality tools (sometimes called the 7 QC tools) in the 1950s to help workers of various technical backgrounds implement effective quality control measures.
At the time, training programs in statistical quality control were complex and intimidating to workers with non-technical backgrounds. This made it difficult to standardize effective quality control across operations. Companies found that simplifying the training to user-friendly fundamentals—or seven quality tools—ensured better performance at scale
7 quality tools
1. stratification.
Stratification analysis is a quality assurance tool used to sort data, objects, and people into separate and distinct groups. Separating your data using stratification can help you determine its meaning, revealing patterns that might not otherwise be visible when it’s been lumped together.
Whether you’re looking at equipment, products, shifts, materials, or even days of the week, stratification analysis lets you make sense of your data before, during, and after its collection.
To get the most out of the stratification process, consider which information about your data’s sources may affect the end results of your data analysis. Make sure to set up your data collection so that that information is included.
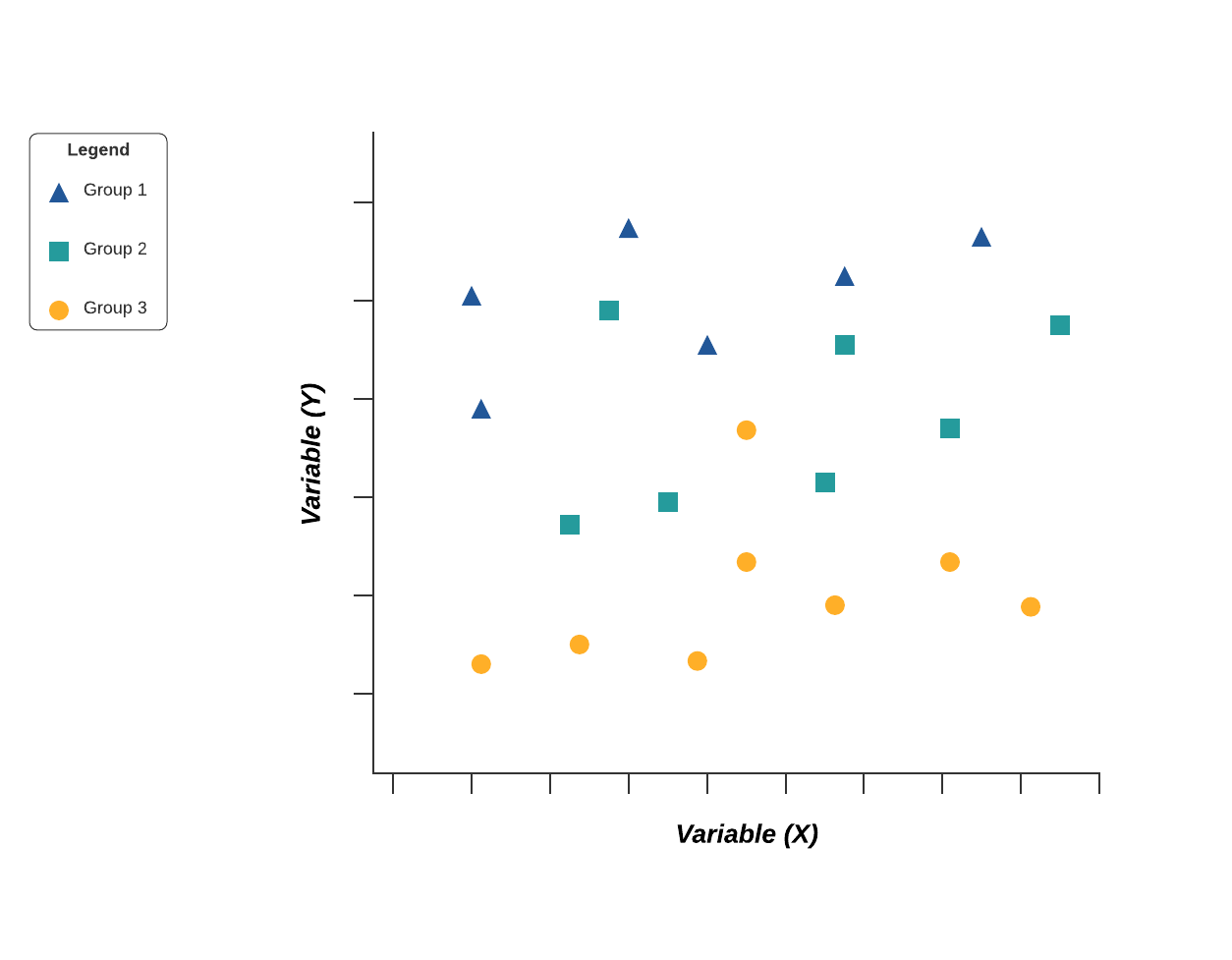
2. Histogram
Quality professionals are often tasked with analyzing and interpreting the behavior of different groups of data in an effort to manage quality. This is where quality control tools like the histogram come into play.
The histogram represents frequency distribution of data clearly and concisely amongst different groups of a sample, allowing you to quickly and easily identify areas of improvement within your processes. With a structure similar to a bar graph, each bar within a histogram represents a group, while the height of the bar represents the frequency of data within that group.
Histograms are particularly helpful when breaking down the frequency of your data into categories such as age, days of the week, physical measurements, or any other category that can be listed in chronological or numerical order.
