

What is Plant Layout? Definition, Types, Objectives, Factors Affecting
- Post last modified: 7 April 2024
- Reading time: 19 mins read
- Post category: Uncategorized

What is Plant Layout?
Plant layout is the overall arrangement of the production process, store-room, stock-room, tool-room, material handling equipment, aisles, racks and sub-stores, employee services and all other accessories required for facilitation of the production in the factory.
It encompasses production and service facilities and provides for the most effective utilization of the men, materials and machine’ constituting the process, it is a master blueprint for coordinating all operations performed inside the factory.
Table of Content
- 1 What is Plant Layout?
- 2 Plant Layout Definition
- 3 Objectives of Plant Layout
- 4 Factors Affecting the Plant Layout Decision
- 5.1.1 Advantages of Process Layout
- 5.1.2 Disadvantages of Process Layout
- 5.2.1 Advantages of Product layout
- 5.2.2 Disadvantages of Product layout
- 5.3 Combined Layout
- 5.4 Project Layout
- 5.5 Group Layout
Plant Layout Definition
According to F G. Moore, “ A good layout is one which allows materials rapidly and directly for processing. This reduces transport handling, clerical and other costs down per unit, space requirements arc minimized and it reduces idle machine and idle man time.”
Objectives of Plant Layout
A good plant layout strives to attain the following objectives:
- Minimization of material handling.
- Elimination of bottlenecks through the balancing of plant capacities.
- High material turnover through a shorter operating cycle.
- Effective utilization of installed capacity so that the returns on the investments may be maximized.
- Effective utilization of cubic space in the factory area.
- Effective utilization of manpower resources through the elimination of idle time.
- Elimination, improvement or confinement of objectionable operations e.g., operations with bad odour, vibrating operations etc.
- Elimination of physical efforts required by operative workers.
- Avoidance of industrial accidents.
- Better working conditions for the employees like lighting, ventilation, control of noise and vibrations etc.
- Decency and orderliness inside the plant area.
- Better customer services through cheaper and better product supplies according to the delivery promises.
Factors Affecting the Plant Layout Decision
The decision of the plant layout is affected by the following factors:
- Type of production: The layout for an engineering unit will be quite different from that of a flour factory, similarly layout of a paper mill will be different from a tool room and layout of an engine assembly line is different from the toy-making facility.
- Production System: The plant layout in a continuous production system will be totally different from the intermitted production system.
- Scale of Production: The plant layout and material handling equipment in the large scale organization will be different from that in the small scale manufacturing activity.
- Type of Machines: The use of single-purpose and multipurpose machines substantially affects the plant layout. Similarly, noisy and vibrating machines require special attention in the plant layout decision.
- Type of building facilities: The plant layout in a single storey building will be different from that in a multi-storey building.
- Availability of Total Floor Area: The allocation of space for machines, workbenches sub stores, aisles, etc is made on the basis of the available floor area. Use of overhead space is made in case of shortage of space.
- Possibility of Future Expansion: Plant layout is mad in the light of the future requirements and installation of additional facilities.
- Arrangement of Material Handling Equipment: The plant layout and the material handling services are closely related and the latter has a decisive effect on the arrangement of the production process and plant services.
Type of Plant Layout
The popular types of plant layout are:
- Process layout
Product layout
- Combined layout
- Project layout
Group Layout
Process layout.
This type of layout is also called functional layout. All machines performing a similar type of operations are grouped at one location in the process layout e.g., all lathes, milling, machines, cutting machines etc. in the engineering shop are clustered in their like groups. Thus all forging will be done in one area and all the lathes will be placed in another area.
In this layout, several products may share a machine to make its full use. The sequential arrangement of the machine group is generally, but not necessarily made on the basis of labor operations.
In this type of layout, the process rather than the product has dominating role. The product is given secondary consideration and is moved for the purpose of operations to the process section with like machines stationed at a particular point. This type of layout is more suitable to job order type of production.
The typical arrangement of the machines in the process layout will be as under:
Advantages of Process Layout
- It eliminates the duplication of machines and enables the optimum use of installed capacity.
- It facilitates flexibility in production. It is more flexible than a line layout. Different products can be made without changes in the arrangements of the machine.
- The production capacity is not arranged in rigid sequence and fixed rated capacity with line balancing.
- The break down of one machine does not interrupt the entire production flow.
- Specialization in supervision becomes possible.
- Individual incentive schemes can be developed.
Disadvantages of Process Layout
- Due to a lack of straight-line sequence of production, it is impossible to maintain the line balancing in production. So the problems of bottleneck and waiting and the idle capacity.
- The cost of material handling increases due to long routing and backtracking between the processes.
- The processing time is prolonged which reduce the inventory turnover and increases the investments in inventories.
- The inspection cost increases. Due to frequent changes in the machine set up, inspection is required at each stage of the process.
- The cost of supervision increases due to specialist supervisors and more number of supervisors are required at each process unit.
- The production planning and control become difficult due to complexities arising in routing, scheduling, dispatching and follow-up.
- It is not possible to implement the group incentive schemes on the basis of the quantity of the products manufacturing.
- More space is required for internal storing, a reservoir of materials and provision for the expansion of the particular process section.
In this type of layout, the machines are arranged in the sequence as required by the particular product. All machines as required to balance the particular product line are arranged in a sequential line but not necessarily in the straight line. It is also known as “ the product line layout.”
In this layout, one product goes through all the machines lined up, in the order required by its manufacture. The best-known example of this type of layout is seen in motor car production. To make this layout successful, the workload on the various machines must be balanced. The process of getting even loading at each stage of production is called line balancing .
In this type of layout, the product is dominating over the process, in the sense that the product is given the primary importance and the process machine must remain present at a point where the product needs its services.
Thus, unlike the process layout , the process is given secondary importance in relation to the product. Product layout is more suitable for continuous flow-production with few items of production. It does not require frequent changes in machine set up.
The typical arrangement of the machines in the product with separate independent product lines for Product A and Product B will be as shown in the following figure :
Advantages of Product layout
- Reduced material handling cost due to straight-line production flow.
- Mechanization of material handling between fixed points.
- Line balancing may eliminate bottlenecks and idle capacity.
- Shorter operating cycle due to shorter and speedy movement of materials.
- Maximum utilization of machine and labour capacity through developing a proper balance between them.
- Effective control over production with reduced supervision by generalists supervisor. By reducing the manufacturing to simple steps we can often use less skilled labour.
- Effective quality control with reduced inspection points. It does not require frequent changes in machine set-up.
- Effective production planning and control. Unlike process layout, the routing, scheduling, dispatching and follow up are relatively easier.
- Maximum use of space due to straight production flow and reduced need of interim storing.
- It facilitates the implementation of group incentive schemes for the workers.
- It is relatively easy to control.
Disadvantages of Product layout
- The duplication of machines and equipment necessitates the increased investments in them sometime resulting in idle capacity.
- The production flow is regulated through the straight line sequence and fixed rated capacity, and thus makes it highly inflexible.
- The breakdown of one single machine in the line interrupts the entire production flow.
- Unlike process layout, the benefits of specialized supervision is not possible.
- As the entire production is the result of the joint efforts of all operations in the line, it is difficult to implement individual incentive schemes.
- They are less flexible than others. Any change in product requires rebalancing the line.
Combined Layout
Generally pure process or pure product layout is not found in practice. Both process and product layouts are mutually exclusive. Proper compromise reaping the benefits of both the layouts is possible to some extent. So efforts are made to have the combined layout incorporating the benefits of process and product layout.
Combined layout is developed as under:
- Product layout for the main product with a process layout for joint or by-product tapping the idle capacity of product layout along with marginal investments required in process layout.
- To diversify the production with a view to tap the idle capacity of the product layout. Products with a complete negative correlation with the product line can make the maximum use of idle capacity of the product layout.
- In the product layout, some process may be segregated from the product line e.g., objectionable, hazardous, requiring special treatment and repetitive performance etc.
Project Layout
The manufacturing operation require the movements of men, machines and materials. Generally few inputs tend to be static while the others are moving.
In the product layout and process layout generally the machines have fixed installations and the operators are static in terms of their specified work stations.
It is only the materials which move form operation to operation for the purpose of processing. But where the product is large in size and heavy in weight, it tends to be static, e.g., shipbuilding.
In such a production system, the product remains static and the men and machines move performing the operations on the product. The production characteristics are sufficient enough to treat it as a separate type of layout, viz. static product layout.
Here an attempt is made to introduce some of the advantages of a line layout into a situation where pure line layout is not practicable. Here machines are placed in groups.
Each machine group makes maximally of parts which require similar treatment. This layout lies between process layout and line layout. It is easier to control than a strictly process layout and has more flexibility into the manufacturing system as regards the batch size variations and the differing operations sequences.
- Chase R.B., Jacobs F.R., Operations Management for Competitive Advantage, The Mc Graw Hill
- R.Johnson, “Spacecraft for Multi- Floor Layout Planning, Management Science 28, No.4(April 1982), PP407-17
- M.S. Sommers and J.B. Kernan, “A Behavioral Approach to Planning, Layout and Display,” Journal of Retailing, Winter 1965-66, PP 21-27.
Go On, Share & Help your Friend
Did we miss something in Organizational Behavior Tutorial or You want something More? Come on! Tell us what you think about our post on Plant Layout | in the comments section and Share this post with your friends.
You Might Also Like
Contract of indemnity: essentials, rights, financial decision making, what is consumer protection malpractices, system, right, methods, management concepts notes, pdf i mcom 2022, what is natural resources, 5 ways to make sure an assignment writing service is good, what is technopreneurship traits, challenges, importance, risk, detailed syllabus of m.tech in defence technology | 2021 – 22, zero based budgeting: meaning, definition,process, advantages, 5 best free open source alternatives to ling app, deductions to be made in computing total income, legality of object and consideration, leave a reply cancel reply.
You must be logged in to post a comment.
World's Best Online Courses at One Place
We’ve spent the time in finding, so you can spend your time in learning
Digital Marketing
Personal growth.
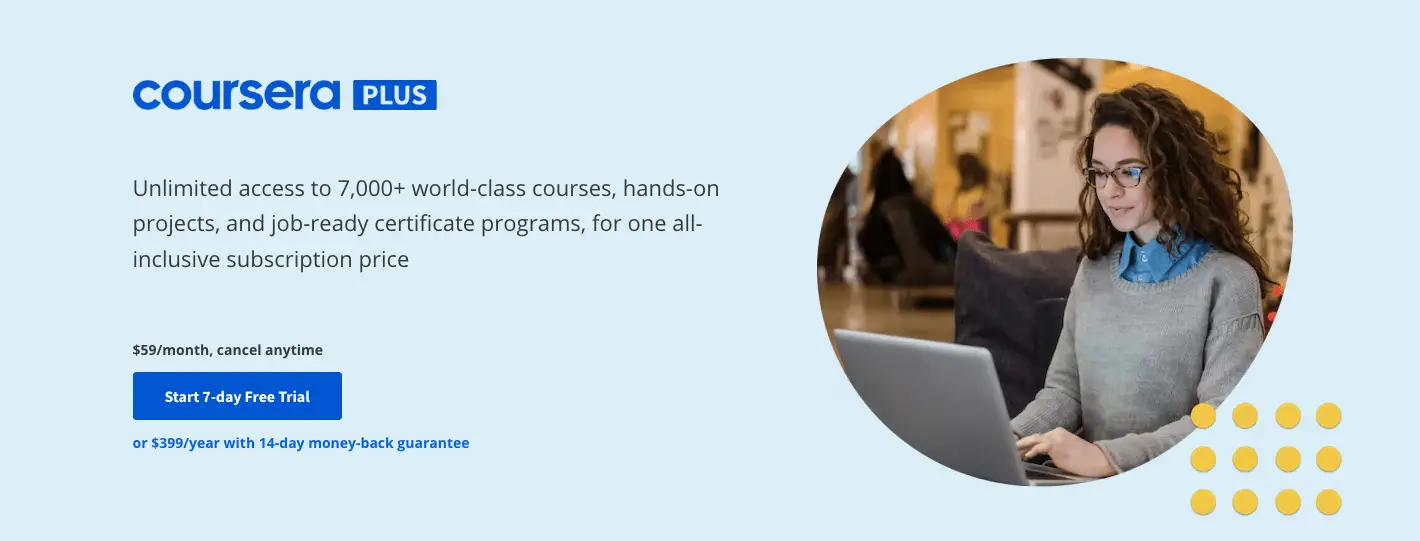
Development
A Guide to Effective Plant Layout and Expansion Strategies
If you are a plant manager, you know how important it is to have an effective plant layout. It can make or break your manufacturing operations, affecting efficiency, productivity, quality, safety, and customer satisfaction.
Got a manufacturing company with less than 20 employees? Transform operations with the GENEDGE Emerging Business Program!
But what makes a good plant layout? And how can you design or improve your existing layout to meet your current and future needs?
In this blog post, we at GENEDGE will share tips and best practices for using lean principles to create a lean plant layout.
In this blog, we’ll cover:
- What a lean plant layout is
- How to design a lean plant layout
- How industry leaders are applying lean principles to production
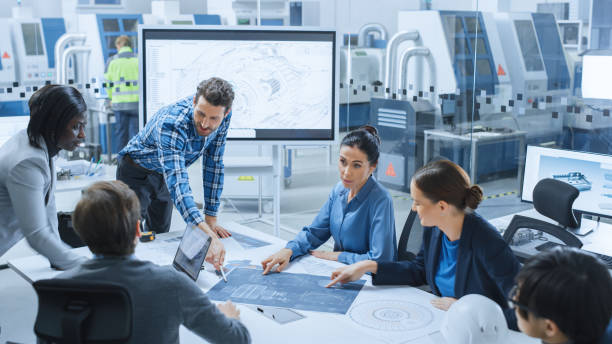
What is a Lean Plant Layout?
A lean plant layout streamlines your smart factory workflow, cuts waste, and enhances value, leading to reduced costs and improved quality. It’s all about arranging your processes with the end-to-end flow in mind—turning raw materials into customer-ready products efficiently. Unlike conventional setups, lean layouts align tasks side-by-side, slashing unnecessary movement and handling of materials. This minimizes delays and inventory build-up, keeps the work area clear, and makes troubleshooting straightforward.
To the manufacturer’s benefit, lean layouts favor versatile, appropriately sized equipment tailored to specific product lines, boosting adaptability and reducing downtime. Visual cues play a big role, too, making operations transparent with indicators like kanban cards and color-coded areas, aiding in real-time communication and organization.
How to Design a Lean Plant Layout
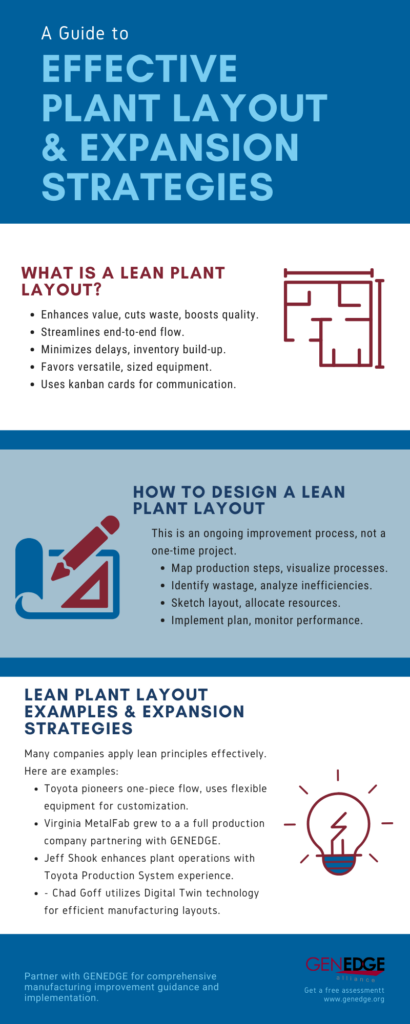
Designing a lean plant layout is not a one-time project but a continuous improvement process . But the steps can be pretty simple:
Map Your Value Streams
Identify what you produce and the steps involved from start to finish. Use value stream maps to visualize your process, noting times, inventory, and the flow of information.
Identify and Analyze Wastage
Look for inefficiencies—long walks, excess stock, quality issues, bottlenecks, or unnecessary production. Tools like spaghetti diagrams and 5S can help identify what’s not working and why.
Plan Your Future State
With your analysis in hand, sketch out a new, waste-reducing layout. Use diagrams and software to bring your vision to life, and plan the resources and time you’ll need to make the changes.
Implement and Monitor
Put your plan into action and rejig your space. Keep an eye on key performance indicators to see how things are improving. Regular checks and team feedback will help you refine your layout even further.
Examples of Lean Plant Layout and Expansion Strategies
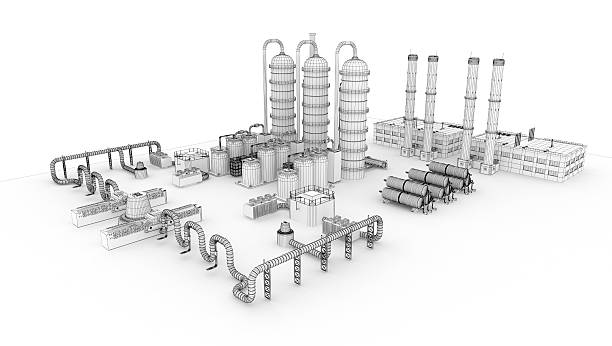
Many companies have successfully applied lean principles to their plant layout and expansion strategies. Here are some prime examples:
- Toyota , the pioneer of lean manufacturing, has designed its plants to achieve a one-piece flow, where each product moves smoothly from one process to the next without any interruption or waste. Toyota also uses flexible equipment that can produce different models for better customization . Neat!
- Virginia MetalFab , a leading metal manufacturer in Virginia, partnered with GENEDGE to evolve from a small “job shop” into a full production company. With GENEDGE’s assistance, Virginia MetalFab expanded its manufacturing and fabrication services, achieving a leap in market share for the transportation industry and enhancing its physical footprint. This expansion was facilitated by a comprehensive commercialization plan and a lean facility layout, resulting in significant sales, job creation, and cost savings.
- Jeff Shook at GENEDGE , an Engagement Manager, stands out for his skill in improving how plants are arranged and operated. Thanks to his international experience and hands-on work with the renowned Toyota Production System, Jeff has played a key role in bringing manufacturing back to local shores and driving efficiency in a range of sectors. He’s known for significantly upgrading Pioneer Electronic Corporation’s assembly lines to handle thousands of products every day and for improving the manufacturing of heating, ventilation, and air conditioning (HVAC) units at Daikin Applied Americas, which greatly boosted their output and quality.
- Chad H. Goff at GENEDGE , an engagement consultant with over 29 years of experience in product management, spearheads 2D & 3D design and oversees large-scale projects. Chad excels in utilizing Digital Twin technology and software like FlexSim to refine manufacturing processes and create digital plant layouts.
Redefine Your Factory Plant with GENEDGE
Remember, perfection may be a moving target, but with lean, you’re always driving forward—the quest for improvement is unending. Ready to start this transformative journey? Partner with GENEDGE. Our expertise will guide you through every step, from initial assessment to final implementation, ensuring continuous improvement becomes the hallmark of your manufacturing operations. Get a free assessment with GENEDGE today.
Join the Conversation Cancel reply
Log into your account to leave comments.
Related Resources
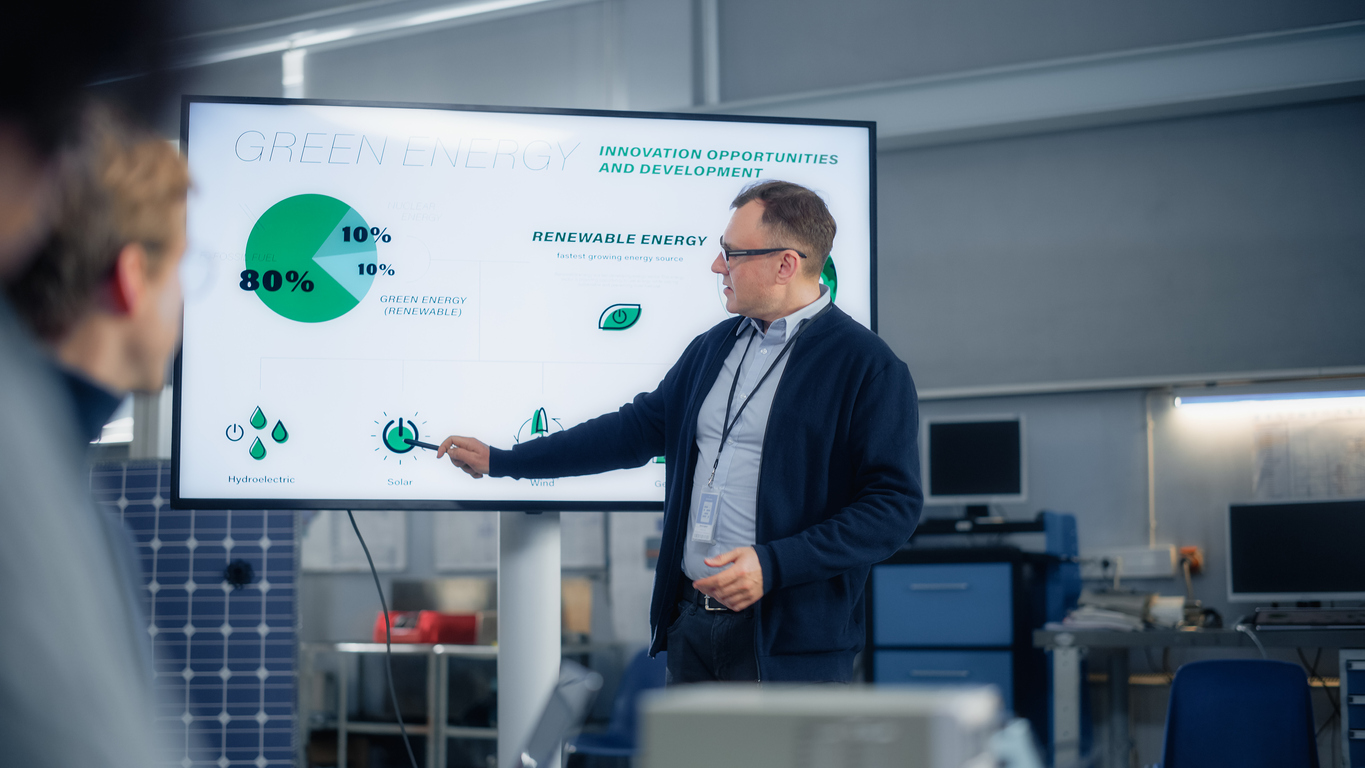
GENEDGE's Expertise in energy Management for Small Manufacturers
Energy is one of the largest expenses for small and medium manufacturers. According to the U.S. Energy Information Administration (EIA), the industrial sector, which includes manufacturing, accounted for 35% of total U.S. end-use energy consumption and 33% of total U.S. energy consumption in 2021. Manufacturing alone accounted for 76% of...
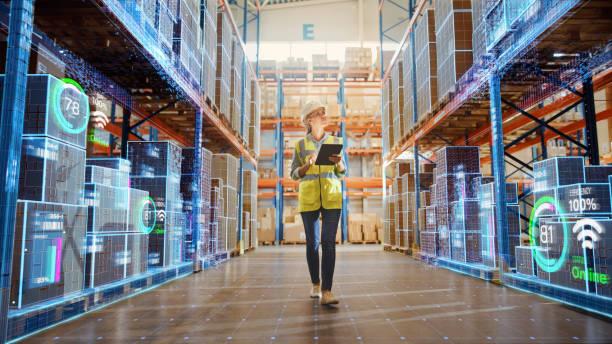
How Virginia is Leading the Way in Smart Manufacturing with IoT
Imagine a factory where everything is connected, intelligent, and responsive. Where machines can talk to each other, monitor their own performance, and optimize their operations. Data flows seamlessly from the shop floor to the cloud, providing insights and feedback. Where products can be tracked and traced from the source to...
Check out everything that is new in the latest version of Visual Components!
December 28, 2021
How to Plan & Design a Manufacturing Plant Layout? (Video Examples Included)
Our experts at Visual Components discuss how to plan and design a manufacturing plant layout with a simulation case. We review the benefits, process, and necessity for a high-quality plant layout in your business organization.
Discover the essentials of factory layout design using advanced simulation and CAD technology. This approach aims to optimize space and efficiency, catering to each factory’s unique needs. Learn about creating lean layouts that streamline production and enhance workflow. Gain insights into how strategic planning can lead to cost savings and increased productivity. Explore the steps from concept to execution, including real-world examples, demonstrating the benefits of effective layout planning for manufacturing success.
Share this article