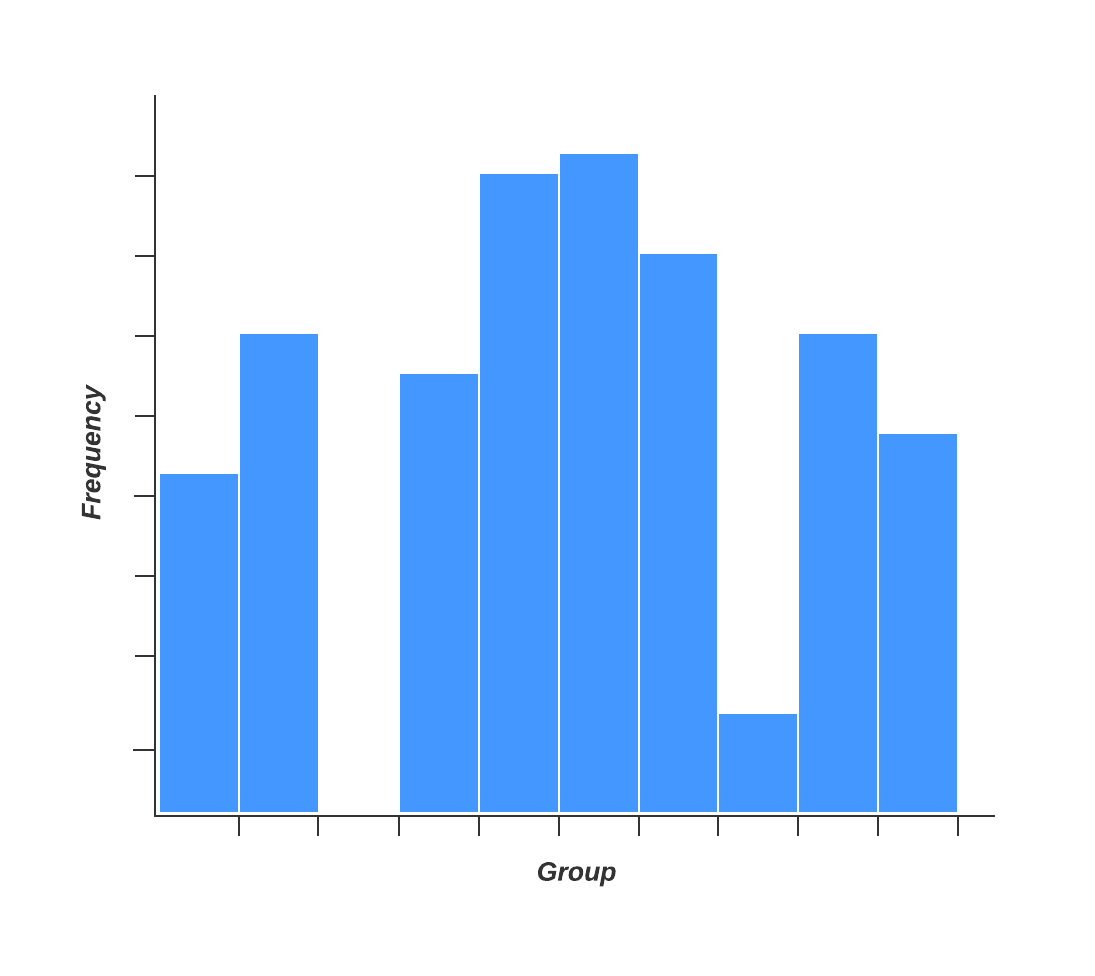
3. Check sheet (or tally sheet)
Check sheets can be used to collect quantitative or qualitative data. When used to collect quantitative data, they can be called a tally sheet. A check sheet collects data in the form of check or tally marks that indicate how many times a particular value has occurred, allowing you to quickly zero in on defects or errors within your process or product, defect patterns, and even causes of specific defects.
With its simple setup and easy-to-read graphics, check sheets make it easy to record preliminary frequency distribution data when measuring out processes. This particular graphic can be used as a preliminary data collection tool when creating histograms, bar graphs, and other quality tools.

4. Cause-and-effect diagram (also known as a fishbone or Ishikawa diagram)
Introduced by Kaoru Ishikawa, the fishbone diagram helps users identify the various factors (or causes) leading to an effect, usually depicted as a problem to be solved. Named for its resemblance to a fishbone, this quality management tool works by defining a quality-related problem on the right-hand side of the diagram, with individual root causes and sub-causes branching off to its left.
A fishbone diagram’s causes and subcauses are usually grouped into six main groups, including measurements, materials, personnel, environment, methods, and machines. These categories can help you identify the probable source of your problem while keeping your diagram structured and orderly.
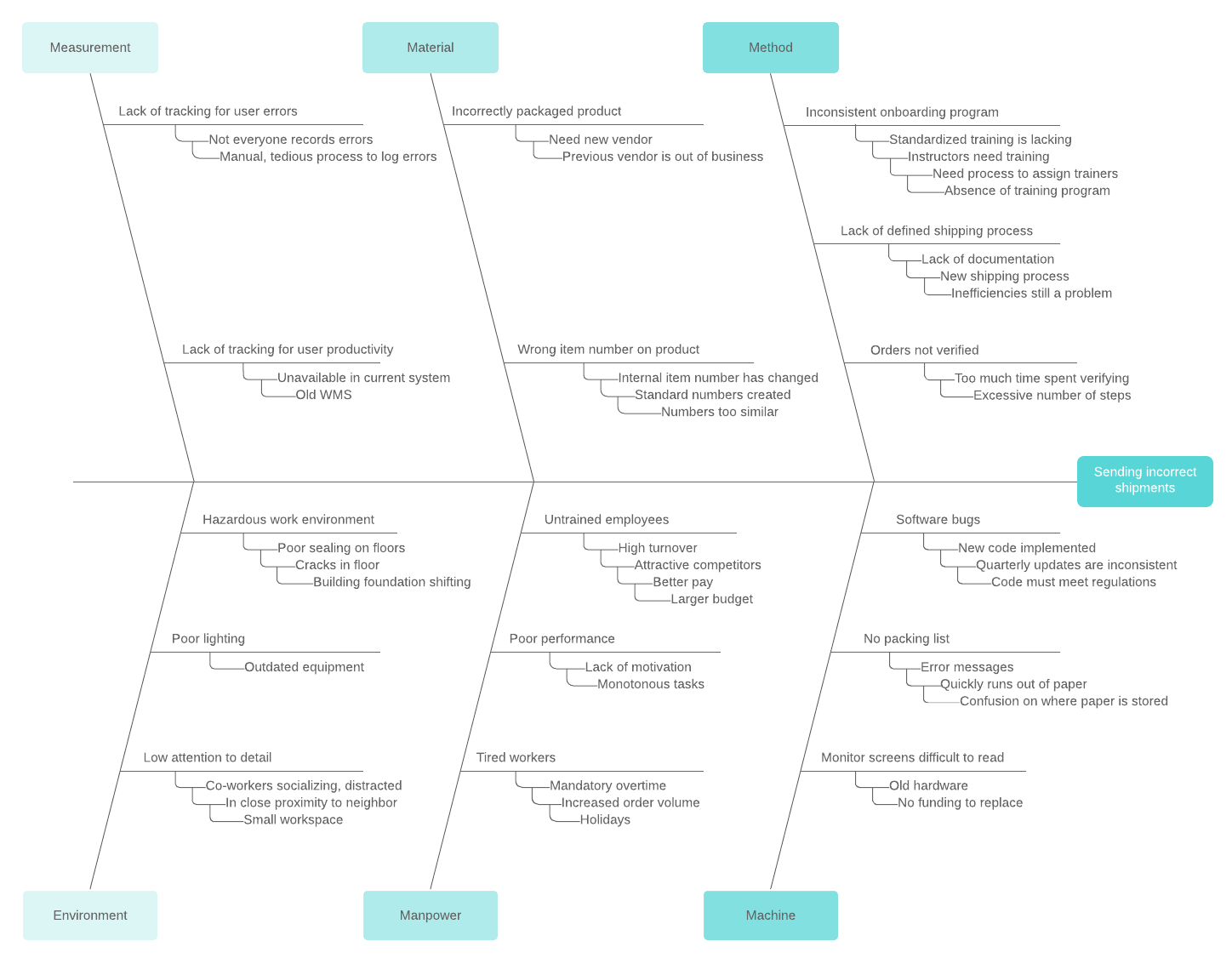
5. Pareto chart (80-20 rule)
As a quality control tool, the Pareto chart operates according to the 80-20 rule. This rule assumes that in any process, 80% of a process’s or system’s problems are caused by 20% of major factors, often referred to as the “vital few.” The remaining 20% of problems are caused by 80% of minor factors.
A combination of a bar and line graph, the Pareto chart depicts individual values in descending order using bars, while the cumulative total is represented by the line.
The goal of the Pareto chart is to highlight the relative importance of a variety of parameters, allowing you to identify and focus your efforts on the factors with the biggest impact on a specific part of a process or system.
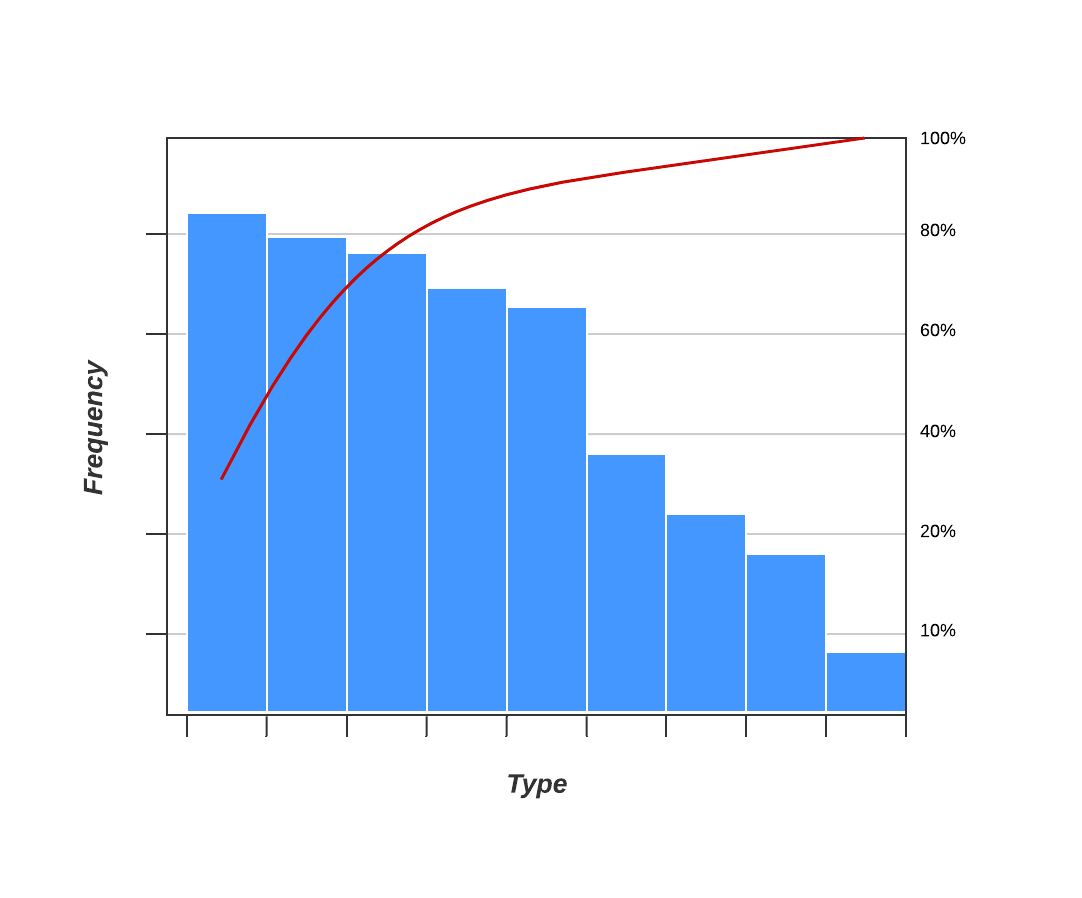
6. Scatter diagram
Out of the seven quality tools, the scatter diagram is most useful in depicting the relationship between two variables, which is ideal for quality assurance professionals trying to identify cause and effect relationships.
With dependent values on the diagram’s Y-axis and independent values on the X-axis, each dot represents a common intersection point. When joined, these dots can highlight the relationship between the two variables. The stronger the correlation in your diagram, the stronger the relationship between variables.
Scatter diagrams can prove useful as a quality control tool when used to define relationships between quality defects and possible causes such as environment, activity, personnel, and other variables. Once the relationship between a particular defect and its cause has been established, you can implement focused solutions with (hopefully) better outcomes.