When it comes to running a manufacturing facility, there are a lot of things to consider. As an owner or manager, you’re probably looking for ways to speed up your process, improve your yield, and increase your profit. Did you know that a simple plant layout can achieve all three of these goals?
Layouts are often overlooked, despite their huge money-saving potential.
In this piece, we’ll discuss what is meant by a plant layout, some benefits of a layout, an example, and our step-by-step process for laying out a plant.
These are the topics we’ll cover. You can also jump to the part that interests you the most 🏃🏻
- What is meant by a plant layout?
- What is a lean plant layout?
- What are the characteristics of a good plant layout?
- Plant layout design benefits
Plant layout example
- Step-by-step plant layout design process
- Case: tire assembly and warehousing layout
Let’s go!
What is meant by a plant layout?
The plant layout definition is simple: it’s a way to draw your facility’s building, equipment, and major components on paper. It’s typically done through 2D CAD (2-dimensional Computer-Aided Drafting and Design) software.
The designer will use real-world dimensions of your equipment and facility and layout a scaled model of your plant. Without using real dimensions, the final layout won’t be as helpful for your plant.
In a lot of cases, the designer will submit a final layout that allows the viewer to fly through the building, seeing the equipment in motion and observing how the process looks. Since everything is a scale model, the viewer can find out how much distance there is between equipment, for walkways, and so on.
Since it’s all done on paper, this can be done before getting equipment or before having a warehouse. It also allows the designer to change the layout as much as they’d like.
The layout includes a lot of different features:
- How product moves through your building
- Equipment
- Building floorplan
- Dimensional distances between everything
- Visualization of your process
What is a lean plant layout?
If you take the concept one step further, you can start optimizing everything. In a lean plant layout, the designer will start incorporating lean principles into the floorplan.
A big principle in lean layouts is adding sections for different operations. If your process has multiple steps, like cutting, organizing, and packing your product, then it will be broken into different physical areas.
Cutting will be done in one zone, organizing in another, and packing in a third. This also groups together the required machinery and personnel to expedite the process.
Why does this work? Material and people travel shorter distances, the layout is more compact, and everything is streamlined.
There are a lot of other concepts that go into lean principles (a lean layout). For the sake of brevity, we’ll leave it there.
What are the characteristics of a good plant layout?
Knowing whether a plant layout is good or not really depends on your operations and needs. In general, there are a few characteristics to look for:
- Effectively uses the space . One of the limiting factors in your operation is how much space you have. You can’t just invent new space, so you have to get creative with the space you have. A good plant layout effectively uses every square inch of operation space.
- Accessible design . At the end of the day, there should be enough space between items for the full floorplan to be accessible. This means that material handlers need enough space for themselves as well as the product they’re carrying around the building.
- Flexibility for future growth . Make sure that the floorplan isn’t going to constrict your operation. A lot of manufacturing plants benefit by adding a potential for 20-40% growth. This doesn’t mean that you have to predict exactly how much you’ll grow in a decade, just design with future growth in mind.
- Has your operation in mind . You need a layout that works for your individual operation. There are very few cookie-cutter solutions that fit the needs of your business — your layout is the same way. A good plant layout is specialized to what your business needs.
If you want to oversimplify this idea, a good plant layout is one that achieves the goals of your operation while optimizing every possible parameter.
Plant layout design benefits
Why do people spend so much time putting together a plant layout? There are a number of benefits. Let’s quickly review some of the top reasons why people opt for a plant layout in their business organization.
Reduce cycle time
Cycle time is a term that quantifies how long it takes a business to make a product. It’s the combination of every process step that’s required to make your end product.
With a good plant layout, everything is set up with the operation in mind. As a result, businesses will see a reduced cycle time.
Increase Operational Speed
On top of an overall speed increase, you’ll find speed increases in every step of the process. This goes back to the idea of splitting your operation into different zones.
Rather than an operator walking across your warehouse to perform a task, everything will be centralized. Think of it as storing the knives next to the cutting board in your kitchen.
Maximize Your Square Footage
Depending on where you’re located, the price of your land could be your biggest expense. Due to that fact, most people want to maximize their square footage.
With a manufacturing plant layout, you have the ability to move equipment around on paper in order to maximize your square footage.
The designer can do things like relocating, rotating, and reorienting equipment to see which option makes the most sense for your facility. Clearly, this is a lot faster and less expensive than physically changing around equipment and testing the new layout.
Visualize and Tweak Your Operational Process
Once things are laid out, it might help you to see a potential shortcut in your operation. Maybe you can save time and money by moving one step of your process to another part of the cycle.
This is highly dependent on your operation, but we’ve seen it happen in the past: a company thinks their operation is optimized until they do a plant layout and notice some shortcomings.
Maximize Profits
When you combine all of these factors, you’re left with one big benefit: maximized profits. This is the major reason why a lot of businesses opt for putting together a plant layout.
You save time, space, and create more products each year. That should sound like millions of dollar signs annually.
To help illustrate this idea, let’s look at an example. Our team at Visual Components lead the design for a company called Midea.
Here’s a case study of one of our previous clients, Midea . They’re the world’s largest producer of major appliances. Before adding a new, high-end production line, they decided to get a plant layout.
Our simulation looked at the real-world size and operational speed of their different machines. We worked closely with their team to understand how the process works, what the limiting factors were, and what kind of flow their operation had.
This video cannot be displayed unless all necessary Cookies are accepted. Youtube uses three cookies that are VISITOR_INFO1_LIVE, CONSENT, YSC and they all live in targeting cookies category Accept all Cookie settings
After we produced some rounds of layouts, we arrived at, what both parties deemed to be, the best possible arrangement. We saved their operation a lot:
- Floor space used was reduced by 10%
- Production capacity increased 10%
- Reduced product defects by 10x
- Construction schedule expedited 20%
- Total project cost savings: $879,000, roughly 15%
- Long-term labor cost reduction, operational efficiency increase, and projected profit increase
This project for Midea shows the importance of lean plant layouts. We foresee an increase in their profits year over year — this isn’t just a short-term, upfront cost saving. The future of their operation will benefit thanks to an initial plant layout.
Step-by-step plant layout design process with a case example
Curious about what the plant layout design process looks like? Here’s a step-by-step process that we typically follow for our clients. Here’s our workflow for planning and building a plant layout:
1. Understanding clients’ needs
It all starts with understanding our clients’ needs. Before a plant layout can be generated, some information about the operation needs to be explored.
This entails a few conversations going over some basics like floor space, equipment, flow, and more.
For example, our customer Firac received a clear request from their client — to automate a manual screw tightening process. Read the whole story.
2. Planning manufacturing system design
Now it’s time to start drafting. Different companies will opt for different manufacturing programs in this step.
Some companies will only provide a 2D layout with no motion included. Others will use a 3D layout that shows how the equipment will move and how the product goes through the cycle.
At Visual Components, we typically use a 2D layout for the building and add a static 3D layout on top. This overlay ensures dimensional accuracy which is paramount in making a plant layout.
3. Equipment selection
Now it’s time to select and add equipment. This will go right into our static 3D layout, so it can be changed later.
Things like the overall size, motion constraints, and equipment parameters will be inputted during this step. This is done to ensure the model is precise and accurate.
As you probably noticed from our Midea case study, the equipment physically moves and operates in our model. During this step, we’re making sure our clients get the best visual of their potential layout.
To help our clients save time on equipment selection, we offer ready-made components. Visual Components eCatalog has a library of virtual models of robots, machines, and equipment from dozens of leading brands in industrial automation. We have over 1,500 pre-defined and ready-to-use components, to be exact.
4. Layout design
Once the equipment is selected, the designer can start moving around components. This is part of the optimization process where items are moved around until they’re in the perfect place.
Since the equipment and building are already drawn on the computer, this step is more of a “drag and drop” process. On the computer, the designer will move around equipment, change its orientation, and find the best place for the physical pieces.
Jump to 2:34-5:50 in the video below to see how it works in practice.
5. Define the flow
In step 5, we’ll start optimizing the flow. There are three major parts of this step:
- Defining the products
- Defining the processes
- Defining the process flow
There’s some overlap between this and the first step on the list. However, this step focuses on optimizing everything from a layout perspective.
This might mean changing the location of equipment, storage, and walkways to improve the overall process.
The flow is how the material cycle looks in your operation. In other words, when you trace the product from raw material to shipment, that’s the flow.
Jump to 6:43-9:22 in the same video below to see how it works in practice.
6. Simulation
With all of these parameters in mind, our team is ready to put together a simulation. The simulation will show the material and how it physically moves down the line.
A simulation is a 3D video that shows a flyby through your facility. It shows how the equipment and product move throughout. The Midea video discussed earlier is a great example of a simulation that our team makes.
However, this isn’t the final stage. Part of the simulation entails finding bottlenecks. This is where your operation is slowing down and hurting the production speed.
After finding a bottleneck, our team will work to alleviate them. Removing even one bottleneck in your operation can result in a huge performance improvement.
Some of our design software comes with plant layout analysis that aides us in targeting and alleviating these bottlenecks. This is another benefit of using computer-based plant layouts.
7. Modify And Validate the Changes
The final stage is all about making changes to improve the design. We typically target metrics when it comes to the use of space, operation cycle time, and the ability for product defects.
These changes result in faster speeds and more room for profit within your business on an annual scale.
If this layout is done before construction, you’ll also find some construction cost savings built into this step.
The validation stage involves our clients and getting valuable feedback from you.
Case: Tire Assembly and Warehousing Layout
Let’s discuss a case where the task was to design, simulate, analyze and optimize a manufacturing and warehousing system based on predefined production and layout goals.
This case is about a tire assembly and warehousing facility that is capable of handling a certain number of tires before they are supplied to a downstream assembly line. We can assume that the downstream is a car manufacturing plant.
Products and product variants
The product that we had to work with in this case was tires however there were many product variants.
First, we had three tires types meaning tires in three different materials.

Next, we had five tire sizes in the three tire types. These sizes are represented in different colors of tire rims.

So including all the product variants, we had to design a system that could handle 15 different tires.
Production goals
Once the products and product variants were clear, the next step was to evaluate the pre-defined goals. Here’s the list of the production goals that we had to meet,
- The customer needed a setup that was capable of handling all these tires in batches of 4.
- The downstream assembly required that this tire plant could supply 720 tires per hour regardless of how many it can store. The main objective was to have a functional system that provides uninterrupted supply to the downstream assembly regardless of how many tires it could store.
- Since we were working with batches of 4, 720 tires per hour meant that the goal was to supply 3 sets of tires per minute.
Layout Goals
Based on the production goals, there were also some layout goals,
- There must be enough buffer to recover from possible machine downtime.
- There must be enough warehouse to store tires for 5 hours of production meaning 900 sets in 5 hours and they must be available at all times to ensure any downtime does not interrupt the downstream supply.
- Also, in addition to storage, we needed to ensure that we had enough conveyor capacity to handle this amount and variety of products.
Layout Overview and Functionality
There layout was then designed based on the given production and layout goals. Here is a video for a closer look at the layout design and functionality of different sections,
1. The tire types are fed to the robot cell as a batch of 4.
2. Next, Tire rims which represent different sizes of the tires are incoming through conveyors behind the robot cell.
3. The robot cell is designed with 4 assembly lines. Each of these has a Yaskawa HP20RD robot on top of a smart pedestal with a tire tool. This tire tool helps to pick the tire type, lubricate it and assemble it with the rim.
4. Once Assembled, these tires go through a different set of machines where they are fixed and balanced before they are ready to be stored in the warehouse.
5. The tires are then sent towards the warehousing side with five storage sections, one for each tire size and four cartesian robots.
6. Each of these robots has certain tasks assigned to them shortly explained here,
- The first red cartesian robot sorts the tires by sizes onto their specific conveyors
- The second dark grey cartesian robot picks one stack of tires at a time and places them in their relevant tire size storage section.
- The third dark grey cartesian robot with beige pillars stores the tires by their sizes in the storage section and also supplies the sets forward when needed.
- The fourth steel-blue robot that is closer to the entrance of the warehousing collects the supplied stacks of tires released by the previous robot and places them in the rack. These racks are then picked and stored by the forklift in the next storage area.
7. From the last storage, the tires are then supplied to the downstream assembly as they’re needed.
Performance evaluation of the designed systems
Initially, two scenarios were designed and their simulation performance was evaluated.
The first scenario consisted of 4 robot assembly lines.

The second one had 5 robots assembly lines.

Later, we realized that machine breakdowns are not taken into account in the first two scenarios. Machine breakdowns could be due to many reasons but the most common reason for a production stoppage is usually Maintenance. So, the Maintenance times or Mean Time Between Failures (MTBF) averaging 150 seconds were added to the machines in the robot cell. Also, the maintenance cycle was defined which meant the machine maintenance had to be carried out after every 30 tires were produced.

After these metrics were clear and defined, two more scenarios were built, basically, the same and 1st and 2nd scenarios but now with MTBF values included.

Overall, four scenarios were designed and simulated. Here is the summary of all scenarios with their production output.

The difference in the production output is quite clear between scenarios where MTBF values were not considered and once they were. Based on the scenarios, it was safe to say that Scenario four with five assembly lines was able to generate the required goal of 780 tires per hour. This scenario was then locked as the final design for this case.
Summary of case results
Some important conclusions of this case were,
- The designed system was capable of handling batches of four tires in all the product variants.
- There was enough buffer to recover from possible machine downtimes.
- The production rate of tire assembly was not constant after the maintenance times were added but with enough buffers and storage systems, the supply to downstream was smooth.
- The last but one of the most important lessons to learn from this case was if the simulation is run with too few details, the results may be wrong like the clear difference between the production outputs in the first two scenarios compared to the last two.
Conclusion
We just reviewed how to plan and design a manufacturing plant layout. Now, you should know the benefits and process that goes into making a layout for your plant. With Visual Components , designing a plant layout is more logical, visual, and easier to do. Contact us today to get started. We’ll show you how your operation can save time and money thanks to our services.
Curious to learn more on the topic? Be sure to download our eBook about planning and optimizing your manufacturing plant layout.
Further reading
Boosting Production Line Efficiency: A Guide on Improving Production Output
Blog | March 27, 2024 Industry
An Introduction to Virtual Commissioning
Blog | February 22, 2024 Industry
Are Manufacturers Really Ready for the Digital Era? (Survey Results)
Blog | October 16, 2023 Industry
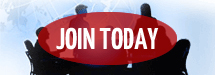
DO I NEED TO KNOW THIS CHECK POINT?
OPERATIONS MANAGEMENT CHECK POINT 68: PLANT LAYOUT
Please Select Any Topic In Check Point 68 Below And Click .
HOW CAN YOU BENEFIT FROM CHECK POINT 68?
LEAN MANAGEMENT GUIDELINES FOR CHECK POINT 68
LEAN OPERATIONAL GUIDELINES RELATED TO PLANT LAYOUT
ADDITIONAL INFORMATION ONLINE
IMPORTANT FACTORS IN PLANT LAYOUT DESIGN
The planning procedure and Plant Layout design depend primarily upon the nature of the manufacturing or operational process . It is important, therefore, to identify the particular parameters of the manufacturing or operational process and to establish the most suitable type of production or operations at the outset of the plant layout planning procedure. Furthermore, there is a need to determine the Total Capacity Of The Facility and to evaluate the future requirements of the expansion program. The ultimate purpose of the plant layout design process is the completion of several tasks outlined below.
PLANT LAYOUT DESIGN TASKS
Certain companies, however, may decide to employ any combination of the above types of plant layout within the same facility to ensure maximum flexibility of overall operational abilities.
ARE YOU SERIOUS ABOUT YOUR BUSINESS TODAY?
Reprinted with permission.
LESSON FOR TODAY: Your Plant Layout Today Will Determine Your Profit Layout Tomorrow!
Go To The Next Open Check Point In This Promotion Program Online.

Manufacturing plant layout design
- Digital Factory & Factory Design
- André Heller
- last updated: 31. March 2023
Maximize Efficiency and Productivity

When it comes to planning a new plant or factory layout, there are many things to consider creating an efficient and effective design. The type of manufacturing process, the machinery and equipment required, the flow of production, and the overall operation of the plant all need to be taken into account. With so many elements to pay attention to, it’s no wonder that plant layout and design is often seen as a daunting task. However, with careful planning and execution, it is possible to create a well-designed and efficient manufacturing plant that can support a successful business.
The Benefits of an Efficient Plant Layout
Planning and designing a plant layout is an important step in the manufacturing process. It can have a significant impact on efficiency, machinery, and flow. Industrial Engineering professionals are experts in plant design and can help planters design a layout that is best suited to their needs. A well-designed plant can help improve production and operation management.
Factors to Consider When Designing a Plant Layout
Reorganizing the layout of a factory plays an integral role in production. By reforming and restructuring, it is possible to optimize efficiency, cut costs and facilitate communication. There are many different configurations that can be adopted; one popular approach is setting up stations along a definite path – referred to as ‘production line’ design. Alternatively, workstations may follow the order of manufacturing processes, which is known as ‘process arrangement’. If you haven’t fully analyzed your type of production, start with our blog post Job shop production vs. production line?
Types of Plant Layouts
When it comes to plant layout and design, there are a few different types that you can choose from. The type of layout or design that you choose will depend on the type of manufacturing process that you are using, as well as the kind of equipment and machinery that you have in your factory. Here are a few of the most common types of plant layout and design:
1. Process-oriented layout: This type of layout is designed around the manufacturing process. The goal is to create a smooth and efficient flow of production so that each operation can be carried out in the most efficient way possible.
2. Equipment-oriented layout: This type of layout is designed around the machinery and equipment in the factory. The goal is to create a flow that is efficient and makes best use of the available space and resources. Sankey-diagrams will help you, to make the flow more tangible.
3. people-oriented layout: This type of layout is designed around the people who will be working in the factory. The goal is to create a comfortable and safe working environment, with easy access to all the necessary equipment and resources. Cardboard engineering is a typical method to adress these issues.
4. product-oriented layout: This type of layout is designed around the products that will be produced in the factory. The goal is to create a flow that is efficient and makes best use of the available space and resources. You can switch over to our blogpost, in case you want to get a deeper understanding about What is a production cell?
5. hybrid layout: This type of layout combines elements from two or more of the above types of layouts. The goal is to create a layout that is custom-tailored to the specific needs of the manufacturing process. Creating an ideal-layout is your first step for designing these types of manufacturing.
Strategies for Optimizing Your Plant Layout
When it comes to running a successful manufacturing process, having an efficient plant layout is essential. An effective facility ensures that all parts of the production process are connected, equipment and machinery are adequately spaced, and the flow of materials is efficient. Industrial Engineering and Plant Design play a key role in mapping out the placement of equipment and machinery in a facility. Here are some tips for creating an effective plant layout:
1. Include Your Operations Management Team – It’s important to involve your operations management team when creating a plant layout. They understand the operational needs and have a deeper understanding of how all the processes interact with each other. Having them involved will ensure that all aspects are considered before making any final decisions. If you want to know more on the importance, you may read through our blogpost Teamwork in shopfloor layout planning .
2. Analyze Workflow – Every production process has its own workflow, and it’s important to analyze this before designing a layout. This will help you determine where to place different pieces of equipment and machinery so that everything flows efficiently within the facility. Learn more about how to analyze the flow: Material flow planning to optimize logistics, production, and storage
3. Allow Room For Growth – When designing your manufacturing layout, be sure to keep in mind future growth. The last thing you want is to be stuck with a design that can’t accommodate additional equipment or personnel if need be. Any manager would no doubt agree that optimized space utilization in production and logistics areas is a key goal of factory planning.
4. Keep Safety In Mind – The safety of workers should always be top priority, as well as adhering to local regulations regarding safety standards in industrial spaces. Make sure pathways are wide enough for workers to move around safely, adequate lighting is installed throughout the facility, and emergency exits are clearly marked at all times. Floormarkings are an important topic: How important are floor markings in industry settings?
A well-designed layout for a plant can mean the difference between success and failure. By taking the time to design a custom layout, manufacturers can improve communication, efficiency and decrease costs.
No problem, simply subscribe to our Blog-News!
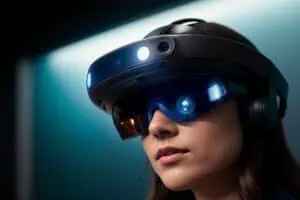
Liked This Article?
By entering your email, you agree to receive future messages about visTABLE® and have read the Privacy Policy .
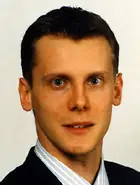
Hello, I am glad that you are interested in my article.
Do you wish to be informed about new content?