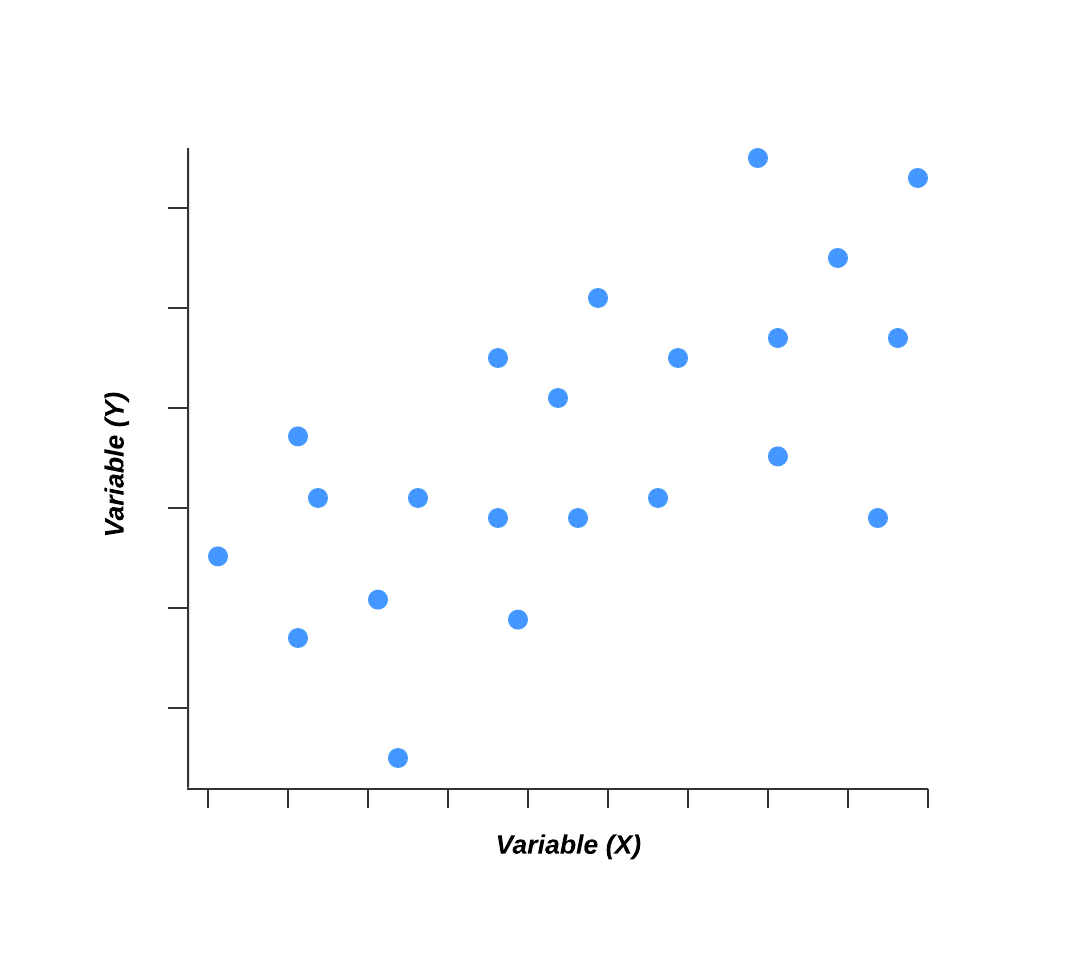
7. Control chart (also called a Shewhart chart)
Named after Walter A. Shewhart, this quality improvement tool can help quality assurance professionals determine whether or not a process is stable and predictable, making it easy for you to identify factors that might lead to variations or defects.
Control charts use a central line to depict an average or mean, as well as an upper and lower line to depict upper and lower control limits based on historical data. By comparing historical data to data collected from your current process, you can determine whether your current process is controlled or affected by specific variations.
Using a control chart can save your organization time and money by predicting process performance, particularly in terms of what your customer or organization expects in your final product.
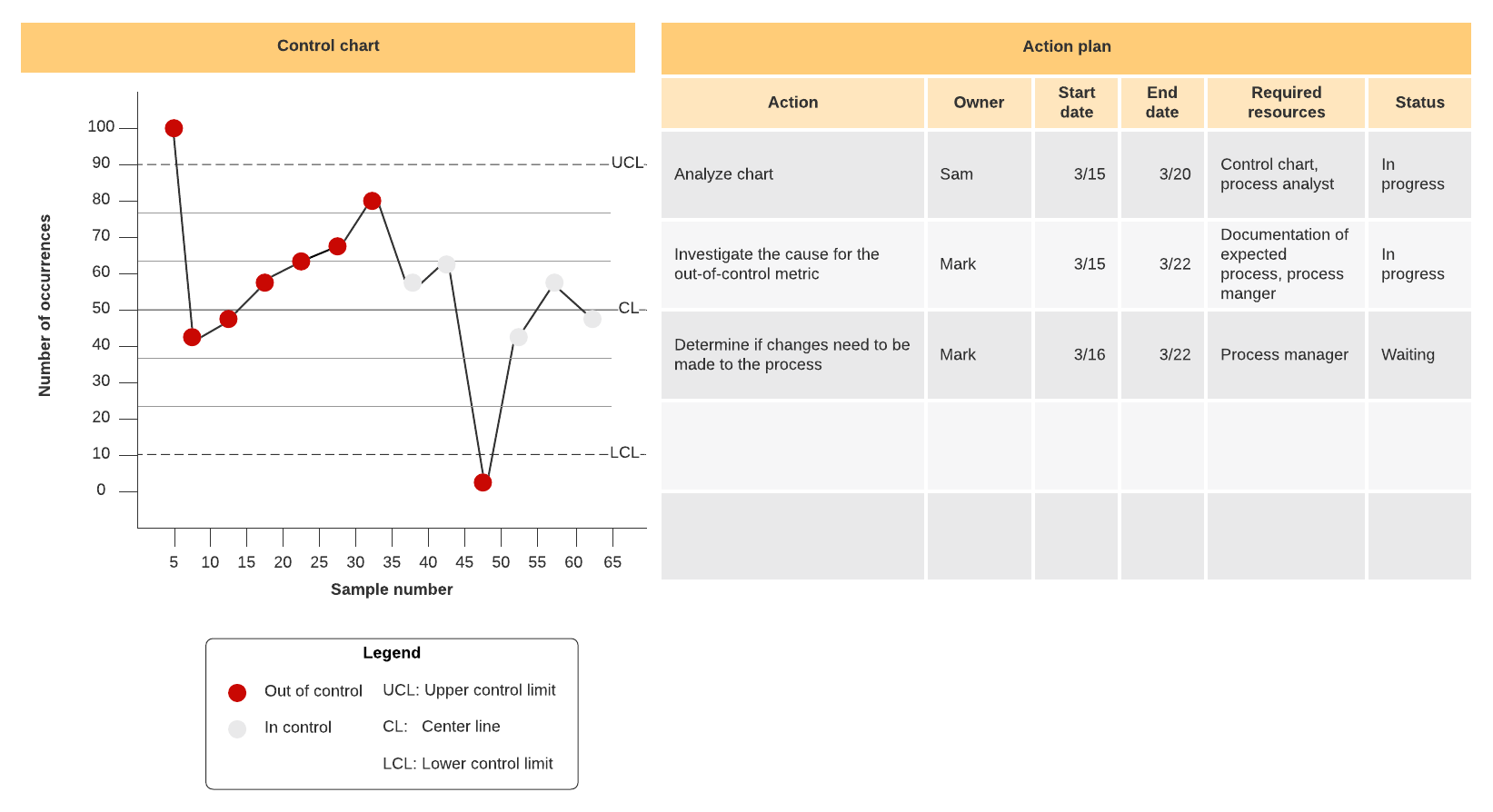
Bonus: Flowcharts
Some sources will swap out stratification to instead include flowcharts as one of the seven basic QC tools. Flowcharts are most commonly used to document organizational structures and process flows, making them ideal for identifying bottlenecks and unnecessary steps within your process or system.