- Basic Types of Plant Layouts
Table of Contents
Plant layout is a crucial aspect of operations management that directly impacts productivity, efficiency, and safety within a manufacturing facility. In this blog, we’ll explore the fundamental types of plant layouts, each with its unique advantages and applications.
Plant Layout Basics
Plant layout refers to the arrangement of machines, equipment, workstations, and resources within a manufacturing or production facility. The choice of layout depends on factors such as the type of product being manufactured, production volume, workflow, and safety considerations. Here are the basic types of plant layouts:
1. Process Layout (Functional Layout)
- Description: In a process layout, similar machines and equipment are grouped together based on their functions or processes. Each department or section specializes in a specific operation.
- High flexibility to accommodate changes in product types.
- Specialization leads to expertise in specific tasks.
- Equipment is utilized efficiently within departments.
- Job shops and small-scale manufacturing where product variety is high.
- Hospitals and service organizations with specialized departments.
2. Product Layout (Line Layout)
- Description: A product layout arranges machines and workstations in a linear or assembly line fashion. Each workstation is dedicated to a specific task in the production process.
- High production efficiency with reduced material handling.
- Consistent product quality and standardized processes.
- Lower labor costs due to specialized tasks.
- Mass production environments such as automobile assembly lines.
- High-volume manufacturing of standardized products.
3. Fixed-Position Layout
- Description: In a fixed-position layout, the product remains stationary, and all resources, equipment, and workers are brought to the product. This layout is common in large projects like construction sites and shipbuilding.
- Suited for large and heavy products or projects.
- Minimizes the need for moving heavy items.
- Provides control over project management.
- Construction sites, shipbuilding, and aircraft manufacturing.
- Large-scale infrastructure projects like bridges and dams.
4. Cellular Layout (Group Layout)
- Description: Cellular layout groups machines and workstations into self-contained cells, each responsible for a specific set of processes. Within a cell, machines are arranged to optimize flow.
- Enhanced communication and collaboration within cells.
- Reduced material handling and lead times.
- Flexibility to handle a variety of products with minimal changeover.
- Lean manufacturing environments aiming for efficiency and waste reduction.
- Small to medium-scale production with frequent product changes.
5. Hybrid Layout
- Description: A hybrid layout combines elements of different layout types to suit the specific needs of a manufacturing facility. It may involve a mix of product, process, or cellular layouts.
- Tailored to meet unique production requirements.
- Allows for flexibility and adaptability.
- Optimizes resources based on varying demands.
- Complex manufacturing environments with diverse product lines.
- Facilities that prioritize both efficiency and flexibility.
Choosing the right plant layout is a critical decision in operations management. Each type of layout has its advantages and applications, making it essential for organizations to carefully consider their production needs and goals when designing their workspaces. MBA students studying Operations Management should understand these basic types of plant layouts as they form the foundation for efficient and effective manufacturing processes.
How useful was this post?
Click on a star to rate it!
Average rating 5 / 5. Vote count: 1
No votes so far! Be the first to rate this post.
We are sorry that this post was not useful for you! 😔
Let us improve this post!
Tell us how we can improve this post?
Management of Machines and Materials
1 Operations Management-An Overview
- Systems Concepts in Operations Management
- Objectives in Operations Management
- Operations Management Decisions
- Types of Production Systems
- Management of Materials in Production Systems
- Concepts in System Life-cycle
- Role of Scientific Method in Operations Management
- Historical Development of Operations Management
2 Product Selection and Process Selection
- Introduction to Product Selection
- The Product Selection Process
- Selection of the Products
- Product Development
- Product Design
- Introduction to Process Selection
- Forms of Transformation Processes
- The Project Form
- Intermittent Flow Processes
- Continuous Flow Processes
- Processing Industries
- Selection of the Process
3 Facilities Location
- When does a Location Decision Arise?
- Steps In the Facility Location Study
- Subjective, Qualitative and Semi-Quantitative
- Techniques Locational Break-Even Analysis
- Some Quantitative Models for Facility Location
- Some Case Examples
4 Facilities Layout and Material Handling
- Plant Layout Factors
- Layout Design Procedure
- Flow and Activity Analysis
- Space Determination and Area Allocation
- Computerised Layout Planning
- Evaluation, Specification, Presentation and Implementation
- Materials Handling Systems
- Materials Handling Equipment
5 Planning and Control for Mass Production
- When to Go For Mass Production
- Features of a Mass Production System
- Notion of Assembly Lines and Fabrication Lines
- Design of an Assembly Line
- Line Balancing Methods
- Problems and Prospects of Mass Production Modular
- Production and Group Technology
- Automation and Robotics
6 Planning and Control for Batch Production
- Features of Batch Production
- How to Determine the Optimum Batch Size
- Aggregate Production Planning
- Material Requirements Planning
- The Line of Balance (LOB)’ for Production Control and Monitoring
- Problems and Prospects of Batch Production
7 Planning and Control for Job Shop Production
- Variety of Problems in Job Production
- n Jobs One Machine Case
- n Jobs Two Machines Case
- Two Jobs m Machines Case
- Scheduling Rules for Job Shops (Job Shop Scheduling)
- Problems and Prospects of Job Production
8 Planning and Control of Projects
- Defining Projects
- Network Representation of Projects
- Time Management of the Project
- Critical Path Method (CPM)
- Programme Evaluation and Review Technique (PERT)
- Time Cost Relationship and Project Crashing
- Resource Allocation
- Project Updating and Monitoring
9 Capacity Planning
- Meaning, Definition and Measure Of Capacity
- Process for Capacity Planning
- Predicting Future Capacity Requirements
- Generation of Capacity Plans
- Evaluation of Alternate CapacityPlans
10 Work and Job Design
- Introduction to Work Design
- The Work Study Approach
- Method Study
- Work Measurement
- Work Study Application
- Introduction to Job Design
- Design Factors
- Environmental Factors
- Organisational Factors
- Behaviour Dimensions of Job Design
- Socio-Technical Approach to Job Design
11 Value Engineering and Quality Assurance
- Basic Concepts in Value Engineering
- Historical Perspectives
- Functions and Value
- Value Engineering Job Plan
- Fast Diagram as Value Engineering Tool
- Some Case Studies in Value Engineering
- Behavioural and Organisational aspects of Value Engineering
- Benefits of Value Engineering and concluding Remarks
- Introduction of Quality Assurance
- Concept of Quality
- Cost of Quality
- Quality Management
- Quality Organisation
- Acceptance Sampling
- Process Control
- Use of Computers in Quality Control
12 Purchase System and Procedure and Inventory Management
- Introduction: Role of Purchasing Function
- Preparation of Inputs
- Restraints and Factors
- Purchasing Decisions
- Purchasing Organisation
- Procedures, Forms, Records and Reports
- Evaluation of Departmental Procedures
- Vendor Evaluation and Rating
- Computerized Purchasing Systems
- Purchasing in Government Organisations
- Introduction to Inventory Systems
- Functions of Inventory
- Classification of Inventory Systems
- Selective Inventory Management
- Exchange Curve and Aggregate Inventory Planning
- Deterministic inventory Models
- Probabilistic inventory Models
- Inventory Control of Slow Moving items
- Recent Developments in Inventory Management
13 Standardization, Codification and Variety Reduction
- Classification of Materials
- Codification
- Standardisation and Variety Reduction
14 Waste Management
- Complementarity of Waste Management and Resource Management
- Taxonomy of Wastes
- Definition of Wastivity: Gross and Net Wastivity
- The Functional Classification of Waste Management
- Outline of I-O-W (Input Output Waste) Model
- Treatment of Wastage in Cost Accounts
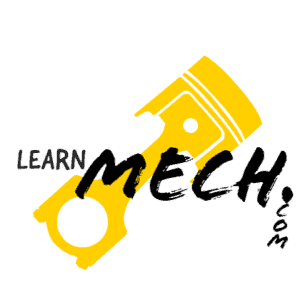
What Is Plant Layout | Objectives and Principles
What is Plant Layout :
Plant layout is the most effective physical arrangement, either existing or in plans of industrial facilities i.e. arrangement of machines, processing equipment and service departments to achieve greatest co-ordination and efficiency of 4 M’s (Men, Materials, Machines and Methods) in a plant.
Layout problems are fundamental to every type of organization/enterprise and are experienced in all kinds of concerns/undertakings. The adequacy of layout affects the efficiency of subsequent operations.
Definitions of Plant Layout : According to James Lundy, “Layout identically involves the allocation of space and the arrangement of equipment in such a manner that overall operating costs are minimized”. In the words of Mallick and Gandreau, “Plant layout is a floor plan for determining and arranging the designed machinery and equipment of a plant, whether established or contemplated, in the best place, to permit the quickest flow of material, at the lowest cost and with the minimum handling in processing the product, from the receipt of raw material to the shipment of finished product”.
According to Apple, “Plant layout is planning the path each component/ part of the product is to follow through the plant, coordinating the various parts so that the manufacturing processes may be carried out in the most economical manner, then preparing drawing or other representation of the arrangement and finally seeing that the plan is properly put into effect.” (Plant Layout and Material by Apple).
Plant layout means the disposition of facilities like equipments, material, manpower etc. and the services of the plant within the area of the site selected for plant setup. It begins with the design of the factory building and extends up to the location and movement of a work table. All the equipments and resources are given a proper place.
Need of Plant layout:
Many situations give rise to the problem of plant layout. Two plants having similar operations may not have identical layout. This may be due to size of the plant, nature of the process and management’s caliber. The necessity of plant layout may be feel and the problem may arise when.
(i) There are design changes in the product.
(ii) There is an expansion of the enterprise.
(iii) There is proposed variation in the size of the departments.
(iv) Some new product is to be added to the existing line.
(v) Some new department is to be added to enterprise and there is reallocation of the existing department.
(vi) A new plant is to be set up.
Objectives of a good plant layout:
1. Material handling and transportation is minimized and efficiently controlled 2. Bottlenecks and points of congestion are eliminated (to make the raw material and semi finished goods move fast between consecutive work stations) 3. Suitable and adequate spaces are allocated to production centres and service centres 4. Minimizing the workers movement 5. Enhancing safety of the working conditions for all employees 6. Increased flexibility in design changes for future changes and expansion 7. Reduced plant maintenance cost
Principles of Plant layout: a) Integration of production facilities in an efficient manner b) Minimum movements and material handling c) Smooth and continuous flow, by implementing proper line balancing techniques d) Cubic space utilization by saving the floor space for storage and making use of ceiling e) Safe and improved environments in shape of safe and efficient work places
f) Flexibility for accommodating changing product designs and production process
Related posts:

Sachin Thorat
Sachin is a B-TECH graduate in Mechanical Engineering from a reputed Engineering college. Currently, he is working in the sheet metal industry as a designer. Additionally, he has interested in Product Design, Animation, and Project design. He also likes to write articles related to the mechanical engineering field and tries to motivate other mechanical engineering students by his innovative project ideas, design, models and videos.
Leave a Reply Cancel reply
Your email address will not be published. Required fields are marked *
Save my name and email in this browser for the next time I comment.
This site uses Akismet to reduce spam. Learn how your comment data is processed .
Recent Posts
Top Branches of Mechanical Engineering
Mechanical Engineering is an essential discipline of engineering encompassing many specializations, with each contributing its unique aspect to the dynamic and inventive nature of this field. With...
Shree Ram Ayodhya Murti, idol - Vector , Wallart
The Ram Lalla idol, which is installed at Ayodhya's Ram temple has many significant religious symbols from Hinduism. All 10 incarnations of Lord Vishnu are engraved on the idol. Notably, Lord Ram is...

How to Write a Business Plan: Step-by-Step Guide + Examples
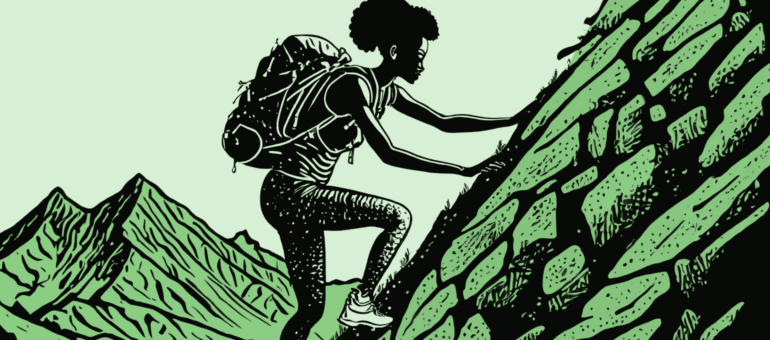
Noah Parsons
24 min. read
Updated May 7, 2024
Writing a business plan doesn’t have to be complicated.
In this step-by-step guide, you’ll learn how to write a business plan that’s detailed enough to impress bankers and potential investors, while giving you the tools to start, run, and grow a successful business.
- The basics of business planning
If you’re reading this guide, then you already know why you need a business plan .
You understand that planning helps you:
- Raise money
- Grow strategically
- Keep your business on the right track
As you start to write your plan, it’s useful to zoom out and remember what a business plan is .
At its core, a business plan is an overview of the products and services you sell, and the customers that you sell to. It explains your business strategy: how you’re going to build and grow your business, what your marketing strategy is, and who your competitors are.
Most business plans also include financial forecasts for the future. These set sales goals, budget for expenses, and predict profits and cash flow.
A good business plan is much more than just a document that you write once and forget about. It’s also a guide that helps you outline and achieve your goals.
After completing your plan, you can use it as a management tool to track your progress toward your goals. Updating and adjusting your forecasts and budgets as you go is one of the most important steps you can take to run a healthier, smarter business.
We’ll dive into how to use your plan later in this article.
There are many different types of plans , but we’ll go over the most common type here, which includes everything you need for an investor-ready plan. However, if you’re just starting out and are looking for something simpler—I recommend starting with a one-page business plan . It’s faster and easier to create.
It’s also the perfect place to start if you’re just figuring out your idea, or need a simple strategic plan to use inside your business.
Dig deeper : How to write a one-page business plan
Brought to you by
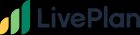
Create a professional business plan
Using ai and step-by-step instructions.
Secure funding
Validate ideas
Build a strategy
- What to include in your business plan
Executive summary
The executive summary is an overview of your business and your plans. It comes first in your plan and is ideally just one to two pages. Most people write it last because it’s a summary of the complete business plan.
Ideally, the executive summary can act as a stand-alone document that covers the highlights of your detailed plan.
In fact, it’s common for investors to ask only for the executive summary when evaluating your business. If they like what they see in the executive summary, they’ll often follow up with a request for a complete plan, a pitch presentation , or more in-depth financial forecasts .
Your executive summary should include:
- A summary of the problem you are solving
- A description of your product or service
- An overview of your target market
- A brief description of your team
- A summary of your financials
- Your funding requirements (if you are raising money)
Dig Deeper: How to write an effective executive summary
Products and services description
This is where you describe exactly what you’re selling, and how it solves a problem for your target market. The best way to organize this part of your plan is to start by describing the problem that exists for your customers. After that, you can describe how you plan to solve that problem with your product or service.
This is usually called a problem and solution statement .
To truly showcase the value of your products and services, you need to craft a compelling narrative around your offerings. How will your product or service transform your customers’ lives or jobs? A strong narrative will draw in your readers.
This is also the part of the business plan to discuss any competitive advantages you may have, like specific intellectual property or patents that protect your product. If you have any initial sales, contracts, or other evidence that your product or service is likely to sell, include that information as well. It will show that your idea has traction , which can help convince readers that your plan has a high chance of success.
Market analysis
Your target market is a description of the type of people that you plan to sell to. You might even have multiple target markets, depending on your business.
A market analysis is the part of your plan where you bring together all of the information you know about your target market. Basically, it’s a thorough description of who your customers are and why they need what you’re selling. You’ll also include information about the growth of your market and your industry .
Try to be as specific as possible when you describe your market.
Include information such as age, income level, and location—these are what’s called “demographics.” If you can, also describe your market’s interests and habits as they relate to your business—these are “psychographics.”
Related: Target market examples
Essentially, you want to include any knowledge you have about your customers that is relevant to how your product or service is right for them. With a solid target market, it will be easier to create a sales and marketing plan that will reach your customers. That’s because you know who they are, what they like to do, and the best ways to reach them.
Next, provide any additional information you have about your market.
What is the size of your market ? Is the market growing or shrinking? Ideally, you’ll want to demonstrate that your market is growing over time, and also explain how your business is positioned to take advantage of any expected changes in your industry.
Dig Deeper: Learn how to write a market analysis
Competitive analysis
Part of defining your business opportunity is determining what your competitive advantage is. To do this effectively, you need to know as much about your competitors as your target customers.
Every business has some form of competition. If you don’t think you have competitors, then explore what alternatives there are in the market for your product or service.
For example: In the early years of cars, their main competition was horses. For social media, the early competition was reading books, watching TV, and talking on the phone.
A good competitive analysis fully lays out the competitive landscape and then explains how your business is different. Maybe your products are better made, or cheaper, or your customer service is superior. Maybe your competitive advantage is your location – a wide variety of factors can ultimately give you an advantage.
Dig Deeper: How to write a competitive analysis for your business plan
Marketing and sales plan
The marketing and sales plan covers how you will position your product or service in the market, the marketing channels and messaging you will use, and your sales tactics.
The best place to start with a marketing plan is with a positioning statement .
This explains how your business fits into the overall market, and how you will explain the advantages of your product or service to customers. You’ll use the information from your competitive analysis to help you with your positioning.
For example: You might position your company as the premium, most expensive but the highest quality option in the market. Or your positioning might focus on being locally owned and that shoppers support the local economy by buying your products.
Once you understand your positioning, you’ll bring this together with the information about your target market to create your marketing strategy .
This is how you plan to communicate your message to potential customers. Depending on who your customers are and how they purchase products like yours, you might use many different strategies, from social media advertising to creating a podcast. Your marketing plan is all about how your customers discover who you are and why they should consider your products and services.
While your marketing plan is about reaching your customers—your sales plan will describe the actual sales process once a customer has decided that they’re interested in what you have to offer.
If your business requires salespeople and a long sales process, describe that in this section. If your customers can “self-serve” and just make purchases quickly on your website, describe that process.
A good sales plan picks up where your marketing plan leaves off. The marketing plan brings customers in the door and the sales plan is how you close the deal.
Together, these specific plans paint a picture of how you will connect with your target audience, and how you will turn them into paying customers.
Dig deeper: What to include in your sales and marketing plan
Business operations
The operations section describes the necessary requirements for your business to run smoothly. It’s where you talk about how your business works and what day-to-day operations look like.
Depending on how your business is structured, your operations plan may include elements of the business like:
- Supply chain management
- Manufacturing processes
- Equipment and technology
- Distribution
Some businesses distribute their products and reach their customers through large retailers like Amazon.com, Walmart, Target, and grocery store chains.
These businesses should review how this part of their business works. The plan should discuss the logistics and costs of getting products onto store shelves and any potential hurdles the business may have to overcome.
If your business is much simpler than this, that’s OK. This section of your business plan can be either extremely short or more detailed, depending on the type of business you are building.
For businesses selling services, such as physical therapy or online software, you can use this section to describe the technology you’ll leverage, what goes into your service, and who you will partner with to deliver your services.
Dig Deeper: Learn how to write the operations chapter of your plan
Key milestones and metrics
Although it’s not required to complete your business plan, mapping out key business milestones and the metrics can be incredibly useful for measuring your success.
Good milestones clearly lay out the parameters of the task and set expectations for their execution. You’ll want to include:
- A description of each task
- The proposed due date
- Who is responsible for each task
If you have a budget, you can include projected costs to hit each milestone. You don’t need extensive project planning in this section—just list key milestones you want to hit and when you plan to hit them. This is your overall business roadmap.
Possible milestones might be:
- Website launch date
- Store or office opening date
- First significant sales
- Break even date
- Business licenses and approvals
You should also discuss the key numbers you will track to determine your success. Some common metrics worth tracking include:
- Conversion rates
- Customer acquisition costs
- Profit per customer
- Repeat purchases
It’s perfectly fine to start with just a few metrics and grow the number you are tracking over time. You also may find that some metrics simply aren’t relevant to your business and can narrow down what you’re tracking.
Dig Deeper: How to use milestones in your business plan
Organization and management team
Investors don’t just look for great ideas—they want to find great teams. Use this chapter to describe your current team and who you need to hire . You should also provide a quick overview of your location and history if you’re already up and running.
Briefly highlight the relevant experiences of each key team member in the company. It’s important to make the case for why yours is the right team to turn an idea into a reality.
Do they have the right industry experience and background? Have members of the team had entrepreneurial successes before?
If you still need to hire key team members, that’s OK. Just note those gaps in this section.
Your company overview should also include a summary of your company’s current business structure . The most common business structures include:
- Sole proprietor
- Partnership
Be sure to provide an overview of how the business is owned as well. Does each business partner own an equal portion of the business? How is ownership divided?
Potential lenders and investors will want to know the structure of the business before they will consider a loan or investment.
Dig Deeper: How to write about your company structure and team
Financial plan
Last, but certainly not least, is your financial plan chapter.
Entrepreneurs often find this section the most daunting. But, business financials for most startups are less complicated than you think, and a business degree is certainly not required to build a solid financial forecast.
A typical financial forecast in a business plan includes the following:
- Sales forecast : An estimate of the sales expected over a given period. You’ll break down your forecast into the key revenue streams that you expect to have.
- Expense budget : Your planned spending such as personnel costs , marketing expenses, and taxes.
- Profit & Loss : Brings together your sales and expenses and helps you calculate planned profits.
- Cash Flow : Shows how cash moves into and out of your business. It can predict how much cash you’ll have on hand at any given point in the future.
- Balance Sheet : A list of the assets, liabilities, and equity in your company. In short, it provides an overview of the financial health of your business.
A strong business plan will include a description of assumptions about the future, and potential risks that could impact the financial plan. Including those will be especially important if you’re writing a business plan to pursue a loan or other investment.
Dig Deeper: How to create financial forecasts and budgets
This is the place for additional data, charts, or other information that supports your plan.
Including an appendix can significantly enhance the credibility of your plan by showing readers that you’ve thoroughly considered the details of your business idea, and are backing your ideas up with solid data.
Just remember that the information in the appendix is meant to be supplementary. Your business plan should stand on its own, even if the reader skips this section.
Dig Deeper : What to include in your business plan appendix

Optional: Business plan cover page
Adding a business plan cover page can make your plan, and by extension your business, seem more professional in the eyes of potential investors, lenders, and partners. It serves as the introduction to your document and provides necessary contact information for stakeholders to reference.
Your cover page should be simple and include:
- Company logo
- Business name
- Value proposition (optional)
- Business plan title
- Completion and/or update date
- Address and contact information
- Confidentiality statement
Just remember, the cover page is optional. If you decide to include it, keep it very simple and only spend a short amount of time putting it together.
Dig Deeper: How to create a business plan cover page
How to use AI to help write your business plan
Generative AI tools such as ChatGPT can speed up the business plan writing process and help you think through concepts like market segmentation and competition. These tools are especially useful for taking ideas that you provide and converting them into polished text for your business plan.
The best way to use AI for your business plan is to leverage it as a collaborator , not a replacement for human creative thinking and ingenuity.
AI can come up with lots of ideas and act as a brainstorming partner. It’s up to you to filter through those ideas and figure out which ones are realistic enough to resonate with your customers.
There are pros and cons of using AI to help with your business plan . So, spend some time understanding how it can be most helpful before just outsourcing the job to AI.
Learn more: 10 AI prompts you need to write a business plan
- Writing tips and strategies
To help streamline the business plan writing process, here are a few tips and key questions to answer to make sure you get the most out of your plan and avoid common mistakes .
Determine why you are writing a business plan
Knowing why you are writing a business plan will determine your approach to your planning project.
For example: If you are writing a business plan for yourself, or just to use inside your own business , you can probably skip the section about your team and organizational structure.
If you’re raising money, you’ll want to spend more time explaining why you’re looking to raise the funds and exactly how you will use them.
Regardless of how you intend to use your business plan , think about why you are writing and what you’re trying to get out of the process before you begin.
Keep things concise
Probably the most important tip is to keep your business plan short and simple. There are no prizes for long business plans . The longer your plan is, the less likely people are to read it.
So focus on trimming things down to the essentials your readers need to know. Skip the extended, wordy descriptions and instead focus on creating a plan that is easy to read —using bullets and short sentences whenever possible.
Have someone review your business plan
Writing a business plan in a vacuum is never a good idea. Sometimes it’s helpful to zoom out and check if your plan makes sense to someone else. You also want to make sure that it’s easy to read and understand.
Don’t wait until your plan is “done” to get a second look. Start sharing your plan early, and find out from readers what questions your plan leaves unanswered. This early review cycle will help you spot shortcomings in your plan and address them quickly, rather than finding out about them right before you present your plan to a lender or investor.
If you need a more detailed review, you may want to explore hiring a professional plan writer to thoroughly examine it.
Use a free business plan template and business plan examples to get started
Knowing what information to include in a business plan is sometimes not quite enough. If you’re struggling to get started or need additional guidance, it may be worth using a business plan template.
There are plenty of great options available (we’ve rounded up our 8 favorites to streamline your search).
But, if you’re looking for a free downloadable business plan template , you can get one right now; download the template used by more than 1 million businesses.
Or, if you just want to see what a completed business plan looks like, check out our library of over 550 free business plan examples .
We even have a growing list of industry business planning guides with tips for what to focus on depending on your business type.
Common pitfalls and how to avoid them
It’s easy to make mistakes when you’re writing your business plan. Some entrepreneurs get sucked into the writing and research process, and don’t focus enough on actually getting their business started.
Here are a few common mistakes and how to avoid them:
Not talking to your customers : This is one of the most common mistakes. It’s easy to assume that your product or service is something that people want. Before you invest too much in your business and too much in the planning process, make sure you talk to your prospective customers and have a good understanding of their needs.
- Overly optimistic sales and profit forecasts: By nature, entrepreneurs are optimistic about the future. But it’s good to temper that optimism a little when you’re planning, and make sure your forecasts are grounded in reality.
- Spending too much time planning: Yes, planning is crucial. But you also need to get out and talk to customers, build prototypes of your product and figure out if there’s a market for your idea. Make sure to balance planning with building.
- Not revising the plan: Planning is useful, but nothing ever goes exactly as planned. As you learn more about what’s working and what’s not—revise your plan, your budgets, and your revenue forecast. Doing so will provide a more realistic picture of where your business is going, and what your financial needs will be moving forward.
- Not using the plan to manage your business: A good business plan is a management tool. Don’t just write it and put it on the shelf to collect dust – use it to track your progress and help you reach your goals.
- Presenting your business plan
The planning process forces you to think through every aspect of your business and answer questions that you may not have thought of. That’s the real benefit of writing a business plan – the knowledge you gain about your business that you may not have been able to discover otherwise.
With all of this knowledge, you’re well prepared to convert your business plan into a pitch presentation to present your ideas.
A pitch presentation is a summary of your plan, just hitting the highlights and key points. It’s the best way to present your business plan to investors and team members.
Dig Deeper: Learn what key slides should be included in your pitch deck
Use your business plan to manage your business
One of the biggest benefits of planning is that it gives you a tool to manage your business better. With a revenue forecast, expense budget, and projected cash flow, you know your targets and where you are headed.
And yet, nothing ever goes exactly as planned – it’s the nature of business.
That’s where using your plan as a management tool comes in. The key to leveraging it for your business is to review it periodically and compare your forecasts and projections to your actual results.
Start by setting up a regular time to review the plan – a monthly review is a good starting point. During this review, answer questions like:
- Did you meet your sales goals?
- Is spending following your budget?
- Has anything gone differently than what you expected?
Now that you see whether you’re meeting your goals or are off track, you can make adjustments and set new targets.
Maybe you’re exceeding your sales goals and should set new, more aggressive goals. In that case, maybe you should also explore more spending or hiring more employees.
Or maybe expenses are rising faster than you projected. If that’s the case, you would need to look at where you can cut costs.
A plan, and a method for comparing your plan to your actual results , is the tool you need to steer your business toward success.
Learn More: How to run a regular plan review
Free business plan templates and examples
Kickstart your business plan writing with one of our free business plan templates or recommended tools.
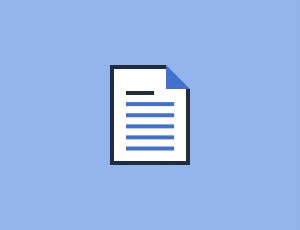
Free business plan template
Download a free SBA-approved business plan template built for small businesses and startups.
Download Template
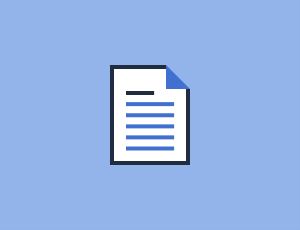
One-page plan template
Download a free one-page plan template to write a useful business plan in as little as 30-minutes.
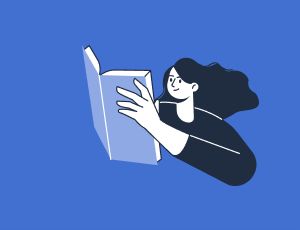
Sample business plan library
Explore over 500 real-world business plan examples from a wide variety of industries.
View Sample Plans
How to write a business plan FAQ
What is a business plan?
A document that describes your business , the products and services you sell, and the customers that you sell to. It explains your business strategy, how you’re going to build and grow your business, what your marketing strategy is, and who your competitors are.
What are the benefits of a business plan?
A business plan helps you understand where you want to go with your business and what it will take to get there. It reduces your overall risk, helps you uncover your business’s potential, attracts investors, and identifies areas for growth.
Having a business plan ultimately makes you more confident as a business owner and more likely to succeed for a longer period of time.
What are the 7 steps of a business plan?
The seven steps to writing a business plan include:
- Write a brief executive summary
- Describe your products and services.
- Conduct market research and compile data into a cohesive market analysis.
- Describe your marketing and sales strategy.
- Outline your organizational structure and management team.
- Develop financial projections for sales, revenue, and cash flow.
- Add any additional documents to your appendix.
What are the 5 most common business plan mistakes?
There are plenty of mistakes that can be made when writing a business plan. However, these are the 5 most common that you should do your best to avoid:
- 1. Not taking the planning process seriously.
- Having unrealistic financial projections or incomplete financial information.
- Inconsistent information or simple mistakes.
- Failing to establish a sound business model.
- Not having a defined purpose for your business plan.
What questions should be answered in a business plan?
Writing a business plan is all about asking yourself questions about your business and being able to answer them through the planning process. You’ll likely be asking dozens and dozens of questions for each section of your plan.
However, these are the key questions you should ask and answer with your business plan:
- How will your business make money?
- Is there a need for your product or service?
- Who are your customers?
- How are you different from the competition?
- How will you reach your customers?
- How will you measure success?
How long should a business plan be?
The length of your business plan fully depends on what you intend to do with it. From the SBA and traditional lender point of view, a business plan needs to be whatever length necessary to fully explain your business. This means that you prove the viability of your business, show that you understand the market, and have a detailed strategy in place.
If you intend to use your business plan for internal management purposes, you don’t necessarily need a full 25-50 page business plan. Instead, you can start with a one-page plan to get all of the necessary information in place.
What are the different types of business plans?
While all business plans cover similar categories, the style and function fully depend on how you intend to use your plan. Here are a few common business plan types worth considering.
Traditional business plan: The tried-and-true traditional business plan is a formal document meant to be used when applying for funding or pitching to investors. This type of business plan follows the outline above and can be anywhere from 10-50 pages depending on the amount of detail included, the complexity of your business, and what you include in your appendix.
Business model canvas: The business model canvas is a one-page template designed to demystify the business planning process. It removes the need for a traditional, copy-heavy business plan, in favor of a single-page outline that can help you and outside parties better explore your business idea.
One-page business plan: This format is a simplified version of the traditional plan that focuses on the core aspects of your business. You’ll typically stick with bullet points and single sentences. It’s most useful for those exploring ideas, needing to validate their business model, or who need an internal plan to help them run and manage their business.
Lean Plan: The Lean Plan is less of a specific document type and more of a methodology. It takes the simplicity and styling of the one-page business plan and turns it into a process for you to continuously plan, test, review, refine, and take action based on performance. It’s faster, keeps your plan concise, and ensures that your plan is always up-to-date.
What’s the difference between a business plan and a strategic plan?
A business plan covers the “who” and “what” of your business. It explains what your business is doing right now and how it functions. The strategic plan explores long-term goals and explains “how” the business will get there. It encourages you to look more intently toward the future and how you will achieve your vision.
However, when approached correctly, your business plan can actually function as a strategic plan as well. If kept lean, you can define your business, outline strategic steps, and track ongoing operations all with a single plan.