Mapping out your current process can help you to more effectively pinpoint which activities are completed when and by whom, how processes flow from one department or task to another, and which steps can be eliminated to streamline your process.
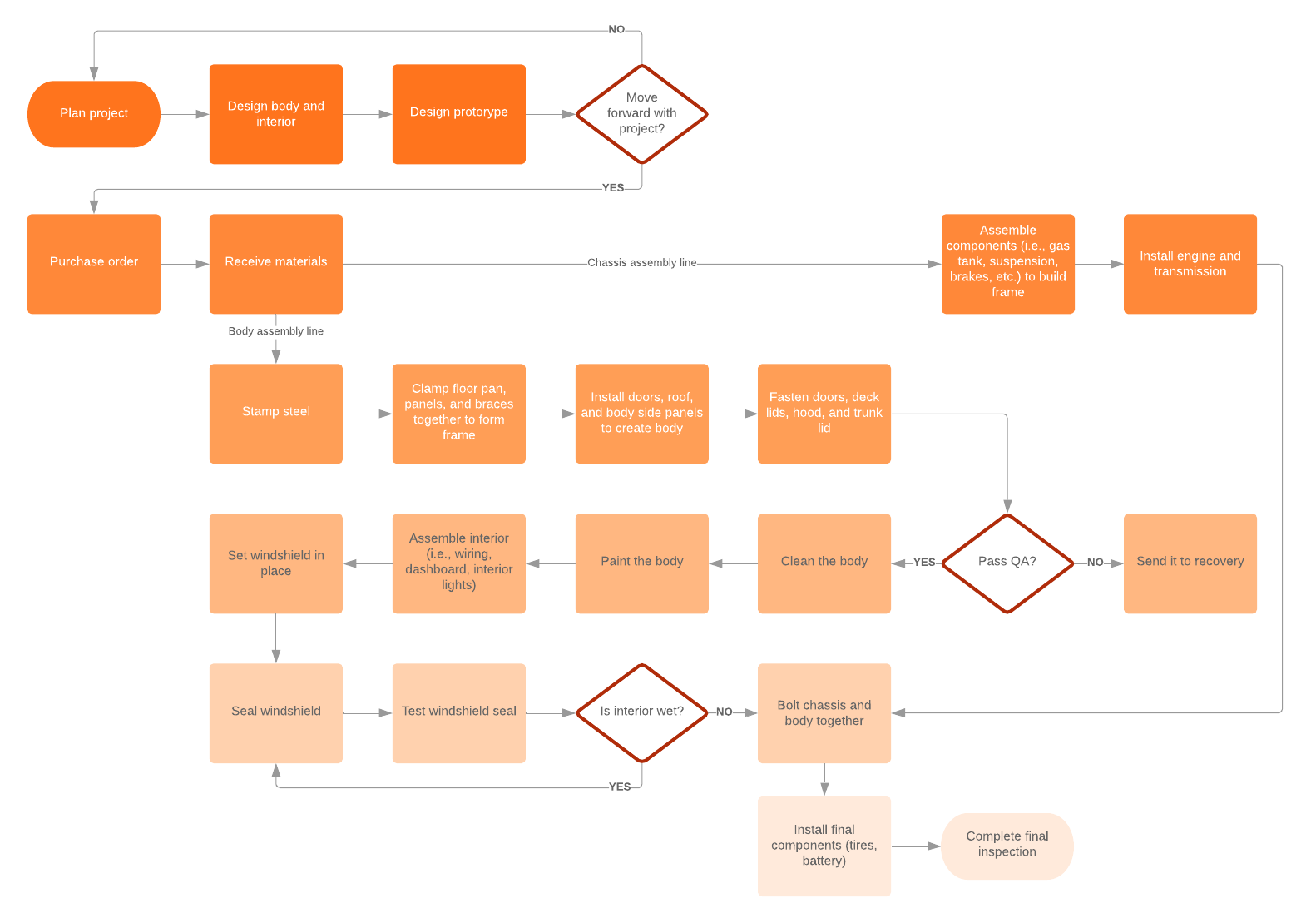
Learn how to create a process improvement plan in seven steps.
About Lucidchart
Lucidchart, a cloud-based intelligent diagramming application, is a core component of Lucid Software's Visual Collaboration Suite. This intuitive, cloud-based solution empowers teams to collaborate in real-time to build flowcharts, mockups, UML diagrams, customer journey maps, and more. Lucidchart propels teams forward to build the future faster. Lucid is proud to serve top businesses around the world, including customers such as Google, GE, and NBC Universal, and 99% of the Fortune 500. Lucid partners with industry leaders, including Google, Atlassian, and Microsoft. Since its founding, Lucid has received numerous awards for its products, business, and workplace culture. For more information, visit lucidchart.com.
Related articles
How to improve process visualization.
In this article we’ll talk about how to improve visualization, even if you are not a visual presentation expert.
Which process improvement methodology should you use?
Struggling to decide which process improvement methodology to use? Learn about the top approaches—Six Sigma, Lean, TQM, Just-in-time, and others—and the diagrams that can help you implement these techniques starting today.
Bring your bright ideas to life.
or continue with
By registering, you agree to our Terms of Service and you acknowledge that you have read and understand our Privacy Policy .
- Search Search Please fill out this field.
- What Is Total Quality Management?
- Understanding TQM
- Primary Principles
How to Implement TQM
- Pros and Cons
Industries Using TQM
The bottom line.