Noah is the COO at Palo Alto Software, makers of the online business plan app LivePlan. He started his career at Yahoo! and then helped start the user review site Epinions.com. From there he started a software distribution business in the UK before coming to Palo Alto Software to run the marketing and product teams.
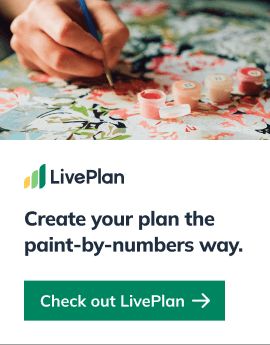
Table of Contents
- Use AI to help write your plan
- Common planning mistakes
- Manage with your business plan
- Templates and examples
Related Articles
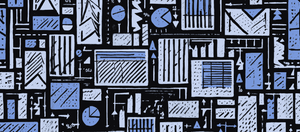
3 Min. Read
What to Include in Your Business Plan Appendix
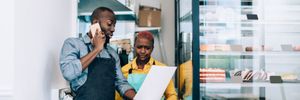
7 Min. Read
How to Write a Bakery Business Plan + Sample
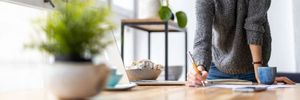
5 Min. Read
How To Write a Business Plan for a Life Coaching Business + Free Example
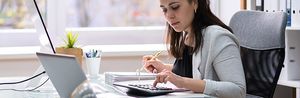
1 Min. Read
How to Calculate Return on Investment (ROI)
The Bplans Newsletter
The Bplans Weekly
Subscribe now for weekly advice and free downloadable resources to help start and grow your business.
We care about your privacy. See our privacy policy .
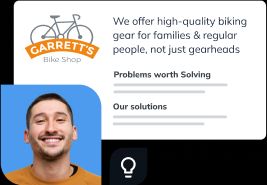
The quickest way to turn a business idea into a business plan
Fill-in-the-blanks and automatic financials make it easy.
No thanks, I prefer writing 40-page documents.
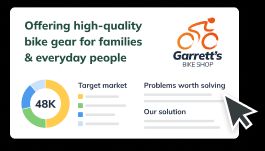
Discover the world’s #1 plan building software

MBA Knowledge Base
Business • Management • Technology
Home » Operations Management » Plant Layouts – Definition and Objectives
Plant Layouts – Definition and Objectives
Plant layout means the disposition of the various facilities (equipment’s, material, manpower etc.) within the areas of the site selected. Plant layout begins with the design of the factory building and goes up to the location and movement of work. All the facilities like equipment, raw material, machinery, tools, fixtures, workers etc. are given a proper place.
Some definitions of Plant Layout are;
- In the words of James Lundy, “It identically involves the allocation of space and the arrangement of equipment in such a manner that overall cost are minimized”.
- According to MoNaughton Waynel, “A good layout results in comforts, convenience, appearance, safety and profit. A poor layout results in congestion, waste, frustration and inefficiency”.
- According to Andrew Greasly (2007), the layout of a plant or facility is concerned with the physical placement of resources such as equipment and storage facilities, which should be designed to facilitate the efficient flow of customers or materials through the manufacturing or service system.
- In the words of Sansonneti and Mallick (Factory Management, Vol. 103) “It is placing the right equipment, coupled with right place, to permit the processing of a product unit in the most effective manner, through the shortest possible distance and in the shortest possible time.”
- According to Apple, “Plant layout is planning the path each component/ part of the product is to follow through the plant, coordinating the various parts so that the manufacturing processes may be carried out in the most economical manner, then preparing drawing or other representation of the arrangement and finally seeing that the plan is properly put into effect.”
Plant layout is very complex in nature as it involves concept relating to such fields as engineering, architecture, economics and business administration. Hence a plant layout, with proper design, encompasses all production and service facilities and provides for the most effective utilization of men, with materials and machines constituting the process, is a master blue print for coordinating all operations.
Objectives of a Good Plant Layout
The principal objective of a proper plant layout is to maximize the production at the minimum of the costs. This objective should be kept in mind while designing a layout for a new plant as well as while making the necessary changes in the exiting layout in response to change in management polices and processes and techniques of production with the production system, i.e. workers, supervisors and managers.
If a layout is to fulfill this goal, it should be planned with the following clear objectives in mind.
- There is the proper utilization of cubic (i.e. length, width and height). Maximum use of volume available should be made. For example, conveyors can be run above head height and used as moving work in progress or tools and equipment’s can be suspended from the ceiling. The principle is particularly true in stores where goods can be stored at considerable height without inconvenience.
- Waiting time of the semi-finished products is minimized.
- Working conditions are safer, better (well ventilated rooms etc.) and improved
- Material handling and transportation is minimized and efficiently controlled. For this, one has to consider the movement distances between different work areas as well as the number of times such movements occur per unit period of time.
- The movements made by the worker are minimized.
- Suitable spaces are allocated to production centers.
- Plant maintenance is simpler.
- There is increased flexibility for changes in product design and for future expansion. It must be capable of incorporating, without major changes, new equipment to meet technological requirement or to eliminate waste .
- A good layout permits material to move through the plant at the desired speed with the lowest cost.
- There is increased productivity and better product quality with reduced capital cost.
- Boosting up employee morale by providing employee comforts and satisfaction.
- The work should be so arranged the there is no difficulty in supervision, coordination and control. There should be no ‘hiding-places’ into which goods can be mislaid. Goods — raw materials and ready stocks — must be readily observed at all times. It will reduce the pilferage of material and labor.
It should be noted here that the above stated objectives of plant layout are laudable in themselves; it is often difficult to reconcile all of them in a practical situation. And as such, the highest level of skill and judgment are required to be exercised. For this, close association between the entrepreneurs and experienced engineers is a must.
Related posts:
- Factors Influencing Plant Layouts
- Techniques or Tools Used for the Design of Good Plant Layouts
- Types of Plant Layouts
- Objectives and Principles of a Good Plant Layout
- Production planning- Definition, Objectives and Levels
- Lean Manufacturing – Definition, History and Objectives
- Features of an Ideal Plant Layout
- Operations Management – Definition, Elements and Objectives
- Production Control- Definition, Objectives, Levels and Factors
- Characteristics of a Good Plant Layout
One thought on “ Plant Layouts – Definition and Objectives ”
looking to get an author and year for this information so i can reference some of the info
Leave a Reply Cancel reply
Your email address will not be published. Required fields are marked *
- Business Ideas
- Grow Your Business
- Online Business
- Internet Marketing
- Use Of Cookie
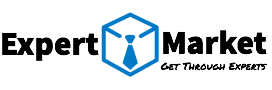
15 Profitable Business Ideas & Opportunities In South Africa for 2024
The most profitable food franchise for sale to invest in, starting a pool cleaning business – profitable business plan sample, starting a new business abroad: is it worth it, starting a food truck business in new zealand – procedure, permits…, how to work effectively with a local marketing consultant, the business of opulence: how luxury hotels stay ahead in the…, 10 situations when your business should consult an employment attorney, top tips for success as a new e-commerce firm, partnering with an amazon fba prep centre: what to look for…, peter’s success: navigating nyc’s vacation rental business legally, examining the top challenges faced by start-ups in australia, how artificial intelligence is changing appraisal management and how to adapt, starting a small business in australia – an overview, find the perfect led display rental for your business needs, 5 reasons to combine dropshipping with shopify, 5 new online business trends for 2024, andrew’s inspiring blogging success: from passion to prosperity, 5 ways to make money from home right now, success in e-book publishing business: a journey from dream to reality, seo tactics tailored for the hospitality industry, marketing the unique: strategies for promoting boutique hotels in a competitive…, 4 ways to optimize underperforming email campaigns, how to create product descriptions that convert.
- Factory and Plant
- Manufacturing
10 Importance of a Plant Layout to Improve your Business Manufacturing Process
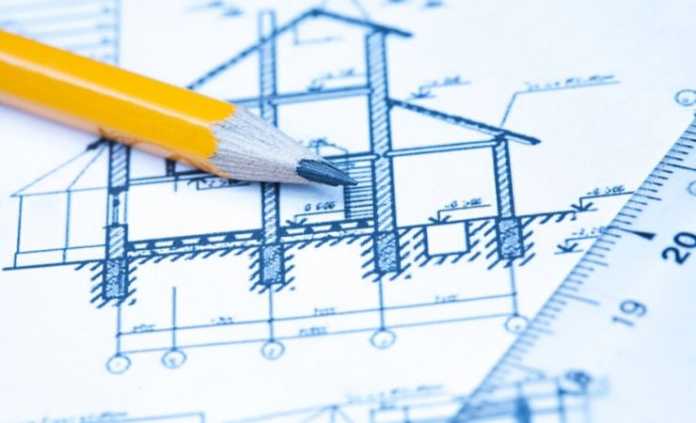
A plant layout is an important part of improving your business’s manufacturing process, as it determines the most efficient use of the available space, materials, and equipment. By carefully examining the layout of your manufacturing facility, you can reduce the amount of time and effort required to set up and operate the equipment, while improving safety and production. Also, implementing an effective plant layout reduces the cost of manufacturing and increases the speed at which goods are produced.
By optimizing the layout of production equipment, workers are able to maximize the efficiency of their labor by eliminating extra movement, decreasing fatigue and increasing productivity. Also, it can help improve the quality of the end product by reducing the number of errors due to poor organization or inefficient processes. A well-designed plant layout encourages the reuse of resources and recycle wasted materials, which increases sustainability and reduces waste.
As we know that having a well-thought out plant layout is the cornerstone of successful manufacturing. It provides the basis for creating a stream-lined production process, which optimizes the use of space, labor and materials. Additionally, it enables the efficient use of resources and technologies, which reduces costs and increases quality. A well-designed plant layout also reduces hazards and improves overall operation, for a more profitable and sustainable business.
10 Importance of a Plant Layout
- Increases Efficiency : A good plant layout will help to increase efficiency by optimizing workflow and reducing material flow.
- Enhances Productivity : With fewer obstructions and less wastage, better communication and a more streamlined flow of the production process, a well-organized plant layout can result in higher productivity.
- Reduces Wastage : Poor layouts can cause wastage of resources due to inefficient and ineffective production line.
- Minimizes Risk and Accidents : Improved safety can be achieved in the workplace by minimising obstructions and unnecessary equipment.
- Enhances Employee Job Satisfaction : An efficient layout increases employee job satisfaction as they are able to perform their duties quickly and precisely with less confusion.
- Responsible for Maximizing Efficiency : A well-designed plant layout takes into account various factors such as material flow, production demands and human resources. As a result, it can maximize efficiency
- Develops Economy of Scale : Plant layouts support economies of scale and can help to increase profits by reducing production costs.
- Manages Transportation : A well-thought-out plant layout will limit the amount of transportation necessary. This reduces the cost of production and improves efficiency.
- Facilitates Communication : Plant layout makes communication between departments and workers much easier through enhanced visibility.
- Streamlines Maintenance : By removing obstructions from areas that are necessary for maintaining the machinery, a good plant layout has the ability to minimize downtime and costs associated with repairs.
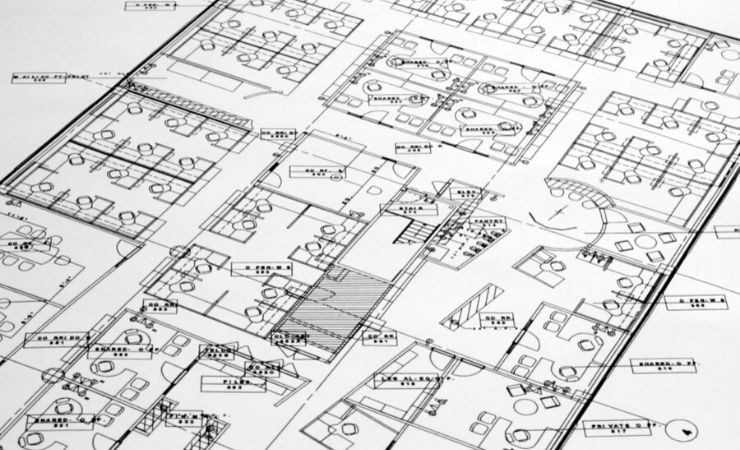
The Cost Of Materials Handling Will Reduce
When you’re operating a manufacturing plant, one of the most significant concerns that you have to be wary about has to do with the reduction of costs. As much as possible, the plant has to operate most economically. This can be achieved with a plant layout.
With a plant or factory layout, you’re able to arrange every section in the plant. Because this layout works as a floor plan, before every aspect of production is sectioned together, you’re able to study which position works best for the most efficient results.
For instance, long-distance movements are reduced or avoided. Materials don’t have to be moved consistently from one end of the plant to another. When you’re talking about large materials, this means that you have to transport them to a vehicle. This means an added gas expense, and so on. If there was a proper plant layout, this could’ve been avoided.
For instance, you run a garment factory. This requires a lot of work and processes. The demand is very high, so time has to be efficiently managed. Resources also can’t be wasted. This is where the benefits of a plant layout come in handy.
You’ll Have Better Visual Control
When you visit a manufacturing plant, you’ll want to know where you’re going. Even if you own or manage the business, this doesn’t necessarily mean that you know every section. With a plant layout, you have a better visual control every time you visit your business.
You know what needs to go on in every area of the manufacturing plant. If there’s an activity going on in an area that you know doesn’t belong there, you can correct this as soon as possible before a more significant problem arises.
Every Area In Your Plan Will Be Used Efficiently
Running a manufacturing plant is costly. Apart from the salaries of the employees and the cost of the materials, there are utilities that need to be considered. Electricity, for instance, makes up a huge bulk of your operating expenses. This highlights the importance of being able to use every inch in your existing area efficiently.
Don’t waste a single space and make sure that every area is put to good use. This can be achieved through a plant layout.
Here are some ways to achieve efficient use of space, such that you can effectively improve factory operations:
- Proper job assignments in each area, so every member of the workforce is contributing productively
- The location of the equipment, so that multiple job functions for every area can be done
- The creation of up-to-date work areas
Eliminates Bottlenecks In Production
Bottlenecks in the production line refer to delays. In a chain of processes, delays should be avoided. While sometimes it’s inevitable, some strategies are in place that can help reduce this occurrence.
In business operations, bottlenecks are negative. This pulls down the efficiency and productivity. In turn, results are also going to get affected.
When the manufacturing plant goes through bottlenecks, the following may happen:
- There will be increased pressure from customers to deliver on time
- There will be stalls in the production line
- There might be perishable supplies that are going to be wasted
Here, it’s safe to say that a bottleneck is a major problem in any manufacturing plant. As big as this problem is, it can be avoided by simply having a plant layout.
Allows For Better Quality Control
Quality control is an important aspect of any factory or manufacturing business, which begins by having a plant layout. This serves as the guide during the inspection process as to the tasks required to be done in every area. This plant layout also shows the expected results in every area or every level of the production line.
Without quality control in any business, there won’t be a timely execution in orders. Delay will start piling up, which also puts your reputation in a bad light. This is precisely why it’s imperative to have some form of control and inspection in every stage of the manufacturing process.
The abovementioned are some of the best reasons as to why a plant layout is critical. These benefits are common to all manufacturing plants. Whether it’s for a small company or a large scale one, a plant layout shouldn’t be skipped.
When a company has this floor plan as the foundation of daily operations, efficiency and productivity are surely increased.
RELATED ARTICLES MORE FROM AUTHOR
Waste tyre recycling plant business plan & profit in india, how to remove tough carpet stains, 20 manufacturing business ideas without breaking the bank, crafting a profitable paper bag making business plan in india & profit margin, 7 ways to enhance durability and performance using vespel in your designs, how to improve production efficiency in manufacturing, leave a reply cancel reply.
Save my name, email, and website in this browser for the next time I comment.
TRENDING ARTICLES
20 best franchise business opportunities under 10k dollars in the usa, 20 best business ideas & opportunities in dubai – uae.
- Advertise With Us
- Privacy Policy
Privacy Overview
Plant Layout: Meaning, Need and Benefits | Industrial Engineering
After reading this article you will learn about:- 1. Meaning of Plant Layout 2. Need for Plant Layout 3. Objectives 4. Benefits 5. Factors 6. Tools and Techniques.
Meaning of Plant Layout:
The term ‘Plant Layout’ has been defined by many authors in so many ways A few of these definitions are given below:
According to Shubin, “Plant Layout is the arrangement and location of production, machinery, work centres and auxiliary facilities and activities (inspection, handling of material, storage and shipping) for the purpose of achieving efficiency in manufacturing products or supplying consumer services.”
According to Keith and Gubellini, “Plant layout deals with the arrangement of the physical facilities and the manpower which are required to manufacture a product or perform a service.”
ADVERTISEMENTS:
According to J. Lundy, “Plant layout ideally involves the allocation of space and the arrangement of equipment in such a manner that overall operations costs be minimised.”
The above definitions indicate that plant layout is the physical arrangement of planned industrial operations. It implies the preparation of the entire stage of setting for the functioning of the plant designed to produce the specified goods or services.
Laying out in a suitable order of productive equipment with all its ancillary requisites in order to enable the personnel to efficiently operate the machines in pre determined sequence and effectively fulfill their assignments, is the idea involved in the concept of plant layout engineering.
The implications of the plant layout concept are indicated below:
(1) Designing the building with alterations and arrangements, sufficient and suitable to house the plant, equipment and appliances required for manufacturing or allied activities.
(2) Installing the machines at proper places with well prepared floor areas.
(3) Placement of plants, machines etc. in systematic sequence as per the order or work planned and programmed.
(4) Provisions of tools, appliances, stores, materials etc. required for operating the machines.
(5) Making adequate arrangements for service activities or auxiliary facilities for operations of the main plants and handling the equipment.
Need for Plant Layout:
Plant layout has become inevitable function of management due to far-reaching developments in the field of science, technology and their application to wide range of industrial and commercial activities.
Proper plant layout is necessitated by the following factors:
(1) Establishment of new plant to manufacture newly designed and developed products.
(2) Major expansion of the capacity of existing plants to meet additional load of demand.
(3) Incorporation of latest changes in technology, plant design, equipment etc.
(4) Need for increasing the efficiency of operations through radical as well as routine changes in design and methods of production.
Objectives of Plant Layout (or Essentials of an Ideal Layout) :
Plant layout implying the development of physical equipment and facilities aims at integration of machines, materials and men for economical, productive operations.
As Shubin and Madeheim observe, “its objective is to combine labour with the physical properties of a plant (machinery, plant, services, handling equipment) in such a manner that the greatest output of high quality goods and services manufactured at the lowest unit cost of production and distribution will result.”
Systematic arrangement of plant and its ancillaries in accordance with the nature of the job to afford maximum convenience to the workers to operate the activities assigned to them is the basic objective of plant layout.
Since production is nothing but the movement of materials in different stages for conversion into finished products, plant layout is intended to fulfill the following fundamental objectives, which are also the criteria for an ideal layout.
(a) Providing facilities to receive the materials intended to be used in the manufacturing processes.
(b) Proper arrangement of machinery and equipment in each department to provide ample room to place materials within easy reach of the workers.
(c) Near accessibility (through proper routing) to stores centres and ensuring direct and continuous movement of stores materials to initial and subsequent operations.
(d) Free access to machines and assembly lines for quick delivery of materials within each department and for fast pick up of outbound material and wastes.
(e) Adequate storage facilities for materials in process between consecutive operations.
(f) Grouping of machines and departments in such a manner that movement of materials or job on hand between the successive operations is as short as possible with minimum of back tracking and needless handling.
(g) Stock-rooms and tool cabins with facilities for storing, recording and handling of materials, tools, etc. with minimum delay.
(h) Arrangement for packing and creating finished products instantly and automatically moving them to warehouses or different corners bound for different markets destinations.
(i) Arrangement of plant, tools and physical facilities consistent with maximum convenience, safety and health of workers.
Benefits of Plant Layout:
Plant layout planned according to the above noted objectives helps in attaining high productivity in the use of plant, equipment, labour and materials.
Its benefits can be summarised as under:
(i) Good plant layout facilitates accurate planning and control of production. A steady quantity of output is assured by proper layout of the productive capacity and its utilization. Idleness of machinery and man would be reduced to the minimum and production capacity would be maintained intact.
(ii) A sound layout ensures more efficient utilisation of machinery and men. It avoids congestion of production areas, overcrowding of personnel at the production spots and thus seeks to avoid delay in flow of product of eliminates bottlenecks that cause slowdown of the product-schedule. Thus overhead costs are reduced by continuous or uninterrupted use of machines and personnel.
(iii) The proper arrangement of equipment and plant operations would also minimise the effort and cost of materials handling.
(iv) Ideal plant layout secures better utilisation of available floor space. Well-designed plant layout economises the space required for production and reduces the unit cost and at the same time makes provision for additional floor space that may be felt necessary for expansion of productive capacity or diversification of product lines.
(v) Proper machine arrangement and service facilities will reduce “the overall time of work in process” by securing a smooth flow of work over the shortest routes of production. The work in process, the hold of stock, costs of inventory are all minimised by sound layout of plant operations in logical sequence.
(vi) A well designed layout is regarded as “a prerequisite to effective supervision.” Good layout makes it easy for the workers to carry out their assigned activities without the need for elaborate instructions and supervision.
Since the ideal plant layout involves standardised sequence of operations with greater degree of automatic movement of materials and operational processes, supervisory efforts and costs are obviously reduced to the minimum.
(vii) Good plant layout ensures safety to the operating personnel. The risks or hazards in mechanical operations at work centres are eliminated by safety devices built into the design of the plant and the allied layout of the equipment. Plant layout which incorporates safety element will result in lesser accidents and lesser loss of man-hours.
(viii) A good plant layout buttressed by wholesome service facilities, better working conditions like lighting, ventilation, noise-control etc. improves employee morale and enhances their efficiency in performance.
In short, plant layout brings about:
(a) Economies in materials and product handling;
(A) Reduction in number of accidents, loss of man-hours and wastage of equipment;
(c) Better utilisation of available floor space;
(d) Cut-back in idle capacity, superfluous work and delay in operations;
(e) Better provision for maintenance and inspection of the production capacity, work in process and the work completed;
(f) Reduction in cost of supervision; and
(g) improvement in personnel morale and response.
Factors Influencing the Plant Layout:
Let us analyse the important factors influencing a sound plant layout:
1. Nature of the Industry:
Manufacturing processes peculiar to different industries govern the type of plant layout to be arranged.
Industries are classified into following main types for the purpose of layout analysis:
(a) Synthetic Processes:
Synthetic process is one that combines several different ingredients or which involves assembling of numerous components for manufacturing a final product, e.g., soap, medicines, cement, automobiles radio- sets, shoes, etc.
(b) Analytical Processes:
Analytical process is one in which final product is obtained by successive processes that separate the final product from the mass of original material, e.g., oil refining.
(c) Conditioning Industry:
Is one where finished product is turned out by converting raw materials, e.g., sugar, textiles, etc.
(d) Continuous Process Industry:
This involves a sequence of processes serving as a prelude to release of the final product. It is characterised by an uninterrupted flow of operations from raw materials to the completion of the product through integrated facilities, e.g., cement, printing, flour mills, paper, etc.
(e) Intermittent Process Industry:
In this type of industry work is completed by stages. It is carried on in a series of distinct work centres. The final product is not turned out at one stroke in a single factory or work place. Final product is completed after different components are prepared at different centres, e.g., automobiles, radio-set, etc.
This classification should not be viewed as rigid because many industries are combinations of these processes, e.g., continuous synthetic industry like paper.
For continuous process Industries the layout is so arranged that work can be conducted in precise progression as per the sequence of planned operations. Successive operations are carried out in adjacent departments. Plant and equipment are to be laid out in such an order that raw materials are received at one end and passing through different stages finished products are turned out and released at the other end.
The movement of job-piece in the sequence should be well-planned avoiding delay and interruption. The span of movement should not be lengthy and the routes to the followed are to be systematically regulated. Such plant layout should reveal the interdependence of the individual processes in the continuous progression. Usually such movement is automatic and there should be built-in-sequential process.
In intermittent types of industry, plant layout should contain arrangements for the flow of different parts or components from respective departments to the central assembly shop at the required time. There should also be arrangements for storage of intermediate goods till they are diverted towards the assembling centres.
Handling through cranes, conveyor belts and other mechanical devices makes assembling quicker and easier. Complementary work centres should be located at convenient points but there should be arrangement for all the parts to convene on the central department for assembling into a finished product.
2. Influence of Location on Layout :
Layout is influenced by the geographical setting of the site where the enterprise is located. Machine arrangement is designed after taking into consideration the characteristics of the region with reference to power, personnel, climate, market etc.
“The size, the shape and topography of the site will affect the spotting of the building on the plot and for receiving and shipping and for best flow of production in and out of the plant.”
3. Managerial Policies :
Shubin points out that layout is influenced by policies framed by the management regarding the quality of products, size of the plant and the extent to which it is to be integrated, the plans if any for expansion and the quantity of inventory to be stored and the facilities to be provided for employees.
4. The Product and Its Influence on Layout:
The design and the specification of the product to be turned out and its physical and chemical characteristics including the size, the shape and bulk, would decide the pattern of layout of the plant and equipment. If the design of the product is of high quality involving complicated mechanical equipment, the layout should be in elaborate and continuous sequence.
If the design is simple, then the plant layout may consist of arrangements for small process. The type of the product classified from the point of demand would also influence the layout. If the product is luxury article, it is produced on a limited scale under conditions of process layout which minimise specialised equipment.
A product categorised as a necessity would provide the mass market and its layout should consist of a complex of specialised equipment to support longer volume of production. This justifies “the line layout” involving continuous flow of output in planned sequence.
Tools and Techniques for Plant Layout:
The layout engineering aims at proper placement of machines and equipment in order to ensure the turnover of the required output as per schedule. In planning a scientific layout, layout engineer has to devise certain tools, models and techniques as a prelude to actual installation of the machines, equipment and appliances.
The important tools used in layout engineering are process charts, flow diagrams, machine data cards, templates, machine models and plot places. These are meant to analyse production processes to be fitted into the plant layout.
1. Process Charts and Flow Diagrams:
The process charts are of two kinds:
(i) Operation Process Chart:
Any manufacturing activity is a composition of operations on set machines. Plant layout is arrangement of machine, operations wise. The process chart classifies the different operations implied in manufacturing a given product. It is generally preferred for use in planning a new layout. “An operation process chart sub-divides the manufacturing process into its separate operations and inspections.”
The chart is a summary of the manufacturing operation intended to show the planned order of work. Its aims are:
(a) To indicate the points at which materials are introduced, and
(b) To show the sequence of all operations and inspections excepting the materials handling process.
The chart is a symbolic plan of productive action. The usual symbols adopted in chart are: O-operation and □ -inspection.
The circle indicates an operation and the square represents inspection involving the checking of quality of the output and verifying other details.
The operation chart brings out an overall picture of the process and serves as a basis for location of plant, tools etc., or for improvement of operations by elimination, combination or rearrangement. Where two or more allied articles are produced, products are grouped into categories which have common operational requirements.
A “generalised operation chart” can be prepared to indicate the process that produces related products.
(ii) The Flow Process Chart:
“The flow process chart is a graphic representation of all production activities occurring on the floor of the plant.”
While operation process chart shows only the operational points in the sequence, the flow process chart traces out the operations, along with transportation (movement), storage and delay. It charts out the movement of work from stage to stage, the storage points of work-materials, work-in-process, completed jobs, etc.
2. Flow Diagram or String Diagram :
Flow diagram represents the flow chart into a line diagram. A single line is drawn to scale on the floor plan to represent the physical movement of materials through the entire plant. The diagram graphically shows the operations, indicates the process facilities and may also spot out any superfluous process and bring about fruitful re-location of plant activities.
Flow diagram helps in deciding upon the natural and economical sequence of plant operations and arrangement of the production facilities.
3. Machine Data Cards:
Information pertaining to machine is collected and consolidated on a card to get the idea about the nature and capacity of the concerned machines before they are laid out on production line.
These cards contain the following information:
(a) Output capacity
(b) Space requirements
(c) Power needs
(d) Foundation details
(e) Suitable handling devices.
4. Templates:
Templates are cutouts to scale of various machines, equipment, the product or any other physical item, necessary to the process of work. They serve as visual aids in planning the layout.
Spriegel observes, “An excellent procedure in making a layout is to cut small-scaled templates of card-board or paper representing each machine or grouping machine in the process.” Templates are made out from a sheet of heavy paper, plywood, bristol board etc., which should be durable and usable for planning different layouts.
Templates are prepared to indicate the area required by machines, equipment, conveyors, benches, storage centres, etc. These areas and equipment may be shown by templates of different colours to facilitate easy identification. These templates are located in sequence on paper which give a total visual picture of the whole production-complex.
Template arrangement of machinery is an important step in planning the layout. As noted above, templates of machines and operations are fixed upon the floor plan indicating the sequence plotted on process charts in conformity with the criteria of general production plan.
Adequate space should be provided around each machine to facilitate smooth operation of the equipment, for the storage of goods in process, the use of handling devices and maintenance and repairs requirements. The convenience of the worker ensuring him ease in operation should also be borne in mind in plant arrangement.
The templates will enable the holding of trial layout. Revisions, if any, can be made by moving the templates and observing the changed sequence. After the template arrangement is finalised and found suitable, blueprints of the layout are taken out.
5. Machine Models :
Machine models are more elaborate and effective form of trial evaluation of the plant layout. Machine models are three dimensional moulds of machines, equipment, storage fixtures, handling devices etc.
Machine models are prepared when layouts for complex operations are to be planned. When expensive installations of machines are to be made, wooden models of such machines, allied apparatus, etc. are got prepared and fixed on to the floor plan, with storage and aisle space necessary for swinging or moving parts of the machines set in operation. Such models will give a clearer idea of the intended layout and flashes a realistic picture of the operations.
Templates will not unfold the entire perspective. The models with details of machine-name, weight, capacity noted thereon will give the layout engineer a precise vision of the planned operations.
In the words of Keith and Gubellini, “Scale models of men, machines, and all the physical units which enter into the layout problem are intended to achieve the same purpose as templates but do so more realistically.
Machine models help in visualisation of layouts even by non-technical personnel. Models are more durable and can be used for long. They can be photographed for comparative studies. But models are more expensive and time- consuming. Hence only in case of complicated layouts models are used in combination with two-dimensional templates.
6. Layout Drawings:
Layout drawings are floor-plan drawings made to scale. These drawings show the walls, partitions, columns, stairways, elevators, machines, storage areas, aisles etc. Drawings however do not set forth structural details. Coloured and shaded sketches may indicate shops or departments like receiving, storage, assembling, office areas, dispatch sections etc.
7. Plot-Plan :
It is said to show the overall arrangement and utilisation of the plant site, buildings and the adjoining areas.
Related Articles:
- Improvement of Plant Layout: Need and Procedure | Industrial Engineering
- Layout Procedure for a New Plant | Plant Layout | Industries
- Procedure for Building Plant Layout: 15 Steps
- Top 3 Types of Layout | Layouts | Industrial Engineering
We use cookies
Privacy overview.
Your Article Library
Plant layout: meaning, need and importance.
ADVERTISEMENTS:
After reading this article you will learn about:- 1. Meaning and Definition of Plant Layout 2. Need of Plant Layout 3. Importance 4. Objectives 5. Factors Affecting 6. Types 7. Advantages.
Meaning and Definition of Plant Layout:
Plant layout is the most effective physical arrangement, either existing or in plans of industrial facilities i.e arrangement of machines, processing equipment and service departments to achieve greatest co-ordination and efficiency of 4M’s (Men, Materials, Machines and Methods) in a plant.
Layout problems are fundamental to every type of organisation/enterprise and are experienced in all kinds of concerns/undertakings.
The adequacy of layout affects the efficiency of subsequent operations. It is an important pre-requisite for efficient operations and also has a great deal in common with many problems. Once the site of the plant has been decided, the next important problem before the management of the enterprise is to plan suitable layout for the plant.
Definitions:
According to James Lundy, “Layout identically involves the allocation of space and the arrangement of equipment in such a manner that overall operating costs are minimized.”
In the words of Mallick and Gandreau, “Plant layout is a floor plan for determining and arranging the designed machinery and equipment of a plant, whether established or contemplated, in the best place, to permit the quickest flow of material, at the lowest cost and with the minimum handling in processing the product, from the receipt of raw material to the shipment of finished product.”
According to Apple, “Plant layout is planning the path each component/part of the product is to follow through the plant, coordinating the paths of the various parts so that the manufacturing processes may be carried out in the most economical manner, then preparing drawing or other representation of the arrangement and finally seeing that the plan is properly put into effect.” (Plant Layout and Material Handling by Apple).
In the words of Sansonneti and Mallick (Factory Management, Vol. 103) “It is placing the right equipment, coupled with right place, to permit the processing of a product unit in the most effective manner, through the shortest possible distance and in the shortest possible time.” The last definition seems to be most appropriate.
Need of Plant Layout:
Many situations give rise to the problem of plant layout. Two plants having similar operations may not have identical layouts. This may be due to size of the plant, nature of the process and management’s calibre.
The necessity of plant layout may be felt and the problem may arise when:
(i) There are design changes in the product.
(ii) There is an expansion of the enterprise.
(iii) There is proposed variation in the size of the departments.
(iv) Some new product is to be added to the existing line.
(v) Some new department is to be added to the enterprise and there is reallocation of the existing department.
(vi) A new plant is to be set up.
Importance of Plant Layout:
The layout of a plant is quite important in view of the above definition but the importance of a layout may greatly vary from industry to industry.
The possibility of attaining the best possible layout is directly proportional to following factors:
(i) The Weight, Volume or Mobility of the Product:
If the final product is quite heavy or difficult to handle involving costly material handling equipment or a large amount of labour, important consideration will be to move the product minimum possible e.g. boiler, turbines, locomotive industries and ship building companies etc.
(ii) Complexity of the Final Product:
If the product is made up of a very large number of components and parts i.e. large number of people may be employed for handling the movement of these parts from shop to shop or from machine to machine or one assembly point to another e.g. automobile industry.
(iii) The Length of the Process in Relation to Handling Time:
If the material handling time represents a appreciable proportion of the total time of manufacturing, any reduction in handling time of the product may result in great productivity improvement of the industrial unit e.g. Steam Turbine Industry.
(iv) The Extent to which the Process Tends towards Mass Production:
With the use of automatic machines in industries for adopting mass production system of manufacturing the volume of production will increase. In view of high production output, larger percentage of manual labour will be engaged in transporting the output unless the layout is good.
Objectives of Good Plant Layout :
A good rather an optimum layout is one which provides maximum satisfaction to all concerned i.e. shareholders, management employees and consumers.
The objectives of a good layout are as follows:
(i) Should provide overall satisfaction to all concerned.
(ii) Material handling and internal transportation from one operation to the next is minimized and efficiently controlled.
(iii) The production bottle necks and points of congestions are to be eliminated so that input raw materials and semi-finished parts move fast from one work station to another.
(iv) Should provide high work in process turnover.
(v) Should utilize the space most effectively; may be cubical utilization.
(vi) Should provide worker’s convenience, promote job satisfaction and safety for them.
(vii) Should avoid unnecessary investment of capital.
(viii) Should help in effective utilization of labour.
(ix) Should lead to increased productivity and better quality of the product with reduced capital cost.
(x) Should provide easy supervision.
(xi) Should provide space for future expansion of the plant.
(xii) Should provide proper lighting and ventilation of the areas of work stations
Factors Affecting Plant Layout:
Whatever be the type of layout being contemplated the following factors are to be considered because these factors have got significant influence on the design of the layout.
(i) Man Factor:
The man is very flexible element who can be made suitable for all sort of layouts.
Main considerations are as follows:
(i) Safety and working conditions.
(ii) Man power requirements-skill level of workers, their number required and their training programme.
(iii) Man power utilization in the plant.
(iv) Human relations.
(ii) Material Factor :
It includes the various input materials like raw materials, semi-finished parts, and materials in process scrap, finished products, packing materials, tools and other services.
The main considerations are:
(i) Design and specifications of the product to be manufactured.
(ii) Quantity and variety of products and materials.
(iii) Physical and chemical characteristics of various inputs materials.
(iv) Component parts or material and their sequence of operations i.e. how they go together to generate the final product.
(iii) Machinery Factor :
The operating machinery is also one of the most important factors therefore all the information regarding equipment and the tools are necessary for inspection, processing and maintenance etc.
(i) The processes and methods should be standardized first.
(ii) Machinery and tools selections depend upon the type of process and method, so proper machinery and other supporting equipment should be selected on the basis of volume of production.
(iii) Equipment utilization depends on the variation in production, requirements and operating balance.
(iv)Machines should be used to their optimum levels of speed, feed and depth of cut.
(v) Machinery requirement is mostly based on the process/method.
(v) Maintenance of machines and replacement of parts is also important.
(iv) Movement Factor:
It mainly deals with the movement of men and materials. A good layout should ensure short moves and should always tend towards completion of product. It also includes interdepartmental movements and material handling equipment. This includes the flow pattern reduction of unnecessary handling, space for movement and analysis of handling methods.
(v) Waiting Factor:
Whenever material or men is stopped, waiting occurs which costs money. Waiting cost includes handling cost in waiting area, money tied up with idle material etc.
Waiting may occur at the receiving point, materials in process, between the operations etc.
The important considerations in this case are:
(a) Location of storage or delay points.
(b) Method of storing.
(c) Space for waiting.
(d) Safeguard equipment for storing and avoiding delay.
(vi) Service Factor:
It includes the activities and facilities for personnel such as fire protection, lighting, heating and ventilation etc. Services for material such as quality control, production control, services for machinery such as repair and maintenance and utilities like power, fuel/gas and water supply etc.
(vii) Building Factor:
It includes outside and inside building features, shape of building, type of building (single or multi-storey) etc.
(viii) Flexibility Factor:
This includes consideration due to changes in material, machinery, process, man, supporting activities and installation limitations etc. It means easy changing to new arrangements or it includes flexibility and expendability of layouts.
Types of Plant Layout:
Production results from men, materials and machinery together with management. The characteristics are changed. To manufacture a product layout begins with which element or elements mentioned above move.
Keeping in view the type of industry and volume of production, the type of layout to be selected is to be decided from the following:
1. Product or Line Layout.
2. Process or Functional Layout.
3. Fixed Position Layout.
4. Combination type of Layout.
1. Product or Line Layout :
If all the processing equipment and machines are arranged according to the sequence of operations of a product, the layout is called product type of layout. In this type of layout, only one product or one type of products is produced in an operating area. This product must be standardized and produced in large quantities in order to justify the product layout.
The raw material is supplied at one end of the line and goes from one operation to the next quite rapidly with a minimum work in process, storage and material handling. Fig. 3.3 shows product layout for two types of products A and B.