- Business Essentials
What Is Total Quality Management (TQM), and Why Is It Important?
:max_bytes(150000):strip_icc():format(webp)/Group1805-3b9f749674f0434184ef75020339bd35.jpg)
Yarilet Perez is an experienced multimedia journalist and fact-checker with a Master of Science in Journalism. She has worked in multiple cities covering breaking news, politics, education, and more. Her expertise is in personal finance and investing, and real estate.
:max_bytes(150000):strip_icc():format(webp)/YariletPerez-d2289cb01c3c4f2aabf79ce6057e5078.jpg)
What Is Total Quality Management (TQM)?
Total quality management (TQM) is the continual process of detecting and reducing or eliminating errors in manufacturing. It streamlines supply chain management , improves the customer experience, and ensures that employees are up to speed with training.
- Total quality management aims to hold all parties involved in the production process accountable for the overall quality of the final product or service.
Key Takeaways
- Total quality management (TQM) is an ongoing process of detecting and reducing or eliminating errors.
- TQM is used to streamline supply chain management, improve customer service, and ensure that employees are properly trained.
- The focus is to improve the quality of an organization’s outputs, including goods and services, through the continual improvement of internal practices.
- There are often eight guiding principles to TQM that range from focusing on customers, continually improving, and adhering to processes.
Katie Kerpel / Investopedia
Understanding Total Quality Management (TQM)
Total quality management is a structured approach to overall organizational management. The focus of the process is to improve the quality of an organization’s outputs, including goods and services, through the continual improvement of internal practices. The standards set as part of the TQM approach can reflect both internal priorities and any industry standards currently in place.
Industry standards can be defined at multiple levels and may include adherence to various laws and regulations governing the operation of a particular business. Industry standards can also include the production of items to an understood norm, even if the norm is not backed by official regulations. Acceptance sampling might be used to check the progress toward the TQM goal.
Example of TQM
Perhaps the most famous example of TQM is Toyota’s implementation of the kanban system. A kanban is a physical signal that creates a chain reaction, resulting in a specific action. Toyota used this idea to implement its just-in-time (JIT) inventory process.
The company decided to keep just enough inventory on hand to fill customer orders as they were generated to make its assembly line more efficient. All parts of Toyota’s assembly line are therefore assigned a physical card that has an associated inventory number.
The card is removed and moved up the supply chain right before a part is installed in a car, effectively requesting another of the same part. This allows the company to keep its inventory lean and not overstock unnecessary assets . Effective quality management resulted in better automobiles that could be produced at an affordable price.
History of TQM
TQM’s history often dates back to the early 1900s, when Walter A. Shewhart introduced modern quality control. Shewhart produced a landmark piece of industrial work titled “Economic Control of Quality of Manufactured Product” in 1931. This exposition is considered one of the founding and basic principles of manufacturing quality control.
Further developments in Shewhart’s work introduced new standards in quality management decades later. Joseph M. Juran published a book called “What Is Total Quality Control? The Japanese Way” in 1954. The work was based on Juran’s experience of being invited to Japan by Japanese scientists and engineers. Juran later co-authored “Quality Planning and Analysis,” another bestseller in TQM.
Another prominent figure in TQM history is W. Edwards Deming. Posted in Japan after World War II, Deming became involved with the Union of Japanese Scientists and Engineers (JUSE). His career work included several TQM frameworks (Deming’s 14 Points, Deming’s Seven Deadly Diseases of Management, and The Deming Wheel).
The exact origin of the phrase “total quality management” is not known, but several parties mentioned above are credited for helping develop the general concept.
Primary Principles of TQM
TQM is considered a customer-focused process that focuses on consistently improving business operations management . It strives to ensure that all associated employees work toward the common goals of improving product or service quality, as well as improving the procedures that are in place for production. Several guiding principles define TQM.
Focus on Customers
Under TQM, your customers define whether your products are high quality. Customer input is highly valued because it allows a company to better understand the needs and requirements in the manufacturing process. Customer surveys may reveal insufficient durability of goods. This input is then fed back into TQM systems to implement better raw material sourcing, manufacturing processes, and quality control procedures.
Commitment by Employees
Employees must buy into the processes and system if TQM is going to be successful. This includes clearly communicating across departments and leaders what goals, expectations, needs, and constraints are in place. A company adopting TQM principles must be willing to train employees and give them sufficient resources to complete tasks successfully and on time. TQM also strives to reduce attrition and maintain knowledgeable workers.
Improve Continuously
A company should gradually evolve and strive for incremental, small improvements as it learns more about its customers, processes, and competition. This concept of continuous improvement helps a company adapt to changing market expectations. It allows for greater adaptability to different products, markets, customers, or regions. Continuous improvement also drives and widens the competitive advantage that a company has built over related companies.
Adherence to Processes
TQM’s systematic approach relies heavily on process flowcharts, TQM diagrams, visual action plans, and documented workflows . Every member engaged in the process must be aware and educated on their part of the process to ensure proper steps are taken at the right time of production. These processes are then continually analyzed to better understand deficiencies in the process.
Strategic and Systematic Approach
A company’s processes and procedures should be a direct reflection of the organization’s vision, mission , and long-term plan. TQM calls for a system approach to decision making that requires that a company dedicate itself to integrating quality as its core component and making the appropriate financial investments to make that happen.
Data Utilization
The systematic approach of TQM only works if feedback and input are given to evaluate how the process flow is moving. Management must continually rely on production, turnover, efficiency, and employee metrics to correlate the anticipated outcomes with the actual results. TQM relies heavily on documentation and planning, and only by utilizing and analyzing data can management understand if those plans are being met.
Integrate Systems
One way to utilize data is to integrate systems. TQM strategies believe systems should talk to each other, conveying useful information across departments and making smart decisions. When goods or inventory are used in one area, another department should have immediate access to that enterprise resource planning (ERP) information. TQM strives to allow everyone to be on the same page at the same time by linking data sources and sharing information across systems.
Communication
Data may transfer between departments freely, but there is a human element to coordinating processes and making sure an entire production line is operating efficiently. Effective communication plays a large part in TQM to motivate employees, educate members along a process, and avoid process errors, whether it is normal day-to-day operations or large organizational changes.
Successful TQM requires a company-wide buy-in of every principle. The benefits of TQM quickly diminish if a company does not receive complete buy-in.
TQM is a unique process. There is not a specific formula for implementing a system that suits every business and each type of industry. But you can create a checklist of issues that might suit your enterprise and proceed with them in chronological order. Some may suit your business, while others will not. Select those that you think will provide an advantage.
- Identify your company’s existing culture, its core values, and its systems.
- Use this information to create a system that will serve as your master plan.
- Establish what your customers and clients want and what they expect from your business. Determine how to best meet these expectations and needs.
- Create a team of management and employees to guide and implement your goals, and include these efforts in your daily business management process.
- Consistently gather feedback from employees and customers to gauge your progress.
TQM is not a speedy process. Expect to dedicate an extended period of time to your efforts.
Advantages and Disadvantages of TQM
TQM results in a company making a product for less when it’s implemented correctly. Companies that engage in TQM provide more consistent products that yield stronger customer loyalty when they emphasize quality and minimize waste.
As TQM touches every department across an organization, a company may reap substantial savings from materials sourcing, production, distribution, or back-office functions. Companies that successfully implement TQM can usually react more quickly to change and proactively plan ahead to avoid obsolescence.
A company must fully engage TQM principles to fully reap the benefits of TQM. This requires substantial buy-in from every department across an organization. This level of commitment is very difficult to achieve, requires substantial financial investment, and necessitates all levels of management to engage in TQM.
The conversion to TQM may be lengthy, and workers may feel resistant to change. A company may be required to replace processes, employees, equipment, or materials in favor of an untested, partially developed TQM plan. More skilled workers may decide to leave the company if they feel TQM processes don’t appropriately utilize their skill sets.
Total Quality Management
Delivers stronger, higher-quality products to customers
Results in lower company-wide costs
Minimizes waste throughout the entire production and sale process
Enables a company to become more adaptable
May require substantial financial investment to convert to TQM practices
Often requires conversion to TQM practices over a long period of time
May be met with resistance to change
Requires company-wide buy-in to be successful
TQM originated in the manufacturing sector, but its principles can be applied to a variety of industries . It provides a cohesive vision for systemic change with a focus on long-term change rather than short-term goals. TQM is used in many industries with this in mind, including but not limited to manufacturing, banking and finance, and medicine.
These techniques can be applied to all departments within an individual organization. This helps ensure that all employees are working toward the goals set forth for the company and improving function in each area. Involved departments can include administration, marketing, production, and employee training.
What Does Total Quality Management Do?
TQM oversees all activities and tasks that are necessary to maintain a desired level of excellence within a business and its operations. This includes the determination of a quality policy, creating and implementing quality planning and assurance, and quality control and quality improvement measures.
What Are the Principles of TQM?
Various iterations of TQM have been developed, each with its own set of principles. Certain core elements persist nonetheless. These include good leadership, emphasis on quality, customer priority, error correction and improvement as an ongoing process, and job training.
What Is a TQM Diagram?
A TQM diagram is a visual depiction of the business and process layout. The diagram usually shows different processes or steps, allowing management to see a process, analyze weaknesses or risks in the flow, and strategically adjust how things are done.
Total quality management is the strategic framework that encourages everyone in an organization to focus on quality improvement. The theory holds that customer satisfaction will increase by being operationally excellent. Many principles drive TQM, but the overall purpose is to eliminate errors, streamline processes, and maximize efficiency.
Toyota. “ Section 4. Plant Construction and Expansion: Item 4. Development and Deployment of the Toyota Production System .”
American Society for Quality. “ Walter A. Shewhart .”
American Society for Quality. “ Joseph M. Juran .”
British Library, via Internet Archive Wayback Machine. “ W. Edwards Deming .”
:max_bytes(150000):strip_icc():format(webp)/business-people-using-pen-tablet-notebook-are-planning-a-marketing-plan-to-improve-the-quality-of-their-sales-in-the-future--881542122-6767a39f655b4a018019715734dcfbe0.jpg)
- Terms of Service
- Editorial Policy
- Privacy Policy
Online ordering is currently unavailable due to technical issues. We apologise for any delays responding to customers while we resolve this. For further updates please visit our website: https://www.cambridge.org/news-and-insights/technical-incident
We use cookies to distinguish you from other users and to provide you with a better experience on our websites. Close this message to accept cookies or find out how to manage your cookie settings .
Login Alert

- > Lean Evolution
- > Problem solving, TQM and Six Sigma
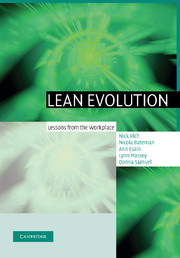
Book contents
- Frontmatter
- List of boxes
- List of figures
- List of tables
- 1 Introduction
- 2 Understanding the lean journey
- 3 Understanding your organisation
- 4 Laying the foundation stone of CANDO
- 5 Visual management and performance measurement
- 6 Problem solving, TQM and Six Sigma
- 7 Pull systems
- 8 Total productive manufacturing (TPM)
- 9 Sustainability
- 10 Group learning
- 11 Reflections and future challenges
6 - Problem solving, TQM and Six Sigma
Published online by Cambridge University Press: 17 August 2009
If you work in industry or commerce today, then the topic of ‘quality’ will be part of your business language. Quality is an order qualifier, something demanded and expected by customers and the cost of poor quality is quite often a measurement at the highest level of an organisation (Hill, 1985). This is not surprising when figures such as 40% of the total cost of doing business is attributed to avoidable activity due to rework, scrap and rejects. Known as the ‘hidden factory’, this describes the multitude of, mostly, small activities which make up a significant cost to business, but are unnecessary. A waste of resource, worse still, a source of frustration between employees and across the different levels of an organisation.
This chapter will briefly outline the role of quality in a lean transition and its place in supporting such a transition. We are aware that the concept of quality is discussed in many guises and often as ‘initiatives’ by management authors, and, for the most part, these initiatives are considered old and staid. Quotes, from line workers and managers, that ‘we did TQM in 1996’ are not uncommon and reinforce the idea that this type of approach is a ‘tick in the box’ exercise. However, ‘world class’ businesses, and those determined to become world class, know well that quality management lies at the heart of all improvement activity.
We know that to maintain performance we need to continue focusing on a task.
Access options
Save book to kindle.
To save this book to your Kindle, first ensure [email protected] is added to your Approved Personal Document E-mail List under your Personal Document Settings on the Manage Your Content and Devices page of your Amazon account. Then enter the ‘name’ part of your Kindle email address below. Find out more about saving to your Kindle .