Create a plant layout
The Plant Layout template provides shapes you need to create a detailed manufacturing plant design, including the building, machinery, storage, and shipping and receiving facilities.
Note: The plant layout template is only available in Visio Professional and Visio Plan 2. It is not available in Visio Standard.
In the Categories list, click the Maps and Floor Plans category.
Click Plant Layout , and then click Create .
Create or insert a floor plan. You can do this one of three ways — create a Visio floor plan, insert a CAD floor plan, or copy and paste an existing Visio floor plan drawing into a new drawing. See the subsequent procedures on how to do this.
Add shapes to represent machinery, storage, and shipping and receiving facilities.
Create a floor plan
Create the basic exterior wall structure in one of the following ways.
Use room shapes
From Walls, Shell and Structure , drag one of the room shapes onto the drawing page.
Resize the room shape by dragging the control handles and selection handles on individual walls.
Use wall shapes
From Walls, Shell and Structure , drag Exterior wall shapes onto the drawing page.
Resize walls by dragging an endpoint.
Drag an endpoint of one wall to another wall.
The endpoints turn red when the walls are glued. Intersections between two walls get cleaned up automatically.
Note: For walls to join properly, Glue to Shape geometry must be selected in the Snap & Glue dialog box.
Create the interior wall structure.
Drag Wall shapes onto the drawing page, positioning them inside the exterior structure.
Add other structural elements.
From Walls, Shell and Structure , drag structural shapes, such as columns, onto the drawing page.
From the Building Core stencil, drag building core shapes, such as stairs, onto the drawing page.
From Walls, Shell and Structure , drag door and window shapes on top of walls.
Doors and windows rotate to align with the wall and glue to the wall. They also acquire the wall's thickness and move with walls when you reposition them.
After you assemble the building shell and wall structure, you can add electrical symbols and dimension lines.
Add electrical symbols
You can also drag ceiling fixture shapes, such as the Ceiling fan , onto the drawing page.
Add dimension lines to walls
Right-click a wall, and then click Add a Dimension .
Reposition dimension lines and dimension text by dragging a control handle.
Note: To see a tip about a control handle for a selected shape, pause the pointer over the handle.
If you add a dimension to a wall, you can resize the wall by selecting the dimension shape, typing the dimension you want, and then clicking away from the dimension shape.
Insert a CAD floor plan
On the Insert menu, click CAD Drawing .
Under Files of type , select AutoCAD Drawing (*.dwg, *.dxf) . Locate the CAD file and click Open .
To accept the size and location of the CAD drawing, click OK .
After you have inserted the drawing, you can resize it, change its scale, or move it. You can also lock the Visio layer that contains the CAD drawing.
Copy and paste an existing Visio floor plan drawing into a new drawing
Open an existing Visio drawing.
On the File menu, click Page Setup , and then click the Scale tab. Make note of the scale setting in the existing drawing, and then set the scale of your new drawing to match.
In the existing drawing, select the shapes you want to use in the new drawing and then, on the Edit menu, click Copy .
Switch to the new drawing, and then, on the Edit menu, click Paste .
Tip: You can lock the existing layers of a drawing so that you do not accidentally change them when you create a new plan on top.

Need more help?
Want more options.
Explore subscription benefits, browse training courses, learn how to secure your device, and more.

Microsoft 365 subscription benefits

Microsoft 365 training

Microsoft security

Accessibility center
Communities help you ask and answer questions, give feedback, and hear from experts with rich knowledge.

Ask the Microsoft Community

Microsoft Tech Community

Windows Insiders
Microsoft 365 Insiders
Was this information helpful?
Thank you for your feedback.

IMAGES
VIDEO
COMMENTS
Plant layout is the overall arrangement of the production process, store-room, stock-room, tool-room, material handling equipment, aisles, racks and sub-stores, employee services and all other accessories required for facilitation of the production in the factory. ... Business Policy and Strategic Management Notes, PDF, Paper I MBA (2024) 21 ...
A lean plant layout streamlines your smart factory workflow, cuts waste, and enhances value, leading to reduced costs and improved quality. It's all about arranging your processes with the end-to-end flow in mind—turning raw materials into customer-ready products efficiently. Unlike conventional setups, lean layouts align tasks side-by-side ...
laying down a comprehensive business plan. For implementation of this plan, he has to take various crucial decisions namely location of business, layout (the arrangement of physical facilities), designing the product, production planning and control and maintaining good quality of product. This lesson deals with various aspects of plant ...
Examples of Plant Layout Design: Automobile Manufacturing Plant (Product Layout): Description: In an automobile manufacturing plant, a product layout is commonly employed. Assembly lines are ...
Here is a video for a closer look at the layout design and functionality of different sections, 1. The tire types are fed to the robot cell as a batch of 4. 2. Next, Tire rims which represent different sizes of the tires are incoming through conveyors behind the robot cell. 3.
Having a good production layout plan can bring numerous benefits to your business, especially for SMEs. A well-thought-out plant layout can improve efficiency, reduce waste and ultimately lead to higher profits. By understanding your workflow and value stream, you can design a layout that maximizes the use of space and resources and ensures ...
More defines plant layout as follows: "Plant layout is a plan of optimum arrangement of facilities including personnel, equipment's, storage space, material handling equipment and all other supporting services along with the decision of best structure to contain all these facilities." ... economics and business management. (ii) Most of ...
Plant layout is a business structure in which the resources such as materials, equipment and workforce are properly placed and organized within the selected site. It is the planning to ensure that ...
Plant layout is the arrangement of machines, work areas and service areas within a factory. George R. Terry. Plant layout involves the development of physical relationship among building, equipment and production operations, which will enable the manufacturing process to be carried on efficiently. Morris E. Hurley.
Cellular layout is an attempt to bring more order to a process layout by introducing elements of a product layout. Pros & cons Each layout has its own advantages and disadvantages. Product layout has low unit costs for high volume production. It can incorporate specialised equipment, which improves efficiency, and it can be calibrated for
Definition: Plant Layout involves the optimum physical arrangement of the economic activity centres so that they are easily manageable. It aims at finding the quickest route for efficient material flow at minimum cost. We can also understand it as a floor plan of the men, machines and resources used in production.
THE MAIN PURPOSE OF PLANT LAYOUT. The main purpose of a good Plant Layout is to make the manufacturing and operational processes simpler, faster, more efficient, and less expensive, while maintaining high quality and the ability to make products and provide services to meet customers' needs at any time. In order to accomplish this task, you and your management team must become familiar with ...
Here are a few of the most common types of plant layout and design: 1. Process-oriented layout: This type of layout is designed around the manufacturing process. The goal is to create a smooth and efficient flow of production so that each operation can be carried out in the most efficient way possible. 2. Equipment-oriented layout: This type of ...
Plant layout is a plan for effective utilization of facilities for the manufacture of products; involving a most efficient and economical arrangement of machines, materials, personnel, storage space and all supporting services, within available floor space. A good rather an ideal layout is one which provides maximum satisfaction to all concerned i.e. shareholders, management employees and ...
The choice of layout depends on factors such as the type of product being manufactured, production volume, workflow, and safety considerations. Here are the basic types of plant layouts: 1. Process Layout (Functional Layout) Description: In a process layout, similar machines and equipment are grouped together based on their functions or processes.
Principles of Plant layout: a) Integration of production facilities in an efficient manner. b) Minimum movements and material handling. c) Smooth and continuous flow, by implementing proper line balancing techniques. d) Cubic space utilization by saving the floor space for storage and making use of ceiling.
Most business plans also include financial forecasts for the future. These set sales goals, budget for expenses, and predict profits and cash flow. A good business plan is much more than just a document that you write once and forget about. It's also a guide that helps you outline and achieve your goals. After completing your plan, you can ...
Plant layout is very complex in nature as it involves concept relating to such fields as engineering, architecture, economics and business administration. Hence a plant layout, with proper design, encompasses all production and service facilities and provides for the most effective utilization of men, with materials and machines constituting ...
0. A plant layout is an important part of improving your business's manufacturing process, as it determines the most efficient use of the available space, materials, and equipment. By carefully examining the layout of your manufacturing facility, you can reduce the amount of time and effort required to set up and operate the equipment, while ...
After reading this article you will learn about:- 1. Meaning of Plant Layout 2. Need for Plant Layout 3. Objectives 4. Benefits 5. Factors 6. Tools and Techniques. Meaning of Plant Layout: The term 'Plant Layout' has been defined by many authors in so many ways A few of these definitions are given below: According to Shubin, "Plant Layout is the arrangement and location of production ...
ADVERTISEMENTS: After reading this article you will learn about:- 1. Meaning and Definition of Plant Layout 2. Need of Plant Layout 3. Importance 4. Objectives 5. Factors Affecting 6. Types 7. Advantages. Meaning and Definition of Plant Layout: Plant layout is the most effective physical arrangement, either existing or in plans of industrial facilities i.e […]
In the Categories list, click the Maps and Floor Plans category. Click Plant Layout, and then click Create. By default, this drawing type opens a scaled drawing page in landscape orientation . You can change these settings at any time. Create or insert a floor plan. You can do this one of three ways — create a Visio floor plan, insert a CAD ...
1. Run a nursery business. When it comes to a plant start-up, the first thing that comes to mind is probably a plant nursery business. Retail nurseries grow plants from seeds or saplings with the intention that they'll end up in the homes of happy plant lovers. And online plant nurseries are a fast-growing industry!