Note you can select to save to either the @free.kindle.com or @kindle.com variations. ‘@free.kindle.com’ emails are free but can only be saved to your device when it is connected to wi-fi. ‘@kindle.com’ emails can be delivered even when you are not connected to wi-fi, but note that service fees apply.
Find out more about the Kindle Personal Document Service .
- Problem solving, TQM and Six Sigma
- Nick Rich , Cardiff University , Nicola Bateman , Cardiff University , Ann Esain , Cardiff University , Lynn Massey , Cardiff University , Donna Samuel , Cardiff University
- Book: Lean Evolution
- Online publication: 17 August 2009
- Chapter DOI: https://doi.org/10.1017/CBO9780511541223.007
Save book to Dropbox
To save content items to your account, please confirm that you agree to abide by our usage policies. If this is the first time you use this feature, you will be asked to authorise Cambridge Core to connect with your account. Find out more about saving content to Dropbox .
Save book to Google Drive
To save content items to your account, please confirm that you agree to abide by our usage policies. If this is the first time you use this feature, you will be asked to authorise Cambridge Core to connect with your account. Find out more about saving content to Google Drive .

IMAGES
VIDEO
COMMENTS
Finding a suitable solution for issues can be accomplished by following the basic four-step problem-solving process and methodology outlined below. Step. Characteristics. 1. Define the problem. Differentiate fact from opinion. Specify underlying causes. Consult each faction involved for information. State the problem specifically.
Lynch then set three objectives for the workshop session: (1) identifying the seven steps in problem solving, (2) learning to write clear problem solving statements, and (3) diagnosing a prob- lem solving story. Problem solving is just one component of the ldrger TQM pro- cess. Lynch first provided a context for problem solving by present- ing ...
In true nature of preventing rather than curing problems, some of the most popularly used TQM Tools are as follows: Checklists. Fishbone Diagrams. Histogram charts. Pareto Diagrams. PDCA Cycle (Which TQM is built around) Process Flow Charts. Process Control Chart. Find out what TQM tools are and how you can use them as a part of a problem ...
To start building a culture of quality, consider applying these five key management principles within your organization. 1. Use "Plan-Do-Check-Act" (The Deming Cycle) This is a structured problem solving system based on the scientific method of hypothesize-experiment-evaluate. Plan - Take the lead in making an improvement.
Total Quality Management is much more than a set of techniques or procedures; it's a holistic approach that infuses quality into every aspect of an organization's operations and culture. By adopting TQM, organizations commit to a path of continuous improvement, where the pursuit of excellence is a constant goal. ... 8D Problem Solving ...
An analytical approach to decision-making and problem-solving is inherent in TQM. It relies on data and facts to drive informed decisions and solve problems systematically. TQM organizations utilize various quality tools, techniques, and statistical methods to benchmark performance, monitor effectiveness, and drive continuous improvement. ...
Total Quality Management (TQM) is an organization-wide, customer-focused mindset and data-driven approach to eliminating, reducing, or preventing errors. ... Train and coach employees on new processes and problem-solving techniques; Develop effective measures of product and service quality;
Total Quality Management includes a number of management practices, philosophies and methods to improve the way an organization does business, makes its products, and ... people's problem-solving skills in organizations that have not yet introduced TQM as a leading management policy: not only in profit-making organizations but also in non ...
Total Quality Management requires an approach that encompasses an organization. Based on the principle of continuous improvement, TQM can help spark innovation within that organization by drawing on the ideas and problem-solving abilities of its most incredible resource - people.
2 TQM tools. TQM provides a set of tools that can help you implement its principles and improve your problem management skills, such as the PDCA cycle, the fishbone diagram, the Pareto chart, the ...
Total Quality Management (TQM) is a management approach that originated in the 1950s and has steadily become more popular since the early 1980s. Total quality is a description of the culture, attitude and organization of a company that strives to provide customers with products and services that satisfy their needs. ... B. Problem solving teams ...
Total Quality Management (TQM) emphasizes continuous improvement, involving all employees in achieving quality excellence. It fosters a culture of ingrained quality, teamwork, proactive problem-solving, and commitment to excellence, aiming to eliminate defects, reduce waste, and enhance overall performance. TQM focuses on customer satisfaction ...
A core definition of total quality management (TQM) describes a management approach to long-term success through customer satisfaction. In a TQM effort, all members of an organization participate in improving processes, products, services, and the culture in which they work. Primary elements of TQM. Benefits of TQM.
The Total Quality Management (TQM) framework is a technique based on the premise that employees continuously work on their ability to provide value to customers. ... framework emphasizes a total commitment to long-term change through a cohesive and collaborative approach to employee problem-solving. The TQM framework utilizes eight principles ...
4. Cause-and-effect diagram (also known as a fishbone or Ishikawa diagram) Introduced by Kaoru Ishikawa, the fishbone diagram helps users identify the various factors (or causes) leading to an effect, usually depicted as a problem to be solved. Named for its resemblance to a fishbone, this quality management tool works by defining a quality-related problem on the right-hand side of the diagram ...
Total Quality Management - TQM: Total Quality Management (TQM) is the continuous process of reducing or eliminating errors in manufacturing, streamlining supply chain management , improving the ...
A waste of resource, worse still, a source of frustration between employees and across the different levels of an organisation. This chapter will briefly outline the role of quality in a lean transition and its place in supporting such a transition. We are aware that the concept of quality is discussed in many guises and often as 'initiatives ...
Employees receive training on quality management techniques, problem-solving skills, and new technologies to ensure they have the knowledge and skills to meet quality standards. Step 6: Supplier relationships. ... "Total Quality Management" (TQM) gained prominence in the 1980s. It integrated various quality management practices into a ...
The eight disciplines (8D) model is a problem solving approach typically employed by quality engineers or other professionals, and is most commonly used by the automotive industry but has also been successfully applied in healthcare, retail, finance, government, and manufacturing. The purpose of the 8D methodology is to identify, correct, and ...
15.Use a Graph to show the magnitude and importance of the problem. 16.The 7‑Step Structured Problem Solving Process works best where a process already exists and is understood. 17.The 7‑Step Structured Problem Solving Process works best when data is generated and obtainable on a frequent basis. 18.The theme should be measurable.